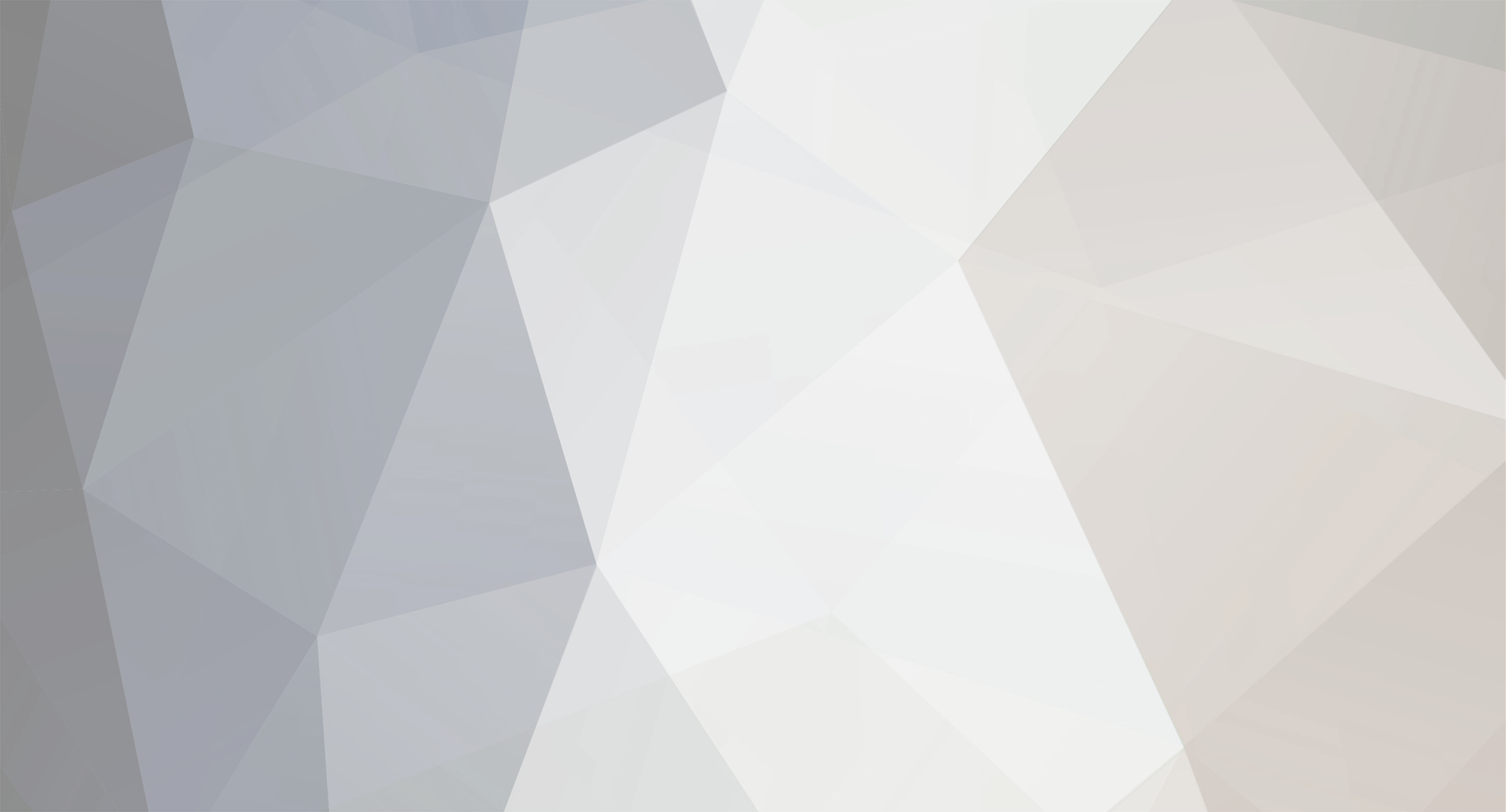
jlunseth
Basic Member-
Posts
3,751 -
Joined
-
Last visited
-
Days Won
9
Content Type
Profiles
Forums
Blogs
Gallery
Downloads
Media Demo
Events
Everything posted by jlunseth
-
GAMI is General Aviation Modifications Inc. They sell tuned injectors. https://gami.com. One runs a lean test that is described on GAMI’s website. The idea is to determine at what fuel flows each factory injector causes its cylinder to hit peak EGT. With that information, GAMI sells you a set of injectors that brings the range of fuel flows at which peak is reached to within 0.5 GPH or less. This helps the engine run more smoothly. It also is very helpful if you want to operate your engine lean of peak.
