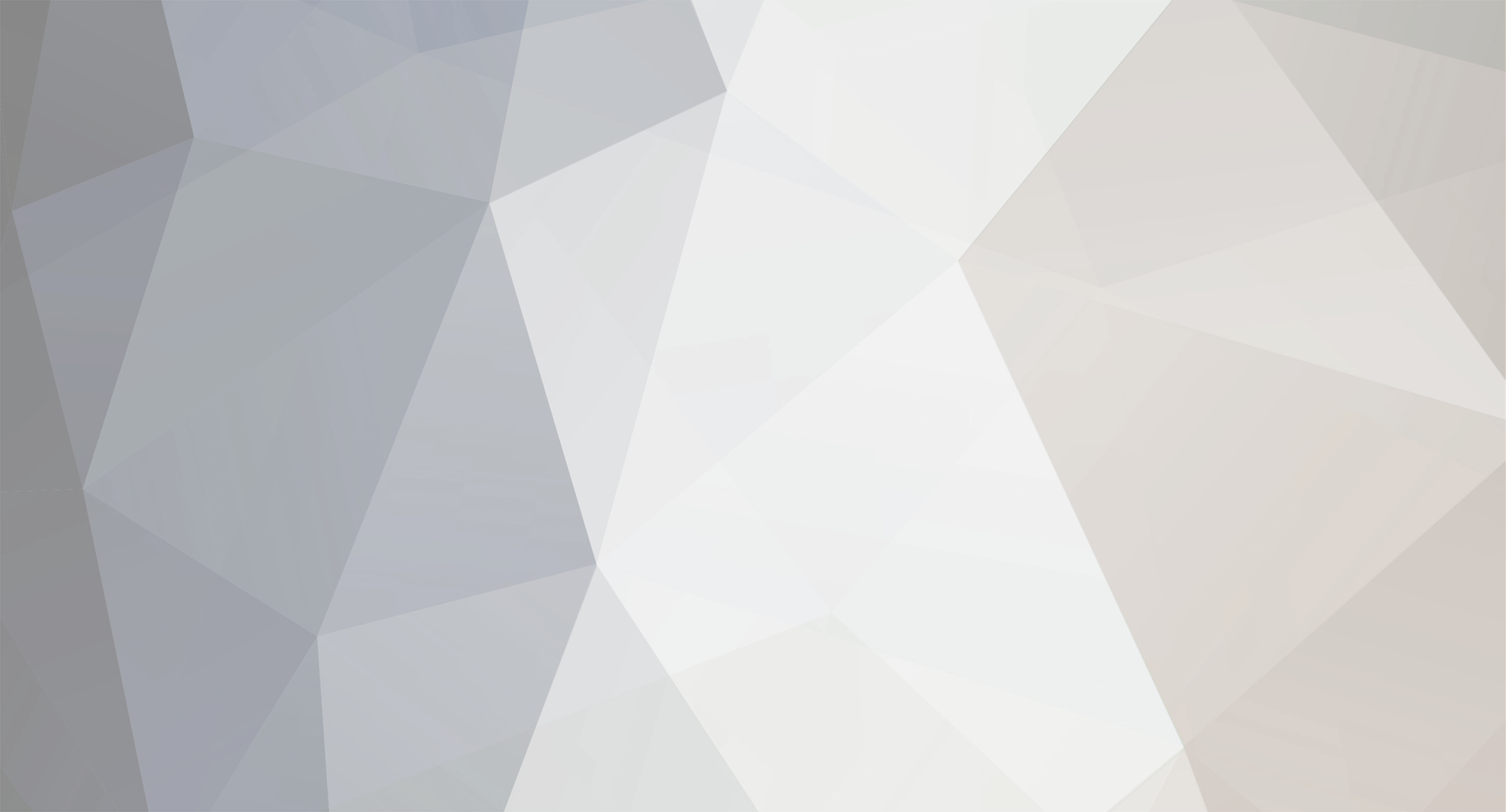
jlunseth
Verified Member-
Posts
3,800 -
Joined
-
Last visited
-
Days Won
10
Content Type
Profiles
Forums
Blogs
Gallery
Downloads
Events
Store
Everything posted by jlunseth
-
Well, it should be. This happened to me in Canada, and the Canadian mechanics immediately figured out that the quick drain was leaking. But they also found that a fairly large piece of rubber gasket material was swimming around in the oil, and managed to plug the intake hole of the quick drain. So the engine still had about 2 1/2 quarts of oil, it was not completely dry. The OP got to 4 psi because I throttled the engine to idle to try to save it in case I needed a little power to make it to the runway, and also because I tipped the nose over fairly sharply because I had to dive about 18,000 feet quickly to avoid being blown over Lake Huron by tailwinds. Tipping the nose over causes the oil to run away from the pump intake. It was not unexpected, but still tightened the sphincter muscles. So the Canadian mechanics felt they did not have to disassemble the engine. Unfortunately, the steep unpowered dive caused some piston slap and within a couple hundred hours I had the entire engine IRANd, which is probably what should have happened right away.
