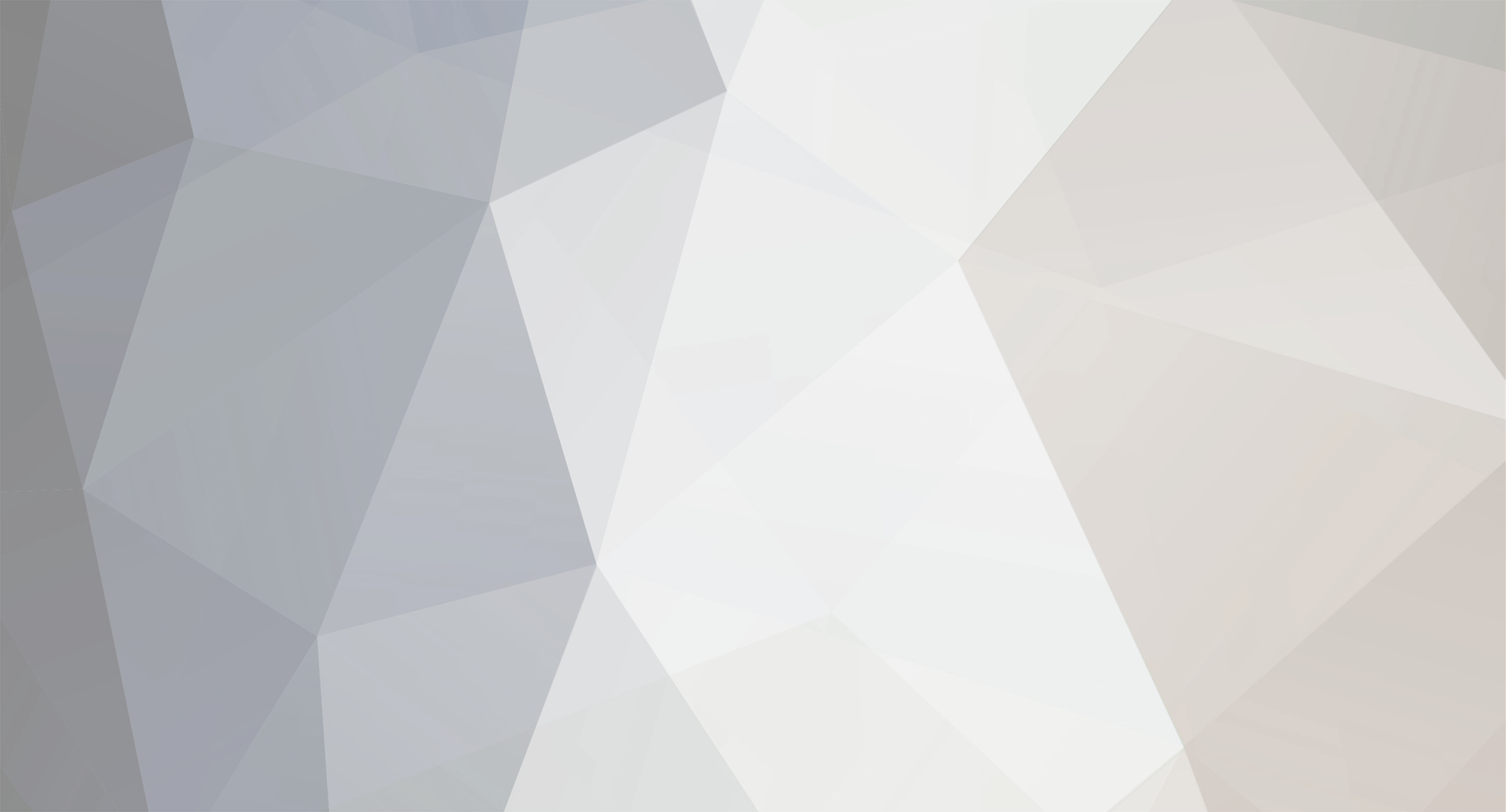
A64Pilot
Basic Member-
Posts
7,988 -
Joined
-
Last visited
-
Days Won
21
Content Type
Profiles
Forums
Blogs
Gallery
Downloads
Media Demo
Events
Everything posted by A64Pilot
-
Actually not, the airspeed you go to when time wasting is the goal, like holding for instance, isn’t Carson’s Speed, it’s max endurance speed which isn’t really even close to Carson’s speed. While I cannot follow Cobra Drivers math, Carson’s speed can’t be actually defined, because it’s someone’s opinion of an airspeed at which going faster wastes fuel and going slower while conserving fuel wastes time. It can’t be defined or calculated because time is worth different amounts to different people. The only logical way I could see to define what’s time is “worth” would be to calculate operating costs per hour including all costs not just fuel, but I’ve not seen that done, only then could you argue how much money you saved by flying less hours, even though more fuel was burned, and how much to operate an aircraft will change for each model, so even within the M20 fleet each model would have a “cheapest” speed to fly An example is let’s say taking engine and prop TBO in account with other items that last x number of hours like vacuum pumps and alternators etc you came up with $50 an hour, on a trip if you fly faster and burned $30 more in fuel, but cut one hour off your flight time going faster you saved $20. These numbers are made up, but I’d bet money Airlines etc have done that math, or I’d be surprised if they haven’t. If you go out and graph fuel burn vs speed you will get a graph that’s U shaped, It’s sometimes referred to as bucket shaped, with the two bottom