-
RNAV TAA sector altitudes. Minimum or mandatory altitudes
jlunseth replied to AIREMATT's topic in Miscellaneous Aviation Talk
Well, ok, I looked at it, but it does not say that when ATC assigns you an altitude you can freely deviate downward from it so long as you are within a TAA. It allows the controller to issue a clearance without an altitude restriction, it does not authorize a pilot to break one, and in my example they did issue an altitude restriction. They said “maintain 4,000.” So am I allowed to go down to 3,000 assuming that is the TAA minimum? If they simply issued the instruction “cleared the RNAV x approach” I would understand it, I am within the TAA, cleared for the approach and can follow the chart. But that is not the instruction they give, they invariably assign an altitude. TAAs are pretty big, that would mean that 30 miles out from the FAF I can descend to 3,000 if want, notwithstanding the “maintain 4,000.” Also, virtually every time I have received that instruction in connection with an RNAV I am already inside the 30 mile TAA or whatever the distance restriction happens to be. I appreciate the reference though, it is helpful. -
RNAV TAA sector altitudes. Minimum or mandatory altitudes
jlunseth replied to AIREMATT's topic in Miscellaneous Aviation Talk
Well, the better question is when can you descend to the minimum sector altitude in light of ATC’s instructions. My experience is that they always assign an altitude until you receive something like “Maintain 4,000 until established on a published segment of the approach, cleared the RNAV x.” But is a sector a published segment of the approach? I don’t think so, the way I understand it, published segments means getting on one of the course lines, the TAA is just an area. So in practice the TAA minimum altitudes mean very little, I really don’t ever remember having been allowed by ATC to fly the TAA minimum, I have always been assigned an altitude until on a published segment. As far as “shall” and “may” are concerned, one factor not to forget is the nature of the document in which the word appears. If in a regulation or statute, it is binding. But the AIM is not supposed to be a binding document. What it is in that regard is a little murky. An AC or an SB are advisory. Yes you would be in big trouble if you did not follow it and an accident resulted because the document would be pulled out as evidence of due care. But they are not binding in the way a regulation is. And as far as regulations are concerned, we have an unfortunate legal doctrine called Chevron deference that basically says that a regulation means what the regulatory body says it means. So a reg can use “may,” but if the FAA says it means “shall” then it means “shall.” -
@Q That is good information about the standing wave. If Bob says he proved it, he did. The issue I have always wondered about in a non-tuned exhaust like the GB/LB is whether the successive cylinders along the log (my word for the main runner) receive the same MP. We have measured MP at the start of the intake, of course, let's just say its 30" for the sake of discussion, but whether it is 30" at each of the cylinders down the log is another question. I have reason to believe that at near idle it is not. The last two cylinders on each side do not "come alive" and start producing power until the engine is warm and powered up a little. The cylinders upstream seem to be stealing all the air. It is entirely possible that MPs vary not only along the log, but also vary differently depending on the measured MP. So at, say, 14", not much pressure gets to the last cylinders because it is being stolen by the first cylinders, while at, say, 36" there may be so much pressure in the log that it evens out to all the cylinders, and at measured pressures in between it may be mixed results. There are also no doubt standing waves produced in multiple directions along the log and the position of the wave fronts probably varies with measured MP. GAMIs (which I have) operate on a sort of "all other things being equal" basis. In other words, one runs a lean test at a certain MP, installs GAMIs that even out the fuel flows for each cylinder, and the thesis is that if the MP changes from the MP used for the test, it affects all cylinders more or less equally and therefore the GAMI's continue to provide the proper fuel flow to each cylinder to make the mixtures more or less the same. But what if the pressures at each cylinder intake do not increase or decrease equally with increases and decreases in measured MP, what if the wave fronts change, what if at high pressures relatively more air gets to the back cylinders than at low pressures, etc. This is all theoretical. My engine (Merlin and intercooled LB) runs well LOP at all power settings. But I have often wondered what is going on inside that untuned manifold. Beyond my instrumentation.