-
No, I did not use the chart to arrive at my setting. These are true numbers. I should add that I arrived at the setting with my old engine, I now have a new engine and am finding that it wants a little less fuel flow. Around 10.9, but otherwise the same. I am still working out the numbers for the new engine though. I derived the old numbers with fairly exhaustive testing using the individual EGTs, the idea being to keep the EGT that is nearest to peak, far enough away from peak for engine health. Once I know how that worked, I just use TIT. I keep my TIT at or under 1600 (the max is 1650). In the old engine I found that if TIT got over that number by very much it had a tendency to continue rising. I use a little flex in the number, in other words if the TIT is 1609 or something in that vicinity and is stable (is not continuing to rise) I am ok with that. The new engine is very slightly hotter than the old, either that or I am doing the testing in mostly summer conditions. The idea behind the 34" MP number is that lean of peak is an air/fuel ratio. The "perfect" ratio is known as stoichiometric mix. It is that mix where all of the O2 and all of the fuel is consumed in the combustion process. I put "perfect" in quotes because while it would seem to be ideal, it results in the highest Internal Cylinder Pressures and the hottest CHTs, which are hard on the engine. What you are trying to do with either lean of peak or rich of peak, is slow the combustion cycle, which lowers the ICP and CHT. In the case of lean of peak you are doing that by supplying the engine with a mixture that has more air than can be consumed by the available fuel. There are two ways to do that with a turbocharged engine. Either you leave the MP at a fixed setting and reduce the fuel, or you set the fuel at a specific number and increase the MP, which increases the air (O2) being introduced and thus makes the mixture leaner than stoichiometric. I was initially concerned that would be hard on the turbo, but the turbo in the old engine made it well over 1,000 hours without a problem. The percent power is about 70-71%. Percent power when lean of peak is determined by the formula 13.7 x fuel flow in GPH/rated HP (210). Please note that the 231 power controls are different from virtually every other aircraft because the wastegate controller is not automatic, in other words you can't set the MP to, say, 34", and then roll the fuel flow back to 11 GPH and watch your engine monitor to see where the peak is. The classic manner of making this setting, as I said earlier, is to either hold the fuel flow at a fixed setting and increase the MP, or hold the MP at a fixed number and decrease the fuel. But there is an interlink between the MP and fuel flow in the 231 engine, so a change in one parameter will change the other parameter. In effect you change the entire power setting if you do that and you are not affecting the air/fuel ratio much if at all. What I do to get to this setting is takeoff full rich, 36" and climb to altitude without changing anything except to adjust the MP up as I climb to maintain 36. Then at cruise altitude I reduce the MP to around 34-35" followed by reducing the RPMs to 2450. As you reduce the RPMs the MP will reduce so once you get the RPMs to 2450 you need to adjust the MP back up to around 34". Then reduce the fuel flow from wherever it is to your desired setting, say 11.0 GPH. Then you will once again need to adjust the MP to get to 34". In the first ten minutes or so of flight at this setting you need to watch the setting carefully, because the aircraft will speed up and so will the turbocharger, so you need to stay on top of that and keep the MP at 34 and the fuel flow at, say 11. Then periodically check the power setting during your flight to make sure it is staying where you want it. The 231 system is very analog, it takes awhile to settle in where you want it, and any changes that happen in ambient conditions will affect the power setting. That's what I do. YMMV
-
The Garmin 275s have a turn and slip indicator as well as being an Attitude Indicator. That's what I replaced my TC with. If you are looking for just a ball and turn you can go to pretty much any avionics shop and find one, or get ahold of one of the online suppliers like SEAerospace
-
Busted into a class Charlie yesterday
jlunseth replied to Thedude's topic in Miscellaneous Aviation Talk
Which doesn’t help the pilot. If the tower or the FAA wants to pursue a violation they will go after the pilot. What usually happens is just a scolding and you file a NASA report. But if the deviation caused a serious problem in the Class C or D that the tower is going to be responsible for, the pilot will be violated. When using VFR Flight Following it is the pilot’s responsibility, not the controllers, to insure that the requirements for entering the airspace are met. FAR3-2-1 VFR Requirements. It is the responsibility of the pilot to ensure that ATC clearance or radio communication requirements are met prior to entry into Class B, Class C, or Class D airspace. The pilot retains this responsibility when receiving ATC radar advisories. (See 14 CFR part 91.) This is really simple. ATC is not responsible while you are on VFR Flight Following, you are. You make sure you have yourself covered. You don’t treat ATC like an adversary, you cooperate with them and they with you. So if directed into Class C or D, or even B, and there is ambiguity, you are responsible to ask if you are cleared in. -
