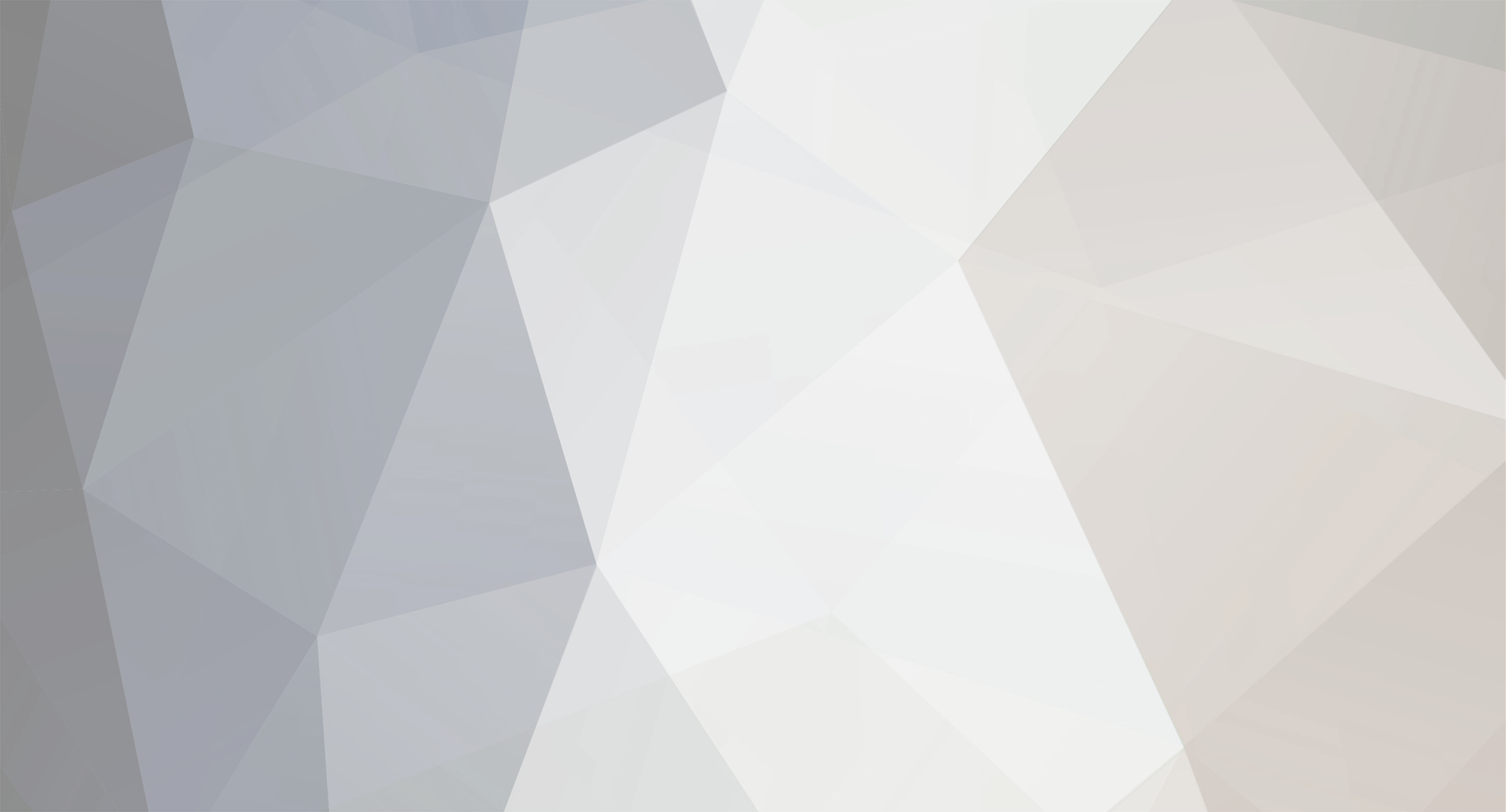
cujet
Basic Member-
Posts
302 -
Joined
-
Last visited
-
Days Won
1
Content Type
Profiles
Forums
Blogs
Gallery
Downloads
Media Demo
Events
Everything posted by cujet
-
I have tried this approach. Does not work all that well. Better to thin AV-30 and use heat lamps to ensure wicking, as in the picture above. Once a part is coated with a waxy, hard coat film, thin oils won't penetrate. They will only soften the AV-30. So, you could easily end up with a sealed seam that has no corrosion inhibiting compound inside (over time, Corrosion-X and ACF simply disappear)
-
Corrosion-X and ACF-50 are thin oils that will GENERALLY, but not always go into tight areas. ACF "claims" to have more corrosion inhibiting additives (ACF's other claims I discount from experience) and it certainly seems to have solids that settle to the bottom of the bottle over time, I suspect these solids actually do something worthwhile. Corrosion-X does not seem to have solids that settle. Both work well in the short term and are good choices for application on assembled parts. AV-30 is my absolute favorite product. It goes on about the thickness of motor oil and dries waxy and stops corrosion dead. Regardless of claims on the can, it really does not "wick" very well. But, it can be thinned with MEK or other solvent and will "wick" into tight areas quite well. I did this on my Cessna with great results. I generally use a heat lamp array to keep the AV-30 "application area" hot and the AV-30 thin until it goes where I want it. Pilatus uses it on the PC-12 as the major method of corrosion control. In this picture, you can clearly see that the thinned AV-30 came out the other side, and it's also on the outside of the fuselage seam here. I used heat lamps. Corrosion-X's "Max-Wax" is much like AV-30. Dries tough and won't attract dirt or dust. Lasts forever. Has an amber tint so you can determine how much, and where it has been applied. (believe it or not, this is very important) Corrosion-X's "Heavy Duty" is a very thick oily film that does not dry. It's perfect for preventing corrosion on components that must move, such as rod ends and things that rub. Interestingly, "Heavy Duty" eventually releases it's oil and drips out of my wing all year long. YUK. But does not wick well otherwise. It just flows downhill. Note: Think of "wicking" as capillary action. Thin oils will climb into very tight areas. You can see this when placing a threaded bolt tip in the fluid. It will climb up. LPS-III is a thick waxy substance that dries to a waxy film, but does not "wick" at all, and forms a weak surface that eventually goes away under use. It's "old school" I don't like it and no longer use it. There are many other products too. Aircraft Spruce sells quart of "Par-al-Ketone" a thick, waxy, cosmoline type product that's been around forever. It works