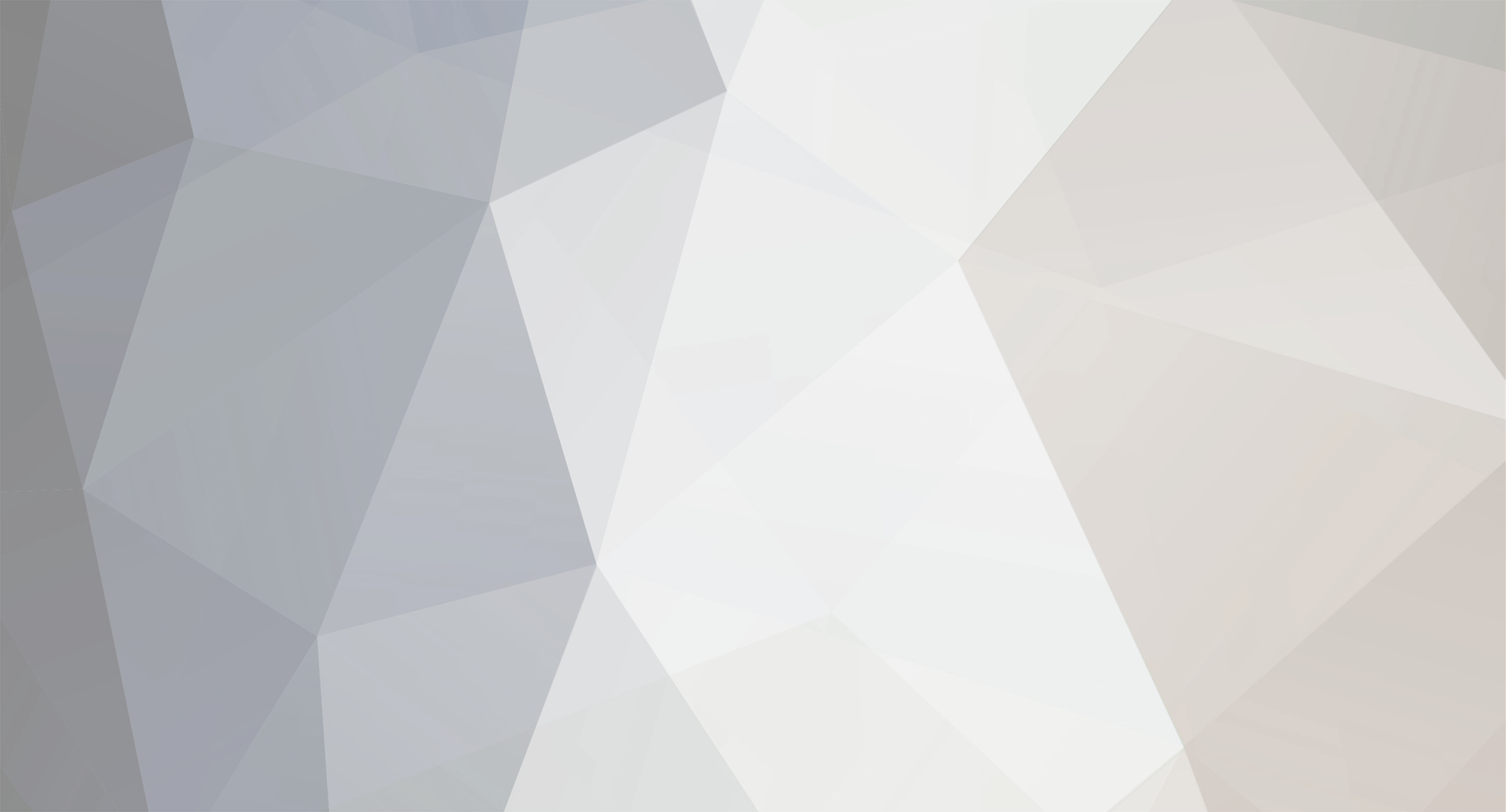
cujet
Verified Member-
Posts
302 -
Joined
-
Last visited
-
Days Won
1
Content Type
Profiles
Forums
Blogs
Gallery
Downloads
Events
Store
Everything posted by cujet
-
From a practical standpoint, large aircraft use "flight time" to track engine time . We commonly use a Hobbs meter that tracks flight time. Often it's configured to count time through the nose/main gear gear squat switch and an oil pressure switch. Ground operations do not affect recorded flight time. For example, both of our Pilatus PC-12's are configured this way. As is our EC-135 helicopter (uses collective pitch to start the timer) . Our larger aircraft, a G650ER and G550 both use the FMS for flight time, calculated by, you guessed it, oil pressure and squat switch. Tach time can also be mechanical or electronic. The mechanical tach is available with configurations such as, 1:1 = 2556RPM or 2300 RPM. Clearly the engine RPM chosen and the type of tach installed make a big difference. Many small aircraft have the wrong tach installed.
