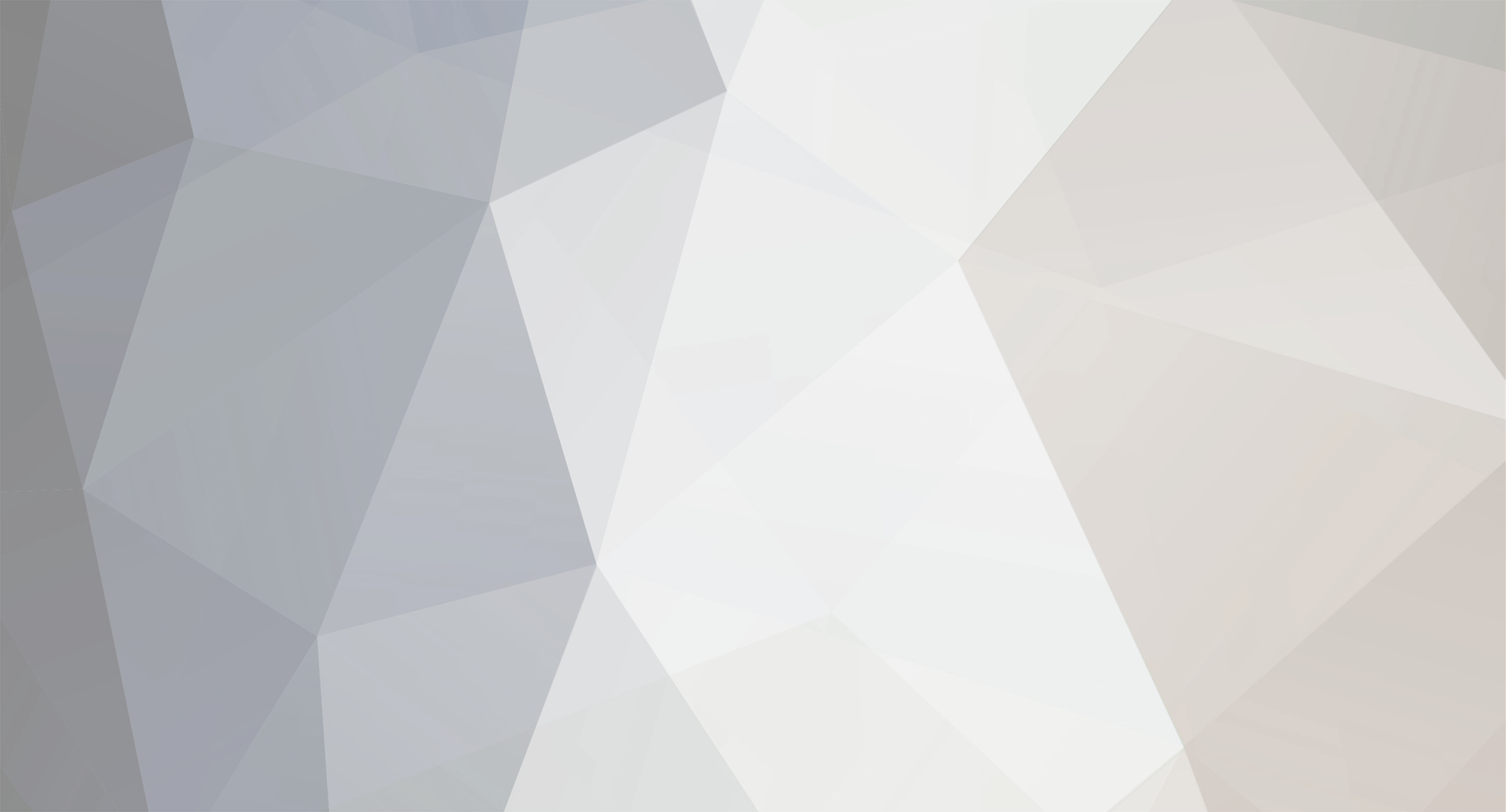
A64Pilot
Basic Member-
Posts
7,653 -
Joined
-
Last visited
-
Days Won
21
Content Type
Profiles
Forums
Blogs
Gallery
Downloads
Media Demo
Events
Everything posted by A64Pilot
-
SureFly Mag install for M20D, O-360 A1D
A64Pilot replied to Verv's topic in Vintage Mooneys (pre-J models)
Normally, yes. I have never figured out why only one mag has an impulse coupling, my 1946 C-85, both mags have impulse couplings, among other things it means of course they are identical, which would seem to be a plus, but I guess impulse couplings aren’t free. ‘Knowing nothing about this installation but I assume it’s an STC? If so then your held to whatever the STC says, it may indicate which mag to replace? -
Your in a chamber, I think you’ll survive, but one wonders if it really does and of so by how much? This is the only study I could find that actually tested for that, and they had multiple doses of significant amounts of aspirin. I know one study, is well just one study, but I’m no Physician either. https://www.aafp.org/pubs/afp/issues/1998/0801/p540.html Maybe it doesn’t reduce oxygenation of the blood? You had me thinking, because if you were right then we shouldn’t take aspirin when flying or at least maybe think about supplemental O2?
