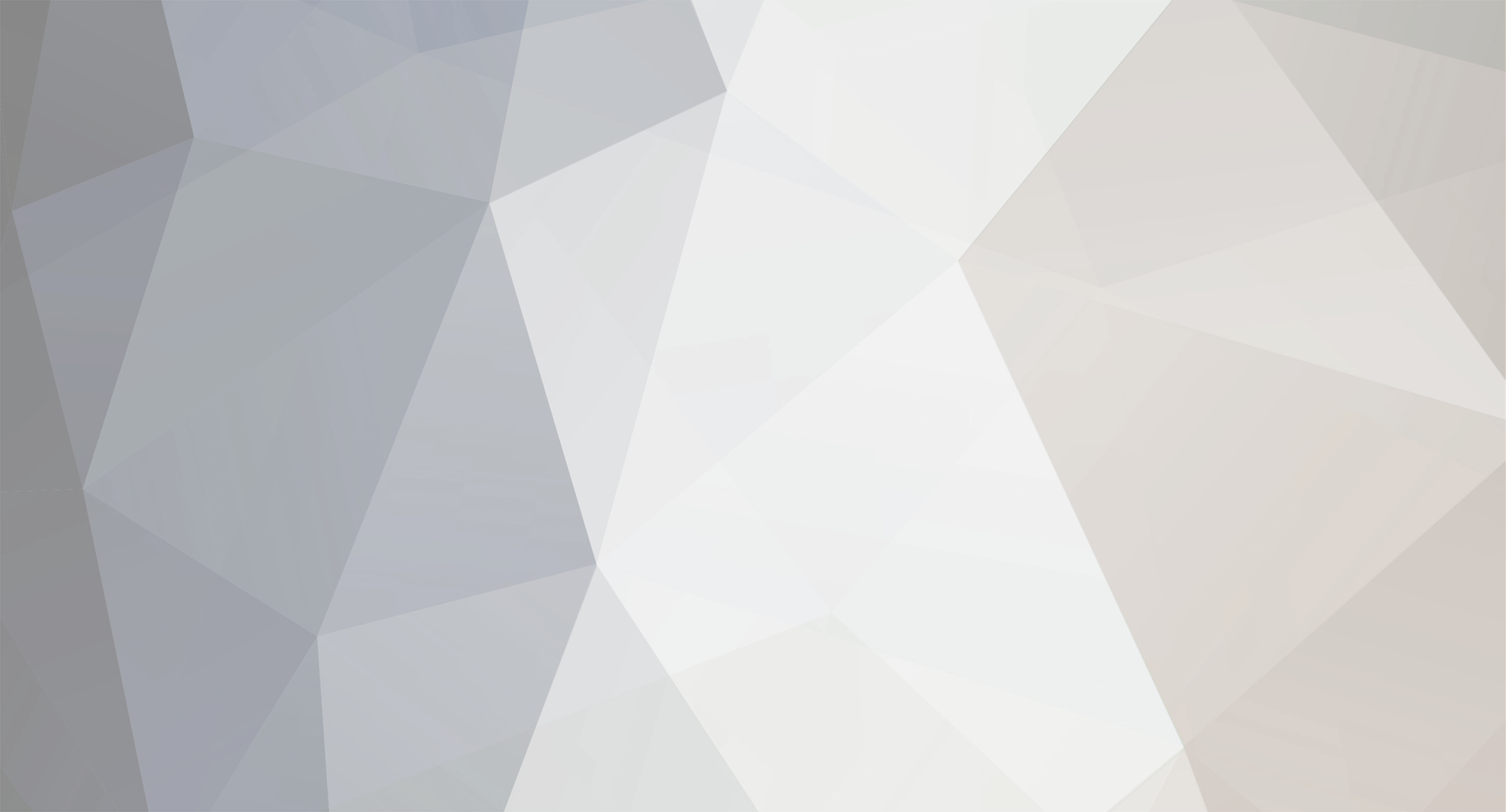
jlunseth
Basic Member-
Posts
3,753 -
Joined
-
Last visited
-
Days Won
9
Content Type
Profiles
Forums
Blogs
Gallery
Downloads
Media Demo
Events
Everything posted by jlunseth
-
Bootstrapping on takeoff with new Merlyn and intercooler
jlunseth replied to Scott H Poms's topic in Modern Mooney Discussion
The Merlyn wastegate is not a truly automatic wastegate, although I believe it has been marketed that way. It is a differential pressure controller. A differential pressure controller senses the pressure change across the throttle and tries to maintain the same pressure difference. In other words, it senses the pressure when the induction air enters the induction system, and senses the pressure on the downstream side, after the air passes the throttle, and works to keep that pressure difference the same. The idea is to reduce bootstrapping, so imagine that you takeoff and the aircraft accelerates. As it accelerates, there is a ram air effect that boosts the power output. When the power output is boosted, that in turn produces more exhaust pressure, which drives the turbo faster and outputs more compressed air. This relationship - increase in engine output increases turbo output - is not necessarily linear, in other words, an increase in power output of, say, 5%, does not necessarily mean an identical 5% increase in output from the turbo, the turbo might put out more than that, which in turn would feed back to the engine in the form of more compressed air. This can be exaggerated on takeoff when the engine starts the takeoff roll at idle, there is turbo lag before the turbo spins up, and then suddenly the turbo spins up and power output spikes. All the Merlyn does, is to try to keep that pressure differential stable, so an increase in throttle does not lead to a relatively large increase in turbo output, which feeds back into the engine, which then feeds into the turbo, etc. The Merlyn is very much an "all things remaining equal" type of system. If something happens to cause MP to rise, such as ram air, the Merlyn does not try to maintain the original MP, rather, it continues to try to keep the pressure difference across the throttle, the same. Thus, MP rises, it results in an increase in turbo output, just not a high spike in turbo output. The Merlyn does some other things as well, but they are not related to the differential pressure regulation. One principal additional advantage over the fixed wastegate is that the Merlyn can fully close and fully open. A fixed wastegate has a fixed opening, it is always wasting some amount of exhaust overboard. A 231 with a fixed wastegate has a critical altitude of about 15,000 (dependent on day pressure and temp). At that point the turbo is working as hard as it possibly can, the fixed wastegate vents some exhaust