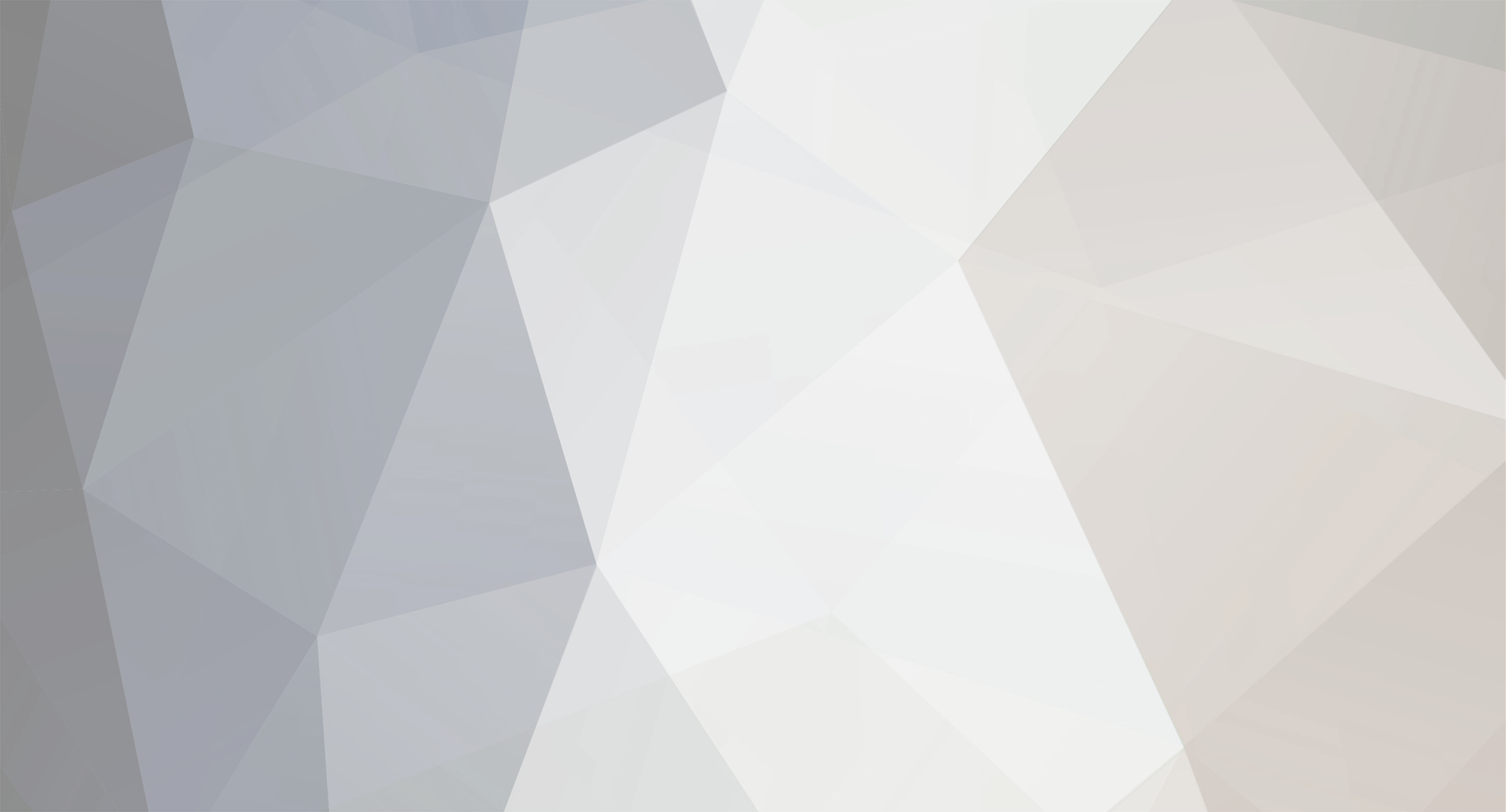
mike20papa
Basic Member-
Posts
359 -
Joined
-
Last visited
Content Type
Profiles
Forums
Blogs
Gallery
Downloads
Media Demo
Events
Everything posted by mike20papa
-
There could be several issues...work with your mechanic. Okay, now that thats been said... Remove the inspection panels at the rear of the fuselage and inspect everything for obvious wear. Then lift up on the rear of the tail cone and see how much "play" there is. 1/8 inch or so? Then check the leading edge of horiz. stab at tip for fwd/aft play - SHOULD BE ZERO! Then remove the AN4 bolt that connects the ACME screw to the tail cone bracket - but have some padded/stable means available to support the tail cone when bolt removed. (2 person job) Now, lift up on the tail cone and check for binding, free movement, etc. Now...very important! DO NOT ALLOW the connector on the end of the ACME screw to rotate (or you will loose the trim reference)..while someone rotates the trim wheel. Does it bind, move freely. It should. Now start chasing down the source of the resistance...either in the empenage/tailcone pivot hinges..or in the trim wheel assembly all the way to the acme screw. The hinge pivots for the tail are hard to access. Get a bottle of triflow with the long tube and dose the pivots - along with all the ball joints, etc. Also, before you start, sit in the cock pit, pull back all the way on the yoke and see if that helps with rolling the trim wheel "nose up" it should.