-
I just received this Notice from the FAA, I assume others have also. I know that these issues with the GFC500 have recently been the subject of at least a couple of other threads. Just putting the Notice up so everyone sees it: Garmin GFC 500 Autopilot Notice Notice Number: NOTC2741 Garmin has identified an issue with GFC 500 autopilots with optional auto trim installed in certified, experimental and Light-Sport Aircraft, including certified installations installed with optional GSA 28 pitch trim in accordance with Garmin STC SA01866W. This issue may result in an uncommanded automatic trim runaway when the autopilot is first engaged. This condition could result in a sudden and significant deviation from the intended flight path. Garmin Service Alert 22109 Revision A requires operators of certified installations to pull and collar the autopilot circuit breaker and placard the autopilot as “inoperative” prior to further flight. Operators may contact a Garmin dealer regarding reactivation of the GFC 500 autopilot with the optional pitch trim configured off in accordance with recommended service bulletin 22110 Revision A. Garmin is working to fix this issue for certified installations in a future software update expected in Q4 2022. Garmin Service Bulletin 22112 Revision A requires operators of Experimental and Light-Sport Aircraft to update system software or disable the autopilot or trim control prior to further flight. Service Alert 22109 Rev A is available at: https://support.garmin.com/en-US/aviation/faq/mZwVwMogJ09ZLIPJgWTBJA The recommended Service Bulletin 22110 Rev A is available at: https://support.garmin.com/en-US/aviation/faq/s7SeFk9oh96I8qVfjtNbV8 For non-certified aircraft, Service Bulletin 22112 Rev A is available at: https://support.garmin.com/en-US/aviation/faq/QFnVz92cFZ5AvovG4LF6l5 If you have any questions or comments, contact the Wichita ACO Branch at: Phil Petty 1801 Airport Rd. Wichita, KS 67209 (316) 946-4139
-
I have written about this before as you know Anthony, so repeating myself. I generally use two cruise mixtures, one LOP and one ROP. I am not really setting to TIT, I use TIT to manage my temps once I have my selected mixture put in. My LOP setting is 11.1 GPH/2450 RPM/34” MP. This is 71% power. My ROP mixture is 31”/2450 RPM/at least 13.3GPH. With the LOP mixture I keep the TIT at or below 1600 (continuous is 1650). I suppose I could run hotter but there are two reasons I don’t. One is that I just don’t want to be that hard on the turbo. Two is that my LOP mixture starts to generate too hot temps somewhere around 12-16k in the summer so I must go ROP, and when it does the TIT will creep up. So if the creep happens I want to have room between the 1600 I want to run at and the 1650 redline so I have time to detect and do something about it. If the temps creep up at the higher altitude I go ROP. With the ROP mixture I am watching CHTs, not TIT. If the CHTs start to climb because of OAT the cure is to increase the fuel as high as 14.5 GPH. The TIT while ROP will be lower than the TIT while LOP by quite a bit, around 100 dF, so there is not much reason to be concerned with it while ROP. One the other hand, the CHTs while LOP will be quite a bit cooler, generally, than while ROP so not much reason to be concerned with those, the temp to watch is TIT. My approach setting is 24.5 MP/2450 RPM/8.8 GPH. I use this to fly holds, instrument approaches, and on downwind in the pattern, or any other time I am not in need of full cruise speed. This is a LOP setting. In reality I target airspeed, I want my approach speed to be 120 kts. With gear down it is slower, around 90-100. The MP and fuel flow may need to be a little higher on some days, say in the middle of the summer, up as high as 25.5 and about 8.9 GPH. On final I keep the engine leaned out to stop the burble. The burble is the engine missing or making little power on some cylinder strokes, because of excessive fuel. You can hear when you have it leaned far enough, the engine should run smoothly. These settings may be a little high. Mine engine is old, way past TBO, we are waiting on a new one. In a turbo I can make up for lost HP because of engine age, with higher power settings. When I get the new engine I am going to have to revisit the whole thing.