overboard. The Merlyn, on the other hand, can fully close, so the turbo can output more compressed air at higher altitudes. The critical altitude in my aircraft, with a Merlyn, is about 22,500. Technically, CA is when the aircraft can no longer maintain a climb rate of 100 ft. per minute. My personal definition is simpler, and that is when the throttle stem is fully in and the engine can no longer make 100% HP if altitude continues to increase. In true carusoam tradition, let me say I am just a pilot, not an engineer nor flight instructor. However, I have had some firsthand experience with a turbocharger company and their engineers, who are pilots as well. Hopefully I am translating their education correctly. -
Bootstrapping on takeoff with new Merlyn and intercooler
jlunseth replied to Scott H Poms's topic in Modern Mooney Discussion
Well, wait. What do you suppose a turbocharger does when it spins up? You should be getting a distinct surge in power when you push the throttle in for takeoff. This is a good thing, it means you have a turbo. If you are a former NA pilot used to a set and forget throttle you just need to learn new technique. The Merlyn does not stop the turbocharger from working the way a turbocharger works. Bootstrapping is when the turbo and engine start to chase each other, up and down, back and forth. On takeoff you put in about half or 60% throttle, you let the turbo kick in, then you progressively push the throttle in to make full power. You can’t shove the throttle around in a 231, with or without a Merlyn. -
5 & 6 are right at the intake holes, as opposed to 1 & 2, which sit behind all the other cylinders. One of 5 & 6 is partially blocked and the other is not. I don't remember without looking what is there doing the blocking, I think it is the intake scoop for the induction system, but not sure. It would be nice if the CHTs were all within a few degrees of each other but that is generally not the case. My 6, sitting right in the unblocked intake hole, is generally cooler than the others. Rather than comparing 5 to 6, I am more interested in the variation across all six. If your 5 is the hottest and your six is the coolest, and all the others are in between, that is not a bad spread based on what I see on my engine and tweaking the baffling might help. The other contributor to temp differentials is how evenly the fuel flow is between the cylinders, if you run ROP and have one that is persistently significantly leaner, that could be your warmer cylinder. The usual cure for that is GAMIs if you don't already have them. But I think you are chasing a spread that is pretty normal given the layout and untuned induction system of the engine and compartment. Now that I said that, someone will have a TSIO360 where all the cylinders are running within a few degrees of each other.
