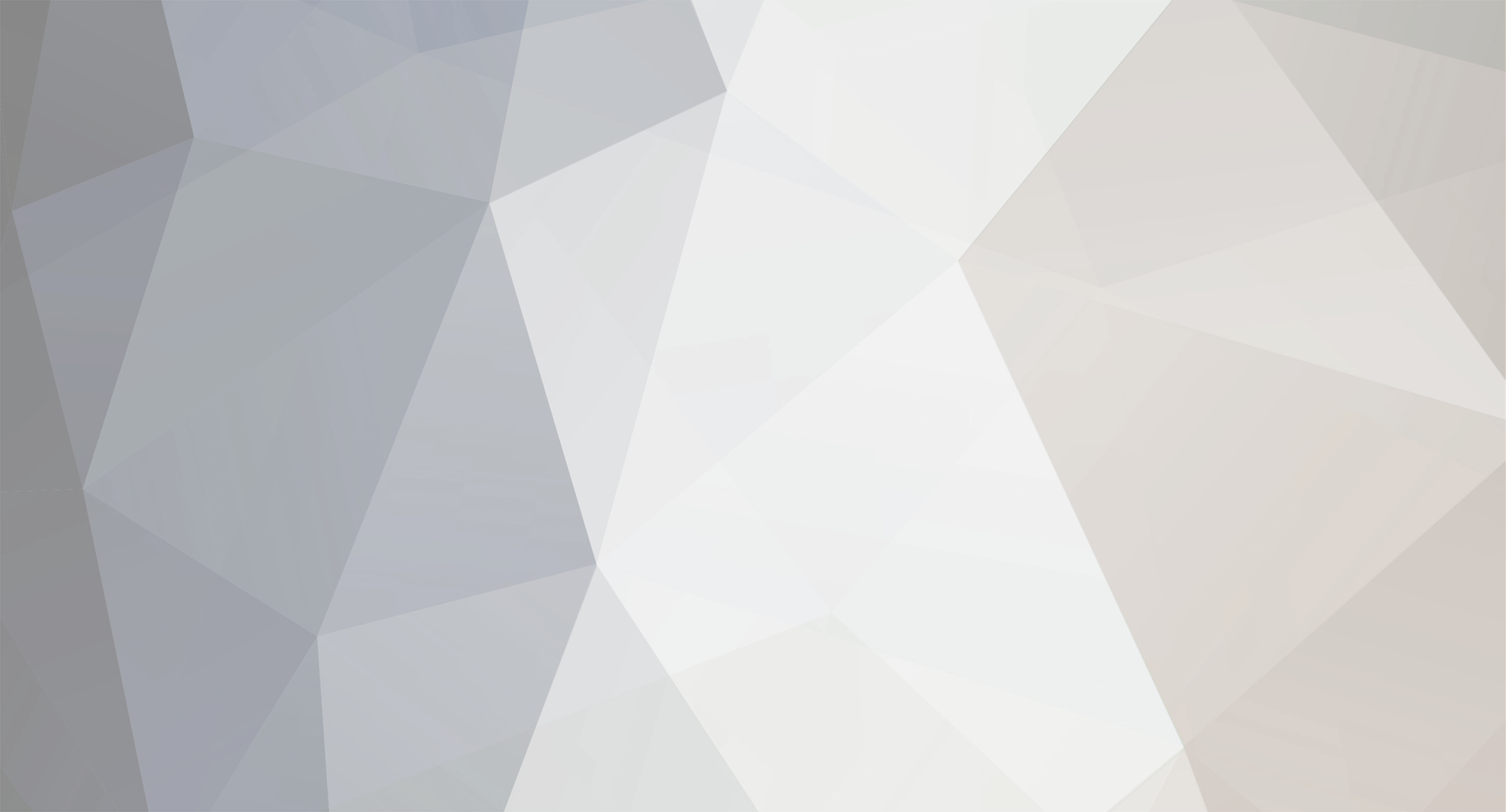
jlunseth
Supporter-
Posts
3,739 -
Joined
-
Last visited
-
Days Won
9
Content Type
Profiles
Forums
Blogs
Gallery
Downloads
Media Demo
Events
Everything posted by jlunseth
-
I ran my engine to 2400 hrs before replacing it. It had an IRAN at about 1100, but the reason was an incident where I lost oil pressure at 19k and had to make a rapid, no power descent to a safe no power landing. According to my A&P, that caused piston slap that scored the cylinder walls, hence the IRAN. It also had a turbo rebuild at about 700 hrs, right after I got it. That turbo made it all the way to TBO without further incident. I firmly believe that the TSIO360LB can run to TBO and beyond, if the engine is run correctly. Unfortunately, I think that many of the original engines were not, and part of the fault falls on misleading information in the POH. For example, the CHT redline is 460 dF. If you ever hit 460 dF it is probably time for a top overhaul at least. The goal is 380 dF. During high, hot climbs in the summer, such as out of a western airport, the engine might creep up a little over 400, but if the fuel flow is set up correctly to generate at least 24.0 GPH in a full rich full power climb, the CHTs will routinely be around 380, and in the spring, fall and winter they will be lower than that. The POH also has cruise power settings with the engine at or just slightly rich of peak. This is the worst possible place to run an engine and will generate the highest Internal Cylinder Pressures. From my experience, any cruise power setting in the range of 70-75% HP or higher, where the fuel flow is 12 something GPH, is a “red box” setting, hard on the engine. I was able to run the now-replaced engine for hundreds of hours at 11.1 GPH/2450 RPM/34” MP. The reason for the 34” is that lean of peak operation is a fuel/air ratio and you can make the mixture more lean either by reducing the fuel flow while the MP remains constant, or by adding MP while the fuel flow remains constant. So I used the 34” to make the mixture sufficiently lean to be reasonably healthy for the engine. I was concerned about the extra work this puts on the turbo so after it hit 1000 hours from the replacement I had it borescoped by my A&P several times and there were no ill effects. The other thing to watch is cooling of the cylinders, which is affected primarily by the baffling. My old baffling was not great, but with the new engine I have been a stickler on keeping the baffling in good shape, no gaps or creases. Creases where the baffling meets the top