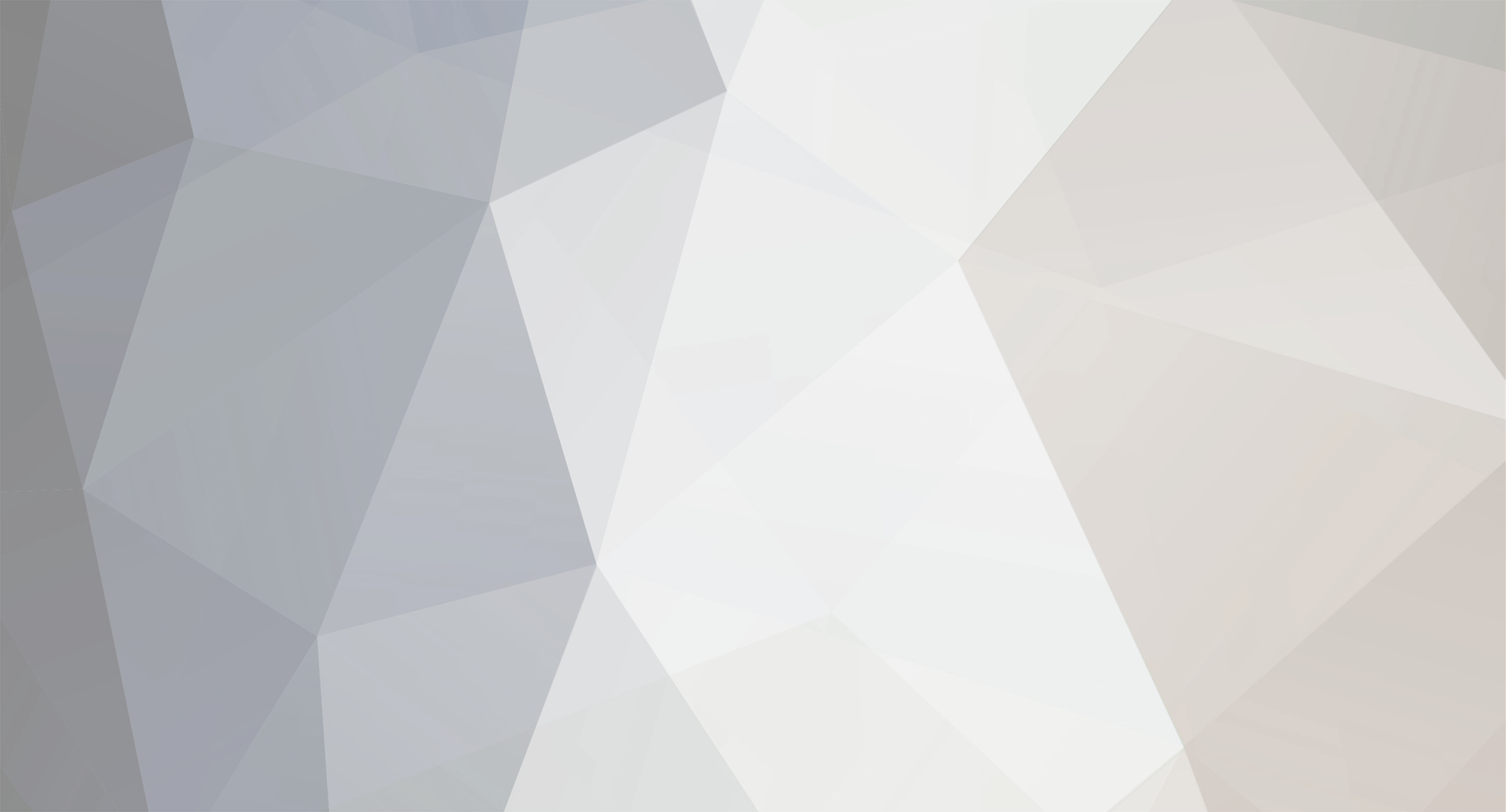
A64Pilot
Basic Member-
Posts
7,988 -
Joined
-
Last visited
-
Days Won
21
Content Type
Profiles
Forums
Blogs
Gallery
Downloads
Media Demo
Events
Everything posted by A64Pilot
-
Sigh, Shock cooling is not a myth, statements like if it was real then shock heating would ruin engines on takeoff etc are non sensical. As is the belief that sudden engine cooling is going to result in sudden engine destruction. There are very few if any limitations that exceedence results in nearly instant damage. Like the avoid 1500 - 2000 RPM at manifold pressures below 15” MP on my J. Some people ignore it saying it’s a myth, thinking I did it a few times and nothing bad happened so it’s not real, but the damage is real, it’s cumulative. Like over revving, or exceeding the redline on cyl head temp, just because the engine didn’t seize doesn’t mean you didn’t cause damage. Ever wonder why some seem to crack cylinder heads and others don’t? Just like dropping gear at max extension speed causes higher wear than if you don’t. In almost all limitations there is no exact point where below it causes no additional wear but above it causes instant damage, even VNE isn’t like that. I know someone that hit VNE with the flaps in T/O position and it didn’t damage anything, does that mean that there is no airspeed limit for flaps in the T/O position? Of course not. Most damage is fatigue induced, and fatigue doesn’t come from one time occurrences. As much as practicable, avoiding operations at the limits and rapid changes will result in longer component life, and that’s true for everything from slamming on the brakes to overheating starters as well as engines
-
Anything going on? Have the problems stopped? Are they selling fuel still? I would have thought by now I would have heard something, but it seems to have gone away, where I would have thought with time things would have worsened.
-