-
I'd say the fluctuations are on the outside edge of what you might see with updrafts and downdrafts but your aircraft is naturally faster than mine. The pickup in speed can be pronounced when you experience a downdraft, sometimes the aircraft noticeably noses down and you are running down hill. Acclaims being as slick as they are, probably that is what causes it to go over 10 kts. Usually in the vicinity of 5-10 knots, more prevalent some days than others, I have noticed them more while flying out over the Great Plains than anywhere else.
-
No, my cold cylinder is 6, it sits right in the intake hole. You are lucky if your 2 is cold, that is hiding in the back behind all the other cylinders, last to get cooling air.
-
I should clarify that my climb outs are nearly always with cowl flaps full open. In the winter it gets so cold here sometimes that it is necessary to protect the engine in the opposite direction from summer. Fall climbouts with the temps in the 40s F or cooler might be half cowl flaps, you will quickly be in below freezing temps just a couple thousand feet up. Real winter temps where we can be 20 dF down to -35 dF on the ground and the air is very dense, it is very important to keep the engine compartment as warm as possible, so I might climb with no cowl flaps at all. Can't let the OT fall below 100 dF and I have one cylinder that likes to run cold, below normal operating temp of 240.
-
Me too. There are times of the year when half cowl flaps and even no cowl flaps works fine. The key is the CHTs, I use the flaps to keep the CHTs at or under 380 if that is possible. Airspeed is also important as Paul says. There are occasionally days, usually out west in the hot days of summer, when none of that works really well and I will see one or two cylinders above 400 dF. Don't like it, but there are only so many things you can do.
-
FLAP RETRACTION AFTER TAKEOFF
jlunseth replied to DCarlton's topic in Mooney Safety & Accident Discussion
Blame it on Jack Napoli. He is the Mooney PPP instructor who taught me to put a little trim-up in for takeoff. Note, I said a little. Better to need a little back pressure on the yoke to complete the task rather than have the aircraft take nose-up overcontrol on its own. As I said, its a quarter, maybe a half inch above the "takeoff" line on my trim indicator. -
The problem with airplane ownership
jlunseth replied to N201MKTurbo's topic in Miscellaneous Aviation Talk
Its not a courtesy car unless the check engine light comes on. I always enjoy riding in the retired squad cars, some of them still have “Call 911!” on the side. Out on the highway, everyone you come up behind slows down. They see the tall bumpers, the paint job, and they want to be doing something under the speed limit. I am borrowing one later today in a small town to see my dad. I am grateful they exist. -
FLAP RETRACTION AFTER TAKEOFF
jlunseth replied to DCarlton's topic in Mooney Safety & Accident Discussion
Yes, true. However, my plane and many of our Mooneys have very forward CG’s, especially with two guys sitting in the front seats and little or no luggage. They have a tendency to wheelbarrow during the takeoff, that is, lift off one or both mains and run on the nose tire. A little up trim and a little back pressure during the roll will keep the aircraft on the mains until liftoff, where it should be. Certainly the big engines would want to take care in how much up trim, if any, they put in. -
Ok, what airplane WOULD you trade your Mooney for?