cowling were the primary issue with the old baffling. I am at about 150 hours on the new engine. Had to run it ROP for the first 100 hrs per TCM’s break-in instructions, and just beginning to work up LOP operations again. The biggest issue when you buy a used aircraft is that you have no idea how the prior owner ran the engine. If they believed everything that is in the POH the engine may be doomed to an early top or IRAN already.
-
"It's hard to say on this one, it could have been the low fuel set-up, combined with a pilot leaning during climb, which he might have been used to doing on a normally aspirated engine. Not good to do on a turbo engine. His low time with the airplane and possible mismanaging the engine may have been the ultimate cause. Or the engine just came apart at that point due to no one else's fault." It is possible to get the TIT to exceed redline and get the engine into detonation territory in a few short minutes after takeoff in the TSIO 360 if you lean the engine at full power. Worse if the fuel is not setup properly. In fact, you can do this at any time during climb if you leave the power in full and back the red knob out far enough. One cause is exactly what Lance says, the pilot is used to operating a normally aspirated engine and leans in the climb while the engine is making full power. The other is to fail to set the fuel knob to full rich right before takeoff, and the way that can happen is that you pull up to the hold short line, find out your takeoff is going to be delayed so you had the engine set full rich but now you back the knob off, and then you just forget to put it back in before taking off. If you don't catch it you will shortly see some magnificent temperatures, both TIT and CHT. Obviously can't say that is what happened here, maybe something did fail in the engine because of the prior work, but pilot error in managing the engine is possible.
-
Oil Drain Hose Diameter For The Ovation - Stock Quick Drain IO550G?
jlunseth replied to EricShr's topic in Ovation Owners
A small, long piece of plastic that was swimming around in the oil entered the quick drain and prevented it from completely sealing. We lost the oil over about two and a half hours, resulting in an emergency descent and landing north of Toronto. As a result, periodically, and usually during the annual, I have my A&P remove the quick drain completely in order to let the oil drain out the big hole, and have a "kit" for the quick drain installed that returns the seal mechanism to next-to-new. -
Quite sure. If you have other information, provide it.