Fine wires I think should be good, I’ve never done it but feel sure you can check resistance without pulling the plugs, would of course have to remove the wire, but I’m afraid that’s honestly not it. If you swapped them from another cylinder, and the problem reoccurred in the same cylinder, there is an almost zero chance that’s it’s plugs. If your sure it’s not valves, then the only other likely possibility that jumps out is Injection or ignition, might not hurt to do a flow test and possibly clean that injector, very unlikely I know, but I like to troubleshoot with the free stuff, then the easy stuff before I start spending money myself. If nothing else you eliminate systems. It could be an ignition wire or even cap. If it happens to you again if you can do a mag check looking for increased EGT on the “bad” cylinder, if a plug isn’t firing then of course you won’t get a rise when you turn off that plug in that cylinder but will of course on the others whether the cause be the cap, plug or wire. I’m afraid that testing when it’s running fine won’t show anything, because it’s not “broke” then. Call Lycoming’s help desk, they are very knowledgeable and they don’t cost anything.
-
They might depends entirely on insured hull value, but if they do I’d love to have it, it would be a cheap and easy fix to resell.
-
Understood, my main point is to keep looking. However if the reamer is of the right size and the guide is also correctly sized the reamer won’t do anything, it will only remove metal if the guide is undersized, but I understand if it ain’t broke, don’t fix it. Try this, exchange the plugs with another cylinder, it’s rare but sometimes you just get a “bad” plug, one that fires correctly when hot but not so much when cold, if it’s a bad plug then the problem will move to the other cylinder. This is unlikely, but it costs no money, is easy and does no harm, so eliminate plugs as a possibility. Oh and check the plug resistance when you have them out especially if the are Champion’s, many say resistance doesn’t matter but by definition high resistance resists electrical flow wasting some energy as heat, the result is less current to the electrodes
-
Yeah I’m sure he was overly stressed and not at the top of his game after prop striking the airplane.