jlunseth replied to 201er's topic in General Mooney Talk
Probably even an Ultra can’t do the Kessel run in 12 parsecs. -
FLAP RETRACTION AFTER TAKEOFF
jlunseth replied to DCarlton's topic in Mooney Safety & Accident Discussion
231 here. Gear up as soon as I have a positive rate on the VSI, regardless of runway left. Flaps up when the gear is in the wells. Then pitch for midway between Vx and Vy to gain maximum altitude with minimum risk, as close to the airport as possible. Vx risks an inability to get the nose over in time if the engine quits. It is for performance takeoffs but not everyday takeoffs. Vy gains altitude too far from the airport to make it back if the engine quits. My initial climb in my aircraft is 85 KIAS. Getting the gear and flaps stowed helps to accelerate to that speed faster and allows a steeper climb at that speed. I use takeoff flaps for takeoff in my aircraft, that's half flaps. -
I visited the service ceiling once, just to say I did it. That’s 24,000. The climb rate from 22,5 up to 24 is really anemic. I generally do not fly above 21k though. The time of useful consciousness starts to fall quickly, so you have just single digit minutes, and if you consider that it may take some time to discover you have an O2 problem, and then to troubleshoot it, and then to get down to a better altitude, well, I just don’t go above 21k unless there is a really good reason. It is also directional and depends on trip length. Generally, going up to the flight levels is counterproductive on an east-west leg, and on the other hand, gives you a great speed boost on a west-east leg. It takes quite a bit of time to get up to, say, 20k. I use 500 fpm, so that would be 38 minutes from a 1,000 foot airport. Therefore, the trip has to be long enough to justify it and you have to plan the descent as far as 125 miles before your destination. I used to fly in the flight levels all the time just to say I did it. Now it is probably a half dozen times a year, whenever it is of real benefit. Much more common is just getting above the everyday stratocumulus, which is usually in the 14-18 range, I do that often. I was not aware of the FAA Circular but I am aware of most or all of the issues it addresses. Quite a bit of it, like explosive decompression or the coffin corner, are for pressurized jets and turboprops and not very relevant to us. There is training when you get to the High Altitude endorsement and for the ME ATP, for the jet type issues. I am not aware of any really good, comprehensive training aimed at turbocharged piston aircraft. Most of it you learn by doing, or going to individual courses here and there like the APS course in Ada, OK. Unfortunately, most instructors are either NA pilots or jet pilots in real life, so even at the Mooney PPPs I have not heard a lot about the issues that affect turbo piston aircraft. There are a bunch of unique things, high altitude miss, for example, or induction icing, or getting yourself trapped above an ice cloud deck, or hypoxia, or general engine management. Parvez Dara gave a talk at a Mooney PPP on hypoxia that was good. Everything else is taught in bits and pieces in other courses of much more general application.
-
I have the JPI 930 in my 231 and it has a fuel pressure readout. I almost never look at it. Fuel flow is more important. The factory gauge configuration did not have a fuel pressure gauge. From experience, fuel pressure drop, or its more like variation, does occur when you run a tank dry but there is not much warning. The engine is already talking to you.
-
There are a combination of things going on. Remember that the turbocharger is what produces MP above ambient, and it is not mechanically connected to anything in the engine, so it is not driven by the prop. The prop can be windmilling and the engine turning, but unless there is exhaust the turbo winds down. Another complicating factor is that the mags are pressurized and pressurization will fail without your pressurization source (the turbo) in operation. If pressurization fails the spark can arc across the mag cap to a cylinder the spark was not intended for. The resulting phenomenon, called “high altitude miss,” is very hard on the engine. Or the spark may simply be insufficient to cause combustion. See e.g. https://www.aviationpros.com/home/article/10388584/magnetos-under-pressure At 20k the standard ambient pressure is less than 14”. From experience I can tell you that the engine cools rapidly when you are at best glide and the engine is not firing. So now you are trying to start a cold to very cold, low compression engine, without enough spark. The POH for the 231 warns that you may need to descend below 12,000 for restart to happen. Even then, there are warnings throughout the POH against operating the engine at greater than 16” or 20”, depending on how low the oil temp has fallen. The POH warns that if the OT falls below 100, an attempt to run the engine at power may result in a sudden engine stoppage. What is going on, is that the oil is too cold to properly lubricate the turbo bearings, and the OT must be warmed before making power. Add in that you are crossing the Alps, or the Rockies, and you can’t descend to 12k and don’t have time anyway to warm the engine if it gets cold. It is not a wise move. These recommendations in the POH are conservative. And sure, if you jump on the fuel switch the instant the engine stumbles it should fire right away. I have done it. But I have done it over the mid-section of the US where I have all day to restart or find an airport if things don’t go perfectly. I would not do it, say, on a jump from Great Falls to Kalispell. Having done it, and having more than 6 hours of fuel on board, I no longer feel the need to give it a try. Much safer, is to test your fuel flow meter so you know its readings are accurate, fill the tanks correctly, know to a few tenths what is in each tank, and then not run one dry. Turbo ops are different from NA ops in many ways. For one thing, the NA is unlikely to fly at an altitude where unpressurized mags will not function properly. Turbo ops are very safe, in some ways safer than NA because you have an improved ability to get above weather. But you cannot just blythely apply NA ops to turbo ops or vice versa. PS I want to say that I admire curiosity and people who are willing to ask questions and seek information. I wish, when I first started flying my 231, that there had been more pilots savvy about turbo ops out there. I am not a CFI nor an engineer, just a pilot with some hours. I learned about “high altitude miss” the hard way, by having the “joy” of experiencing it firsthand, and I also learned the hard way not to “climb to target EGT,” which means leaning in a climb, an NA technique. Turbo ops are not complicated, when I fly, I have reduced my power settings to just some simple techniques. But to do that, one must understand the “why.” If anyone has more to teach about turbo ops I would love to hear it.
