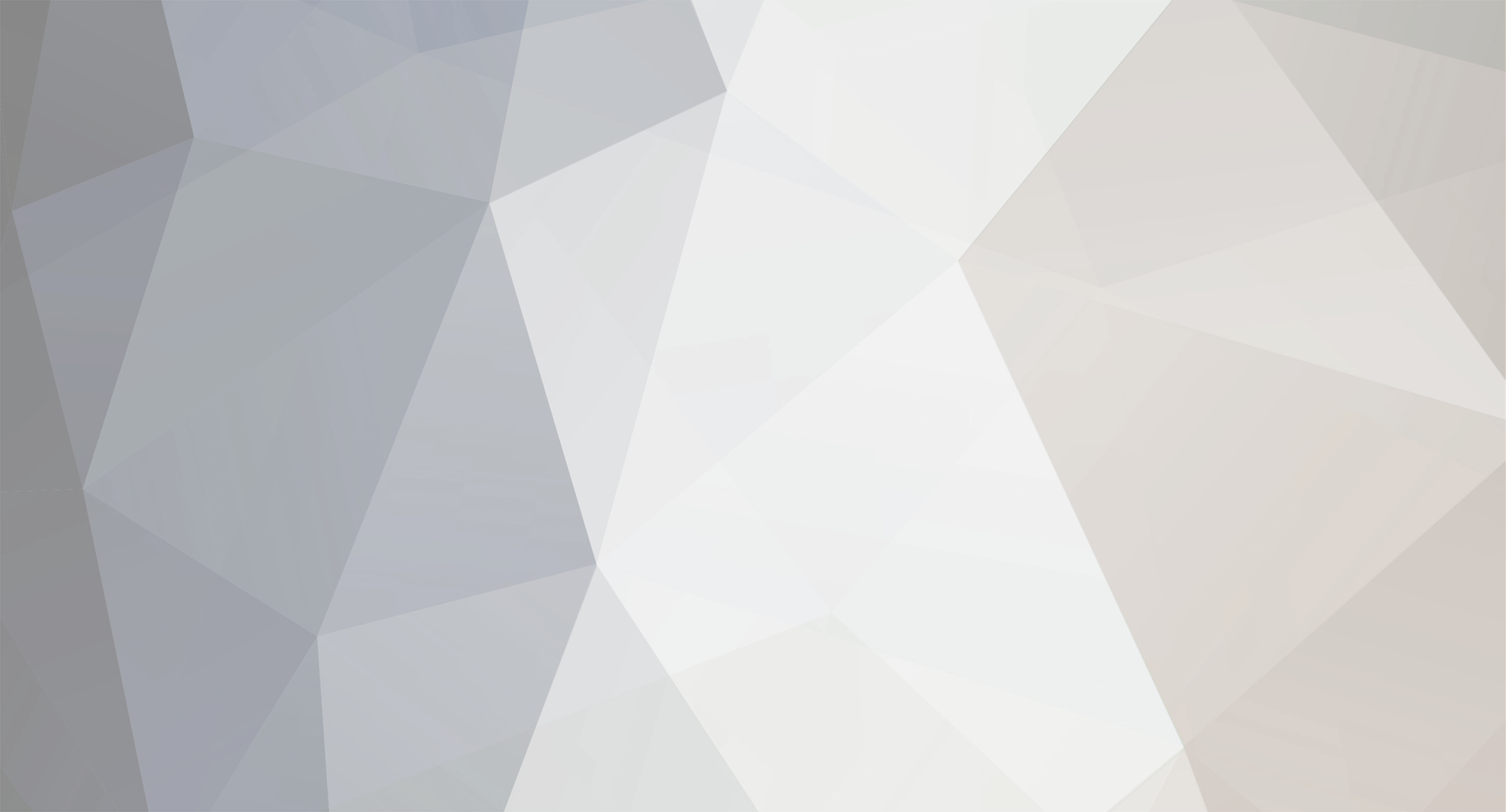
Aerodon
Supporter-
Posts
1,243 -
Joined
-
Last visited
-
Days Won
1
Content Type
Profiles
Forums
Blogs
Gallery
Downloads
Media Demo
Events
Everything posted by Aerodon
-
K Factor going from a Shadin MiniFlo to a JPI 930
Aerodon replied to LANCECASPER's topic in General Mooney Talk
This is probably for a fuel pump engine so start with 30.00. For a gravity system start with 20.00 and you will be close. If the FF indication is way out, then you will have to change the FF transducer. (some of the other FF systems have a completely different output). Then fly a few hours and generate some data from your refuelling slips and the JPI, and follow the instructions in the book on resetting the K factor. Don -
Why are you turning the bug in GPSS mode, i thought the whole point was for the GPS and flight plan to direct it? Aerodon
-
Hi Nic, Yes I can customize the mounts, but I have found the Mooney panels a little tight. Attached is an image of an overlay to go on top of the panel to hide a bit of a gap with a pair of flush mounted G5's. Send me some pictures via email and I can see what I can do. My current recommendation is to spend more on GI-275's and less on labour to make the G5's fit. Garmin make an adaptor plate that will make them fit, and you also don't need the remote GAD29B box (not needed). supercub180@gmail.com Don
-
I don't think so. The 660 selects the channel on the GDL and the GDL receives and plays the XM music - either hardwire or BT. Turn the 660 off and the music still plays. The 660 has audio out wires, but I believe they are for 'alerts' and messages generated by the 660. Aerodon
-
Don, I can BT my cellphone audio to my Bose A20 very nicely. I tried the BT music audio from a GDL52 and a 52R (as apposed to the 'alert' audio) to my A20, and the volume was way too soft. I came to the conclusion that it was not possible. Yesterday my friend managed to get successfully get BT music from a GDL52R to his Lightspeed headsets. So at the next opportunity, I plan to go try by A20's alongside his Lightspeeds for music. Hardwire, no problem. Aerodon
-