Busted into a class Charlie yesterday
jlunseth replied to Thedude's topic in Miscellaneous Aviation Talk
This is simple. Midlifeflyers post is accurate up to a point, and I certainly don’t mean to get into an argument with him, from what I can tell reading the forum he is a good guy. But his post is based on the controllers manual. Pilots are not subject to the controllers manual, they are subject to the FARs. Don’t get caught sleeping if you are approaching a C, D, or B and have not received an express clearance and read it back, or you have not been handed off and talked to tower. Prompt the controller and don’t enter unless it’s clear that you have complied with the FARs. I have heard more than one pilot get yelled at on the radio by tower for this, or get a number to call if it has created a traffic problem for tower. Flight Following means you are VFR which means you are in control not ATC, it is going to be your problem. IFR is a completely different animal don’t get them confused. -
Busted into a class Charlie yesterday
jlunseth replied to Thedude's topic in Miscellaneous Aviation Talk
This discussion has gone on forever, I don’t mean the discussion in the forum here, but the discussion about whether you can enter a Class B, C or D while on Flight Following, without meeting the airspace rules for contacting the tower or getting a clearance before entering. And the answer forever has always been the same. No, you cannot. It is your responsibility to contact FF and prompt them to hand you off, and/or do a 360. Will you get a violation? Unlikely. But it is your responsibility and not the controller’s to stay out of controlled airspace when VFR until specifically authorized to enter. -
Yes, if the TIT varies when the fuel flow varies it is a real issue as opposed to an instrument issue. I had one fuel pump rebuilt as I mentioned, it had to go back once for a similar issue to yours. Don't know who the vendor was, it was 15 years ago. Good luck.
-
Well, it depends on how big the fluctuation is. I have had two engines with different fuel pumps and the fuel pump on the first engine was rebuilt back in about 2009 so that is three fuel pumps. All three behaved in basically the same way. When I fly LOP, very small changes in fuel flow will affect TIT, which is what I mainly watch. So it is not uncommon for the fuel flow to vary up and down a few tenths. And when I take a flight and set a LOP fuel flow it is also not uncommon for the fuel flow to increase by about .5 GPH or thereabouts, in the first ten or fifteen minutes, and for the MP to increase also. Probably this is because the aircraft is picking up speed and as it goes faster the ram air effect increases, and that increases MP which in turn increases fuel flow. I dial them down and after awhile the system finds and equilibrium. Remember that in the 231, fuel flow and manifold pressure are co-dependent, a change in one causes a change in the other. Now if your fuel flow variation is big, say 1 GPH or more, probably a fuel pump issue. But if it is relatively small the issue can be (1) the 231 MP and fuel flow control systems are inherently not that precise, or (2) there is an issue with the throttle control that in turn is reflected in changing fuel flows. Also, check the "waterwheel." That is the paddle wheel sensor that detects fuel flow and reports it to the engine monitor/display. I have had two of those wear out. You will see fairly large changes in fuel flow without significant changes in either MP or the temps that you would expect to see change if the fuel flow were actually fluctuating (EGTs and TIT). Relatively simple replacement. Best of luck, hope you can figure it out.
-
I did a search on my old posts and found the Turboplus instructions for setting fuel flow:TSIO360 Fuel Setup - NEW 08.pdf As I said earlier, some of us try to get the fuel flow set a little higher. Please note that the max power MP in these instructions will generally be higher than the 36-37" most of us use to set full power in flight. The fuel setting process is conducted on the ground with the aircraft not moving and therefore very little air is passing over the intercooler to cool the induction air. The intercooler becomes more efficient as the aircraft picks up speed during takeoff and flight, and air passes through the scoop and over the fins of the intercooler. At cruise at altitude it is not uncommon to see a differential temperature (Compressor Discharge Temperature minus Induction Air Temp) of 100-125 degrees. So the higher max power MP in the table in the instructions is not directly applicable to in-flight power settings.