parts of the bucket as “bucket airspeeds” with best glide being the very bottom of the bucket in between the bucket airspeeds. ‘So pick any airspeed you want in the bucket, probably those who seek efficiency will pick the forward portion of the bucket, but of course even the “bucket” isn’t well defined as it’s a pretty gentle curve.
-
Carpet: to glue or not to glue?
A64Pilot replied to AndreiC's topic in Vintage Mooneys (pre-J models)
Mine is just laid in there and does fine, it moves a little sometimes but is easy to move back. Don’t glue it, you will likely never get all the glue off. My luck if I used screws I’d find a fuel line or a wire that would cause something to work intermittently, or short and catch fire. My carpet has a stiff backing of some kind and foam padding, it could be original, not sure. -
Fine wire plugs aren’t nearly as new as we think, in fact many if not most “new” things for piston engines our Grandfathers knew about and was normal ops for them, like LOP for example http://www.enginehistory.org/Operations/R-4360Ops/r-4360ops1.shtml Ignition System: 4 Scintilla S14RN-15 low tension magnetos mounted on the propeller reduction gear case, 56 Transformer Coils (2 mounted on the top of each cylinder) and 56 fine-wire spark plugs. The magneto gear drive mechanism permitted the Flight Engineer to select either 20° or 30° spark advance magneto-to-engine timing. The 30° selection was limited to cruise power settings only. I went through WOEC “Warrant Officer Entry Course” with an old National Guard guy that had been a Crew Chief on a B-36, he said it took a squad of men pulling a wagon full of 336 plugs to change plugs in a B-36, took them most of the day.