-
That works for a NA engine, it’s my understanding that a turbo at altitude it’s a little more complex, but if managed correctly it will come back
-
leaning/enriching on descent - M20J
A64Pilot replied to dominikos's topic in Modern Mooney Discussion
Shock cooling is real, it’s not been debunked, but it’s more of a problem for the High HP big turbo motors usually found on twins running at high HP and therefore high temps trying to get down fast like a turbine can, or glider tugs / parachute aircraft that can go from full throttle to idle in the mission. For almost all of our little NA motors at altitudes we can’t make the HP and temp for it to be a real issue, if we are only mid 300’s it would be really difficult to cause damage even by reducing ti idle and pointing the nose down, we just aren’t hot enough to begin with. Only real issue with being LOP and descending and not touching the mixture is the engine may not respond when you add power after descending several thousand feet, of course enriching the mixture will bring it back, you didn’t hurt anything just it can cause some stress if you add power and it starts running rough and doesn’t give you power. Saying that shock cooling doesn’t exist is as logical as saying you don’t need to cool your turbo because on approach your EGT’s are off scale low. Lycomings take on it, they call it sudden cooling, not shock cooling. You can choose to believe the Lycoming are a bunch of idiots that don’t know anything about the engines they manufacture or not, that’s up to you. They even give you a list of specific components you can damage https://www.lycoming.com/content/how-avoid-sudden-cooling-your-engine My personal belief has been forever that for any engine from your leaf blower to large Turbo Diesels that engines live longer if gradually warmed up and gradually cooled down. Even if it’s BS, it doesn’t cause any harm to follow manufacturers recommendations. -
My opinion is the oil cooler was relocated for two reasons. First nearly everybody else locates it like it is in the J, it works well there, and secondly not having that structure out in front of the airplane is less drag. I can’t get the oil temp in my J to even run in the middle of the green, it’s always low.
-
Heating air thereby increasing pressure which can be turned into velocity can be very significant. In WWII some water cooled airplanes used this waste heat to generate thrust and significantly increase their speed, probably the P-51 did this to greatest effect, but the Spitfire and Hurricane did it first I think. it’s called the Meredith effect. https://en.wikipedia.org/wiki/Meredith_effect#:~:text=The Meredith effect is a,hot air in the duct.