very well, can be thinned, sprayed when thinned, and hardens into a relatively dust resistant, moderately tough, waxy surface. It's the cheapest of all the options, and the most cost effective. It's also probably the most versatile. However, it has a distinct, but mild odor and I try to avoid using it inside small aircraft. I'd NEVER use it inside a "cabin class" aircraft, such as a Gulfstream G550, as the odor would be forever there. Lastly, I'd like to talk about Boeshield. It's a thin product that sprays nicely. Can be used nearly anywhere, "wicks" fairly well, dries to a waxy film and is nearly 100% clear (at least initially) and it's nearly impossible to tell if a part has been coated or not. Over the years, it turns slightly milky, and eventually starts to flake or "sluff off" for lack of a better term. If applied liberally, it will protect a flat surface better than Corrosion-X or ACF-50 (as it's waxy) . I suspect, (but don't know) that it may not wick as well, with this stuff, you just can't tell. Heat lamps work with this stuff too. I like Boeshield very much, but I generally don't use it often due to the lack of visible film and questionable lifespan in some EXPOSED applications such as landing gear and wheel wells (its fine inside a wing) . For example, I applied it to my motorcycle engine. Imagine my surprise when it was mostly gone after a year. (when dry, you can scrape it with a fingernail)
-
I balance helicopters and props as part of my job. It's not possible to achieve jet/turbine levels of smoothness from a piston powered prop aircraft. Don't expect Gulfstream G550 like smoothness (designed to keep all the noise and vibration behind you) from a front engined, piston powered, prop driven aircraft with an exhaust directly under your feet..... Obviously, design configuration is a large part of the noise and vibration we experience. Interestingly, there are apps for the iPhone that will display and record vibration. They are handy to help determine the frequency of the vibration you are experiencing. Much of what we experience is normal and should be expected. As mentioned above, dynamic prop balance is a good thing and will often lead to a more pleasant experience and longer exhaust and baffle life. Another factor, often overlooked, are rubber engine mounts. They insulate the airframe from much of the engine vibration. The rubber engine mount's age, temperature and condition will affect what you feel. Even how long they have been sitting between flights affects the stiffness. Ever wonder why some days the airplane seems smooth and other days there just seems to be more vibration no matter what you try? Engine mount temperature and stiffness could be the reason. Some owners will turn mounts upside down about half way through their life (they sag and take a set) . This often results in a noticeably smoother airplane.