-
231 crash on takeoff at 47N
jlunseth replied to Brandt's topic in Mooney Safety & Accident Discussion
I hate to say it, but I have developed a very jaded view of plane mechanics after several have tried to kill me. I tried a few at my home base, KFCM, when I first owned the airplane. In retrospect, diagnoses were generally bad because they did not know the Mooney aircraft, but that is not what got my attention. The first in-air emergency happened when I detected a new drop of oil on the nose gear prior to a flight over Lake Michigan. I had the plane rolled into a local mechanics shop and told them there was a new oil drip and I was going over Lake Michigan, please make sure it is ok. They diagnosed it as a leaking quick drain, which was right, but they told me quick drains just do that, it would not be a problem. Turned out a sliver of plastic had gotten into the seal and we lost all oil at 19k, in the dark, over Canada, about to be blown over Lake Huron by the strong tailwinds. An emergency descent to London, ONT with the engine idled followed, and it worked out. On another occasion I had a different mechanic at my home field replace a failed alternator coupler. They left a bushing out (didn’t have the Mooney shop manual). The coupler fell off into the running engine. Another emergency descent to landing that worked out. Luckily, in the aftermath, we found all parts and the engine was ok. There have been other incidents, less dramatic. But after 7 or 8 years of trying different mechanics I only use one, Oasis Aero at Willmar. There have been three generations of ownership. First Bruce Jaeger, who sold it to Brian Negen. When Brian’s business failed, Eric Rudningen and Paul Beck started Oasis. I have to compliment Bruce on having a fastidious nature, which led him to inculcate a culture of great care that still exists today. In the early days I wrongly saw this as overly costly, with repairs sometimes being made that I would have left alone, but not anymore. So I don’t even take my oil changes anywhere else. I don’t know what to call it, but there is a characteristic of good management that insures that issues that have the chance to create real problems are always addressed and cured. Other things might be lower in priority and not perfect, but when it comes to safety, it has to be perfect. As a student pilot I like to think that I got some of the best emergency procedures training that was available and it served me well, since these incidents happened when I just had a couple of hundred hours. But I would greatly prefer to practice those skills without actually having to put them into practice. In fifteen years of working with Oasis and its predecessors, their work has never put me in that position. So that is my standard, if they try to kill me I just don’t go back, ever. Wrong culture. -
Yes, I am talking about a tiny addition. A very few tenths sometimes corrects and sometimes it doesn't. The more dependable correction is to reduce a little.
-
That is a perfectly acceptable way to operate the aircraft. The only thing I will say, is that it is premised on GAMI's statement (entirely true) that you can't hurt the engine if you operate at 65% HP or less, regardless of where you set the fuel (ROP, LOP or at peak). So your really aren't taking full advantage of the potential of LOP ops, you are just reducing power to a place where it does not matter how far LOP you are operating, or if you are even LOP. When I went to the GAMI seminar and first began to experiment with LOP fuel settings, it seemed to me that wastes the potential of the turbo. LOP is an air/fuel ratio. There are two ways you can affect that ratio. One is by leaving the MP static and reducing the fuel flow, and that is the only real option open to pilots of NA aircraft, because the MP is capped at whatever ambient pressure is, which will be low at anything other than sea level. The GAMI guys were/are fond of LOPWOTSOP, which means to just firewall the throttle on an NA and then manage HP with the fuel flow. You can't do that in the 360 because you will overboost. The other way is to add air, which you can do with the turbo. When I experimented, I found that I could take the MP as high as 34" and that allowed me to use a somewhat higher fuel flow and still stay safely lean of peak. 11.1 GPH worked out great. If you run it through the HP formula for LOP operations on the 360LB, that works out to 71.1% HP and the TIT would be right at or under 1600. I use 1600 as my limit, and if the TIT starts to go much over that I either adjust the fuel flow up just a little (i.e. 11.3-.7) or I reduce the MP, and if neither works it is time to fly ROP. As I said above, that usually happens around 12-16k depending on day temps. I worried at first that I was overworking the turbo, and at 1,000 hours on it (a rebuild in about 2010) I started to have my A&P borescope it. There were no problems and it was still going strong at some 12 or 1,300 hours from rebuild when I replaced the engine. The 71.1% results in really nice speeds and its hard to argue with 11.1 GPH.
-
That is excellent. The engine had such a bad reputation for running hot that I never expected to get the kind of longevity I ultimately saw, as did you. The problem, it turns out, was us - pilots - running the thing the wrong way.