-
Best thing to do
-
OK it’s put together and it works, a few caveats of course. First I used the stand @rickseeman recommended, not the original I looked at, his fit better and besides was cheaper. Second the threaded rod portion as your moving it, it’s length is the limit that you can jack up, so you have to have it fully screwed down and then using the sliding tube portion of the jack adjust it so it just fits under the wing with the screw portion fully down. There is enough lift for a Mooney, but this may not work for an Oleo strut airplane, if we had a longer screw portion, ideally 7” longer that would be perfect. Second there is a “window” on the adjustable sliding tube, when the bottom of the threaded portion is in that window, that’s it, you should stop jacking up or there won’t be enough of the threaded portion sticking into the pipe to be safe. I bought an 18” portion of 1.25 “ galvanized pipe and cut it into two 7” pieces, one for each jack, on one end I welded on a thick fender washer for the jack to push against and I then welded it 100% around to the threaded rod portion of the jack, initially I didn’t weld it, but as I’m jacking so the threaded rod is up high in the tube, I wanted the additional security of 7” more pipe still sticking into the jack stand and feel that 100% weld out is justified, of course real thick tubing would be much better than galvanized plumbing pipe, if you weld galvanized, be sure you have good ventilation as the gas burning zinc gives off apparently isn’t healthy. OK you get this thing and the first thing you see is there is a cap on the bottom acting as a stop for the legs that fold, it’s screwed on with an internal wrenching bolt, remove it, then you see a washer in the tube with three spot wells, that’s what the cap screws to, drill out the three spot wells, then drive it out the bottom. You can weld the portion that slides up and down to fold, or what I did was drill a hole through the tube and the clamp screw screws through the tube, securing the ring that slides up and down, so it can still fold but it’s held secure. If you have one in your hand all this will make sense. Using a hacksaw or band saw cut off the V on the end of the screw, keeping all the length you can of the screw, the screw is solid steel, so take a 1/2” bit and drill into the sawed off part to center the jack point. To jack the airplane up, position the jack stand under the airplane with the screw fully screwed in, then simply put the jack under the center of the stand and start jacking, as the airplane is lifted keep the barbell looking locking ring tightened so if the jack fails the aircraft can’t fall. Watch the jack stand legs, for some reason one may not be carrying its share of the weight, the BFH is to make an impact adjustment so that all three legs are carrying the load, check that every inch or two. Once fully lifted I take the load off of the jack, but keep it there just in case. Your not getting it out anyway as the piston won’t collapse without weight on it https://www.amazon.com/dp/B09Z367HM5?ref=ppx_yo2ov_dt_b_product_details&th=1 https://www.amazon.com/dp/B07WTKXP1V?psc=1&ref=ppx_yo2ov_dt_b_product_details Personally I think it’s more secure than most aircraft jacks and as it doesn’t rely on hydraulics to hold the airplane up, just to lift it, and even then if you keep moving the lock down even if the jack blew nothing bad would happen, the airplane would drop the 1/4” or so that you had the lock up. The little jack just barely fits under the stand, but it does fit. Whole thing took less than an hour to put together. The down side is your limited by the length of the screw portion how much you can raise it as a jack. Ideal would be about an 18” screw with lock ring that would give you over a foot of lift.
-
Weight is I think the issue with that, these stands I’m looking at fold up, but I suspect will still be so heavy shipping would be expensive. Having said that it’s supposed to arrive today, Amazon shipped the thing via Fed-ex. Give me a day or two and I should at least know if it’s viable or not, I already bought a little 2 ton bottle jack that will of course do the lifting. I expect cost wise for one to be maybe $100 or so?
-
You know I hate to say it, but there are a lot of things like that. We magnaflux connecting rods and crankshafts during overhaul, but it’s just not realistic to do so any other time and rods and crankshafts do occasionally let go from cracking. You takes your chances when you buy a ticket, we do what we can to reduce risks, but you can’t drive them to zero. But in your case I’d take solace in knowing what the main spar failure rate is, and what the cause was. Have any failed without being subjected to extreme overload?
