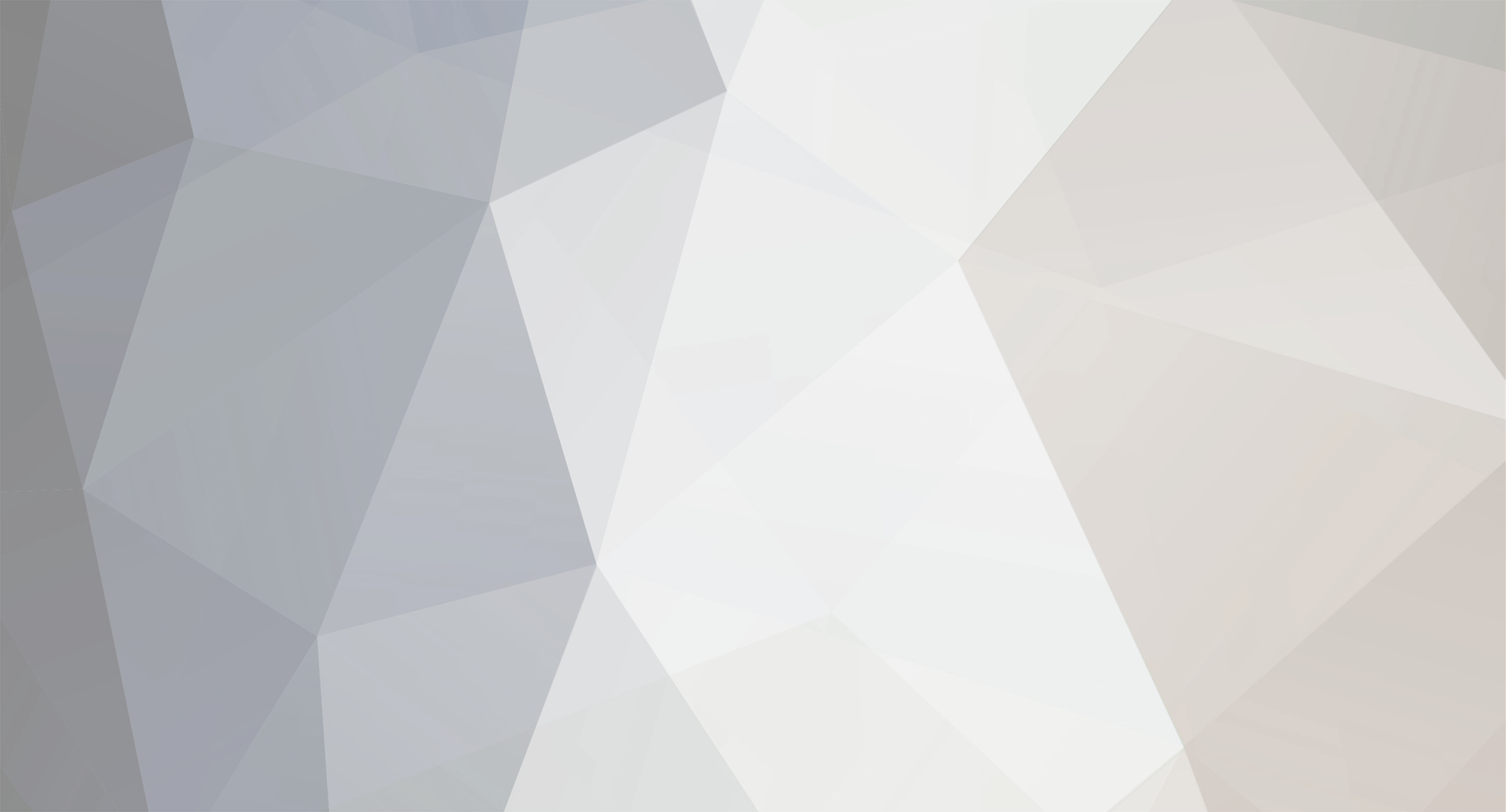
wpbarnar
Verified Member-
Posts
127 -
Joined
-
Last visited
Content Type
Profiles
Forums
Blogs
Gallery
Downloads
Events
Store
Everything posted by wpbarnar
-
We are exploring having an Instrument Procedure developed for the airpark that I live in. Hughes Aerospace is one of the big players for developing Special Instrument Procedures for private airports, airlines, EMS services, etc.... Does anyone know of other companies that can provide a similar service? Google has not been very helpful. Bill
-
It may be obvious to you but it is clear as mud to me.
-
The approach list a DA for the LPV and LNAV/VNAV of 359’ and 378’ respectively. It also includes a MDA for the LNAV/VNAV of 500’ So can I go down to the MDA?