I disagree with you. On the upside, Mooney have a pretty good well established design. On the downside it probably takes 3-4000 hours to build one and the competition takes 2000 hours? So the real question is whether you can set up a production line that will cover the overhead and compete in the market. Any assistance you try provide will jets reduce efficiency. Experimental or owner build airplanes are a different market. The new generation of kits has laid out the future. If you are going composite, the factory or shadow factory needs to help the kit builder build the wing in a week using factory jigs, large single pice parts, experienced labor etc. Then the fuselage in a week, the avionics need to be almost ready to drop in etc. If you are going metal, same idea but the parts need to be match drilled and have all the jigs available. And its not cheap either. A friend built a Lancair IV over 20 years and could have put the same hours into his day business and bought a new Malibu Mirage. He tried various owner assist facilities, but the math (or the results) did not work out. Aerodon
-
Mi Mark I'm trying to do the same thing as you, so will do the research needed to get to the bottom of this. It's a good point, does the 'standby ADI display enough information for a legal second navigation display. After all, thats the main objective. It seems that to get full GPS1, GPS2, Nav1, Nav2 configuration you would need pretty much the latest generation of navigators like GTN / GNC series. It seems technically possible to connect both your GNS530 and KX155 to both displays. (The KX155 manual shows multiple indicators on the composite output). But it is a little tedious installing parallel wiring for the composite output a GS indications, and ILS selected etc. I would not bother trying to get KX155 Nav onto the Aspen. But I would try get both navigators onto the GI-275. 1) I doubt there is a way for the GI-275 to identify an aspen failure. Might be an idea to install the switch for instant 'pullup' of the ADI. 2) This is the key, and I have not found documentation yet. I do know that if you set-up the GI-275 as a MFD, you get everything. If you setup as a primary ADI, you get far fewer pages. So why not think the physical installation through to achieve the most functionality that you can reasonably achieve. Then set the instrument as HSI / Standby ADI and see what's left? Don (sorry about the wrong name, I was thinking of GSX,)
-
You can install a toggle switch to instantly get to the ADI. Or select from the menu. Or it does it automatically when it detects a failure of main ADI. Aerodon
-
1 in 100 GA Pilots Killed in an Airplane?