-
GAMI injectors are sized. "IF" you have a larger one on another cylinder, try swapping the injectors. IF number 3 peaks first, simply get a larger GAMI injector for that cylinder. It's too lean, too quickly. Mine peak almost identically. Very nice, as I can lean it out like crazy and it remains smooth right up until it quits. Be very careful cleaning GAMI injectors. They do not have steel internals and just about any physical object placed inside can damage them.
-
I've done it many times in various aircraft. Works great, when done correctly. Take your time and make foam pieces that conform to the seat. Then fabricate a "bed" to sit on top, with supports up front. I used 2 core 2 (rigid foam core) composite panel, for light weight and ease. But you can use wood. Some aircraft need multiple parts to make it fit through the door. Generally, I velcro them together or use a piano hinge.
-
Always liked wishbone ash! Anyway, in my example above, I know you hinted at "remote spots" but GA is not always 3x slower than the airlines. Depending on the choice of GA aircraft, and the airports involved and so on. I spent a summer commuting between Naples, FL and Denton, TX. Beat the airlines every time at 182Kts. Nothing remote about either location, or my above example of PBI (F45) to SAV. It's just that airlines sometimes don't have direct flights between 2 points. Longer flights, such as Florida to Montana, or Florida to California are better served by the airlines. I've done the cross country trips many times in a number of different GA aircraft from helicopters to G650ER's. I've formed an opinion that 180Kts is my magic number, the point at which GA travel is fully worthwhile. For all the obvious reasons.
-
I commuted F45 to SAV ( 300+NM) every week from June through the end of Oct last year. Thunderstorms got in the way a couple of times, mostly causing 4-8 hour delays. Even so, the drive is 7 hours, and the airlines 6. My flight time was 2.2. What it allowed was arrival Monday morning without fail, and Friday night on time returns with 80% reliability. And complete weekends to work hard, change helicopter engines/avionics and so on. If I had driven, I'd have only Sat afternoon, night and Sun morning at home. The rest of the time would have been on the highway. Same goes for the airlines. While I saw no benefit personally, my boss really got the benefit of my airplane and the 2 days per week extra "work" time it provided him.
-
why are turbocharged engines designed with lower compression ratios?
cujet replied to RobertE's topic in General Mooney Talk
The large bore size of a typical aircraft piston engine does negatively impact detonation resistance. It's not unusual for modern small bore automotive engines such as the Ford Ecoboost, to operate at a 10 to 1 compression ratio. And they do so on low octane unleaded and high boost levels, as high as 20PSI. Certainly direct injection is a big help, but it's not the only reason automotive engines can operate with high compression ratios and high boost levels. Active knock sensors, higher RPM and small bores are also important. These technologies may translate to an aviation application. But for now, it's really hard to beat the reliable efficiency and power to weight of air cooled aircraft engines. One thing many pilots and aircraft owners are unaware of, is the superb BSFC (brake specific fuel consumption) of modern piston aircraft engines. In fact, until recently, there were exactly zero automotive engines that match the BSFC of an injected Lycoming. That changed recently with the 2016 Prius engine. Which only just matches an IO-360 Lyc in cruise flight. In addition, air cooling can have lower cooling drag, due to higher temperature differential for rapid heat transfer. Alternative engines such as the Rotax 4 cylinder aviation engines, while thrifty, don't match injected Lycoming efficiency. With the notable exception of the FADEC controlled Rotax 912iS, which just matches a 1970 Lycoming IO-360's BSFC. But in the end, the things that increase aircraft engine efficiency, the large bore sizes, the low RPM and high operating temperatures significantly reduce detonation margin on aircraft engines. The turbocharger adds additional stress and often requires lower compression ratios. -
Just remember, you have nothing to gain by allowing a search. All you've done is introduce significant risk. However, you have much to lose, including your aircraft. A recent case with a King Air clearly illustrates this. DHS confiscated the aircraft, charged the pilot with nothing and it took eon's to get the aircraft returned to the owner. We regularly fly to the shooting range. Carrying weapons, all properly stored and 100% legal. That's another unneeded hassle with likely confiscation.