-
I sure like that video capability. Really neat set up, and what a great tool for improving your landing technique. Looks like you were just carrying to much speed at touch down indicated by not enough flair, certainly. Come down final with full aft trim, Touch down on mains, with full trim makes the effort to pull enough back elev. a piece of cake. Also forces you to control speed on landing. Practice landing with the nose wheel off..and keep holding off as long as you can. Gets to be a game, Lots of fun to bring back up a little power & taxi down to the end of the runway with the nose still not yet on the runway. Improves your rudder skills, too. The video to me didn't look like much of an xwind, There was no evidence of a yaw or correction of crab as the nose wheel was dead straight (except for a little blip there at touch down). If you're a fwd. slip dude, then no bank angle or rudder/nose wheel deflection. No sign that you set the windward wheel down, first. Or that there was a windward wheel. What airport, I fly out of KCFD (Bryan TX). I know when I've got a strong xwind, coming down final and I've got it xcontrolled to the stops and barely able to maintain centerline..when I can't, that's when I go look for another AP! Also, when you get down low..and you see all of the small pieces of grass being blown sideways across the runway...get READY!
-
spark plug replacement, damage from missing gasket??
mike20papa replied to DXB's topic in Vintage Mooneys (pre-J models)
If BOZO the mechanic clown had forgotten plug gaskets.. you wonder if he might have forgotten to wipe his ass before he got u're plane signed off. I'd remove the interior and disenfecal. at the minimum look over those log books for brown spots. Call the mechanic and ask him.. tell him that his work should be reported to the FAA, you want his re-inspection, tell him he is a POcrap! Yike ola.- 18 replies
-
- 1
-
-
- spark plugs
- gaskets
-
(and 1 more)
Tagged with:
-
Poor instruction = poor stick & rudder skills, no idea how to fly an xwind and of course..all of them obviously instructed in the "crab & kick" - "hack & slap" technique. I didn't see a single forward slip into a stabilized approach. These are the same guys, give them a warbird and they'll promptly roll it into the ground.
- 28 replies
-
- 2
-
-
- cross wind
- rudder
-
(and 2 more)
Tagged with:
-
The steering horn has such short linkage pieces that any wear in ball links, loose ball links on rods, loose bolts, etc. can become a problem. If you can raise the nose wheel off the ground enough to wiggle the nose wheel back and forth while you look closely up in the gear bay, you may find the source of wear/play. Could be something as simple as a worn rod end or loose bolt. The phillips head screw facing fwd.just right of the steering arm - that attaches the assembly to the nose wheel truss has to be torqued tight - found that out, myself. Good luck.