-
What does LPV and LNAV/VNAV LINES OF MINIMA NA mean? This was contained in a NOTAM for the RNAV 32 and 24 at KAAF. I don’t know what “lines of minima” are. Bill
-
@carusoam's request I am sharing a data dump from a Garmin G3X as a example of it ability to capture engine and flight data. The file is in Excel. The file is from a short flight I took yesterday. I departed my local airport, clicked on the A/P and let it navigate to a couple intersections nearby. At 14:19:42, I clicked off the A/P for a little sightseeing and play. At 14:30:27, The A/P went back on to fly a Garmin generated visual approach back to my home base. Bill P.S. yes the pitch, roll, and G data is real during the play mode. Don't freak out this is not a Mooney. log_20210224_L31_exercise.xlsx
-
Have you compared the price of the Garmin engine monitor vs a JPI? There may potential saving as you can incorporate the Garmin engine monitor into the 10” G3X. I only have a single 10” display and my engine monitor is incorporated into it. The “normal” display for engine monitor is a narrow vertical column displaying RPM, MP, OIL PRESS, OIL TEMP, & Fuel. I split the screen to see EGT, CHT, Fuel flow etc for leaning. i am not concerned about lack of redundancy of not having a dedicated engine monitor screen. During practice IFR approaches, I will sometimes cover the G3X and fly the approach with the GTN and G5 only. You don’t need RPM and MP to safely execute an approach. Additionally if you are a data geek, I think a data download from the Garmin engine monitor is way cooler than a JPI. In addition to all the engine data, all the flight information is captured also. IAS,TAS,Alt, Density Alt, pitch angle, roll angle and on and on. The spread sheet contains 102 different columns of data, recorded every second. Bill
-
If you are only going with one G3X screen, the 10” is much more versatile than a single 7” in portrait mode. I frequently use the capability to split the 10” screen into two screens and capitalize on the functionality of the G3X system. The two screens on a split 10” still are large enough to remain useful. Bill
-
I experienced the exact same failure and intermittent contact in my Encore. Bill
-
The Acclaim he is looking out has the opposite. The rear bulkhead or flight time is greater than the engine time on the G1000 by a significant amount. @OneAuburnFan what do the log books say? Airframe and engine time should both be noted. Did the difference slowly evolve over time or something else trigger it. Bill
-
The cross over from the mains into the aux begins at approximately 50% capacity of your main tanks, at least that was the case in my Encore. (37.5 main & 15 aux) If I filled my mains and added nothing to the aux, given time the mains would equalize into the aux and the main tank level would decrease indicating about 18 gallons. The fuel level gauge would remain there until the aux was empty. I suspect there is minor differences from airplane to airplane depending on the installation. You can determine your crossover point by very slowly adding fuel to the main and observing the aux for the first indication of fuel in the bottom inboard side of aux. I emphasized slowly as I could easily fill my mains up with very little going into the aux until they sat for a few minutes. Knowing the actual amount per side was a challenge while flying. If the indicated amount was above 18 gallons, then that wing contained the indicated amount plus some quantity in the aux. When potentially starting out with 52 gallons per wing, only when the indicated amount drops below the cross over point does the fuel gauge actually become representative is the downside of the Monroy system. An accurate fuel totalizer can be very beneficial. Bill
-
I have a adequate amount of time in the high teens or low 20’s. to comment Maintaining warm enough engine temperature was never an issue. Thin air does not transfer heat well. I have cracked the cowl flaps at 18K’ and -10C to maintain temperature. When flying in the low FLs, I was always more concerned about ice in the fuel (and my PO2) than anything else. I can’t imagine the oil in the oil cooler congealing while attached to an operating engine. Bill
-
I chased oil leaks on my TSIO 360 so I can speak from experience. The rocker box covers (all 12 of them) are prone to leak. They are easily distorted if over tightened, especially with silicon gaskets. If they are not dead flat on the mating surface, they never will seal. I replaced 10 of mine to stop the seeps. The push rod tubes also are prone to leaks. They are a pain to replace. If you ever have the exhaust manifold off, take the opportunity of easy access and replace the seals on any suspect tube. I also suspect you have a magneto gasket leaking as the area around oil filter appeared wet from drips above. Bill PS. IMO. The G3X/G500 is hard to beat. I have about 100 hrs with that combo. (Not in a Mooney). The experience is in a much poorer IFR platform airplane . I can only imagine how sweet that combo would be in a K model.