-
You should still ream them, but do so slowly to keep a smooth finish, they may just be tight, it happens. Ideal world valve guides are honed not reamed, the finish is important. A Sodium filled valve runs cooler, it does so by transferring the heat from the head to the stem better, the stem then transfers the heat to the head of course, but the stem in a sodium filled valve runs hotter than an unfilled one as metal expands with heat, if you run LOP as I do your EGT is higher than ROP which could run a valve slightly hotter. It’s though that Lycomings are more susceptible to sticking valves due to sodium filled valves. Not taking away from LOP, as I said except for high power I run LOP myself. Sticking valves can lead to bad outcomes
-
I have seen more than one R-1340 that will stick exh valves unless MMO is added to the fuel. Having said that I don’t run any additives in my airplane. Unless things have changed MMO is not approved, but it’s been widely used for decades, probably before I was born. Who formulated it and what it was formulated for is an interesting story. https://marvelmysteryoil.com/pages/our-story I have heard but do not know that’s it has changed ownership and they changed the formulation, I don’t know if any of that is true. It does keep my air tools clean and I think lubricated.
-
I guess the guy in the video crashed and died right, must have There are limits to everything, I never land beyond the first 1/3 of the runway, usually much less, so I have thousands of feet left. Add power if it’s not smooth and accelerating you’re going to land anyway, if you stall and crash it wasn’t the prop or engine, it was you. Not much can happen to an engine and prop to make the flight controls inoperative. Of course I hope to never land gear up, but concede it could happen to anyone that’s been studied and proven decades ago. However if I almost do and by instinct pull up and add power and she’s accelerating, I’m likely not to chop to idle and let it settle onto the runway. I like to think I’d drop gear and land in the last 1/3, but who knows maybe I would go around Face it, that wasn’t planned, nobody thinks that fast, instinct got him away from the runway and yes he made the decision to continue. I think it likely that he was one in a hundred anyway, I think it’s very unlikely for my reactions to be so fast that I could pull that off, I bet 99 out of 100 people are sliding down the runway prop stopped wondering what happened
-
I disagree for many reasons, but it all depends on condition and price and we can’t tell any of that on the internet, sure worth a look I think 1. Compression is no big deal, worst case it needs cylinders, my bet is it won’t, but use it as a bargaining point on price, can even be a good thing, because you might get a good deal and odds are they will be fine with some flying, a borescope will tell the tale. 2. Low hours flown, usually low time airplanes sell for more, but the add for me is always hangared, many airplanes aren’t and I believe sitting outside in the Wx is a killer. 3. Prop strike is another not a big deal, actually I think it’s a value add, because he now has an engine that has been overhauled, but prop strike inspections often add years and hundreds of hours to the life of an engine due to all the wear parts that are replaced. Old Avionics? From 98? For most of us that’s not old, but the potential buyer has said he wants to pick his Avionics anyway so no big deal Finally how many 98 Model Mooney’s are for sale? Depending on condition and price this could be a heck of a buy, the interior and paint for instance if truly always hangared ought to be pretty close to pristine. I’d take nearly pristine factory paint myself over even a new paint job because paint stripper is hard on the airframe.
-
You have had some good answers already. I’ll tell you what I do on most Annuals now, but of course this is what I do, I’m not saying it’s what should be done by others, but I believe each aircraft and the conditions and frequency it’s operated and stored in should be taken into consideration. Realize my Annuals I do are for older Retired guys with Champs, Cubs and the like, not fire breathing twin turbo complex aircraft that fly in the flight levels and fly hundreds of hours a year, none fly 100. They also almost never spend a night outside or in the rain. The problem as I see it is there is an attempt to cover every aircraft flown in every environment under every condition with one yearly inspection, then add in the most conservative response is to do it and we see why wheels are pulled on aircraft that fly less than 50 hours a year and have never been rained on. The FAA relies and gives mechanics the ability to use their experience to adjust the scope of an inspection, but not the frequency. I jack up the wheel, check for radial and axial play, spin it, check for noise and smoothness, in my opinion I have inspected the bearings. Fuel injectors, comply with the AD of course, check for condition and security, leaks and if operation is normal I don’t remove them. I do clean, inspect and repack bearings if the wheels are removed like for example tire replacements. If aircraft wheels were sealed as well as automobiles are then we could not bother but they aren’t, if water ever gets to the axle for example, they need to be repacked. I do check engine oil filters / screens and we usually change the oil, but if it was changed last month and 5 hours ago I recommend we don’t. Compression test, borescope, check / adjust timing. Rarely bead blast plugs, I’m of the dig the carbon / lead out and don’t blast myself. I do check resistance. Condition and security of everything else. I do require checking of all flight and engine control ends as in every bell crank pulley etc, run a Cossosion-X soaked rag over every inch of control cables looking for meat hooks, pulleys for wear / play etc. Gascolators are just too easy not to do, and occasionally I find evidence of deteriorating fuel lines, looks like black granular bits. I think that’s often what clogs injectors (opinion) Owner does all of the manual work, cleaning, and usually if we have to pull mags etc they do so under my supervision, now not all are at the level I’m comfortable with, for those I do the technical stuff myself. For that I charge $300 and I approach Annuals as a teaching event for the owner. Not that I want or expect them to do more than they should unsupervised but I think it helps understand how things work if you took it apart and put it back together yourself. Those that own and fly twin Comanche’s, Bonanza’s and the like there are local Professional shops that usually specialize in a Type that I recommend for them.