-
I don’t think it has anything to do with being a Rocket, I think it’s an MVP-50 thing. Fortunately it’s very easy to re-calibrate, hardest part will be getting the tanks empty, and you may have to call EI and get a one time use code. I’m not sure there, but they will know, give them a call they are very helpful. At least a Mooney is at or close to flight attitude, tailwheel aircraft have to have the tail lifted high to calibrate. It’s been a few years, but I’ve set up dozens of MVP-50T’s, the T just means turbine, but it’s nearly identical to a “P” The Fuel burned calibration is also very easy to do and very accurate, I’d recommending burning several loads of fuel, doesn’t matter how far down you burn the tanks just keep up with the total, then go into the add fuel page and it will read something along the lines of you burned 100 gls and a spot for you to put actual fuel burned, then it will tell you the difference and ask if you want it to recompute, answer yes and your good. You may want to write down the K factor, because one day if you accidentally really screw up, simply re-enter the K factor and your back right where you were. The larger the amount of fuel you’re working with the more accurate the adjustment will be. I could get fuel burn within a gallon in a crop duster that held 228 gls. The MVP-50 is an astonishingly accurate and powerful device and thankfully the senders are readily available and reasonably priced. Depending on if you have EI fuel sending units or not you may have a little black box that your factory Mooney sending units attach to that converts something so they will work with the MVP. If you don’t have the manual I’d download them and read about it. I believe you can find all the manuals here https://iflyei.com/product/mvp-50p-engine-monitor/
-
So fas as I know no CAR 3 airplane has life limits. Except when those are imposed by AD, one I’m most familiar with most is main spar life limits on Thrush Crop Dusters. FAR 23 requires life limits. I can’t quote Chapt and Verse but the Thrush S2R-T660 is the only fully FAR 23 crop duster and it has several life limited components, all in the wing. I wasn’t there when that aircraft was Certified. CAR 3 has some verbiage along the lines of fatigue must be considered where FAR 23 requires it to be calculated or similar language. You get very different “scatter factors” from analysis and testing. For instance Analysis gave the new wing spar life limit of 29,000 hours, but with the H-80 we instrumented the aircraft and I went out and flew test points and testing moved the life limit to 60,000 hours, we could have gotten more but doubling it sounded good and why bother? FAA drug us into being FAR 23 compliant with wing spars as the old design had failed, killing people and was the subject of several AD’s, the new spar was a terminating action. I said fully FAR 23 compliant because it’s normal if you Certify something new under CAR 3 because it’s an existing design for the FAA to force you into FAR 23 in some instances so you meet some FAR 23 standards but still have a CAR 3 airplane. Mooney has I believe some recommended replacement intervals like the unavailable no back spring, but it’s not life limited. Life limited means you must whether you fly part 91 or not. FAA is of the opinion that everything fatigues and will eventually fail, but that’s not true. If for example I gave you a rail road spike and told you to bend it back and forth by hand it will never break, because you can’t impart enough force by hand to fatigue it. If an FAA person ever tells you that everything fatigues, ask them what the 172’s wing spar life limit. Apparently if flown within certified limits it’s outside of the fatigue cycle. So it’s possible to build something that doesn’t fatigue. But it’s incorrect to state that aluminum won’t fatigue for 10’s of thousands of hours, older Air Tractor aluminum wing spars fatigue and break way before then. Nothing magic about aluminum, Titanium? Yeah there may be some magic there, but good ole 4130 or better 4340 steel can be made to where it will outlast the airplane, just takes a re-design. https://www.federalregister.gov/documents/2008/04/28/E8-9058/airworthiness-directives-air-tractor-inc-models-at-300-at-301-at-302-at-400-and-at-400a-airplanes
-
VG’s on Ag planes are a somewhat mixed issue. You see a fully loaded Ag plane has a very high stall speed, an Ag plane often has a useful load that exceeds it’s empty weight and the stall speed requirement doesn’t include the hopper, so in a normal turn when heavy they are nibbling at stall. Almost all Ag operators either bend the stall warning to shut the thing up or otherwise disable the thing as it gets obnoxious listening to it in nearly every turn Some aircraft like the Thrush enjoy a good safety record largely because they have very gentle stalls, and in the case of the Thrush the pre-stall buffet is very pronounced and comes well before the actual stall. If you have any Piper 140 time they stall just like a 140, that is power off level flight they don’t really even stall, just mush but you have full control in all axis. So as VG’s do in fact lower the stall speed by slightly increasing the critical angle of attack one would think they be the best thing going for an Ag plane and in fact as they are so easy to apply and very cheap would come from the factory already installed. ( You see there are many Countries in the world that do not accept US STC’s) but of course do the TC. Well here’s the problem, while VG’s do in fact lower the stall speed slightly, they do make the stall break more abrupt, which in the case of the Thrush is OK, but only because it has such a benign stall, not all Ag planes do. So I had Annie Brogan (Microaerodynamics VG’s) spend some time at the factory and we installed some kits on different aircraft with her DER doing the flights, got the STC’s and incorporated them into our Type Certificate as optional, so people in Countries that won’t accept a US STC can install them, plus it makes their installation easier as it’s not a supplement, they are part of the TC. By the way I got very attractive pricing from her so that I could put them on at the factory if a buyer wanted them, they were popular in Central America, not so much in the US. If anyone who has them installed is going to re-paint she will sell you a re-paint kit at a fraction of what a kit with STC cost. It’s the same kit, just no STC Best way to install them is on a bare metal wing, they are installed with Loctite Depend adhesive, which is an astonishingly strong adhesive, but if installed onto a painted wing the paint bond is what will let go when a refueler drags the hose on the wing or a brush hits one in washing the airplane etc. But if glued directly to the metal they will bend before the glue lets go. However I agree that VG’s on a Mooney is a strange thing, I won’t argue that they do slightly decrease stall, but as a Mooney’s mission almost always is from one long paved runway to another it makes you wonder why they are needed as there IS a slight decrease in high speed cruise and as so many spend big bucks decreasing drag even slightly it would seem curious as to why they are on a Mooney.
