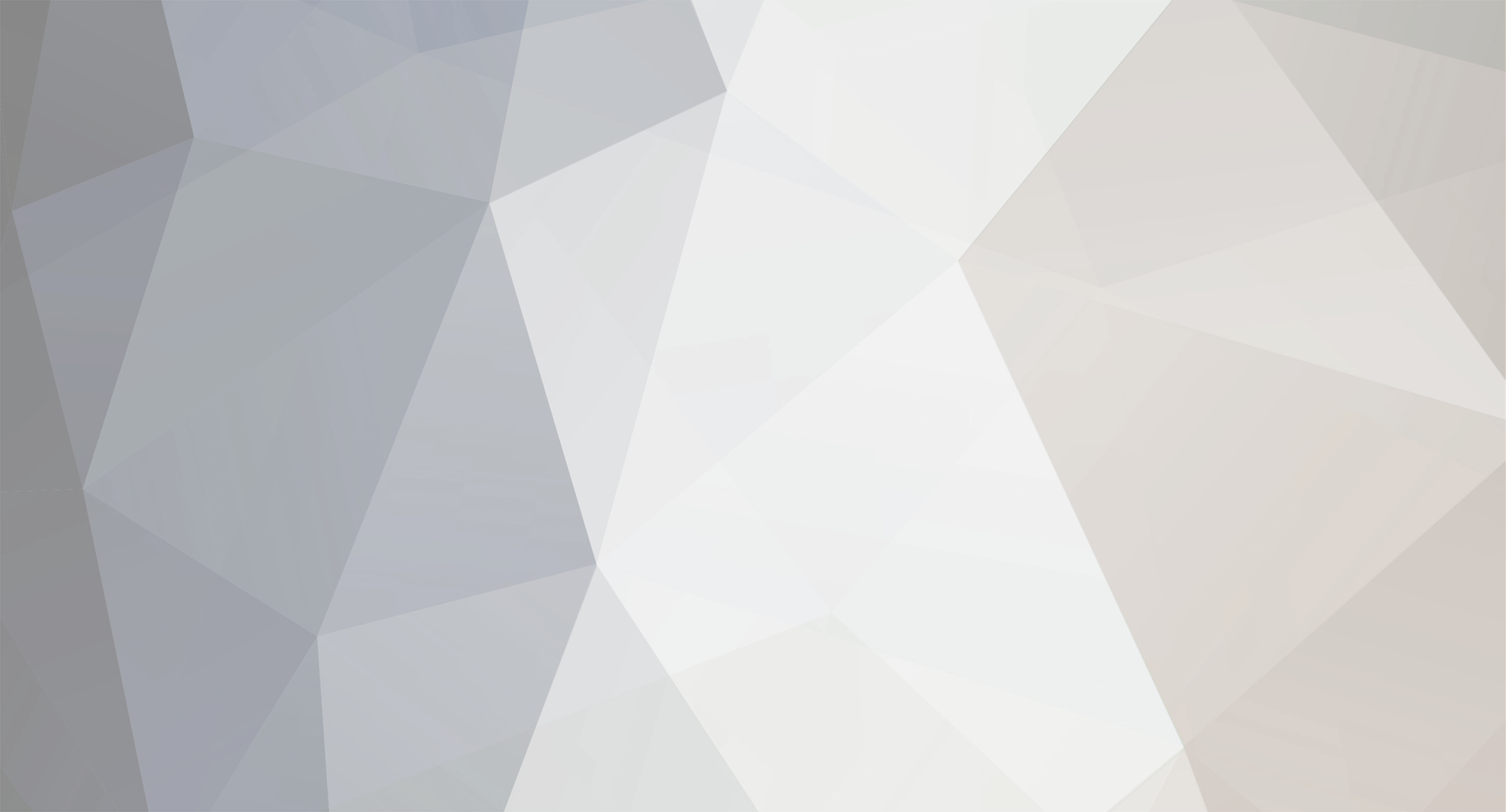
cujet
Basic Member-
Posts
302 -
Joined
-
Last visited
-
Days Won
1
Content Type
Profiles
Forums
Blogs
Gallery
Downloads
Media Demo
Events
Everything posted by cujet
-
Certification is different for heli engines. Also, heli engines drive a large HP consuming cooling blower. Heli engine certification requirements include sustained operation at 105% and 110% of rated power. To achieve this, the ratings must be "adjusted". As you'd never be able to wring 220HP out of a 200HP (really 195HP) IO360 angle valve Lycoming under any conditions. But if it were de-rated to 170, you could then get the 17 additional HP necessary for the 110% certification requirement. The higher RPM is also driven by both practical requirements and certification. As 70% power must be available at 70% RPM, and it must be available at an altitude above sea level. From a practical point of view, any helicopter must be able to hover out of ground effect at 5000 feet, or 25 inches of manifold pressure. In real world terms, similarly built heli and airplane engines make the same HP. EDIT, Note: the higher RPM results in reduced volumetric efficiency. Meaning the torque curve declines as RPM increases. This leads to a favorable characteristic of increasing torque as RPM decreases from redline.