-
I’ve said that so many times here for many to decry that I don’t know what I’m talking about etc that I’ve stopped. An Annual is not a maintenance activity or servicing, it’s an Inspection activity, it’s in the name. Sure there can be excellent pre-buys, however there is no definition of a pre-buy, as far as the FAA is concerned there is no such thing. There is no list of things that must be inspected. A Pre-buy can be a pre-flight or a nearly complete tear down, if you insist on a Pre-buy for God’s sake have a written contract where every inspection you want performed is listed and signed off with results noted. I won’t perform a Pre-buy myself without the purchaser participating, but I’m Retired and not having to make a living turning wrenches. However the Annual is defined, it has a min performance requirement etc. Any IA that’s not a fool treats an Annual seriously as their Professional License is on the line, pre-buy they may have the new kid do because they are busy and the purchaser wants it done now, who knows? Any decent mechanic if conducting a pre buy can tell you on day one if you ought to give this airplane a pass or it’s most probably a good one. If they say it’s most likely a good one, then in my opinion you turn that pre-buy into an Annual, which of course takes an IA. If they tell you they keep running into sloppy maintenance and unairworthy items, then let it pass. Ideally you want the person who you intend to care for the airplane to conduct the pre-buy / Annual. That way they have skin in the game. There have been many posts in this forum that I have read that talk about the serious issues found on the first Annual, that were missed on the pre-buy. Most mechanics take an Annual more seriously, because it’s legally defined and has a list of items that must be inspected. They can get into trouble with an Annual, but not a pre-buy. I’m not sure why but apparently an annual for many people has turned into a major maintenance activity where there is a lot of services performed, instead of the inspection activity it’s supposed to be, maybe it’s to increase revenue, or more likely it’s because the owner wants to get all that over with at one time, rather than performing such servicing themselves as preventative maintenance. Most pilots I guess will not even change oil, some shouldn’t.
-
This, So far as worrying about pulling jugs, it’s been done frequently for way over 60 years, a qualified knowledgeable mechanic won’t screw up, plus you have new jugs, so it’s pull one, replace it. Sure someone who isn’t can cause problems, so use a good engine shop or be darn sure the A&P is good, don’t go to someone your not sure about. The problem comes when the jugs are off, without the studs being retorqued and the aircraft sits for quite awhile while the jugs are being overhauled etc and someone moves the prop. Or possibly an unknowing mechanic rotates the engine with cylinders off to position it to remove pistons on the other cylinders. Simply relaxing the torque and retorqueing without turning the prop won’t cause any issues, the bearings won’t move unless the crank is turned. I would however have a good engine shop rework the valves and possibly guides though, maybe even port and polish them. I’d call Gann Aviation and ask if he would. Conti was notorious for sloppy valve guides as in very poor finish, don’t know if that’s old news or not, maybe they fixed that long ago. So far as treating just the offending cylinder, it works for some, but also some end up spending way more money in the long run and buying lots more down time having the airplane in the shop to replace the next jug that goes bad, the one after that etc. Sure sometimes a jug goes bad and the other 5 are pristine, but more often I think one goes bad and the rest are not too far behind, if you flew infrequently and not that many hours per year, maybe one at a time is the way, but if you fly a lot and don’t want to eat down time, I think removing cylinders as a problem for several years may be a better bet.