-
I’m going to throw this out there, but if you get used to it, you actually can land slightly shorter carrying just a little power, the trick of course it to get the airplane behind the power curve and it will land quite quickly, no float. The reason people have so much trouble with a Mooney is because they carry too much speed over the numbers and wait for drag to slow the airplane to land, because that was how they were taught to land, a Mooney of course has less drag so it slows much less than other aircraft we are used to, so it’s thought that a Mooney “floats”. If you get the airspeed right then you cross the numbers and flare and she lands right away, even with a high idle, but that airspeed is lower than many think. Best way in my opinion to master a Mooney landing is always try for a “spot” landing, that is to always touch down at a planned spot as opposed to just waiting for it to settle because you have a mile of runway and can. Just don’t get obsessed with hitting the spot, if today it’s going to be long, fine keep the nose up, she will land, never drop the nose to hit the spot, go around if you have to. Eventually it will just become the way you land. Oh, my idle is whatever the manual calls for and I regularly land in well less than 2,000 ft grass strips all the time, you just get used to it after awhile, it’s not hard, like riding a bicycle was tough at first, now second nature. I’m not saying to immediately got out and try short fields, work up to it slowly and don’t cheat and use brakes, you’ll end up with flat spotted tires if you do.
-
Anybody want to help me change a tire in Manassas?
A64Pilot replied to wombat's topic in General Mooney Talk
If it’s losing air, take the valve cap off and put some spit on the hole, if it bubbles of course the valve is loose, if so it’s an easy fix. Be sure you always have the metal yellow cap that has an O-ring in it too, don’t use a cap without the O-ring, it’s a back up in case the valve starts to leak. I had one that did and landed a C-210 with a flat nose wheel, it really scares you, your sure the nose wheel has collapsed but it did no damage. I don’t think the big motor Mooney’s carry much if any more weight on the nose wheel, if they did of course the CG would be way forward, but maybe they have a much further allowable fwd CG limit? Never flown one so I don’t know. -
You know I would have bet money on that too, you can feel the boat speed up just as she breaks onto plane and once your over that hump you can back off a little and stay there, everybody knows just on plane is the most efficient speed. oh and trim tabs help. But I had the same results on our little dive boat, a 21’ CC with a 175 HP Mercury Verado. Sometimes things your sure of break down when actually tested, you have to have instrumentation though, on the dive boat it was easy, the Garmin Radar / Plotter was connected to the Verado’s Can Bus and gave instaneous MPG. On edit if graphed speed on the bottom and fuel on the side, it gets very steep climbing onto plane, but there was no steep decline just after it broke onto plane, rather the curve flattened out, then as speed increased began to rise again. If only max range was the issue and time not considered, best MPG was at idle, by a surprising amount, but who can idle around to travel. To continue this on a boat anyway fuel consumption vs speed began to climb the moment you started to have a wake, which makes sense because the energy to roll that wake of course comes from your gas tank. When we were cruising that was something that the Trawler guys didn’t like to hear. Now for most engines there is a “magic” RPM, that is one RPM where the BSFC is greatest, but the drag cost of increased speed overcomes it. For example there are a great many people that are convinced their car gets better fuel mileage at say 70 mph than any lower speed, but that’s not the case unfortunately. The 55 MPH speed limit did work, but it drove me nuts. On edit, if you have ever flow a float airplane you plow along at full throttle until it gets on step, then once on step it will accelerate quickly and fly, but if your heavy getting on step seems to take forever, obviously there is a decrease in drag once it gets on step, but it still takes quite a bit of power to stay there, so intuitively it seems obvious that step taxiing is much more efficient than being off the step, but for some reason the numbers show it’s not. I haven’t tested an airplane, but use it as an example because, well this is an airplane forum.