-
Hope we helped. I agree with your analysis of the takeoff from KVCT. Sounds like all was good but the fuel flow was a little low. The explanation on the MP, is that the whole purpose of the intercooler is to cool the induction air. At cruise the cooling can be as much as 100 dF or more. In other words, the Compressor Discharge Temp (the temp of the air exiting the turbo) might by, say, 250 dF and the Induction Air Temp (the temp of the air entering the induction system) might be 150 or even less. The 40" setting for the nonintercooled engine assumes that the CDT and the IAT are the same. Hot air is less dense than cool air. It has less molecules per unit of volume than cool air, in particular, fewer molecules of O2. So without an intercooler, at 40" you would be feeding the engine "x" molecules of O2 to be used in combustion, and with the intercooler, you only need around 37" to feed the engine "x" molecules of O2. If you feed the engine 40" of cooled air you are feeding the engine significantly more molecules of O2 than the Pilot Operating Handbook anticipates, and thus making significantly more HP than the engine was rated for.
-
Well, that’s the problem Skip. The very cold weather recommendation is a lot of priming. More than most people would consider to be reasonable.
-
We had a father and three sons from Minneapolis (where I live) who went on a ski trip in a J a few years ago. Rather than give you chapter and verse, which the family might read, here is the report. There are some lessons to be learned. What I will say, is that it is generally thought that the aircraft did not have sufficient climb capability fully loaded, to outclimb and survive mountain weather. http://www.kathrynsreport.com/2012/02/mooney-m20j-n201hf-luke-bucklins-former.html
-
Something has gone wrong if you have to try a restart under 40 degrees. The power cord to the pre-heater got disconnected, or the line kid never plugged in after I called and asked. But it does happen. I have started as cold as 10 dF. It’s pretty hard on the starter, but it can be done. I might just stick with the system I have for now.
-
Well, here’s the question about that. Using the existing system the primer fuel is dumped into the intake manifold, not the cylinders. This revised system, without the diverter, will put the fuel directly into the cylinders, and that is fine, it works. Typical warm weather priming is 6-8 seconds per the POH (I am going from memory here). However, cold weather priming, requires 12-15 seconds of prime at 20 dF and 20-24 seconds at 0. It is true, you need alot of fuel if you are to attempt a cold start at, say, 20 dF. The CB warns about hydrolock, which would happen if you dump a lot of fuel directly into the cylinders instead of into the intake manifold. So how long can you hold the button down without risking hydrolock? It appears from the CB that a cold weather start should not be attempted below 20 dF, and that is pretty good advice, the engine is very hard to start if you are ever in that situation and without pre-heat. But it does not directly warn against an attempt at colder than 20 and it does not say at what duration you are going to be risking hydrolock. It also appears there is a special inspection required if you do manage to hydrolock. So why would you want to do this? If you want to prime directly into the cylinders, before this change, you can just use the boost pump button instead of the primer button. Not an irrelevant issue up here in the cold north.
-
The desired value should be in your Pilot Operating Handbook. It is in mine. My POH requires 22.5 - 24 GPH at full power. 24 is better in a hot weather climb. I do not have your SB engine though, I have the LB.
-
If you have the intercooler you should not ever use 40” for a power setting. You should make your max throttle setting to be 37”. If you use 40” you will overboost the engine. The fuel flow should be set per SID 97-3G, modified in accordance with the instructions in the STC for the intercooler. It is those instructions that use a table that tells the mechanic what RPMs to use, given a particular outside air temperature. As I said earlier, it is generally around 37”. If your fuel flow is set at 24.2 GPH at 40” it was set without regard to the STC and it is set too low. You definitely would not want to increase manifold pressure above 37”. Unfortunately, with your current fuel flow setting, at 37” you will be making max power and the fuel flow will be too low. That would be your problem. Talk to Paul, he will get you straightened out.