-
I keep the Sectional up. I fly a few times every year to the west and find it helpful to have a relatively clean display with ground elevations and MOAs so I can plan my altitude adjustments as I progress. I also like to be able to pull up the VORs that are forward of my position and plug in the frequencies just in case of a GPS outage, and to keep that skill up. The Aeronautical and IFR displays are just too cluttered and lacking information I need. On rare occasions, if I have to fly IMC for an extended period I will use the IFR map. If I fly an approach I will put the plate on the sectional and that way I can see ADSB traffic during the approach.
-
Solves it. When you reduce power you will reduce OP. Engine isn’t working as hard, oil pump is not working as hard. In addition to your reduction of power, the act of tipping the nose over and going downhill reduces the load on the engine.
-
Do you by chance reduce the power for the descent?
-
The SID alone is not enough. There are instructions in the STC for the Turboplus. In very general terms, the Turboplus makes the induction air denser. There is a table in the STC instructions that tells the A&P what MP to use as max power during the setup procedure. It varies with OAT and is in the neighborhood of 36-37 inches. According to the STC instructions the A&P is to use the SID, but adjust the SID procedure per the STC. If you were to use the SID straight up you would use the factory MP setting of 40", which is way too high for an engine with an intercooler. I used to have the STC but don't think I have a copy any longer. You could contact Turboplus, they can send you one. It is somewhat difficult to get mechanics to understand the process and the importance of getting it right. They are fairly persistent in just defaulting to the SID. So the fuel flow is set to 24 GPH at 40" of MP, but you use let's say 36" as your full power setting because you have an intercooler and then what you see is insufficient fuel flow at full power which is actually 36", not 40. The fuel flow is supposed to be 22.5 - 24.0 at max, but most A&Ps, following just the SID, set the fuel flow wrong and you will see 19-21.5 at 36". The consequence is an inability to keep CHTs under 400+ in a climb, especially in the "high, hot" conditions out west. Many of us (231 flyers) try to get our A&P to set the fuel flow to about 25 GPH at max power (max power as defined in the STC table), which gives us a little extra fuel to work with in the summer. You could ask Paul Kortopates, he understands it pretty well. This means that on the ground you may want to reduce the fuel flow a little to stay under 24 during takeoff, but it sure helps with summer temps and climb outs.
-
They came out with a new version of the hardware a couple of years ago that deals with that problem. The 200-C if I remember correctly. They had a discount to buy the new version, don't know if that is still true. I have had a few installation problems that got fixed, but those were not the fault of the system but of the installer. The only real issue I have is that alot of the approaches in my area have you flying at 2,000 or 3,000 for extended periods, and when you do that it will repeat "3,000, 3,000, 3,000" ad infinitum until I shut the audio off on the com panel. It really helps with landings, annunciates all the way down.
-
Cheyenne PPP, Inogen Rove 6, and 1st Class on the 787-9
jlunseth replied to donkaye, MCFI's topic in General Mooney Talk
Shoot Don, I wish I had known you were there I would have looked for you just to say hi. So if you have a Bravo with TKS and are instrument current you probably have a superior traveling machine. But I was out of instrument currency and coming from Minnesota that weather you dealt with at CYS spilled out over the prairie for two days. At one point there was an IFR Airmet that looked like Pacman and stretched from SD to TX coming across the prairie. I left on Thursday and could not find any safe route, so spent one night in a motel in O'Neill and another in a bed at the FBO. Finally flew from KONL to KCYS on Saturday morning early and flew with Jerry Proctor. Now I am instrument current so the trip back was pretty easy even though I flew into the back end of the weather when I got to MN. Haven't had the 787 experience. I fly with Delta when I go commercial and it generally works out pretty good. However you look at it, air travel can be a dicey thing. I guess we all need a private jet with warm wings like Tom Cruise. I have a good friend in Cheyenne who flew all over during his working career (commercial). He never flew out of CYS, he always drove to Denver and went from there. Poor connections from CYS I guess. I have been to CYS a couple of times now in my aircraft. Especially in the spring they get those storms that come over the mountains and pick up speed as they spill down the slope. There were peak winds on Friday of 61 kts at the airport according to Foreflight's wx reports. Stay safe. -
Video of door pop, pilot error (not Mooney)
jlunseth replied to 201er's topic in Mooney Safety & Accident Discussion