-
You can actually turn velocity into pressure and vice versa. If there is reverse flow out of the inlet, then of course there is reverse flow of the entire system, meaning air flow in through the cowl flaps. You can’t have air flowing out of both ends You could get outflow through part of the inlet if that part was shielded from the ram pressure by an object being well in front of the opening but nothing blocks part of the Guppy mouth does it? There is only a small gap between the spinner. Ref inlet vs outlet size, you want the inlet bigger if you want to build velocity in the system, you want it smaller if you want to build pressure. This is how velocity and pressure can be manipulated by inlet vs outlet size, just like a carburetor, the middle section is smaller increasing velocity and decreases pressure. Next time you walk by a turbine look at its inlet, it gets bigger towards the engine, being a reverse funnel if you will makes it build pressure by decreasing velocity. More modern cowls decrease drag by being more efficient in flow, first they are round, because a circle has the greatest interior area with the smallest exterior, so round pipes flow more water than any other shape, so they have round inlets and to heck with the esthetics. Bigger odd shaped holes are draggier if that’s a word, A J’s inlets are better than the Guppy but the knowing didn't go for least drag I guess for appearance. In the 10970’s I guess people weren’t ready for round holes? As was brought up, what’s inside is very important too, any restriction to airflow is drag of course, drag is proportional to the airflow, open the cowl flaps increases drag, I think we all understand that
-
Is cruising at lower power bad for the engine?
A64Pilot replied to RescueMunchkin's topic in General Mooney Talk
I just had a thought ref “is flying at low power bad on the engine” Now you guys check my numbers because they may be wrong. A Carbon Cub has a 180 HP Lycoming I believe? I also believe it’s limited to 5 min at 180 HP, after the 5 min your restricted to 80 HP continuous. Then if that’s correct and my math is right then the 180 HP Lycoming in the Carbon Cub is restricted to a maximum cruise power of 45%. Surely it stands to reason that if that were bad for the motor then Lycoming wouldn’t allow it, or there would be reports of engine problems in Carbon Cubs by now? I’m sure many don’t follow the limitation but think quite a few likely do. -
Ref the airflow reversing and flowing out of the engine inlet, Uh, that’s not going to happen I don’t think, if there was no exit there would be no airflow, open just a little exit the flow is slow, but it’s still flowing, but it’s not going blow air out of the inlet. Only way I can see to make the air flow out of the front is if the pressure inside of the cowl were higher than the ram air from the front Now I can see how air could flow in reverse through an oil cooler as it’s possible that the pressure in the cowl could be higher than in front of the cooler due to its mounting angle, maybe, but a direct ram like the inlet? I don’t think that’s likely. It would be real easy to tuft the inlet and prove or disprove it.
-
My fixed wing test pilot mentor told me that up to 25% of the total drag on the average piston GA airplane is from cooling drag, Ralph I’m sure was speaking about vintage aircraft, but 25% is a big number. Internet will return lower numbers but I know Ralph knows what he’s talking about. Significant drag reductions from cooling drag have been made in modern designs, but I believe also at the expense of cooling margins. Even with turbines during Certification we have to do cooling climbs which are worst case of course and are corrected for temps, it’s best for passing the test to test in as hot a weather that you can because the corrections are conservative. The max allowable temps come from the component manufacturers of course, and the max cyl head temps are well in excess I believe of what most of us are comfortable with, so I think it’s common for newer designs to have to climb at higher air speeds than older designs in order to keep temps where some of us are comfortable with. If I’m traveling and have no restrictions on altitude I’ll often climb at the fastest airspeed that will give me 500 FPM, that accomplishes two things, first my speed is much faster of course and the point when traveling is to get there, but it also keeps my cyl head temp very close to cruise numbers. Being as I’m down in the flat lands I don’t go very high usually, it’s rare for me to get above 10K. I’ll only go up there for cloud clearances or to get a smooth ride. Lately I’ve come to rethink that because you burn significant fuel climbing, so it’s likely that for fuel consumption it’s best to minimize time spent climbing, everything is a compromise If I had to climb over rocks like guys out West do, well then that’s different of course, I’ve had to circle as I’m sure everyone has to get enough altitude to clear terrain at a comfortable altitude, so a slow climb isn’t productive.