-
Just to be on the button, for my 231 the transient TIT redline is 1725 and the continuous is 1650. The numbers may be different for the MB and SB engines in the 252. I believe the induction system in the MB and SB is better but I don’t fly one so not sure. It is true that the induction system in the 231 is just a straight pipe along each side of the engine that starts at the front and dead-ends at a flat plate at the rear end. There are three droppers, one for each cylinder, off that pipe. It would be conducive to a standing wave off that flat plate but that would work in a forward direction driving pressure back up the main log. I do not regularly run the engine full rich, I do that always for the climb but not at cruise speeds. It should be leaned to somewhere around 13.3-14.5 when ROP and around 11 when LOP at cruise. So I don’t question the idea that it is set to run quite rich with the mixture in all the way, but you definitely need that for the climb. Probably just technical, and purely my non-engineer opinion, but don’t think the standing wave drives fuel to the rear cylinders. The fuel is injected at each intake port, it is continuous injection so I am sure fuel briefly builds up there, but to drive the fuel from the forward cylinders to the back cylinders it would have to be evacuated up the length of the dropper, into the main log, and then back the length of the log and then down the dropper for the rearmost cylinder. It would run into the standing wave off the back plate that is pushing pressure back up the main log toward the front. I have GAMIs which are designed to provide a more or less equal mixture to each cylinder. I don’t doubt that without GAMIs the mixtures might be uneven between the cylinders. But I don’t think the theory that fuel is being driven from the intake port of the rear cylinders all the way to the intake of the front cylinders is much of a factor. The issue is just that, to get sufficient fuel to keep the cylinders cool at full power in a climb, the engine must be set up to run quite rich. So to fly at other mixtures and not in a climb it is best to lean the engine out, definitely. I would be concerned if at 33” and full rich the engine shuddered substantially. There is something going on that should not be. My aircraft has not ever done that. Generally, it is very smooth. Another issue is the final approach descent, which is a low power descent. We are taught in pilot school to put the mixture in full rich during that descent just in case we need to go to full power for a go around. However, the engine runs rough and burbles if you do that because it is way overrich. Best to keep the mixture well leaned so the engine runs smooth during that portion of flight. If you need to push to full power for a go around you definitely need to remember to push the mixture in all the way or you will see redline TIT very shortly.
-
go, no-go decision - only LIFR en route
jlunseth replied to dominikos's topic in Miscellaneous Aviation Talk
When making these decisions don't forget to look left, right and at your six. We tend to get fixated on the conditions going forward when a 90 degree diversion or even more is available to get out. Once upon a time I was flying home to KFCM from a destination down south somewhere, I think southern MO. I was on the back side of a large storm front that was moving eastward. The front extended from well down in MO all the way to MN. On the back side was not too bad, but there started to be some build-up without Tstorm activity (that was all well to the east). At first I just increased my altitude - until I got up to 21 or 22k and really did not have the capacity to go much higher (service ceiling is 24k and CA is 22,5). It appeared that going north as I had been, the cloud tops were just going to increase in height and I would reach a point where I would be boxed in, they were growing both in front and in back. What to do? Just then I happened to dip through the top of one and although it was mid-summer the temps at altitude were freezing, so in that short dip I got hit with ice. I radio'd ATC and asked for an immediate 90 degree diversion to Des Moines, which was about 60 mile