-
I gather you have no intercooler. If you have an intercooler then takeoff should be a max 37” and if your A&P did his job right (followed the STC in setting the fuel) then it is set for 24 GPH at about 37”. If you have no intercooler it is set for 24 GPH at 40”. If you are running too hot in the climb, then try the counterintuitive thing and use max throttle, 39-40”. That will get your fuel flow up and the engine may run cooler. Climbing in the heat is always a problem. I use 500 fpm, that is two minutes per thousand and if you are going high that can seem slow, but it gives you better airspeed, which in turn gives you better cooling. I fly out west a fair amount in the summer and wind up doing long climbs when it is hot. It is practically impossible to keep all the CHT’s down below 380, especially if the aircraft is fully loaded. In my engine it is usually #2 that is hotter than the rest, probably a baffle issue. #2 is at the back, behind the others. If your #6 is hot, chances are your fuel flow to that cylinder is somewhat off from the rest, probably leaner. #6 sits behind the open intake hole and cooling is probably good, hence my guess that there is a fuel flow issue. My #2 will slip over 400 in hot long climbs and I have not found a great cure, although there are a couple of things to try. Paul Kortopates at Savvy has some good thoughts on this issue. One thing you can do is ask your A&P to set the max fuel flow at max throttle higher than normal, say 25 GPH rather than 24. You may have to manage fuel flow at takeoff and in the climb to keep the numbers normal (22.5-24 GPH), but at least you will be able to keep them normal. Paul suggested I do that a couple of years ago and it worked pretty well for summer, out-west type flying, but you do have to work with your A&P to get it done. The fuel flow, if set per the SID, should be 24 GPH at 40” and 2700 RPMs for the standard, nonintercooled engine. The STC for the intercooled engine has a table where the manifold pressure used to make the max fuel flow setting varies depending on OAT, but is generally around 37”. When you fly the aircraft you won’t get that max fuel flow unless you set the power where it was when the A&P set the fuel flow, i.e. 40” and 2700 for the nonintercooled engine, and 37 (or so) and 2700 for the intercooled. In your case, it sounds like the governor is set to max out at 2670 so I surmise that is what your A&P uses when he sets the fuel, but it is worth asking because he might be shading the fuel flow down to adjust for the slight lower RPMs. Not all A&Ps appreciate the problem of climbing temps in the 231, and unless yours does, you will probably see no better than 21 point something, which is not good enough. I think what they do, is set the max fuel flow, then set the idle fuel flow, and that affects that max flow, and they don’t go back and readjust the max flow upward, so in effect they have set it low. I can manage idle fuel flow with the red knob, it is the max fuel flow they really need to get right. My perception is that there is a “bump up” in fuel flow wired into the engine’s design, so the fuel flow change is not linear as you approach full power, rather, it increases faster towards the full power setting. So a change downward from full power of even an inch will reduce full flow by a couple of GPH pretty quickly, and that in turn will cause the engine to run hotter. Paul K. at Savvy can talk this through with you, he is pretty smart about the issue.
-
Is 36” the max throttle in your engine? I think it is. Max power is more like 37 in a 231 with intercooler, but the lore has been to use 252 tables so everyone uses 36”. So if the A&P sets the fuel flow per the STC for the intercooler, the engine is set to make max fuel flow (usually 24 GPH) at 37, not 36. If you fly a 231 and need full fuel flow you need max throttle, which is 37. My point is, if 36 is not max in your 252 and you need more fuel flow because the engine is not cool enough, then the solution may be to increase throttle, which is a little counterintuitive but it works. If 36 is the max you can set, well, then that’s it and the fuel flow needs to be set better.
-
MAPA Clinic in Kansas 10/15
jlunseth replied to bmcconnaha's topic in Mooney Safety & Accident Discussion
I have been to five, well, four and a half maybe. The first one was in Niagara and we had an event on the trip there that delayed arrival, so they let me come to one in Peoria to make up the missed work. Then I went to one in Boulder with a mountain flying course, and one in Olathe where we got a half day ground school at Garmin and a tour of the factory, and just was at the Santa Fe PPP this spring. The ground school is really excellent and these are all very well versed Mooney pilots so the ground school is model specific throughout. From the student’s perspective, they try to pair you with instructors who know or actually own you particular model, so the airwork is very knowledgeable and just excellent. I try to go every couple of years, it may cost more, but it is far more educational than doing a BFR with an instructor just out of college. Don’t get me wrong, those are very good instructors, but you wind up teaching them as much as they teach you.