When I bought my plane years ago, my instructor and I went to Scottsdale to pick it up. An annual had been performed but not a very good one. The door opened on takeoff. We tried closing it but could not get it done in flight. We flew over Raton (over the toe of the Rockies) at 16,000 and all the way to Kansas, where we stopped for fuel, with the door ajar. It was definitely cold over the Rockies and only so much the heater could do. It subsequently turned out that the latch was maladjusted and simply would not hold. I can tell you from that experience that, (1) it is practically impossible to close the door in flight, the instructions in the POH notwithstanding, (2) it is not a big deal, the plane flies just fine, you will have some noise and wind and if it is cold outside it will be cold inside, but there is no reason for panic or an emergency, (3) the door will not open and no one will fall out - the slipstream is too strong and while the door can't be closed it won't open more than an inch or so either. Just leave it and find a convenient place to land. Baggage doors are a different issue. We had a very good family friend who took off from the now-gone Coronado airport in a twin with several on board for a ski trip at Taos. The baggage door in the nacelle came open. He tried but was unsuccessful to get the plane back safely and all aboard lost their lives. Early on in the life of this forum there were at least a couple of incidents of Mooney baggage doors coming open, one just causing heavy vibration and the other coming off the aircraft and impacting the elevator or rudder, don't remember which. There is just no excuse for allowing anyone other than the PIC to be the last person to check or open the door, and it should be locked in flight. Yes, the emergency latch still works. No excuses now. -
Well, this is a story I have told before so those who have read it, bear with me. I got to do an exciting power-back descent and landing while overflying Canada once. It turned out a tiny but long sliver of plastic, sort of like one of those fingers on an oil bottle cap, had been swimming around in the oil, went into the engine quick drain and was too long to pass through the seal. I noticed a drip on the nose tire so had taken the plane in to the shop immediately before the trip and was told not to worry, quick drains just leak a little. We blew most of the oil out in a couple of hours. The pressure fell to 14 psi (normally around 38) and then when I powered the engine back to idle and tipped the nose down it fell to 6 psi. The landing worked out. Before this flight I was plagued with oil on the belly and it would be variable, some trips the plane would use alot of oil, like a quart an hour, some trips not much. Like you I was trying to chase problems with the air/oil separator or other leaks in the engine. Now, at annual, I have the mechanic remove the quick drain entirely when the oil is changed so anything swimming in the oil can exit through the big hole and ever few years I have a new seal kit installed in the quick drain. Its been more than ten years and two engines since then, and my 231 uses about a quart between oil changes, such a small usage that I can start with 7 qts and wind up at 6 at oil change time. PS power off descent from 19k with strong tailwinds blowing us over Lake Huron, about 7k of the descent was IMC, all worked out with a perfect landing. Getting out of Canada and back to the US without passports or EAPIS credentials was a problem.
-
No. One of the problems I recall was that the DB Manager corrupted Terrain Cards. I (and apparently others) were able to update the Navdata card and that data was good, but the 430 would not initialize because of the corrupted Terrain Card. Garmin developed and sent out a utility that was supposed to fix the Terrain Card, and later I believe it was incorporated in the DB Manager because there was a note or comment about repairing the cards that came with the DB Manager update. In my case, I spoke to Garmin a couple of times and the problem was misdiagnosed as a Navdata card issue. I happened to be at my avionics guy for another reason, mentioned that to him, and he said he had heard there were Terrain Card problems. About that time the DB Update manager came out with the repair capability and that fixed my Terrain Card, so my unit now works fine and both cards are good. But there have been other issues since then. As I said, I just update my cards before I ever update the software and that gives me a month to get the software update working. A part of it may be that I have to do either two or three separate updates. My primary GPS is a GTN750 connected to dual reversionary 275's. Those update in one syncd update. But the 430 card (or sometimes two if there is a change to the Terrain Card) needs to then be separately updated with the manual update process that is selectable in DB Manager and that does not always go elegantly. Everything is working right now, except that somewhere along the way the software was changed in the 275's. Before the change I could load the syncd update in the 750 and it would sync smoothly over to the 275s. After the change there were some people who could not get the 275s to update that way at all, and they went to using a USB or Garmin Connext. My 275s will sync data over from the 750, but not right away. I have to fly the plane once or twice and then miraculously the new data is in the 275s. I tried putting the data in the 750 and then cycling the Master switch thinking that would cause the 275's to see the new data but that does not work, at least not the first time. I have also gone into the 275 menus and the new synced database is there, but it will not enable. It just miraculously syncs over and works the second or third time I fly the plane. As I said, everything is working now, but the update process in the last couple of years has not been seamless.