away, but west was the one direction where the cloud tops were not growing. Landed at Des Moines, re-thought the whole thing, and took a different although longer route home. I guess LIFR does not worry me that much, although I certainly respect Marauder's story and experience. When overflying LIFR I like to be high up where I have choices about how to get down. I don't see LIFR as much different from over-mountain, over water, or night flight. They are all a little more risky in a single than at least some multi-engines. But like the icing story above, if I am going to do something like that I try to always set myself up with an out. ATC will give you that 90 to go 60 miles to the west if you ask. Don't let fear of what ATC might say stop you, they are there to help and always will. -
Well, I suppose its possible there is some kind of interference. The Merlin is a differential pressure controller, meaning it tries to maintain a constant difference between the pressure before and after the throttle. I don't know exactly how it measures this pressure difference or how it is installed, but it makes sense that there would be pressure sensors on each side of the throttle and perhaps that means there would be some mechanical interference in trying to install the sensor for the EIS, say, if it wants to go in the same spot as the Merlin "after throttle" sensor. It is not an outlandish question. But there would seem to be plenty of room to install a sensor after the throttle and the MP after the throttle is what it is. The Merlin's function is not just to fully close the wastegate and allow higher altitude flying than the fixed wastegate, that is certainly one effect of it but was not the principle purpose. The principle purpose was to stop bootstrapping. The lower deck fan of the turbo is driven by the kinetic force of the exhaust coming from the engine. If the pilot increases the MP, that increases the power output of the engine and also the force exerted by the exhaust gases on the lower deck fan. That causes the lower deck fan to spin faster, which causes the upper deck output to increase, which increases the MP more than the pilot wanted. That increase in MP in turn increases the exhaust output further, so up goes the MP some more. The pilot intervenes and tries to control it by reducing the MP again, and that reduces the exhaust which reduces the turbo output. Thus bootstrapping. The purpose of the Merlin was to even out those changes so that bootstrapping was no longer much of an issue. To do it the Merlin senses differential pressure across the throttle. I doubt that the Merlin reducing bootstrapping would have any effect on the Garmin EIS, but sensor placement might be an issue. Maybe where do two sensors go on the output side of the throttle?
-
Newly installed GI-275 software and GTN650
jlunseth replied to gmonnig's topic in Avionics/Panel Discussion
Not terrain, but I have a similar problem with FliteCharts fairly often. They take forever to load to the SD card on the computer because of the size of the file and at least half the time, I load the card at home, take it out to the aircraft, update, and find that the FliteCharts have not updated. I brought this up with Garmin while I was on the phone with them on a different issue and was told that FliteCharts is their largest database and sometimes does get corrupted when it is updated. Whenever it happens I bring the card home, reload only FliteCharts, take it back and update the aircraft, and it always works. So try that. My terrain was loaded by my avionics shop not long ago during a 275 install and it does not update often so I have not had occasion to see if that causes the same issue. -
Generally speaking, it is pretty hard for anyone to catch us without a turbine of some kind.
-
I fly quite a few Angel Flight patients and most of them have never been in a light aircraft, so we discuss this in pre-flight. Usually I wait until we are in the aircraft and show it to them at the same time I am describing the exits, etc. I also put it in my checklist and check it before takeoff every time. It becomes habit to reach down between the seats and verify that the latch is closed. Knock on wood.