-
I have about 2,000 hours in my 231, am working on my second engine, and have flown quite a few trips into and over the western mountains. I also fly for Angel Flight often so am used to managing loads that might seem excessive for the plane, including, once, a wheelchair. I will go through your questions here and give you my perspective for what it is worth. The LB is more desirable. The GB was known for high engine temps. That can be a problem even for the LB under the wrong conditions. As a practical matter, if you want engine life, the GB would limit you to the mid teens. I would want the Merlyn and the intercooler, both of which I have. The absence of the Merlyn limits you to a Critical Altitude of around 15k, where the Merlyn lets you fly well into the flight levels. Without the intercooler, the Compressor Discharge Temp redline is 280 and as a practical matter you will see that in the summer at somewhere between 15 and 17k in the GB, but if you have the LB and intercooler the Induction Air Temp will always be under the 280 limit. The GB engine will also run generally hotter. I don’t know if the 231 is subject to that SB for roll cage corrosion, but I can tell you what to look out for. There was an insulation used back in the day that was textured like wool. It would be cut to fit between the cage bars and the edges would rest on the cage bars. That insulation would absorb moisture and the constant contact with the cage bars would cause corrosion. During a pre-buy it would be worth it to have the side panels come off and inspect for that type of insulation and for corrosion. With the turbo I have not encountered any high DA airport that the aircraft cannot handle easily, including Leadville in the summer. Most western airports have longer runways than what we generally have here in the Midwest. In practical fact, runout is the only thing that changes, and the longer runways take care of that. You do need to stay aware of climb rates though. Many of the western airports have departures where there is a VOR north or south of the airport. You fly to the VOR and if need be you can circle the VOR to climb to cross the rocks. It might seem in theory that you could climb on a direct course over the rocks, but if you try that on the wrong day with strong western winds aloft you will be at the rocks faster than you anticipated. Having tried it the wrong way a couple of times early on, I now use the departures every time. You don’t ever want to fly at a cruise speed with a 12 in it for fuel flow. That may be what the POH says, but it is the dead wrong place to operate the engine. You have two cruise choices, Lean of Peak or Rich of Peak. Either way you want to be far enough away from peak EGT to be easy on the engine. I fly regularly at 11.1 GPH/2450 RPMs/34” MP, that’s LOP and will give you great speeds up to somewhere around 12-16k in the summer. If you try to go higher you will find that the TIT becomes unmanageable. To fly LOP however, the engine must be set up to do it and you may need GAMInjectors. The other way is ROP, which would be around 29.7 MP/2450RPMs/13.3-14.5 GPH. ROP or LOP you want to keep the CHTs at or under 380 as much as possible. When you are flying ROP, if the temps start creeping up, you just add more fuel to lower them. You need to be at least 125 degrees rich of peak EGT. You can fly ROP anytime you want to, whether your engine will fly LOP or not, and ROP is particularly useful when you want to go over the 12-16k area where TIT becomes a challenge if you are LOP. Either way, you will see 160 at around 10-12k and 170 in the mid to higher teens. If you fly locally you can leave out fuel to create more payload. I do this regularly for Angel Flights. However, I can’t remember ever having flown with less than 50 gallons to start a flight (max in the normal tanks is 75.6). I have CiES senders and a JPI930, so my fuel readout is about as accurate as you can get. Even so, I don’t consider it good enough to fly a tank under 10 gallons and I never start with less than 50. If you are going to fly a trip where fuel is an issue you really need to supervise the fueling or do it yourself. The plane has anti-siphon flappers in the neck and it is pretty easy for a line kid to be fooled into thinking that the tank is full when there is fuel on top of the flapper but a big hole underneath. As others have said, it is a reach to expect 1,000 lbs., although there are some 231’s with that UL, Mine is 980. I have been able to manage some pretty big loads by leaving out fuel, including carrying a 295 pound passenger, his wife and 50 lbs of baggage. For Angel Flights, which are generally not over 2 hours, I can fly with 50 gallons, myself (200 these days), and about 450 lbs. The leg room is not great in back, but if you put a smaller passenger in the copilot seat and roll the seat forward, the legroom in the seat behind is not bad. I have managed a collapsible wheelchair plus two passengers and baggage. I have also flown several hundred pounds of medical cargo. Unfortunately, people are getting bigger these days and the 450 lb loads are pretty common. I wouldn’t say there are “gotchas” for the TSIO360LB, it is a pretty nice engine. There are weaknesses. You are limited to one 12V battery and one alternator, and the alternator is direct drive. The clutch in the drive is a weakness and if that goes, the house battery does not last long. If you are going to fly anywhere near IMC conditions over the mountains you need much redundancy for your AI. I have dual redundant GI275’s plus one standard AI operated by the vacuum pump so if I lose all electrical I still have an AI. If you are over the top and over mountains you won’t necessarily find a place to land for awhile. I have had the pleasure of losing the alternator and flying with the Master off (completely dark panel). You want to convert all the lights to LED if they are not already, the old incandescent lights are way too much load on the 231s electrical system. The engine can run hotter than later models, but I have found that with proper fuel management (staying out of the 12s) it is very durable. I flew my first engine to nearly 2400 hours, which is 600 over TBO.