-
I went with what the AC industry calls "non textile" carpet or floor covering. I found some remnants on EBAY and I think the stuff is fantastic. It is an embossed carpet like surface, that is a fiber reinforced silicone material that is backed with a thin dense foam - the complete thickness is about 3/16" or so. It wears like nails, lays & stays flat like a sheet good, water/oil proof, sound absorptive and doesn't look to shabby, either. Here's a link to some similar material. My experience with textile carpet was hopeless. It's amazing when you pull the carpet out..just how small it actually is! Good luck! http://www.h-a-i.de/html/products/floor.html
-
Water under the back seat
mike20papa replied to Guitarmaster's topic in Vintage Mooneys (pre-J models)
Water under the back seat..are you sure you don't have a woodwing A model?! The A model has drain holes in the center section of the wing. The aft fuel tank is under the back seat and sits on wood runners, so any water that collects under the tank can drain out. The water usually comes from the absence of the sealing tape that is suppose to go under the upper wing root faring strip. It is suppose to seal out rain/wash water that runs down the upper surface of the wing, hits the fuselage and will then run into the cabin if not sealed off. I use a heavy plastic tape used to seal the vapor barrier in foundation construction. What ever you do, don't use any silicone sealant under the faring strip, it adheres to alumn. and will never let go. -
Replacing M20B rudder bellcrank?
mike20papa replied to lifftchi's topic in Vintage Mooneys (pre-J models)
Just where is this bellcrank? I don't think the rudder replacement is practical as it would require basically changing out the empenage. I know the lack of right rudder thing as I fly an A model. Take off is always right foot hard to the floor..if you dare let up even just a little, there is not enough right rudder to bring it back. You can be looking at the left side of the runway at lift off. On xwind landings, I find the rudder/aileron balance adequate. In other words, if I'm in a strong enough x wind I can't track the runway on final with bank (aileron) yaw (rudder) is not my concern. Probably a phone call to the guys at LASAR is the best bet to find out what's involved. -
Heloman - the fuel pressure is taken from the carb fuel inlet just upstream of the float controlled needle valve. There is a small dia. hose that feeds the gauge, you can see it leading from the carb. The fuel drawn from the throttle pump is drawn from the bowl. It is not under pressure and you won't get a pressure change until you somehow remove enough fuel from the bowl allowing the float needle valve to open and fuel starts flowing (without the elec. fuel pump on to replenish it). I believe you can look in Trade a plane and find additional sources for OH carbs. This nonsense that you need the elec. fuel pump on in order to prime a non-fuel injected engine is only if it has sat for such a length of time that all of the fuel has evaporated from the bowl. And, then you only need it on long enough to fill the bowl.
-
Vintage Mooney Cowling Mod
mike20papa replied to Sabremech's topic in Vintage Mooneys (pre-J models)
Yes, A FIELD APPROVAL!!?? Wow, David! Right on! All comments aside..it is the issue I wish AOPA would pick up after this medical thing. The whole 337 enchilada, with or with out onions, TEX MEX, or just what comes out of the oven at your local FSDO from one day to the next. It's a freekin' joke! -
Priorities when buying a vintage Mooney
mike20papa replied to a topic in Vintage Mooneys (pre-J models)
Life threatening wood wings...and oHHH...those woody tails! Looks like someone forgot to inform this pilot! There are actually a lot more woody tails flying out there than you might think. Especially when it's appreciated/understood that it's the VFR antenna opng. is what can do one in! The A models should ALWAYS be hangared. Otherwise..it's like buying a Steinway baby grand, and keeping it outside on your driveway and then bitching about how poorley it was designed and built. There are characteristics about ang material that have to be dealt with. Steinway uses spruce for the sound board not alumn. for good reason! -
Priorities when buying a vintage Mooney
mike20papa replied to a topic in Vintage Mooneys (pre-J models)
Even before Russel's unfortunate death, SWTA discontinued their 201 windshield kits (I'm guessing about 5 years ago) it's how I was able to sell mine - with a transfer of the STC. My decision not to install the kit was, in part, per the discussions I had with Russel regarding the advantages/disadvantages of the mod. Engine controls are a safety of flight issue. Not a windshield mod. FAA recommends they be changed out at engine TBO. Pain in the ass, or not. -