-
An FAA type certificate, (and if we want to go off topic, AD compliance) absolutely indicates that an aircraft design is deemed airworthy and has a level of safety acceptable to the administrator. No such compliance requirements exist for amateur built, experimental aircraft. In fact, an argument can be made that AD's don't apply to experimental, amateur built aircraft. Also of note, I think you'd find impressive build and component quality if you disassembled a 737 Max. The fact that a problem exists in any given aircraft is nothing new. Again, the FAA uses the AD system to address significant issues. In fact, despite what people think, with a few notable exceptions, amateur built, experimental aircraft have a horrific safety record, often far worse than the 5 to 1 ratio noted above. The RV series of aircraft tend to bolster the statistics, along with various "Cub" kits. In other words, the farther you get away from an RV-6 with a Lycoming or a Cub kit with a Lycoming = big time risk. Let's look at the positive side of this. Mooney and Cirrus aircraft exist and are popular because they are a good blend of both fast and safe. Both have good stall and spin recovery characteristics. Traits that require larger and thicker airfoils that cost some speed.
-
I'd like to caution against any experimental or amateur built aircraft. The temptation to go fast often overpowers our natural tendency to remain safe. I've been an enthusiastic aviation professional for over 30 years. Yet friend after friend is lost. In the last 2 years, I've lost 3 friends to crashes. Despite the claim that it's pilot error and failure to maintain control, a mechanical was involved in each and every one. The 5 to 1 crash rate of experimental aircraft puts the operation into the very high risk,,,, actually it puts it into the "test pilot" category for "every flight". And many times worse than riding a motorcycle. If you want to go faster, pay the money and get a type certificated plane, of known high quality, that goes faster. If you can't afford it, then go slower. But please don't take the risk.
-
At first annual, have found illegal engine modifications
cujet replied to hmasing's topic in General Mooney Talk
Exactly! I'm Director of Maintenance for a high end corporate flight department. I performed my own careful pre-buy which included interior removal, I found a large number of items, which reduced the price by $12K thereby making the purchase attractive. Even so, after I got into the project an impressive number of additional squawks were found. From cracked brackets, to wrong hoses, to automotive parts installed last century! How many items were missed by my multi day pre-buy? I'd say that in the end, it exceeded 50%. Many people really don't understand that older aircraft do tend to accumulate hidden problems. Short of complete disassembly, many of those issues will remain hidden until they can't be missed. A good example is an aluminum fuel line with internal corrosion. -
A little bit off topic, but still related. The ability to make the originating airport with a climbout engine failure (outside of the airport footprint) remains important. With enough HP, a properly executed climbout can result in the ability to glide back to the airport with little risk. I've practiced this a number of times, as departure from Sebring, FL after midnight is risking a swamp landing and is likely not survivable. We tend to concentrate on the impossible turn, but engines can fail at any point, and failure of an engine at full power, is not limited to the immediate airport area.