-
Here is a Stemme S10 motorglider above Everest! It has a 30,000 ft service ceiling! (yes, we operate one) As for which aircraft, the answer is simple. The most capable one. You can always throttle back to smaller engine power settings for long range cruise. So the Rocket is the correct answer in my opinion.
-
Great job!!! Good decision making is always a factor in success. You are to be congratulated! I always decline intersection departures for this very reason. Somewhat like Antares, twice I've had engine trouble in flight. Both times, my good choices resulted in success. It's why I don't fly low, and it's why I don't depart and climb out over the swamp at night. I perform pattern climbs to altitude before crossing the swamp. I'd much rather land at an airport, engine or not.
-
Noise canceling headsets, how good are they ...really!
cujet replied to nels's topic in General Mooney Talk
In our Pilatus PC-12's and EC-135 helicopter (yes both are different from a piston powered airplane) the Lightspeed headsets get into some form of a feedback resonance. Pushing them on tighter stops the issue, at least temporarily. When this happens, it actually hurts my ears. I have come to despise Lightspeed headsets. The Bose series 10 and 20 don't seem to do this. Even so, they do put significant, transient, air pressure on the ear drums as I move my head around, say, looking for traffic. I find that I'm most comfortable and least fatigued with the "Clarity Aloft" ear bud headsets. They fit me well and are, in the end, far less annoying. -
Can an overhaul be done "on the cheap" ? Especially in a case like yours? You bet ! Even so, any mechanic will follow the Lycoming service bulletin 240 (I think it's revision W now) and there may be mandatory replacement of perfectly good parts. If your cam is truly making metal, take a very good look at the piston skirts and cylinder walls. Metal bits can imbed in the aluminum piston skirts and score the cylinders.
-
I work as DOM in a corporate flight department. It's our policy to sell aircraft "as is" and not "fix them up" prior to sale. Over the last 20 years, this policy has served us very well. We never hide anything, and we give concessions for equipment in need of replacement. But we never pay for it first, then hope to sell. I can't think of a situation where one will make more money completing all the repairs first. If it's absolutely unairworthy, it might make sense to repair just the fault. If it's a cam, replace cam and lifters. Send it on it's way. This can be done WITHOUT an overhaul. For example, the cylinders can be removed without pulling pistons completely out (push piston pin out) and the crankshaft/connecting rods and accessory gears can remain installed and/or assembled. A gasket set, new cam, new lifters and possibly new crank main bearings (not necessary, but not a bad idea) HOWEVER, a note of caution. A failed camshaft will eventually produce enough metal to ruin pistons and cylinders. Leading to a very expensive repair.
-
We operate 2 Pilatus PC-12 aircraft. They really are not all that fast down low. On a flight from Southern Florida, to Northern Florida, (F45-SJG) we raced our Extra 300L and PC-12. The "little" Extra was on heading, up and climbing away at 3000FPM instantly. The PC-12 started using up real estate like crazy. Just to get it on heading took time. By then the Extra was a mile or two ahead, and the Extra's lead grew for quite some time. As my PC-12 climbed at 1500 FPM and 150Kts, the Extra was already level and cruising at nearly 200Kts. The PC-12 did not "catch" the Extra until 1/2 way there! Sure, we landed first and won the race. Even so, the difference was just a few minutes, at most. And, yes, PC-12 app speeds are low.