Priorities when buying a vintage Mooney
mike20papa replied to a topic in Vintage Mooneys (pre-J models)
WOW! What a fabulous example of an immaculately kept E model. You can just change your name to Lucky Dude and count your blessings! I would ask myself..with the obvious priorities & resources of the previous owner, maybe he knew something ..why he did NOT put in a 201 windshield. Even his professional background and NO to a 201 windshield. I'm an owner of a '59 A model and bought a 201 windshield and after a lot of discussions and thought, opted to not put it in. There is not a single annual that goes by that I'm glad I did not. (ask yourself..how to simply top off brake fluid and change vacuum system filters, inspect wiring, ground connections, hoses...etc) I also don't think there is anything wrong with the original classic lines of the airplane - especially the short bodied - pre J's. Also the shorter bodied Mooneys have less wetted surface than the stretched later models and thefore inherently less drag.. No body ever talks about this. I put in a single piece, original sloped 1/4" tinted & UV guard windshield from LP AERO and it's great - for my needs. I also did a panel upgrade on my A model and you couldn't pay me enough money to do the same job on a Mooney with a 201 windshield in. Just imagine lying on your back in the cockpit for hour after hour making the required connections and all. Now, with all that said, you have no panel up-grade to contemplate. You're a young dude and knotting yourself up into any required odd shape to work behind your panel maybe no concern. It is your airplane! ENJOY! -
Call LASAR they have used serviceable parts, also go to EBAY.
-
I've noticed that if the pre-load is excessive, the latch release button is more difficult to push in, also try greasing the moving/lock pin. Now, that wouldn't explain the difficulty in sliding the handle down. That sounds like a lubrication issue.
-
FAA has a circular concerning engine controls for piston aircraft. It's been a while since I read it..but it recommends replacing all cable controls at engine TBO. Might be under the infamous "Instructions for continued airworthiness"
- 13 replies
-
- mixture cable
- throttle cable
-
(and 1 more)
Tagged with:
-
I've got a couple of old donuts & new ones at my hangar. Will get you both measurements this weekend. Joe
-
You actually practice bounced landings.. like on purpose bounced landings...sounds like Jim Younkin who learned to fly way back in the day.. his instructor made him land short of a barbed wire fence and bounce it over ..or else no sign off!!?? When you practice go'rounds or touch and goes.. do you allow the pilot to set the nose wheel down, or is it all done off the mains, only. When x wind landing what do you tell your student to do just as the nose wheel is about to touch down? What about x-wind take off's? I find those to be way more interesting than the landings!? I like flying to Kingsbury TX, turn downwind over the cattle pens, line up for the BIG tree on final - or not ? - then miss the mud hole on landing (middle of the runway) and taxi to the grass parking. Glad to have one of Al's surviving A models, 12lbs/ftsq wing loading and take off - well, it's just another word for show off.
-
Vintage Mooney Cowling Mod
mike20papa replied to Sabremech's topic in Vintage Mooneys (pre-J models)
Aesthetics are wonderful. I wonder about the CFM requirements for engine cooling AND induction being adequate thru the two smaller plenum openings. The LoPresti cowling has the induction separate with a large side mounted NACA scoop and even they brag about how the openings for their cowling is forced close up to behind the prop for higher pressure/adequate CFM for cooling. And the engineering they worked up to develop their design. I guess that's what test flights are for. Best of luck! -
Lycoming Service Instruction gives the following formula for max. allowable oil consumption for all their recip. engines: .006 x BHP x 4 / 7.4 = qt./hr that comes to .65 qt/hr. for a 200hp J. Come on, anything more than qt/7hr.s too much...says WHO?! I would begin by checking the breather hose tube where it connects to the alumn. tube and make sure the vent hole is open & clear, then do a compression check and follow up with a bore scope of the weak cyl. to check for excessive scoring. Could be as simple as some stuck or broken rings. Certainly more expensive items on a Lycoming to repair than pulling jugs & replacing pistons & rings. Bore scoping the valves & doing the "wobble test" could be more conclusive. Also, how does the engine perform? run hot? start-ups? developing full power? What kind of cyl. finish, regularly flown, etc.