-
I use MT props on our experimental Extra 300L aircraft. Including a very cool custom built 4 blade unit. However, they are wood, subject to trailing edge damage and time consuming/exceedingly expensive to repair. Just a tap with a tow-bar on the trailing edge will scrap a blade. Same goes for a kicked up rock or debris. What would cause a ding on an aluminum blade will scrap an MT blade. While there may be online dispute as to performance loss with an MT, due to the thick blade shape, there is no question in my mind. Replacement with just about anything else yields an increase in cruise speed.
-
Those are some serious bragging rights! The fastest I've ever been was just over 750MPH, and that was going 530Kts TAS with a wicked tailwind.
-
Very well said. While politics is often a subject to be avoided, it's relevant here. My aviation dealings with the state of CA have been universally awful. When it comes to any of the many CA confiscatory policies we've run afoul of, I can sum it up in one typical CA statement: "we have investigated ourselves and found that we've done nothing wrong" In other words, not once have we prevailed in court, despite clear evidence they are wrong. Nor, as a FL based flight department, have we ever been able to avoid payment of fees, pro-rated taxes, or other charges on any of our aircraft. If you are going to operate in CA, make sure you have money to burn. My suggestion, stay out of that wasteful, confiscatory and wildly insane state until you fully understand what the charges will be. Our flight department is based in West Palm Beach, FL. We purchased a brand new PC-12 (let's ignore the G550, EC135 and other toys for now) and California came after us for sales tax, as we took an extended (summer) trip to CA within 6 months of purchase. Unfortunately, a $5M plane is heavily taxed at 9.25% in San Jose, CA. After a prolonged and very expensive legal battle, we ended up paying the state of CA over $460K in tax for that trip. A trip that consisted of 3 landings in the state of CA. We've not been back. Oh, and for those who don't know, payment is made to the "California state board of Equalization". Bury your head in the sand and avoid aviation politics at your peril. Or, if you prefer, while flying over LAX, open your DV window, and every 2 minutes, release a $100 bill into the airstream. TLDR: CA politics = unfair taxation and unfair courts.
-
As mentioned above, perform the compression test on a hot engine. Consider purchasing your own $99 compression testing device with a master orifice such as the ATS brand 2EM, (master orifice to determine leakage rate prior to use, a Continental requirement but always useful) and a 0.040 orifice. Insist on the use of your device every time , and not some random, different, beat up, abused and non calibrated unit. You have far less assurance of repeatable results using any other method. One quick and dirty test is to simply pull the prop through a full 2 revolutions, feeling the compression of each cylinder. A low compression cylinder will be self evident as the prop will pull through that cylinder's compression cycle with relative ease.
-
Remember, prop efficiency is roughly equivalent to a gain in HP. Quote Hartzell: "Generally, it requires a large increase in propeller efficiency to produce a small increase in cruise speed on an aircraft" https://hartzellprop.com/faq/technical-questions/ However, as many owners of older airplanes now know, some original prop designs were not all that great and large increases in prop efficiency (for our discussion that's 2% or more) are very possible. It's hard to find published prop efficiency numbers. But most conventional props are, I believe, around 80% efficient in cruise. The more modern aircraft do choose more efficient props and it's one part of the optimization strategy for better speed. As I keep mentioning, it's easy to add an antenna or two and increase drag by 6 pounds. It's exceedingly difficult to get 6 pounds more thrust at altitude without a fuel burn penalty.
-
Partial throttle operation increases engine pumping losses. The engine is performing work creating a lower manifold pressure behind the throttle plate. Note: diesel engines have better efficiency due to compression ratio, diesel fuel has more energy (as much as 18%) per gallon AND there is no throttle plate to increase pumping losses. It's one reason diesels burn so little at idle (and create little heat at idle) Our aircraft engines when well tuned and flown lean of peak, can achieve world class BSFC (HP per weight of fuel consumed) (remember aircraft fuel is purchased in gallons but it's the weight that matters) Partial throttle operation increases the engine's workload and decreases engine efficiency.