-
Opinions wanted! CGR-30 P & C versus EDM 900
jlunseth replied to RDuplechin's topic in Avionics/Panel Discussion
One of the first things I did with my aircraft was to install a JPI 930. I can’t speak to differences between the EI and JPI instruments, EI was just coming on line when I did my work and JPI had readouts that I needed for my 231 that the relatively new EI did not. I have heard nothing but good things about EI. What I can speak to is location. We moved the 930 to the right side of the pilot’s panel, in the pilot’s normal scan and not way over on the co-pilot side. This has save my bacon more than once, any abnormalities become immediately apparent so I can do something about them rather than have a real problem develop. As to the 275’s, I have the dual reversionary 275s -ADI and HSI. They are very nice instruments. But for an EIS I would greatly prefer the larger display like the 930 and the much better definitionx. I had a JPI 700 before the 930 (old round gauge that fit a 3” hole), the def of the 930 is way way better. There gets to be quite a bit of information packed into a small space in the 275. -
I say this every time someone reports oil on the belly and using a quart every 5 or 6 hours. It is not always the right answer but it is the one most often overlooked. Contamination can block the oil quick drain from sealing. The operating engine then blows prodigious amounts of oil out through the drain and onto the belly. You think it is your breather but it is not. I got the wonderful experience of a full blown emergency descent/dive in IMC to make an airport 20 miles away with virtually zero oil pressure. The cause was a tiny but long sliver of plastic. The fix is two things. One, have your A&P drain the oil by removing the quick drain so all the little swimmers can leave through the big hole. Two, have your mechanic install a new “kit” in your quick drain which makes old quick drains seal again. My engine went from one quart every four to five hours, to one every ten or fifteen from that alone, and then we IRANd the engine and for the last more than one thousand hours I may or may not put one quart in between oil changes. The engine is over TBO so now I pretty consistently have to put one quart in between changes every 25-35 hours.
-
I fly a 231. My elevator hangs down. I flew a J before the K and noticed the two were different, the J elevator was level when the aircraft was parked. When I first started flying my aircraft I set trim at the takeoff mark but that required a strong pull to rotate. I flew with an experienced Mooney instructor at a Mooney PPP who also owned an K and he taught me to adjust the trim above the takeoff line. That pretty much is where it is after I land, so there is not much adjustment between landing and takeoff. My aircraft has a forward CG, sometimes I will fly alone on one trip and then cram two full size guys in the front seat the next trip, it is a good idea to trim up a little more for takeoff but if I don’t do that it is not a very big deal. Very shortly after takeoff you are going to go through some trim adjustments anyway when the gear and then the flaps come up. I am half flaps for most landings. Yes, full flap landings are serene in low steady wind conditions, but we don’t get that here very often and my experience with it is that practicing that kind of landing too much gets addicting, you set yourself up for failure the next time the wind is high, gusty, and 60 degrees from the runway, which is quite a bit of the time where I fly. 20 kts of wind is just another day in the Dakotas.
-
Straight replacement, new engine. The difference between a factory reman and new was much smaller than it has been in the past, and I did not want the downtime a field OH would involve. We ordered the new engine I think back in May and were told it would be nine months, so waiting for it to show up. Also the old engine was installed twenty years ago, not that that would make a difference to the case, but all the peripherals are getting up there. Bolduc really did a great job. Engine was very smooth out of the blocks.
-
Well, I agree with your statement, but just to be clear what drives the turbo is not heat from the exhaust, it is the kinetic force. You could aim a radiant heat source all day at the fan on the inlet side and not much would happen. But you could take it to Antarctica and blow -50 air through it and you bet it would spin. But your statement that the turbo extracts heat is certainly correct, that is one of the reasons the turbo runs hot, it absorbs heat from the exhaust. But the heat is not the force driving the fan, at least that is what the engineers tell me.
-
@brandt. To try to answer your question, whether an engine is operated LOP or ROP there is unburned fuel in the exhaust. It burns in the collector of a TCd engine and I am told by engineers that it burns hotter there than in the cylinder. The objective of either LOP or ROP operation is to slow the combustion cycle, which means of course that combustion is occurring later than at peak. So some unburned fuel will always be pushed out. For that matter some unburned fuel would be pushed out even at peak, or at the point where the combustion cycle is quickest which is somewhat after peak, just less of it than if the combustion cycle is elongated. There are three things that cause TIT to be higher than individual EGTs. The first is the measurement effect that has been discussed. The second is the secondary combustion event that occurs in the exhaust system. The third is that the exhaust flow is restricted at the turbine (it hits the fan), meaning higher pressure, and higher pressure equals higher temp. Of these, I am told that the measurement effect is the greater. I should hasten to add that I have heard different explanations of the secondary combustion event from engineers, one being the delayed combustion event that I described and the other being some kind of catalyzation of the exhaust gases themselves as opposed to burning of residual fuel. That is over my head, ask an engineer, which I ain’t. Lance is right this question has come up many times and has been answered many times by people smarter than me. Try searching on “secondary AND combustion AND TIT” and you will see some of the discussions from the past. I found one that I was involved in in 2016 and I know there were discussions even before that. None of it is very important. Simple is that TIT will be hotter than individual EGTs so you know what to expect on your monitor, but other than that it does not mean much. Just understand it is normal. Now if yours suddenly isn’t that should get your attention and lead to an immediate emergency landing post haste and a check of the connection between the collector and the turbocharger but that is another story.