-
As far as the engine "sag" Are you aware you can shim the lower mounts with alumn. sheet shims. make them out of .063 and use up to 2 in the lower mount. I think Maxwell the infamous EasTex Mooney mechanic has a article on his web site. JOe
-
Just about the last thing I've ever wanted to deal with is a magnetic field possessing some part of my aircraft.. when ever I read about these problems..I cringe. Well, sure enough, I just had my turn. I first noticed my whiskey compass acting up - very unreliable and indicating up to 40 degrees off heading, then somewhat normal again. In my hangar, cowling off, I took an extra compass and began scanning for anomalies. I got some very weird readings, compass spinning, etc. around the battery box and engine mount. I took the battery out, scanned it and while it does have a field to it, not enough to account for the problems I had been experiencing. So, back to scanning the engine compartment and strong deviations appeared around the upper engine mount. After reading some info on line, about using a DC welding machine to magnetize or demagnetize steel, I thought about the engine mount bolt that the neg. battery cable bolts thru - grounding the entire airframe & engine. Maybe after years of 12v DC passing thru it, it had become magnetized enough to cause problems. So, after removing it (and it's a large bolt!) and holding it near the compass - it was obvious I had found the culprit. Not only the bolt, but also the nut and 3 washers were highly magnetic! So..fired up my rivet gun and after working them over for a minute - all the magnetic field had been removed. The Lord mounts showed no magnetic field, and the engine compartment tested "clean". So! Nice to have a true mag compass back in my M20A! Joe Philips N8335E
-
Best 2.24 engine gauges ????
mike20papa replied to Wesley brown's topic in Vintage Mooneys (pre-J models)
Wesley, I replaced all of the old gauges in my A model with EI units and I'm very pleased with them. Except for the ammeter - I went with a Mitchell. The FP-5L - I couldn't imagine an airplane without one! It will also talk to your KLN90B, if you hook it up (2 wires) and give you fuel requirements, etc. under "OTHER" pages. My old oil pressure gauge was reading high compared to the EI. The 2.25" tach & MP let me install more radios, so that's why I went with them. Look at my "gallery" for photos. Joe Philips N8335E -
Vertical Card Magnetic Compass
mike20papa replied to rakesb's topic in Vintage Mooneys (pre-J models)
I guess I just always favor the simply solution. Why does anyone want a vert. card compass when you have a DG? When the wet compass is for reference, to set the DG. The beauty of a wet compass is it's unfailing simplicity - the ideal instrument for a reference. The only time I would consider installing a vert. card compass would be in a VFR acro or puddle jump airplane that I wanted to save space, weight and either no electrical or vacuum systems. -
Stupid stuff ; landing , starting?
mike20papa replied to carl's topic in Vintage Mooneys (pre-J models)
This discussin' sounds like FUN. So here's my VFR SOP. Cruise altitude WOT & 2400. Running lean as it will run smooth. Figure what altitude needs to be lost to get me to pattern & divide by 500 then that many minuts out reduce power to get 500ft/min descent and stay out of the yellow arc. (Flying in TX can get bumpy coming thru/below the lifting condensate level) So, I usually use 16" MP. Around 1000ft above pattern I switch from aft to my most trusted main tank, aux. fuel pump on, finalize my pattern entry decision, radio calls, etc. Then I really focus on flighing a precision pattern entry, on the money altitude and at 120mph and my standard distance out from runway. On downwind - trim, trim.trim & more trim & power reduced usually now down to 12" and mixture richened, I look to hit 100mph abeam the numbers - still at pattern alt. , the gear goes down, quick check list, then turn constant rate descending base & final. On final I may use flaps, I may not, mixture rich, prop full last gear check. I do like the slower landing speed on roll out with flaps, but either way, I use power or a forward slip to deal with alt. adjustments, never flaps. If there is a stiff xwind I'll extend down wind to get a longer final - to be sure I have enough control authority to handle the wind that with full X controls I can track runway center line and know my fwd slip is going to be adequate - even in the flair. adjust power to stay at 90 mph - what I like to come down final at. then over the numbers pull power & work out the landing. To me, the key to landing the Mooney is trim. If you don't have almost all of the up trim rolled in before you land, the yoke force goes way up and it looses its sweet personality.