-
It wouldn’t fly if it did. You didn’t read my post apparently, it’s not so much save the insurance company, it’s save the airplane. That engine stopped running when the prop quit turning.
-
I’d go around just like he did. What am I saving? Very likely the aircraft, odds are very good the insured value, if even fully insured of a 1963 Mooney could well be less than the cost to repair. Gear it up and I think it’s going to the scrap yard and one less Mooney in the world. Remember if your insured for say 100K, they won’t pay 100K to fix it, they will pay 100 minus the salvage value, which I’m unsure what that is but have heard 20%, but that’s hear say so it may be not even close. I think it unlikely a 63 model would be insured that high but don’t have any idea what the average 63 sells for. If it wasn’t fully insured, I could fix that aircraft for the cost of a used serviceable prop, and whatever the gear on the back of the crank cost, I think that’s the one anyway. I bet there are some around from people “upgrading” to a three blade. I’ve inspected several engines after a prop strike, yet to condemn one and can’t really imagine if still running that it won’t stay that way. Is there a risk? Sure, but I’d take it as I think it pretty small.
-
At that age of aircraft it’s likely most will have some issues, most anything can be fixed so of course the consideration is cost. Corrosion is the exception, there are I’m sure several aircraft that have enough corrosion to make them uneconomical to repair, that should I think be your major concern. You really, really want the pedal extensions. I’m 5’10” and installed the 3” to get my knees from hitting the nose gear enclosure, and I think it put me right where I want to be yoke position wise. I’d suspect with the seat full forward and a cushion behind your back it might be difficult to get the yoke full back for landing etc. My original rollers were Phenolic, I believe they wear the aluminum as evidenced by the surface was covered by aluminum oxide, plus as they wear down the steel part of the seat frame scrapes the rails and wears them. It’s my opinion that the softer nylon won’t cause as much wear, but they may not last as long as the phenolic. Something has to wear, I’d rather that be the rollers than the rails myself. I think maybe keeping them clean and free of sand etc might also help.
-
Static wicks what benefit do they serve?
A64Pilot replied to Will.iam's topic in Modern Mooney Discussion
Probably any of the above would help. I think it’s more likely corrosion than current discharge causing the problem. DC-4 I think, it’s clean and doesn’t make a mess like some do, it’s called light bulb grease because many put it on trailer tail light bulbs to prevent corrosion when backing the trailer into water, especially salt water. Helicopters build so much static because the rotor system speed is in the hundreds of kts even with the machine at a hover. I have never seen static issues in small GA aircraft, but then I only have a few thousand hours myself. I suspect Mooney put them on for marketing as much as anything, lots of things are done primarily for appearance reasons and not performance -
I watched the video, they are obviously building an Experimental aircraft. That doesn’t do anything towards a Cert aircraft, nor Certification. What is that engine? I applaud their work, I’d love a Helio Courier myself, looked hard at one before buying the Maule, but the engine and I believe a wing AD sealed the deal. There are a very few Turbine ones out there, the Helio Stallion. It uses Thrush Exhaust, an owner in South Carolina owes me a ride for repairing his exhaust. I should have flown up there for the ride. Stallion was a bigger aircraft, think of it as a better looking Pilatus Porter.
-
I didn’t watch the video, but without a Production Certificate you can’t produce an airplane and sell it to the general public. I’m nearly certain that you can’t produce anything, even parts. A PMA would give you parts, but you would be unable to assemble them into an airplane. A PC would be enormously expensive to obtain and I’m sure take years to get. As far as I know Cirrus is the only one to do it in recent past. There may be others that I’m unaware of. However you can buy a PC along with the factory and start producing airplanes tomorrow if you have the required people, QC, DMIR’s etc. The PC is the only real value in Mooney, TC’s especially if they don’t have all the tooling etc don’t have much value. Assumption is all the drawings are kept by the TC holder, without drawings you really don’t have anything, just something you can frame and hang on the wall. If you own the TC, you have the “right” to do anything, having the right and the ability to pay for Certification are two completely different things.