-
I own a 231, not a Bravo, so take this with that grain of salt. I would ignore the mechanic. First, the average idle rise is 75 RPMs. But so what if you see more? The turbo Mooneys are generally set up to run very rich, and the purpose of that is to keep the engine cool when you use full power settings such as during climb or hot weather operations. That is much more important to engine health than whether the pilot needs to use the red knob more at low idle. Lots of mechanics who are experienced with NA engines don’t understand that this is different with a turbo engine. I am not a mechanic, but am told that there are actually three screws for setting fuel flow, and there is some back and forth between them. In other words, if a mechanic sets the full fuel mixture and then sets the idle mixture, it is necessary to go back and check the full fuel mixture to get a balance between the two. Many don’t bother, with the result that the full power fuel flow is low. So yes, more fiddling with the mixture setting might reduce the idle rise that you see. But you can do the same thing with the red knob, just lean it out more at low power. Frankly, you are going to find with some experience with your aircraft that things like how far out you need to lean at idle are going to vary a little each time the engine comes out of annual, where the fuel flows were reset. What is of paramount importance to the health of your engine is that you can get full specified fuel flow at 100% power.
-
Swapping out VM1000 for JPI M20L conversion
jlunseth replied to VA FLYER's topic in Engine Monitor Discussion
I did a little online checking and saw that JPI bought out Vision Microsystems and they (JPI) have some information on their website about their VM1000. They apparently provide some customer support for it. If you find the STC issue insurmountable, you could try them to see if they can service the VM1000. See https://www.jpinstruments.com/technical-support/video-tutorials/vision-micro-vm-1000c/ -
I am getting the mismatch because the new, synced databases are loading into the 275s, but not activating as the primary database. In other words, they are just sitting in the unit as a standby and the old, expired database is still the active database. Can’t get the unit to activate, at least not without shutting down and restarting. As we discuss this, that might be my solution. The 275s are wired to the Master. They do update the next time I start the engine. So maybe what I need to do is cycle the Master after the GTN has updated itself and sent the new db’s over to the 275s. That will reboot the 275s and may solve the problem. I am going to try that the next time I fly. PS I’ll bet that is the problem. My 275s are certified primary for the AI and HSI (and a few other things). To do that they are probably inhibited from rebooting after they are switched on, to prevent a reboot in the air, say, when you are using them to navigate in the clag.
-
I have a GTN 750 Xi, two GI275’s (redundant configuration) and a Garmin data subscription. When I first got all this I could do a Sync update in the Garmin Aviation Database Manager and the 275s would seamlessly update from the GTN. Then there was a software update, I think to the GTN, and it is no longer seamless. I remember reading a topic where this was discussed but at the time there was no good solution. Hoping there is by now. So I still do the Sync update. The GTN populates and shows database mismatches with the two GI275s. I have tried everything I can think of to force the 275s to update, but short of putting the updates on a USB or similar it is not happening. They show up in the 275s as Standby databases, I have tried the Activate Standby button and nothing happens. All is not lost. For better or worse, on the next start up the 275s are magically using the current, apparently synced, database. Taking the hint, I have tried cycling the Radio Master off and on but that does not prompt the 275s to update. I frankly cannot remember if I have tried cycling the Master, maybe that will do it. That might do it, I believe the 275s are wired to the Master and not the Radio Master (the GTN is wired to the Radio Master). But it does not seem logical that something that once worked does no longer, and that I can’t even manually cause it to work using the menu buttons in the 275s. It is a pain going out to the airport, usually on a schedule to pick up someone, putting the cards in, waiting for the GTN to update, and then having to shut down and restart just to get the 275s updated. Frankly, I don’t know what the point of updating their databases even is, they are not the guidance source, the GTN is. Any useful thoughts or solutions?