-
There is also a secondary combustion event that occurs in the collector after the exhaust gas leaves the cylinder and is allowed to expand.
-
It’s an old story now but I had this happen nearly a decade ago, LB engine. A piece of plastic that was long and thin passed into the oil quick drain so when the mechanic closed the drain it did not seal. Blew most of the oil out over Lake Michigan and made an emergency descent and landing at London ONT. There was another “swimmer” in the oil, a piece of rubber about the size of a dime that was speculated to have come from a gasket when a cylinder head was mounted before I owned the aircraft. That appeared to have blocked the quick drain entrance hole so the engine got down to around 2 qts. Yes, there is some pressure at that oil level. It was 14 psi as I recall (instead of around 38), and when I throttle the engine to idle to try to save it in case I needed it to make the airport and tipped the nose over to begin an emergency descent, it dropped to about 4-6 psi. I had the engine IRANd at Bolduc at KANE. They did a superb job and I got many compliments from Mooney instructors after that commenting on how smooth the engine was. All that happened at around 1000 hours and the engine is currently at 2250 and will be replaced this winter. I will miss it, it has been a great running very smooth engine. Hope the new one can come up to that standard.
-
Sorry to hear.
-
Best upgrade option, GI 275, G500Txi or G3X?
jlunseth replied to fixandflysafe's topic in Avionics/Panel Discussion
I have the GTN 750 Xi and the dual reversionary 275 installed in my 231. I have always cherished putting in a G500, there are some benefits and some negatives. A benefit of the g500 is that, as I recall, it includes altitude pre-select. You would be responsible for the power setting, but the G500 would fly you to whatever altitude you chose and then level off. I am pretty sure it would do that with either the KFC150 or the GFC500, obviously you would want to check on compatibility with the 150. You can also install a GAD43e air data computer with the G500 and get information that you do not presently get, such as a real time read on the crosswind and headwind at altitude. The dual 275 is a pretty nifty setup, but the G500 would give you more screen space. There is a lot of information crammed into two small spaces with the 275. I am still getting used to it. The issue for me, though, is durability. We had a report of a “red-x” failure of a dual reversionary 275, it turned out the installation was not dual reversionary. We just recently had Don Kaye’s episode where he lost all power to the instruments because of a loose connection, that thread is recent and you can see more detail there. In my mind the problem is that when you install all these toys and connect them you can never lose sight of the fact that you are creating a new system, and the new system can fail as a whole. You cannot have a single point of failure, apart from the single engine. In the 231 you have a single alternator with a coupler that is a known issue. Failure of the alternator or the coupler is failure of all electrical and therefore all the panel instruments. You cannot rely on the house battery, I had that happen and if I had not put the gear down right away and flown that way to my diversion airport there would not have been enough power to drop the gear at a destination a half hour away. The 275’s have a backup, but the AFMS I received says that in cold temps the 1hr backup time can be 30 minutes. Is that enough time for you to come down from the flight levels, especially if you are, say, over the Rockies, and then fly an instrument approach to a safe landing? I don’t think so. So I have kept my vacuum and a simple vacuum AI. -
It’s true, but if you are looking at a 231 you need a good pre-buy by someone who will look the engine over really well. Too many of them have been routinely run too hot. It is a great little engine if treated right, mine is at 2250 (TBO is 1800), but there is a lot of misunderstanding about how to run that engine. Harder to hurt the normally aspirated engine in the J. On the other hand, harder to get above the cloud deck and into clear sailing too.