-
From a practical point of view, aerodynamics, or more accurately, drag reduction is how speed is achieved. Whether that drag reduction is a function of altitude, engine cooling drag, lift related induced drag, parasitic drag such as fuselage shape/frontal area or antenna/accessories drag. It all matters. The fastest designs address optimize all. The Lancair with IO550 can cruise at 275Kts due to very small frontal area, low cooling drag, a sleek fuselage and minimized external drag inducing antenna and a sleek, small wing. Adding HP and it's related fuel burn is not likely to be the ideal way to achieve a given speed. The exception is adding HP at altitude. The interesting thing that happens with normally aspirated engines is that altitude related HP loss (lapse rate) is, within limits, matched by the reduced drag up high. With many normally aspirated aircraft, the cruise speeds possible at low altitudes are not all that far off from the speeds possible at higher altitudes.
-
As a general rule, a centrifugal compressor has a fairly wide operational range outside of the surge margin. There are certainly times the compressor may not be at peak efficiency, never the less, it will be quite effective. It's good to note the compressor's efficiency is generally between 65% and 75% and unless it's a very modern turbocharger, will never exceed (around) 78% efficiency. Typically the surge margin is located near the 60% efficiency line. Think about what happens making 300HP: At sea level, the turbine/compressor spins at a specific speed to compress 30 in/hg to 42in MP. Let's call it 44,000 RPM in our theoretical model. As you start the climb, HP remains at 300, and manifold pressure remains at 42, yet the turbocharger's RPM increases markedly, compensating for air density. 50,000+ RPM. At 28,000 feet, the turbocharger is now working amazingly hard, spinning nearer to it's 77,000 RPM operational maximum, compressing 13 in/HG to 30 in. The one on your 305 Rocket must perform outside the surge margin at any load and at any reasonable altitude. Fortunately, centrifugal compressors have wide operational ranges. Going up or down a size or two is often quite possible to achieve tuning goals. It's also good to note that compressor efficiency is not a major factor in overall system performance. It's just a measure of the efficiency of a single component. There is not much power to be gained by switching from a compressor operating in the 65% efficiency island and sizing one to be operational narrowly centered on the the very best 80% island. The pic below is not an aircraft part, but it illustrates the operational range well between 60,000 to 140,000 RPM and pressure rises as high as 3.5X
-
TailBeacon ADS-B vs. Anticollision Light
cujet replied to SpamPilot's topic in Modern Mooney Discussion
SP, that would be a no-go, as removal of the tail strobe would not be compliant and I can't think of any options right now. The next easiest answer might be the KT-74 hooked into your WAAS GPS. If you have a KT-76 transponder, it's nearly plug n play. -
The idle RPM would be my first guess. However, it's good to remember that low wing aircraft always have low pressure in the fuel lines when the boost pump is off. This can lead to bubbles. Imagine what would happen if there is a tiny leak that introduces air?
-
Time to get a new cell phone. Need suggestions
cujet replied to nels's topic in Miscellaneous Aviation Talk
I just upgraded from the iPhone 8 to the iPhone Xs max. A few points: 1) It's not too big, although I was really afraid of this. 2) The ultra high resolution screen works amazingly well with VR glasses. Yes, you can still see the pixels, but they are quite small and so VR games are nowhere near as fake looking. 3) Foreflight is lightning fast on it and will display the horizon and synthetic vision and can scroll around to view 3d traffic with ease. I have not seen the airspeed and altitude tapes on the phone's display though. The screen is also big enough to be useful, which my standard iPhone 8 was not. 4) The speaker is considerably louder and better. Useful for driving and talking. I've been able to place the phone over my car's speedometer and talk with clarity. -
Ovation pilots, can you flight plan a trip for me?
cujet replied to cujet's topic in Modern Mooney Discussion
Hahaha, after 10 years of doing this, I'm not so sure about that dispatch rate, errr, ahhh, arrival rate. HPN has terrible fog, maybe that's why they call it "White Plains". JetBlue recently dropped me off at JFK, as HPN was fogged in. $140 uber ride to HPN. JetBlue averages 3x/year fail rate for me. I average 1 to 2. At least when I fly my plane, I can leave at times chosen by me and not subject to some schedule. -
Ovation pilots, can you flight plan a trip for me?