Aerodon replied to 201er's topic in Miscellaneous Aviation Talk
I used to think that the odds of dying in GA was about 1:10,000 of the participants and that it was similar to motorcycling, skiing, scuba diving etc. But I think you are asking the correct question, if there are 500 pilots in a room, how many can expect to die in a year and how many will die in a 30 year flying career. Initially your 1:100 sounds horrifying, but here is a website with some alternatives: https://injuryfacts.nsc.org/all-injuries/preventable-death-overview/odds-of-dying/ First, the lifetime odds of all causes is 1:1. Heart disease 1:6 Motor vehicles at 1:106 Motor cyclist 1:809. So if your calculation of 1:100 is correct, I am happy with that as a risk compared to above. I think your calculation is a bit flawed. If there is a fatality rate of 0.75/100,000 hours, that will include passengers? So if average fatal accident is 3 persons, then the pilot fatality rate is 0.25/100,000 hours. If we all fly 50 hours a year (average), then there are 2000 pilots and .25 pilots die every year. Or 1 every 4 years or 5 every 20 years. 5/2000 is 1 out of 400. If your flying career is 40 years, then 10/2000 = 1 in 200. And then not to be morbid, I hate the saying 'he died what he enjoyed doing'. But if I get 50 years of aviating and die 6 years earlier than I would have of heart disease, I would say thats less tragic than a 25 year old with 2 kids? My mother's friend's son died on his first solo outing after getting his private licence at 18. Thats tragic. Aerodon -
Paul, A second attempt at answering: A KX155 has a composite output, which means that the conversion and OBS are done internally in the GI-275 (and probably the Aspen). So if the KX155 can be legally connected to two displays in parallel, I can see this working. I can see the GNS530 GPS navigation working on two displays. And if the GNS530 has two Arinc ports (in and out), I can see this working on two displays too. So this issue is what Garmin allows once the GI-275 is configured in HSI/Backup mode, or maybe even MFD/Backup ADI mode. And what Garmin says in the installation instructions. Interesting question. Don
-
Paul, great question. I am doing something similar with a GTN driving a G500 primary display and wanting a SL30 and GI-275 as a secondary Nav and ADI backup. Let me try answer this in a roundabout way. If I had a secondary display like a Sandel SN3500, it could have two GPS's, Two ILS, ADF, and more. And then with a flick of a switch I could turn the backup AHARS/display on. It looks like the GI-275 can do all of this (pity no ADF for us in Canada). Now the difficult part - I've seen some GI-275's installed as MFD's, and then you get all the pages (21 I think?). You can hardwire a switch to instantly get to the backup ADI (and I think you will still have a CDI for navigation). This seems to be what you are trying to achieve? The GI-275 has an internal GPS with a simple 'direct to' navigation input. One external GPS (your GNS530) is better, because then it will start displaying a flight plan. I can see this being able to work in parallel with your Aspen as both displays are just showing the same flight plan. If you had 2 external GPS's I can see this being a problem doing all the switching between 2 displays and 2 GPS's. Now 2 Nav's and 2 displays is going to be a problem - which one is the 'master' to set the OBS? If you had an all Garmin panel, I could see this working, they are good at integrating. Aspen and Garmin, not so much. Unless the OBS of the Aspen and GI-275 can be sync'd, I would say your shop is correct. The next issue is configuration, once you start setting the GI-275 as ADI or HSI, you start losing some of the pages. I am not familiar enough yet to know. The question you need to ask, is once the 275 is set as backup Attitude Indicator, what pages are left? And can you navigate off this? Can you set the OBS? I think the real objective is to have redundancy, and not to worry too much about displaying every nav/gps option with every display. I want a GTN750 and G500 to be my primary navigation and display, coupled with the autopilot. My SL30 and GI-275 is my backup (and monitoring) navigation, I think it's great that it also has an internal GOPS and a direct to feature and a backup AH. I want to make sure that with everything else 'off' I can fly direct to a point and keep the right side up. Then next 'must have' is to be able to fly at least a VOR/ILS approach. With these, I don't care that I have to hand fly with no autopilot. I've flown for more than 20 years behind a KFC200 autopilot, and never once wanted the AP to fly Nav2 (or now GPS2). (I wrote this fairly quickly, so E&O excluded) Aerodon
-
Hard to tell, but that looks like a wire to ground the engine to at the engine mount or airframe? That could spoil a lot of annunciators and gauges? Aerodon
-
PA24 long distance flight ends in a dwelling
Aerodon replied to tigers2007's topic in Mooney Safety & Accident Discussion