-
There are many ways in which the operation of a turbocharged aircraft are completely different from a normally aspirated aircraft. Pilots of one type make assumptions, come to conclusions or give advice about the other from their own perspective and the answer or conclusion can be 180 degrees wrong. So without knowing what the aircraft was and what engine it had in it, there is no way to come to any conclusion about what happened. NA pilots, for example, are taught to put in full mixture during the landing phase in case they have to go around. The theory is that if a go around becomes necessary, putting in full mixture is one less thing to do. However, in at least some turbocharged aircraft, the engine is set up to run very rich to protect the engine at full power, in takeoff and during the climb. It is set up so rich that during the final descent to landing the engine will "burble" unless it is leaned out quite a bit. The burbling is not a true miss, a true miss being a cylinder failing to fire. Rather, there is so much fuel and the engine is producing so little HP in that regime of flight that the cylinder fires but the fire is drowned out quickly by the excess fuel. To avoid this we turbocharged pilots lean the engine out quite a bit during the approach to landing. So much so that on occasion we lean it a little too far and forget to put some mixture in right at touch down. When the plane is no longer descending and the prop is no longer being helped by the airspeed the engine can quit on the ground because of too little fuel. The fix, if you hear it happening, is to quick push the fuel knob in. When I first started flying my TSIO360 years ago, being a freshly trained NA pilot (Slohawks, Warriors and Archers) I would put the mixture full in for landing. People on the ground would tell me that there was something wrong with my engine, it was missing during the landing. So I figured out to lean the engine out during the descent and me, the engine, and the people waiting on the ground are all much happier. Oh, and it may come as a surprise to NA pilots, but there is no great trick to pushing in the fuel knob for a go around. You have no choice, if the engine is leaned out it will struggle if you just put in MP. I have done a few emergency go arounds, deer or geese on the runway for example, it has just never been an issue. So back to the OPs question. There is no way to answer without knowing the engine in the aircraft. If it is an NA engine, then maybe some engine adjustment is in order. If it is a turbo'd engine, the pilot may need to change his methods and put in some fuel (not MP) at the runway.
-
"Un-Happy Endings" For Flight to Oshkosh
jlunseth replied to 1980Mooney's topic in Mooney Safety & Accident Discussion
A fellow Angel Flight pilot flew me to Appleton last year, and from there we bused to Oshkosh. I was there to receive the Distinguished Volunteer Pilot award from the NAA. It was supposed to happen in front of the crowd for the afternoon airshow. But as we got ready to make the walk out to the stage we all saw smoke to the south. It was the gyro/helicopter crash last year, one of five accidents as I understand it. The awards were moved to another area. There are issues every year. Pilots who maybe don't belong in that kind of traffic. That was my one and only voyage to Oshkosh, made me think I would never want to fly in. -
I don’t remember if you have an intercooler or not. I think not? If you have an intercooler, then CDT is basically irrelevant. The CDT redline is in the POH for the original factory engine to protect against detonation caused by too hot induction air. If you have the intercooler, then the relevant temp for that purpose is Induction Air Temp (the temp after the intercooler). CDT is the temp before the intercooler. The difference between the two varies depending on the flight regime, but even in a climb with lower airspeeds the temp difference will be around 80 dF and you won’t have to worry about detonation. However if you do not have an intercooler, then CDT is definitely an important redline. I have the intercooler, but I see both CDT and IAT on my JPI930 and can confirm that somewhere around 17-19,000 you will run into the CDT redline in the non-intercooled engine. Even if you do not have an instrument like the 930 that shows both temps, the original intercooler came with a differential temp gauge, needed to be able to use the charts that tell you what MP to use. With a little mental math you would be able to read the CDT and convert it to IAT. Putting in more fuel flow is unfortunately not going to reduce CDT. CDT is a function of how hard the turbo is working to produce a given MP, plus the lack of cooling at high altitudes. It has to run harder at higher altitudes because there is less ambient air to compress. Running into the CDT redline is unfortunately an issue with the non-intercooled engine. The solution would be to install an intercooler, which cools the induction air by quite a bit. I have to say though, it is excellent that you are finding that higher fuel flow and full power makes the engine run cooler in a climb. That is as it should be. But you are always going to see that CDT redline problem around 17-19k so long as you do not have an intercooler. The intercooler gets you to about 22,500 (depends on day temps) before you reach Critical Altitude where the MP begins to fall off even with the MP knob full in.