-
I can't help but think the 172 is a bit more forgiving with regard to CHT, EGT and oil press/temp. They are trainers, as such, they are configured to operate at speeds other than cruise speed. I think the price you pay for such trouble free operation is a maximum cruise speed of 101.4 Kts TAS.
-
I'm looking forward to battery technology that will provide the necessary energy to run those motors. At least, in my example, the batteries are not gonna happen. There really is a finite limit to electrochemical energy storage. And those theoretical limits, while markedly higher than any battery we have today, are still far short of hydrocarbon fuels.
-
Oh, this is nothing new for Lycoming. 10 years ago we purchased 6 brand new cylinders, 4 of them had near zero compression after 30 hours. They warped horribly.
-
How much crank endplay do you feel on prop, IO 360
cujet replied to garytex's topic in General Mooney Talk
Quite a bit of speculation in this thread. If I were to guess, I'd guess that it's cylinder related. But, I'm not there to troubleshoot. On my Lycoming IO-360, I have plenty of end play, always. However, shortly after shutdown, the engine is markedly harder to "spin over". If I listen carefully, I can hear a zzzzzzzz noise from the cylinders. Not an air leak, but a slight scrape. I overhauled the cylinders, and the clearances are on the "loose" end of the acceptable spec. Even so, they are tight just after shutdown. Used oil analysis results show no problems, no high wear metals and compression remains at 78/80. It's been 500 hours of this, without any issue. Speculation in my case: Pistons don't cool as fast as the cylinders, leading to a period of time where clearances are tight. -
Note: This is my personal experience and may not apply to anyone else. In 1990-91, a Gulfstream GIII I crewed had a bad outflow valve. It's an electric, 8 inch diameter, butterfly valve. It opens fully on the ground to allow enough flow for air conditioning, without pressurizing the aircraft. We had a few problems with this system, leading to multiple complete de-pressurization events at 45,000 feet. The "cheap" company mechanic only purchased a new "controller" (called a pressurization transducer) and the system functioned properly, for a while. The outflow valve's motor was drawing too much current. It would eventually overload and "short out" the drive transistors in the "controller" and motor-itself fully open at 45,000 feet. At which point, I would scramble to switch to the manual control DC motor and manually close the outflow valve to re-gain pressurization. My points: 1) One has well more than 5 seconds of useful "life" during a rapid decompression at 45,000 feet. It took me some time just to get the O2 mask on and set to 100%. Other crew members either did not consider it immediately necessary or "forgot". I never knew. But no one passed out. One guy did get completely dopey and did things incorrectly. But that was kind of normal for him anyway. 2) You cannot see anything as "fog" briefly forms in the air as the pressure departs the airframe. 3) You cannot hear anything, as eardrums are affected. 4) You will not see red warning indications, or notice other "emergency" issues for some time. It's absolute chaos. 5) Once it happens a couple of times, it becomes second nature to "don" the O2 mask, hit the 100% button and take a couple of deep breaths. 6) If I were to guess, I'd say that it took 5-10 seconds for all the air to leave the cabin. Couple that with the quoted 15 seconds of useful consciousness and what we experienced was at least a 20 second window. Which really is plenty of time to get your mask on. 7) If you are already on 100% oxygen, the time of useful consciousness is longer.
-
The Mooney is a four seat, single engine, low powered, general aviation aircraft, with all that encompasses. It's not some magical, difficult to control, overpowered monster. They meet all the FAA requirements for single engine stall speed, G loads, and controllability. In other words, they are docile, have low approach and stall speeds and good recovery characteristics. It's an ideal first plane in my opinion. One that you can grow into, is useful, can be operated efficiently at reasonable cost, and is a superb cross country aircraft. What's not to like?