-
I wish. I have a regular PC so there should not be a problem, but there have been three or four in the last couple of years that have caused me problems. So I update the cards before I update the software, that way I have working cards at least, while the issues get worked out.
-
Ditto. I hold my breath every time I update the Database Manager. If I do it at all, I update the cards first so I have a month to get the new version to work (or Garmin has a month to roll out a correction). Its a perennial mess. To the OP, you might need to buy a new 430 card reader. Don't know for sure, but I think the readers might be different for MAC and Windows OS. I just use a PC so have never had to look into it.
-
I always use a checklist, or a flow for some functions. Since I always do them, I have been fortunate and always caught errors. A couple stand out. I always do a P-lead check, also called a mag check, when I shut down, as part of my shutdown flow. On one occasion I found a P-lead failure, immediately informed the FBO, we flagged the prop so no line kids would try to move it, and got it fixed right away. The other one I remember is preventing a gear up. So I always check for gear down on final and I say it to myself, "Gear Down." While practicing for my commercial I was doing power off 180s. A Mooney was on the ground and apparently trying to figure out which direction I was landing in because he did a 180 on the taxiway and then another. There was also a guy assembling an ultralight in the grass right at the approach end. So I was watching the two of them like a hawk, especially since the paraglider guy was not on a radio, and forgot the gear. I did my final gear down check on final and it was not down, so I executed a go around and found another airport without congestion to practice at.
-
I generally fly by the numbers, but have learned to respect the slickness of the Mooney airframe. For example, flying an approach I typically maintain 120 knots to the final approach fix, and going down the glideslope I want to be at 90 knots. 19 inches of MP will usually give me 90 knots. But if I start at 19 inches at the top of the slope I will never get down to 90, the combination of the higher approach speed, the speed going down the slope and the slickness of the airframe will conspire against me. So when I tip the nose over on the slope I will reduce power to 15.5 MP or so, I put in half flaps when speed comes under 100, and then will increase power for the balance of the final approach. There are lots of circumstances where a reduction to allow the airframe time to slow down is needed.
-
The other issue is uneven fuel flows. If the fuel flows at each of the cylinders are far enough apart and you follow the old advice to lean to roughness and then enrich back to smoothness, some of the cylinders may be in the "red box" while others are sufficiently lean. If you run the engine long enough at that kind of setting you are likely to see the need for a top overhaul replacing those cylinders. Again, if you run at or under 65% it does not matter.
-
For those on this thread who are considering experimenting with LOP, the even fuel flows are important, yes. But LOP also requires a strong spark. A mixture is "lean" because it has less fuel than what would be necessary to use up all the available O2 during combustion. In other words, the fuel in the mixture is somewhat rare. That slows the rate of combustion in the cylinder resulting in effect in a long slow push and because of the long slow push, cylinder temps will be cooler. Because fuel is a little rare, it is a little more difficult to ignite the mixture, hence the need for a strong spark. Most of us have found that fine wire spark plugs really help with that, and the mags need to be in good shape. Sometimes my engine will start to miss a little when LOP, when it is getting close to annual time. Then the annual happens and LOP performance is excellent. The reason is that the mags get checked and reset at annual every year.
-
Two things. First, I asked the question because I am not sure that any of our TSIO360 engines can make enough air to run LOP with a fuel flow of 12.8 GPH. I understand that your numbers were just running the formula. But lots of pilots make the mistake that they can use the formula any time to determine percent power. We can't. The air/fuel ratio must be a lean ratio. If the air/fuel ratio is not a lean ratio the formula does not apply. That was my concern/issue. As far as engine smoothness goes, you might run a true lean test and see what you get. The instructions are on GAMI's website (https://gami.com/gamijectors/leantest.php). I am on my second engine and both have run LOP very smoothly, without missing unless deeply LOP. The current one can run very deeply LOP without roughness. That was not true when the TCM injectors were in the engine, they would produce roughness as soon as the engine went LOP. But with the GAMIs I am able to go deep. I don't have any exact numbers yet, I plan on doing a lean test on the new (GAMI) injectors in the next couple of weeks and will report back. Just for the fun of it, I will try your 30"/2400/10.4 GPH and see what I get in terms of "LOPness," although our engines are different it might be instructive.