-
On a turbonormalized engine, operating at sea level manifold pressures, ideal ignition timing won't be far off the magneto's setting. An electronic ignition won't have much room to optimize the combustion efficiency. Contrast that with a normally aspirated engine at 12,500 feet, running 17 inches manifold pressure. The ideal timing in that situation may be as much as 40 degrees advance. A big improvement in efficiency over the fixed 20 degrees of a magneto.
-
Also, be aware that it's common practice for maintenance/overhaul shops to set older Lycoming engines oil pressure to "new production" specs, which are significantly higher. Lycomings have traditionally had issues with sticking valves. One way the factory chose to reduce this issue is with the higher oil flow to the rockers/valves, via higher oil pressure.
-
Here in South Florida, corrosion is always a problem. Corrosion X, ACF-50, AV-30, Max-Wax and other products are lifesavers here. The other part of the equation is that there are some incredibly qualified and capable sheet metal guys here. For example, located in a crusty hangar at Lantana Airport, there is a sheet metal man that is without equal (Robbie) . He does corrosion related repairs on a daily basis. I've used him on our Pilatus PC-12 (yup, it corroded a rib) and the result was perfection. The cost was very reasonable also. I'd use him before I'd attempt such a complex repair myself. And, I'm a qualified A+P, with sheet metal tools and occasional bouts of significant sheet metal experience. I'd guess the airframe could be repaired for a reasonable cost, if the right guy was located.
-
Good morning! I am DOM in a high end corporate flight department. I also have a background in extremely high end automotive painting (from a past life) and I am a moderately experienced sheet metal guy. I prefer stripping an airframe with the proper chemical stripper, a stripper that is reasonably viscous, and neutralized instantly with water. That's how the big boys at Gulfstream do it. What many don't understand is the effort required to strip an airframe properly, as the stripper will find it's way into joints, under hardware, and on to your windows. Done properly, it's the way to go. Then careful prep etch/alodine. Aluminum is an interesting metal. It's very flammable, most people don't know this. However, aluminum, when exposed to the oxygen in the air instantly forms a tough, thin, oxide coating that prevents further oxidation. Hence the inert nature of aluminum in real world use. (off topic, we can talk about thermite powder, a very reactive mix of alum and iron oxide) The aluminum alclad on sheet metal is very corrosion resistant and very thin as mentioned in the post above. Careful use of "Scotch Brite" won't remove it. When using alodine on an aircraft, it becomes clear just where the alclad remains and where it is gone, as the color is markedly different. I generally use etch and the red "Scotch Brite" to scuff the aluminum. Rinse it and rapidly treat with alodine, which also works it's magic rather rapidly. Surprisingly, you will likely see large areas of sheet metal (even on new aircraft) where Alclad is no longer there. When manufacturers drill holes, they often sand off the burrs, sand to promote adhesion and so on. They might even sand the aluminum to remove blemishes. This all becomes clear when alodine is applied. I have been treating minor corrosion on local South Florida aircraft using a Soda Blaster. It's a viable method of stripping paint and corrosion in small areas, such as around rivets. There are some companies stripping entire airframes using Blasting Soda. It's reasonably inert with a pH of around 8.2, and instantly neutralized with water, etch, mild acids and of course Alodine. Done correctly, Soda Blasting won't remove Alclad. And it does leave a good surface for paint to bond to. However, I do not know if it's a viable method for stripping an entire aircraft. I suspect the methodology is not fully worked out. Edit: It's best to make an effort to preserve the Alclad, obviously. But don't get wrapped around the axle on this subject. It's tougher than you might guess, for example, buffing and polishing aluminum with abrasive polish won't instantly remove it. That takes years of buffing... And, if you look carefully, you can see where it's been buffed off. Sanding with 320 will penetrate the Alclad. But, again, the manufacturer may have done this in production.
-
I generally don't run lean of peak. I like the speed, so I run a bit rich of peak. My GEM engine monitor is older and does not display the actual EGT. Only the trend and comparison between cylinders. In fact, the display is adjustable so the bar graph is pilot friendly. I had been operating at 2600RPM, 7500 feet I was using AS-100 oil, with Camguard, it had 23 hours on the oil.