-
You will hear that Mooney’s are too fast to learn IFR in. Just remember that you can slow a Mooney down and fly around all day like a Skyhawk if you want to.
-
Well some of us Mooney pilots made the west coast event even though we live in Minnesota.
-
Where is this symbol defined?
jlunseth replied to N201MKTurbo's topic in Miscellaneous Aviation Talk
Shoot, +/- 10 kts is a daily event in the western part of the Midwest. -
The Safety Foundation is still putting on four or five programs a year in different locations around the country. I went to Santa Maria. There are two left this year, in Vermont and in Texas. Great instructors.I have been five times, still learn something new each time. I agree I am not sure the manual would help much without the classes, more like a slide deck.
-
I haven’t had the 256 itself fail, but did have a vacuum pump go out but in VMC. I knew it right away, of course, because the annunciator and the vacuum gauge let you know. But the 256 was happily spinning so I left it in control for awhile. It wasn’t long before we had gained about 600 feet. The 256 looked perfectly normal but it wasn’t. We found an airport (KBIS) spent the night there on a cot and got it fixed. The incident, although completely safe, left an impression. I now have two 275’s and a separate vacuum operated AI.
-
Precise Flight Mic Mask - Weak Microphone?
jlunseth replied to PhateX1337's topic in Modern Mooney Discussion
The mic in the mask I got was mounted so that it was vertical. The sound was terrible. The mike needs to touch your lips, yes, but you have to bend the wires so that it is oriented horizontally or touching the lips does not do much good. -
@1980Mooney. There are several Federal laws that apply to noise abatement. Most importantly, the Airport Noise and Capacity Act (ANCA) makes clear that jurisdiction over noise abatement is exclusively Federal. The doctrine is called “Federal pre-emption.” There is case law holding that the authority over noise abatement is exclusively Federal, in other words, local (meaning state, county, city, etc.) authorities may not attempt to legislate or control noise abatement. That said, there are far too many “voluntary” programs, etc. It would be a good issue to take up to the SCt. at this point. We have a “voluntary” program at my home base, KFCM. I fly often for Angel Flight. We don’t get to choose when the patients need us.
-
I write because in some recent threads, the “Chevron deference” doctrine has been the subject of discussion. Under the doctrine, which stemmed from a case 40 years ago, the Courts gave deference to an agency’s own rules and interpretations of its rules. In other words, a Federal agency could not only promulgate a rule, it could then decide what the rule meant and how it was to be applied, and the Court’s were not to interfere with that interpretation. This resulted in what some viewed as abuses of the administrative power. On Thursday and Friday of this week the Supreme Court decided two cases that are likely to dramatically change how Federal agencies (including the FAA) operate. In Loper Bright Enterprises v. Raimondo the Court expressly overruled the original Chevron case. “Chevron deference” is gone. The day before, in SEC v. Jarkesy, the Court determined that there is a right to jury trial in instances where an agency seeks to impose a civil financial penalty for violations of its rules. Previously, an agency could decide whether to proceed against a defendant in Court, where the rules of discovery and rules of evidence apply, or before an administrative judge where they do not. The effect of Loper is that an agency is no longer the sole decider of what its governing statute or its rules mean. This has two effects. First, Federal agencies unfortunately have used their authority under Chevron to pass rules expanding their own authority beyond the scope of the statute under which that authority was granted by Congress. As an example (I am deliberately staying away from aviation-type examples), for many years the EPA asserted the right to regulate farmers’ fields. Their jurisdiction extends to “navigable” waterways, and they interpreted “navigable” to include areas where water ponds in the spring. A long battle was fought over this with Chevron very much at play, in other words, the agency asserted it was the sole decider of the extent of its power to regulate. Second, agencies will be limited in their ability to apply their own rules and regulations simply by reinterpreting a rule. Under Jarkesy, enforcement proceedings in which an agency seeks a monetary penalty will be required to proceed in Court where the defendant will have the ability to defend himself, and