-
How hard is it to install Airtex leather seat cover?
cujet replied to ryoder's topic in General Mooney Talk
I use 3M, 1357 contact adhesive. It's the right glue for upholstery. But, it does require the right method. Apply properly to both surfaces (not too lean, not too rich) Use masking tape to keep it neat, keeping the glue only where you want it. Pull masking tape. Let it dry until well skinned over. (about 5 minutes) then carefully assemble. You only get one shot. It will remain where it's placed. Some seats require decking material. Watch this video for an interesting example of decking: You can, of course, simply glue it on. Don't use material that will sag. I'd guess that if you are a skilled craftsman, you won't have any trouble. If you are not, bring it to the shop. You will have to live with the results. -
The owner of our PC-12 is 6' 4" and fits fine. Did you move the rudder pedals forward? I'm not a small guy either and I fit fine, I get to fly it from time to time. Flew it from FL to CA a while back. It's possible the configuration was somewhat different than ours. And there are at least 2 different cockpit seats available. Ours really does have plenty of room. However, it is difficult to "climb" into the cockpit due to the overhead panel location.
-
Near Death Experience (Mid-Air) This Morning
cujet replied to MyNameIsNobody's topic in General Mooney Talk
I've had a close call that was no farther than a few feet. Flying from F45 to PBI, a grand total of 11 miles. Extending my Eastbound downwind at F45, I climb to 1200 and call PBI. PBI gives me a squawk, tells me radar contact. About a minute or two later, PBI barks at me with 7CJ suggest immediate climb, with an urgency I've never heard before. I do so right away. Within seconds, a Southbound Navajo goes just under me at a very high rate of speed. He's Not talking to anybody and blasts right into PBI's class C airspace and out again, off into the sunset. That was the closest call possible without catastrophe. I honestly thought we might hit. Never did find out who it was. All I can say is that they were flying like idiots in uncontrolled and controlled airspace. And, Navajo's are pretty darn fast down low. -
ADS-B out configuration options Mode S with ES
cujet replied to OR75's topic in Avionics/Panel Discussion
Digging up this old thread. I just purchased a KT74, $2500. It does indeed require a certified GPS input to enable ADSB out. It's easy to configure and installation could not be more simple. Good looking unit. Mine says made in the UK.- 30 replies
-
- 1
-
-
- ARS-B
- transponder
-
(and 1 more)
Tagged with:
-
Why is it that an entire engine assembled from PMA parts is far less expensive than a Lycoming? Most of us understand that purchasing parts "a la carte" is absolutely the most expensive method of acquisition. A $25,000 Honda Accord contains $250,000 worth of parts, if purchased separately. Yet, even if each individual PMA part is purchased new, with local expensive labor factored in, the PMA engine is still far less money. Something is very wrong.
-
Engines, Cam, etc... food for thought...
cujet replied to Guitarmaster's topic in Vintage Mooneys (pre-J models)
1) Agreed, oil analysis is a tool and can "sometimes" help spot a trend. And, that's only if you perform a UOA on every oil change. 2) Disagree. The Lycoming 360 is not only subject to camshaft failures. Also crankcase cracks, cylinder head separation, connecting rod corrosion, piston pin wear, valve sticking, and a whole host of other failures. I believe that had the newer Lycomings are considerably better. 3) Disagree. My 1974 IO360 had rust on the camshaft, and it failed at 1700 hours total time. That had nothing to do with 1990's metallurgy. 4) Disagree. Camguard has proven itself in our fleet to reduce all manner of engine corrosion. Including cylinder, connecting rod small end (yes this is a problem) , camshaft, crankshaft and gear rust. And, yes, corrosion elsewhere can be damaging to your engine. Lycomings roller camshaft setup is better, smoother and more reliable. 5) Disagree. Aeroshell 15W-50 semi synthetic also helps with internal corrosion issues, AND I never have valve sticking issues using 15W-50. Yet, I do have sticking issues using conventional oils. Maybe it's a hot-n-sticky Florida thing, but it's not just one data point. We've experienced this multiple times on various Lycoming engines. I don't care that my oil consumption is slightly higher on 15W-50. It's use ensures trouble free operation for us. Nor do I believe that we should consider low oil consumption rates as a major positive factor in engine life. It's not. 6) Disagree. Our fleet has better results with Aeroshell 15W-50. However, I might add that Ed Collin (the maker of Camguard) prefers the Phillips. 7) Agree. Oversquare at high manifold pressure does result in the highest possible cylinder pressure.