-
My Lyc IO-360 just stuck a #2 ex valve at 7500 feet, top of descent. 320 hours since overhaul. What's interesting about this is the fact that I did the overhaul, and documented every measurement. The valve to stem clearance DID tighten up considerably and the result was a valve guide with 0.001 inches LESS clearance than before, in the section nearest the port and a bit tighter than the initial ream elsewhere. Likely it happened in the way you describe. The aircraft is flown often, and oil change intervals never exceed 25 hours. The cylinders had 1700 hours since new, 320 since overhaul, and new valves and guides were installed at overhaul. Of course, the sticking valve happened as I reduced power a bit, and headed downhill, picking up a good bit of speed and cooling air. It went away with reduced RPM. Never had any "morning sickness" or any other form of roughness. This was the first indication there was a problem. During the repair and rework yesterday, after hammering the valve free from the guide, I used the very same reamer on the valve guide that I did initially, and it removed metal. I would guess that the thermal distortion has run it's course, and the repair will be a final fix on my cylinder. The other cylinders "wobble checked" just fine. As another data point, our company's Extra 300L, with a Lyc IO-540 angle valve, with just over 100 hours since new, stuck a #5 exhaust valve. I don't fly that aircraft. I do maintain it, and I do use a different oil in that engine than mine. It gets very frequent oil changes. Edited for clarity. I did not mean to say the valve stem to guide clearance had been reduced to 0.001 inches. Only that it was about 0.001 inches tighter in one small section of the guide, nearest the port/guide interface.
-
With many people, pupils constrict significantly in bright light. The smaller pupil provides a greater depth of field and, in some cases, sharper vision. Often, 50 year olds are able to read newspapers in direct sunlight, but not in low light conditions. Matters not to the FAA, when a medical requires glasses.
-
I said nothing about having a "right" to an airman's certificate. Don't put words in my mouth! Nor will I accept your "paranoid" label. That's a disgusting tactic and you have no business using it here. Aviation is my business and I take it very seriously. I have a set of experiences unique to me. They include some stunning ones with the FAA. As I mentioned above, the FAA can and sometimes does act in an arbitrary manner and there is nothing one can do to change that. One has no constitutional protections against such behavior.
-
I agree about airworthiness. But, the inspector is looking at paperwork, not the crack in your engine case and your corroded main spar. The FAA follows "guidance". But, they are not held to it, and they often act however they want, AND you have NO RECOURSE. Our chief pilot lost his cert for 6 months. The FAA did not follow the very guidance they publish! No, they did not "YANK" his ticket on the spot. They informed him that it was to be sent in. The outcome was the same, no ticket. He was able to get it back, after hiring a very expensive lawyer and battling the FAA, proving that they were in the wrong. Your failure to see the seriousness of destroying one's livelyhood on a whim bothers me. To claim this does not happens flies in the face of the facts. Forget your reading glasses on a clear and bright day, and see how well your "ramp check" goes.
-
Really? The inspector's only goal is to find violations. And you can't see a reason to be concerned? As an aviation professional, I'm here to tell you, I have every reason to be concerned. The FAA can YANK my tickets on a whim, and I have ZERO recourse. I can't take them to court, I can't hold the US Constitution over their heads, I have no power to fight the system. They can, and often do, act arbitrarily, ruining peoples lives in the process. Want to know more. PM me.
-
I agree with you 100% First off, there is something about entry and search that the FAA has in it's guidance, that is unconstitutional. They are required to check the ELT battery date. On many aircraft, that requires entry, baggage removal and some minor aircraft disassembly. A perfect way to do a full search of an aircraft. It's really too bad people don't understand their rights. Such as the right to "free and unrestricted travel".
-
As a FAR 135 operator of a G550, and several other aircraft, ramp checks were a yearly, or more frequent, affair. Not to mention the large number of FAA maintenance (part 145) checks I've been through. Lately, the FAA has been less willing to travel and this months ramp check was canceled. My advice: 1) Review the FAA guidance on ramp checks 2) Ensure you have everything on the guidance list and operate a completely airworthy aircraft. AND, most importantly: 3) If at all possible, avoid a ramp check any way you can, regardless of how innocent the check may seem. It's nice that the inspector above "sugar coats" the situation. The reality is that you are putting yourself at significant risk. Don't ever discount the fact that they are only interested in finding some form of error, a job they are well trained to do, (error is what they are looking for after all) and you will pay the price for that error. Using the "risk-reward ratio" calculation, this situation is 100% skewed against you. As you have nothing to gain and much to lose. I have stories you would not believe, so serious they can't be posted here. I can't tell you what to do if approached. But in my case, I'd rather walk away, hit the head in a dire emergency, rent a car and stay in a local hotel than risk a ramp check.