-
Your not going to hurt the engine, I don’t know about you, but if I’m letting down from altitude at 500’ a min at cruise (23 squared) cowl flaps closed, LOP I have a hard time keeping the Cyl head temp in the green, in Florida in Summer. I often enrichen to add some warmth. When your near the bottom of the green temp wise shock cooling isn’t an issue But I’m a J model, not a Bravo. I depends on what you consider important I guess, to me I’m going to baby the gear. In truth I try to Baby the whole airplane, I’m just not one to run the guts out of it. Some are and that’s fine, I get the “I didn’t buy a Mooney to go slow” You don’t have to slow all the way to flap speed, but I can assure you as an old time A&P that if you don’t treat Maximum permissible gear speed as the normal gear speed pretty much everything in the gear will last longer. Surely none of us run the cyl head temp to redline in every climb do we? Why not, your allowed. I’ve watched time and again people hold that gear switch waiting for the instant they slow to max to drop the gear, many, heck I bet most do, I think they were taught that way.
-
In my opinion I don’t think anyone is going to worry about whether a non critical interior part came from Mooney, is otherwise approved or not. Think the Kool air scoop that goes in my ice window is STC’d or otherwise approved? I would hope not. Yes I know Rosen STC’d their visors, but surely that was some kind of marketing ploy?
-
There is a push, most likely substantiated by statics to rely more heavily on automation, automation when it works is often safer than a person. The stats for instance have been showing that automation is safer, for instance Tesla Full Self Driving is five times less likely to have an accident than hand driving and a Tesla due to the other automation is half as likely to have an accident than the average US car. https://www.torquenews.com/14335/tesla-fsd-releases-safety-data-5x-safer-normal-driving Having said that I still think it’s important to be competent driving myself and while I haven’t tracked ours yet, I’d like to just to find it’s and my limits, because whike I use FSD extensively, I don’t trust it. I don’t know anything about a Cirrus, never flown one, perhaps their Autopilot system is so well integrated and new, modern etc that it has an extreme reliability, but it’s my experience that systems in our older aircraft aren’t, very often it’s installation or other issues not directly related to the Autopilot hardware, I do know that broken or unreliable Autopilots are pretty common. Most don’t trust Vacuum pumps, I don’t although I’ve yet to have one let me down. I had a Pesco pump on the Maule and an electric standby attitude indicator. Maybe if there was a backup for the Autopilot I’d be far more likely to trust one, but so far as I know there isn’t.
-
IF there is oil in the intake, she will smoke on engine start, look for that.
-
I hear people who say “I’d never fly IFR without an Autopilot” and I think what fools, what their plan when it fails? Because one day it will. It’s all proficiency based, I used to fly my Maule without an Autopilot and a Maule isn’t a good IFR platform without issue often to ILS minimums. But I flew real IFR a LOT, now I won’t fly IFR anymore because I’m not going to put the work into it that’s required to gain and maintain proficiency, plus I don’t do the cross country like I used to that demanded IFR. My belief is if you have an Autopilot you need to fly without it often enough that your comfortable hand flying. I fear many can’t they never really trained without one.
-
The Rudder: Friend, or Foe?
A64Pilot replied to Mooneymite's topic in Mooney Safety & Accident Discussion
People who were taught in and fly “modern” aircraft really have no idea how to use the rudder, because you don’t really need to much, aileron to rudder interconnects are responsible for a lot of that. Worst I’ve ever seen was an F-16 driver trying to fly a crop duster, it ate his lunch. A Maule would have been worse as it has a lot of adverse yaw. Getting some tailwheel training will teach you what your feet are for, is fun and probably not that expensive. I thought having thousands of hours flying a tail wheel helicopter would mean that the transition would be easy, I was wrong.