-
Go out and pick a smooth RPM, then start at some low GPH just LOP let speed stabilize, increase 1 GPH or smaller number if you prefer. At each test point write down GPH and A/S. Then take them and graph them, there won’t be one point that fuel consumption suddenly takes off, it will be a steadily increasing arc that gets steeper as speed increases. Now if by chance there is one point that shows a definite knee in the curve, then Voila you have found your “best” airspeed, but I suspect you won’t find a definitive knee. One a similar note, We had a couple of Sportfish over the years and would run out of the Panhandle of Fl to the Middle Grounds, close to the middle of the Gulf, then stay and fish all day Sat and also Sun if we had enough fuel and run all night getting back. So fuel consumption very much determined fishing time, I had flo scan on both engines and was certain that the point of just breaking onto plane would give me my best MPG, but graphing it showed my gut was wrong. I did it on two different boats, one gas, one Diesel, both were the same, unfortunately there was no sweet spot. So the speed we went out at was determined by how big a hurry we were to get there, faster burned more fuel. Not saying a boat is an airplane, it’s not, because a boat will float at zero speed, you can’t get behind the power curve on a boat, but can in an airplane, but if you only are interested at above best glide A/S I bet it will be pretty much like the boats were. If you can handle 118 KIAS then have at it, I can’t just too slow and I can’t keep the engine temps up, and if I abandon LOP to warm up the engine, the. that sort of defeats the purpose doesn’t it?
-
I understand that, however I never fly at FL anything, much less 180. What happens of course for us N/A guys is that if you climb high enough you end up at Carson’s speed or lower and since your WOT that’s what speed your flying at. But that’s like arguing that LOP isn’t viable, because in the FL’s your NA airplane can’t make enough power to get there. Carson’s speed is an arbitrary number, slower and MPG increases, faster and it decreases. Supposedly it’s equally weighted economy and speed, but how do you do that? It probably wouldn’t be hard to come up with a much higher number than Carson’s speed if in fact TBO of the engine and prop were added to fuel burn. If you assume 50K for an engine overhaul and 2,000 hr tbo, then that alone is $25 an hour, add in prop and oil changes and someone could likely “prove” it costs less to go faster and burn more GPH because of the lower operating time. I’m sure the Airlines long ago got this down to a science, but I have no idea what their calculations are, but bet if they could save money by cruising 20 kts slower or faster whether IAS or not they would.
-
Anybody want to help me change a tire in Manassas?
A64Pilot replied to wombat's topic in General Mooney Talk
I don’t know of anything that’s says it’s prohibited, but it is contrary to best practice, but from your description of what it sounds like, a patch isn’t likely to fix it. -
While I’ve not taken a chinese jack apart, on hydraulic cylinders there is usually a wiper seal whose job is to keep the cylinder free from dirt. There isn’t one here? https://www.skf.com/us/products/industrial-seals/hydraulic-seals/wiper-seals
-
I don’t understand, what’s wrong with ships altimeter and clock?