have the matter decided by a jury of his peers. In Jarkesy, the SCt distinguished between enforcement proceedings the purpose of which is solely to restore the status quo, from those where a monetary penalty is sought. So it remains to be seen whether Jarkesy will apply, for example, to proceedings for the suspension or revocation of a license as opposed to a monetary penalty of some sort. These cases - and we may see more aimed at limiting the power of the administrative state - will unquestionably have an affect on how any Federal agency, including the FAA, operates. Personally, I have had nothing but good experiences with the FAA, and as Federal agencies go, it has always appeared to me to want to serve and cooperate rather than mandate and restrict. But things will change. In practice, and from long experience in the legal field, I can tell you that it will take some time for these two decisions to have an effect. When major precedents come down there is always some resistance in the lower courts, which find ways around the new precedent. For example, in Loper the SCt said that the Federal courts may, in deciding what a statute means, consider the agencies interpretation in light of the expertise of the agency in the particular field. So in lower courts sympathetic to an agency, the court will simply use that rule to adopt the agency’s interpretation, right or wrong, and it will up to the appellate courts to straighten it out. There will also be quite a few cases in the lower courts trying to sort out what Loper and Jarkesy mean. So don’t anyone think they can now go fly under bridges.
- 34 replies
-
- 11
-
-
-
I see you base in Sedona AZ. The “high, hot” climbs out of western airports in the summer are the most challenging as far as CHTs are concerned. Rather than reducing your power, you might try a full power/full rich climb. Strong fuel flow is the best way to keep cylinders cool in a high hot climb (or any other climb for that matter). The POH spec calls for 22.5-24.0 GPH at full power. It is actually best, if you can persuade your A&P to do it, to set the fuel flow for about 25 GPH. You can always reduce fuel flow with the red knob but the biggest problem I have run into is that A&Ps persistently set the fuel flow too low, so a full power, full rich climb will be at, say, 21.0 GPH. Too little fuel, cylinders will run hot. Also, in both my 231 engines (I replaced one in the past year) I have noticed that there is a fuel flow bump as the engine approaches full power. In other words, in the area of cruise settings you will see a more or less linear increase in fuel flow as you change settings, but as you approach full power the fuel flow will bump up more rapidly in the last inch or so of manifold pressure. You really want that full fuel flow, so even though it may seem counterintuitive, full power is the way to get the best fuel flow and actually will keep the engine cooler than a reduced power climb in my experience. Lastly, what is “full power” in the 231? If you don’t have an intercooled engine the answer is simple, 40” MP/2700 RPM/24.0GPH . In the intercooled engine it is a little bit of a moving target. If you look at the STC instructions for setting fuel flow with an intercooler, there is a table that the mechanic is supposed to use, which says what MP will provide full power at what OAT. Most of us think of full power as 36” with the intercooler. It is actually a little closer to 37” and varies with OAT. I generally use 36” for full power climbs, but on takeoff it does not offend me if the MP gets up to 37. The important thing is to use an MP that gets you to full fuel flow, which is the way to keep the engine cool. Two more things. One, if you want full power, and I think you do, you have to use 2700. A lower setting will reduce the fuel flow. Two, I climb at 500 fpm. Yields good airspeed and cooling. I can climb at over a thousand in the winter here in MN, but not in summer temps. Final thought: The baffling in my old engine was not ideal. I would see temps like your 405 in high hot climbs quite often. When I had the new engine installed I was a little more demanding about the new baffling, insisting that all the leaks, seams, and wrinkles needed to get sealed. The temps in the new engine are quite a bit cooler, I mean by about 20 degrees, and also more consistent between the cylinders, so in the old engine the difference between hottest and coolest was around 85 degrees, now it is around 45. In the new engine with the new baffling if I see a temp climbing over 400 on a cylinder it is a fuel flow issue that I can adjust for rather than a systemic problem that I could not adjust for as was the case with the old baffling.