I agree with Cruiser, I think this creates a false sense of security. Instrument approaches are all pretty similar. You get used to following a sequence and pre-planning what to do next. Generally you are flying straight and descending. Or flying level and turning. The wheels (wings) start falling off with circling approaches, it can get quite difficult to get back onto a missed approach procedure once you have started circling. Circling down to find the airport on your own made up plan has got to be one of the worst ideas out. I fly over the mountains on the west coast. Having a 760 in front of me might save my life one day. I will absolutely use it to descend into a valley if needs be. There is an accident review on Beechtalk where a Bonanza's engine failed catastrophically over the mountains near Seattle. The pilot crashed into the trees about a mile short of a runway, and somehow miraculously survived. (when you see the pictures, I don't know how he did). Listening to the ATC and looking at the radar track, I think that if the pilot had a 760 in front of him and had turned towards the airport just a little sooner, he would have made it. Aerodon -
Lance I'm probably not making myself very clear, I'm not saying that KAP and KFC150's are not found in Mooneys, I am saying they are installed at the factory as part of the Type Certificate, not by STC. I could be wrong? Sometimes TC's are very clear on 'installed equipment and options', sometimes not. And sometimes manufacturers will install STC'd equipment on a new plane using an STC developed by others. I am not sure what the paperwork would look like. I'm looking at the paperwork for a 252. There is an application for Airworthiness Certificate which lists all the equipment installed by the factory. Including KFC150 and Speed brakes. We know the speed brakes could be installed later using the manufacturers STC, along with a permission letter and amendment for the AFM. But there is nothing in this paperwork except for the fact that it left the factory with speed brakes. I have a Super Cub project - Cubs are notorious for having aftermarket STC's installed with a photo copy of the paperwork, and no original STC. I am being meticulous with my rebuild. In some cases, equipment has been installed, with a 337, accepted by the FAA. I am taking this as adequate and including the equipment in my rebuild. In other cases, some significant mods have been 'included' in a previous rebuild with no particular 337 reference or approval. I deal with these by either removing the equipment or contacting the STC holder and buying new paperwork. Don
-
Let me put an alternative view forward for discussion. I don't think there is or was an STC for the KAP150 in a Mooney. BK would have worked with Mooney to install it in a 231 and it was approved equipment in a certain range of models. Therefore, if you have enough information and parts, just install it as approved equipment and use the part of the AFM and its supplements to use it? You would take this approach in installing say an O2 system or any other factory option? I agree, if it was an STC, you would have difficulty in getting a permission letter. Is it wise to install a KAP150 - I'd say not. Is it wise to install a KFC150, I'd say maybe depending how much of the system you could get? Some people just don't have the $25k for a new autopilot. A long time ago, I had a KAP200 upgraded to a KFC200. We just changed out all the parts that were different, all the wiring was already in place so it was almost plug n play. Aerodon
-
And now for an 'Encore' I have the original sales brochures for my 1980 Seneca. A KFC200 A/P with HSI and flight director was a $9,880 option, or $31,202 in todays dollars. Thats a production line 'exchange / installed price' over and above the standard attitude and directional gyro's. If you had to take your plane to an avionics shop for a retrofit, it would probably be 50% more? I consider the KFC200 to be the peak of 'electro mechanical' devises in GA, maybe the KFC150 is a little better. So now a GFC500 with 2xGI-275's is fairly equivalent. It is the modern day KFC200 with the addition of GPS, air data and battery backup. I suspect you could get these installed for somewhere between $20 and 30K. My take is that Garmin have done a good job of packaging a lot of functionality and reliability at a reasonable price. I want them to sell 10's of thousands of these so that in 20 years there will still be factory service, parts availability and overall support. I'm done with second and third tier suppliers. I will never willingly buy another BK or S-Tec product, in fact I am going to celebrate when BK finally throw in the towel. Aerodon
-
J/K model speed brake cable replacement
Aerodon replied to airmocha's topic in Modern Mooney Discussion
Hi 'Mocha I have some documentation and knowledge on the speedbrakes. I have seen the 100 series OEM vacuum brakes on a 252 and the only difference between the 14 and 28V is a resistor to the solenoid turning the vacuum solenoid on. I have seen an 'electric' cable version on a friend's Lancair. A small electric motor winds the cable up on a capstan. I have heard that Precise Flight made a certified version of this, but not many copies were sold. (I have not verified this). You have a 262 which is an aftermarket version of the 252, you may well have an electric motor version of the 100 series speed brakes? Then the 2000 series came along which are completely different and have no cables. Take some pictures, including the actuator button and warning annunciator on the panel. Look for documentation in you POH, W&B, 337's etc. Aerodon -
Aspen 2500 and a JPI 930...will they fit?