-
Cut n pasted from the article I quoted, from my testing of two different STOL aircraft, a Maule and a turbine crop duster, I concur, there is a small speed loss, it’s not huge, but it’s real and the faster you try to cruise the greater the speed loss, of course that’s how drag works I didn’t have an airspeed boom on the Maule so it’s stall speed is hard to quantify (at steep angles of attack A/S indicators become inaccurate) but I did have one on the Crop Duster. “As part of adding VGs to a Cessna 182J that already had a STOL kit (see sidebar at left), we did before and after cruise speed comparisons at 65, 75 and 80 percent power. We observed a TAS loss of 1 MPH at 65 and 75 percent power (which we think is within measurement error). Going to 80 percent, well above what we think most pilots use, we saw a TAS loss of 5 MPH.” The Maule was notorious for its small ailerons becoming ineffective at very slow speeds, and the VG’s helped greatly with that. On both the Maule and the crop duster although the stall speed was decreased, the break was more pronounced, but as both aircraft had gentle breaks it wasn’t much of an issue, in an aircraft with a much more pronounced break, it might be.
-
All I’ll add is that in theory VG’s promote laminar flow https://www.aviationconsumer.com/accessories/vortex-generators-got-stol-think-twice/ However they add drag doing so, in my testing of a very dissimilar aircraft they do knock off a kt or two from stall, but also the same amount from high speed cruise. There just ain’t no such thing as a free lunch. On some aircraft that suffer from control lack of authority at low speeds they can really help with that. In my testing I’d say they may work really well if you have an airflow separation at a particular area, but so far as putting them full span on an aircraft with no problems, in my opinion it’s not worthwhile. Apparently most manufacturers seem to agree, because I know of very few that come from the factory with full span VG’s.
-
Cylinder peaks way behind others
A64Pilot replied to lithium366's topic in Vintage Mooneys (pre-J models)
I’d be tempted to screw in an automobile compression tester and spin it over, throttle fully open and see what the compression is, compared to another cylinder. -
I’ve considered the hole myself, but you could damage the seal, so I think if you do drill a hole be careful to chamfer / deburr the hole and you should be fine. I’ve considered the clamp lock collar for my engine hoist too as I use it to lift the nose, I need to do something there.
-
You were fine there. I’m usually down low due to short flights and I run usually about 50C LOP but will enrichen in cooler Wx to keep cyl head temps up. I don’t have an analyzer just the factory instruments, so I set at power setting low enough and lean enough so that I’m sure I can’t hurt anything. Not being able to watch each cyl independently I just run conservatively. Normal cruise for me is 8GPH, which calculates out to 60% power. If you go high enough it’s likely you may decide to run richer as you just lose so much power LOP, but at that point power is down so much you can’t hurt anything with any mixture. People have run LOP for decades to save fuel before engine analyzers, so you can do so safely so long as your conservative. Most efficient is richer than that, but in truth at that point we are splitting hairs. On edit these IO-360’s are the poster children for LOP, I’ve never seen any other engine run so well LOP, my IO-540 and IO-520 sure wouldn’t.
-
Yeah, I’ve sort of abandoned the 9” base idea for the reason you state, so either make a jack from a jack stand that has a proper base, or extend the base on the initial jack stand. Leaning towards making a strong stand into a jack Majority of the factory solutions are pretty much a 24” Chinese jack, a simple X base with electrical conduit braces. An hour or two’s work and maybe $150 ea to duplicate a $400 jack. Way back in the day, 1980 to be precise I started my working life as an oilfield contract welder, then of course the oilfield collapsed, but I’m not a bad welder. Its a long story but I got rid of almost all of my tools a few years ago, and have ordered a cheapo Chinese 200Amp DC welder, some 3/32 7018 welding rod etc and will most likely try to knock up something, whether it’s copy a jackhouse etc jack or convert a stand into a jack will I think depend on how well made and robust one of the stands are. I like the idea of the jack only being used to lift the airplane, once lifted aircraft is supported by a stand that’s very strong and stable over a jack that relies on an O-ring in a Chinese cylinder to hold my airplane up.
-
That’s easy, chop saw or band saw or even a die grinder and cut off wheel. Then once removed I think weld on a heavy duty fender washer, the hole in the fender washer of course holds the jack point secure