cujet replied to cujet's topic in Modern Mooney Discussion
I'm currently using JetBlue to do the trip. Seems the Ovation is competitive in every way. 0.5 hour drive to PBI 1 hour ++ early to clear TSA 2.6 hours flight time to HPN 1.4 hour drive to SWF. -
I'm considering upgrading into an earlier Ovation or a 305 Rocket. I'd like to see what a real world flight plan looks like from SWF to F45. (NY to South FL) From a practical point of view, I need O2 at altitudes lower than the normal person might, , with true need starting at about 10,500, and by 18,000, I'm on a mask at 100% oxygen flow just to maintain 97%-98% O2 sat. So while the 305 Rocket is really tempting, I cannot use it's full speed potential. At the altitudes I'd fly, the Rocket may be limited to 205Kts or so. I've flown the 305 Rocket, but not the Ovation. So, I'd really like to see what a real world trip would look like. Thanks.
-
Bendix King offered an LCD conversion for the KX-155's that was under $2K. I recently tried to get that conversion as my KX-155 display was behaving horribly. Interestingly, Palm Beach Avionics found the real problem with my 155, a bad capacitor, which was a fraction of the cost to replace. It seems my display was not the issue after all. I've come to understand that the display drive circuitry is one possible cause of display failure and is very often misdiagnosed.
-
Ground Stoppage going to Florida after Xmas
cujet replied to Yooper Rocketman's topic in Miscellaneous Aviation Talk
You can imagine just how intolerant a Billionaire can be when told to remain on the ground for hours. We use just about every trick possible to get in the air including flying a G550 VFR. I clearly understand you don't want to stop, but that may be exactly what is necessary to make it work. Plus it's always nice to get out and stretch legs after a few hours. Unfortunately, we stopped somewhere unplanned due to awful NY weather and promptly hit the wingtip on an unseen fence post. Even so, 22 years down the road, it's worked out far more often than not. -
I was talking about them wasting my time. It's just insult to injury when they charge too much.
-
There is a very clear reason Sheltair SAV gets our G550's fuel/ramp business and not Signature SAV. It had everything with how I was treated, the willingness to provide fuel at a great cost and fantastic staff. The relationship has been superb and they go out of their way to avoid introducing a delay. Various other FBO's need some serious remedial training. I don't need a fancy lobby and a babe at the front counter. I need to get through the gate and get going. What actually happens is that I end up waiting to pay my bill and waiting for a busy line guy to escort lowly 'ol me to my antique aeroplane. Thank God I had the presence of mind to ask for fuel 3 days earlier, otherwise I'd be waiting for that too. It's great that others have had perfect experiences everywhere they go. It could be that our needs are vastly different. I'm not that demanding jerk of a guy, as this is my world. But waiting 30 minutes for fuel at F45, when nothing is going on, and another 10 after fueling up, for the fuel truck driver to get the upload numbers to the front desk is, quite simply, bad behavior.
-
Ground Stoppage going to Florida after Xmas
cujet replied to Yooper Rocketman's topic in Miscellaneous Aviation Talk
Somehow, I doubt the Lancair altitudes are saturated. -
Ground Stoppage going to Florida after Xmas
cujet replied to Yooper Rocketman's topic in Miscellaneous Aviation Talk
While this may have no bearing on the situation, experimental aircraft may be last on the list of priorities. We operate an experimental EA300L and landing at MIA has been problematic. As they simply refused to let us in the Class B airspace. The suggestion to file to elsewhere is what we do in our G550 corporate jet. Then divert at low altitude. It also matters where you depart from. Guessing you'd have little trouble flying to JAX (or Valdosta, GA) , then VFR to Spruce Creek. No joke, we've been subject to many hour NY ground holds so often, we fly our G550 VFR at 2500 feet, from HPN to SWF (nearby Stewart, NY) . Where we simply file to PBI, SUA (Stuart, FL near PBI) or Pittsburgh :0 (whatever works) and go on our way. Sure, we've had to land at a nearby destination. But we save hours. Nothing like "free and unrestricted travel" in the good ol USA. That is until our superiors simply say "request denied".