-
This may sound strange, but were your panel lights on when the oil pressure indicated low? If the instrument case ground is poor on the ship’s gauges, panel lights can lower your oil pressure indication. The lighting ground is acting as the instrument ground. They don’t like the shared ground. Turn your panel lights on and adjust the lighting rheostat and observe the pressure indication. If it fluctuates with rheostat movement, the instrument ground is poor. It is easy for me to spend other people’s money, but you really need a engine monitor. I don’t have a lot of confidence in 30 year old ship’s gauges and IMO, K models need a engine monitor to be flown correctly. On a separate note, I would verify the safety wire on your oil filter is pulling in the correct direction. It appears to be threaded through the tab and pulling in a counter clockwise direction. Bill
-
They IRAN’d a MT prop for me. The cost were lower than his estimate and the prop was turned around in the time frame that he quoted. (3 weeks). I Would definitely use Jimmy G again. Bill
-
Please note in Rick’s original post he indicated that the gear relay circuit breaker tripped, not the gear actuator. I think everyone assumed he has a problem with the gear actuator motor, which may not be the case. Bill
-
I had the same experience with BAF and Macroair. Total price from Hunter (fan, shipping and taxes) was $3200 for their 8’ Their fan kit was complete and included everything necessary for installation. I installed it it in a 42 x 34 T hangar. More than adequate. There is air movement everywhere in the hangar. All my hangar neighbors are envious. The contact info below is for the sales person I dealt with. Don’t know if she is still there or not. Bill KALEIGH WALKER│ 2434 ATRIUM WAY │ NASHVILLE, TN 37214 P: 629.333.7086 │ C: 615.917.2807│ F: 615.232.3894 INSIDE SALES – INDUSTRIAL/COMMERCIAL DIVISION kwalker@hunterfan.com
-
I installed a Hunter Industrial fan in my hangar. Their industrial line manufacturers HVLS (high volume low speed) fans similar to Bigass or Macroair. After trying to deal with Bigass or Macro directly, I found Hunter much more willing to work direct with the consumer. Bigass or Macro kept trying to direct me to one of their “installers”. Hunter provider better technical support and sold direct to me. Not cheap, but worth the money to me. Bill
-
Agree with Pete. Roll 75+ degrees of bank, and pull back on the yoke. Done correctly pull until you feel buffet. The instantaneous sink rate will be higher but the time in the turn will be much less, hence less altitude lost. Bill
-
I have had good success with 3M Polyurethane Tape 3874 protecting the leading edge on the stabilizer of my tail wheel aircraft. https://www.aircraftspruce.com/catalog/cspages/3m8674tapeft.php Not the easiest thing to install without experience but doable with some practice. I was fortunate enough to attend a forum at Oshkosh put on by 3M and picked up some helpful tips. Mine is applied over a good finish with no existing nicks or chips. It is clear and does not alter the paint color beneath it. Applying the clear tape over an existing chip may look worse than the existing chip. Experiment with a small section before tackling a large area. Trying to do the full length of the leading edge on your wing in one continuous piece would be extremely difficult for an “amateur”. You may want to start with a smaller section starting at the wing root. Most of the damage seems to occur in the prop wash area. I replaced mine after it had been in service 12 years. It looked pretty bad at that point but I think you could expect 8+ years before it gets too cloudy. Removal was not too difficult as 3M makes some adhesive solvents for that purpose. Although the old tape looked bad it was still protecting the finish underneath. The original finish looked excellent after the old tape was removed and new tape was applied. The legality of applying it on certificated airplanes is like flying lean of peak, not as controversial but not everyone agrees. Bill
-
Instrument/avionics tinnerman nuts??
wpbarnar replied to ragedracer1977's topic in Avionics/Panel Discussion
Try https://www.gen-aircraft-hardware.com/template.asp?pagename=nutclip They indicate they can get corrosion resistant versions as a special order. Don’t know what quantity that would require ordering. They have been very helpful when contacted on the telephone. McMaster Carr offers snap in nuts in stainless. Bill -
Trouble shooting Stec 30 Autopilot
wpbarnar replied to wpbarnar's topic in Avionics/Panel Discussion
Yes, the Lateral indicator within the Aspen HSi -
I have a Stec 30, GTN 650, and Aspen with GPSS. Although the airplane gets flown weekly, the autopilot is not used as often. This past weekend on a trip, I discovered the AP: 1) with AP in track mode {high or low) it will not track the CDI. Doesn’t matter if the GPS or VOR is driving the CDI, the AP will not track. Not even attempt or hunt, the airplane will circle to the right. 2) in the heading mode, there is now a 10 degree error to the right. If the desired heading is 180, need to set the bug on 170. The 10 degree offset is consistent all the way around the compass. Seems to hold heading well , just 10 degrees off of what the bug indicates. 3) in the heading/GPSS mode, no problem. The desired track and actual track are within 1 degree. 4) altitude holds OK as normal Where is the problem? 1) autopilot 2) Aspen 3) not enough information to tell I am thinking it is something in the output of the CDI and heading bug from the Aspen. From what I understand the Aspen GPSS is in a separate modular which performs the digital to analog conversion from GPS and feeds it direct to AP. Not 100% on this. Any other suggestions how to pinpoint the problem area? Bill
-
I don’t have a problem with wheel bearings or seldom see evidence of grease contamination. I could have taken if it ain’t broke don’t fix it philosophy but decided to switch to molded seals as I needed new felts and this seemed like a better idea. As it appears that I am the only Mooney Space adopter so far, I will make it a point to post a comment next time I remove a wheel, especially given @philiplanecomments on the aluminum spacer wear. Bill
-
My opinion is to use Gliem or Sheppard Air for your written exam test prep. Don’t fixate on your test score other than passing. A perfect written score will not keep you from doing something dangerous in the real world. The key is the quality and experience of the instructor. There is a difference between a professional flight instructor and someone building time in order to get hired by an airline.... Fly as much actual IFR as possible during your training versus under the hood. The whole experience will be challenging and rewarding. Bill