Aerodon replied to bmcconnaha's topic in Avionics/Panel Discussion
Here's my latest iteration for a Mooney panel. I'm trying to perfect a 3/4 panel much like the later model Mooneys, along with a ne 1/4 panel for the breakers. G500, GI-275 and EDM900. The vertical green lines are for 'radiorax' and there is space for an iPad on the copilots side (still debating). Nowadays its quite feasible to get all your radios in a single column. So I see no reason why one couldn't shift the radios over an inch or two. There is a limitation in the GTN manual on how far the GTN can be form the PFD. Structurally, the M20K has a bar all the way across the lower edge, and then rather flimsy mounting points across the top edge. Unlike the later models that had a bar across the top edge. Aerodon -
I have seen some shockingly bad attempts at recreating factory paint schemes. I used Craig at Scheme Designers to replicate a Piper scheme on my Seneca (it was his design in the first place) with great success. There are numerous benefits, well worth his fee: 1) properly designed, 2) cut vinyl masking to get proper curves 3) proper rights to use the design. Imagine getting a letter from the manufacturer for copyright infringement? A distinct possibility if you copy. 4) Dispute resolution support if it's not done right. That 16 page specification is no joke, and when things are not done right, this is the starting and ending point. My paint shop used 'artistic licence' to do his own thing, despite a written specification and a written agreement to call for owners inspections at various points. It took a few months, but I got 3 of the 7 deficiencies rectified including repainting the aft half of the fuselage at no additional cost, plus some compensation for the lost time. Very unhappy at the time, but extremely satisfied with the end result.
-
Bus connection wire size help?
Aerodon replied to Ragsf15e's topic in Vintage Mooneys (pre-J models)
Yes, I wasn't trying to say the 28 and 14V planes I was looking at were equivalent. The 14V plane I was worked it out for had a 35A breaker switch for the avionics master. The 28V Mooney has a 100A avionics relay, no circuit breaker or fuse. Have you noticed how some manufacturers require the same CB for 14/28V, others show say 5/3A for 14/28V. I'm working through a new CB list for a 28V M20K. New avionics installations shift some devices over to the main bus (displays, GI275, engine monitor etc.). Then in general, there's a major reduction in required power. (more integration and fewer devices). Aerodon -
Bus connection wire size help?
Aerodon replied to Ragsf15e's topic in Vintage Mooneys (pre-J models)
The drawing for a 28V M20K shows the avionics bus wire to be 10Ga. I think I looked at the allowable table and found 14Ga to be acceptable on a 14V airplane. Aerodon -
OK, so then use stainless click bonds with a composite base epoxied into place: I agree, one should be really careful when drilling into any aircraft component. Often the maintenance and repair manual gives guidance on repairs, and I'd drill into a wing rib before a wing spar, and never into a wing skin. But I guess a wing skin is no different to a fuselage skin, and if you followed the same guidance for an antenna installation with doublers, that would be the basis for a wing skin mounted GMU 11. I've had a HID light ballast installed on a Super Cub wing spar. It had a metal plate mounted directly onto the flange of the spar. Aerodon
-
The wing skin outboard of the ailerons is 0.025, so attaching there does not meet all the criteria. Yes, levelling fore and aft can be done by locating in the right place. Levelling laterally could be done with washers. (and I don't know how thick a wing rib is, but I will go measure) Aerodon
-
I saw a Mooney like that and told the installer I would be really unhappy if they did it like in my plane. I have spoken with several installers who agree with me that it would not be acceptable to drill into the wing skin. For a start, Garmin specify a minimum thickness of 0.032 directly connect to the airframe structure. Antennas require a doubler, so I would think that if you attached to a wing skin you would need a doubler attached to a rib? The wing skin is likely at 6 degrees, the GMU11 must be within 3 degrees of horizontal. But it's your plane, do whatever you like. Aerodon
-
Here is my first attempt at making a GMU11 mount for a Mooney. I struggled to do the bends on a standard brake, but I now know what tooling to get to be able to do this nicely.It's designed to go on a rib, and is tilted at 6 degrees. I could do -6 degrees and then you could mount on the inboard side of a rib? GMU11 can be mounted facing forward or rearward, and there is enough space to install a cable tie down. Aerodon