-
Real world experience with electronic ignitions: Note: I work as an A+P in a corporate flight department, I am a pilot and aircraft owner. I've installed, and/or been involved with the installation of a number of electronic ignition systems. Including Lightspeed's on a IO-360 equipped Velocity, Lightspeeds on an IO-540 powered F1-Rocket, E-Mags on a Velocity and others. Starting about 10 years ago. 1) the engines always operate smoother. 2) the peak power might be slightly less, resulting in a possible "slight" reduction in rate of climb. However, this is impossible to verify. 3) cylinder head temps in cruise are always higher 4) audible detonation does occur if mismanaged (running too much advance with high compression pistons for example) 5) Fuel consumption during taxi, low speed flight (such as traffic pattern, or sightseeing at low+lean power settings) and during descent is markedly improved. 6) Fuel consumption during high speed flight is unchanged. (although there may be a slight loss of top speed)(impossible to verify) 7) Overall fuel consumption is reduced on the order of 5% for the folks I've dealt with. 8) Underpowered aircraft won't see much gain in fuel economy, as engines are often run at higher power settings, where timing advance cannot be used. The F1 rocket, for example, has 300HP, and can be thought of as a clipped wing RV-4, plenty of power. He was able to see significant gains in economy. But at uncomfortable altitudes, and modest power settings, while pushing CHT limits. He has a nifty way to adjust ign timing in flight with a simple knob. Guess where that timing eventually ends up? At modest settings that mirror a 25 degree magneto setting. (yes, his engine is tightly cowled, and CHT's are a constant concern) He claims he can get down to 12-13GPH at 200MPH at 12,000 feet, with a CHT of 420. Not exactly comfortable. The Velocity on the other hand, runs it's IO-360 angle valve engine very hard, at 12 gallons per hour in cruise. He shows zero improvement in cruise fuel economy. But, gains in other areas of flight, taxi, pattern, slow speed/lean and descent. My personal feeling: I love the electronic ign systems. For the smoother operation, quick starting, and differing modes of failure. (one mag, one elec have different modes of failure) AND, for the slightly improved fuel economy. I'd guess return on investment is not the way to look at elec ign. Just don't expect more power or significant gains in economy. One regular route we fly at 7500-9500 consumes 40-41 gallons, mags or elec ign matters not on that trip.
-
M20F Vs. Cessna 177RG........Thoughts?
cujet replied to mschmuff's topic in Vintage Mooneys (pre-J models)
I own and fly a 177RG for reasons of easy access. It is a very responsive, comfortable, roomy and capable aircraft. There is a loyal following of owners, who keep the RG's a long time because they love 'em. They are good aircraft, inexpensive, easy to maintain and most/all of the gear/leak/door issues are in the past, fixed by service bulletins and updated parts/practices. The gear is much tougher than it looks too. It's spring steel and will absorb a badly balked landing without any issue! (ask me how I know) . I can eventually reach an absolute maximum speed at 8500ft cruise of 143Kts TAS. But that takes effort, fiddling, CG management and so on. It certainly can't be counted on. Lean of peak operations drop the TAS to the 125Kt range. I plan for 135Kts. FF is around 9.5GPH at 8500. A direct comparison between an M20F vs. 177RG is not easy to find. So, I'd like to post my thoughts, having flown both. We will agree that it's slower. But, how much and does it make a difference? The M20F, will cruise-climb from 3500-7500 feet in 6 minutes, w/full fuel/one occupant, for an avg rate of climb of 830fpm. The 177RG will do the same in 11 minutes, for an avg rate of 450fpm. And, the M20F will be going significantly faster over the ground doing so. At 100Lbs under max gross, a Florida based 177RG will make 11,000-12,000 feet, and be at the 50FPM ROC limit. Up North in the cool air, it will do better. A formation flight between the two clearly illustrate the performance advantage of the M20F, as it will out accelerate, out climb and out cruise the RG, leaving the RG in the dust fairly rapidly, with the M20F being out of sight in about 20 minutes. (ask me how I know that too) The 177RG is slightly underpowered for 2800 pound, max gross ops. To that end, additional power makes a huge difference in performance, and I would say it's "required". The tuned exhaust and/or IO-390 engine (10 more rated HP) bring the Cardinal into the realm of reasonable climb and cruise performance. It's one of those aircraft that is truly "just shy" of enough HP. Mostly due to the horrible Cessna exhaust and intake setup. With the IO-390 engine, my guess is that a 177RG will likely match a stock M20F in most performance aspects. With the Lopresti cowl, 360 engine and powerflow exhaust, 157Kts cruise at altitude is possible.