-
Just sorry he was in a Mooney
A64Pilot replied to Brandt's topic in Mooney Safety & Accident Discussion
OK, I’ll bite. How does my post saying that altitude can increase the effects of alcohol or that as we age maybe we should get on O2 earlier hurt Mooney pilots, or any pilots for that matter? How could that possibly affect our insurance rates? I would hope the opposite. I’m older by the way and concede the fact that I’m not what I used to be. I used to have better than 20/20 vision, but at 40 Presbyopia kicked in and now I wear glasses to fly. I see that as being proactive and taking action to negate an age induced limitation. The truth is as we age we lose some capabilities, vision for example is common, so I see it as being proactive to recognize that fact and take actions that minimize the adverse effects of aging. Why do you think that you can’t fly part 121 after 65? How is going on O2 at a lower altitude and or limiting my altitude if O2 isn’t available any different than wearing glasses? When the day comes that an insurance company won’t insure me anymore I’m not going to stop flying. It probably will have an effect on what I fly and where I fly, but I’m not going to stop flying, why should I? They are private companies, free to do as they want, now admittedly the government had stepped in and tied their hands so that statement isn’t completely true anymore, but if they choose to stop insuring at some age, that’s their right to do so, so far. -
How many amps is the thing rated at? If 2 amps then 2x14= 28watts, that’s enough to get that connector hot, I bet one of the female ends is bent and loose, but I think what your seeing is a symptom not the problem, the problem is that your pulling max amps over an extended period of time, which unless your battery is discharged every time you plug it in you shouldn’t be, or as others have said your using a lot of battery when the engine isn’t running. Now that I think about it a loose connector could cause you to pull amps that aren’t getting to the battery, I think the connector got wiggled excessively or maybe even came loose from the beginning. You can replace them with a model airplane Deans connector or something that’s higher quality. The purpose of the fuse is to protect from the pig tail shorting and the battery causing a fire, the fuse rating is higher than the chargers capacity so the charger can’t blow the fuse. The fuse is why I don’t get concerned about the vinyl wire not meeting FAR specs.
-
Ref hypoxia and symptoms. Being military we all rode the chamber, every one of us just have gone through WOC D etc and due to our age, we were all under 30 as it was the limit, were in about the best shape of our lives, nobody overweight, no health issues etc. Anyway the majority of the people had no idea they were impaired, I was first to put the mask back on so I got to watch, but everyone thought they were doing fine, but they were seriously impaired, couldn’t recite the alphabet etc. I mean stupid, you have to see it to believe it. So what I’m saying is you cannot rely on you feeling symptoms and take action, you think your fine, but aren’t. I guess I was an outlier, it’s not that I knew I was impaired so much as I didn’t like the feeling, hard to explain but I didn’t like it and put the mask back on, I got anxious. If you get a chamber ride take aspirin before hand as it’s likely your going to get a headache, some worse than others. The biggest thing it taught me, and I think the purpose of doing it was to show that you cannot self diagnose, that everyone gets stupid
-
Best story I read was the time to altitude record for a helicopter that the Army flew in I guess it was the 60’s in a Sikorsky Skycrane. The record was terminated when the air got thin enough that one of its main rotor blades stalled and fell out of track, causing I’m sure one heck of a vibration, so they started down and ATC called some Airliner and told them their traffic was an Army helicopter descending out of whatever flight level they had attained. It was apparently over 36,000 when the blade stalled and 1971, the record for some reason is at a lower altitude https://www.smithsonianmag.com/air-space-magazine/what-helicopter-climbs-fastest-180964354/ The AH-64A at its original mission gross weight of 17,500 lbs would climb at a sustained 5,000 ft per min to at least the first 12,000 ft or so. Later its gross weight was raised to 21,000 lbs and I don’t remember trying a max performance climb at that gross weight. The latest model of Chinook can carry significantly more weight than the CH-54 (crane) could and I imagine maybe it could go even higher?
-
I was doing engine testing to validate a ram air recovery inlet, Pratt came down and instrumented the airplane, it was an Experimental aircraft meant to be armed to primarily drop laser guided bombs from high altitude, but also to be a poor man’s Reaper drone. I also did our standard crop duster based on the owner of the factory, stupid exercise, waste of time, but this pic was the standard crop duster. I have no idea how high it could have gone, way higher than FL250 certainly but my mask was limited to FL 250 and that was high enough for the data we needed. I’m guessing the one with the Pitot inlet could have gone at least 10,000 ft higher, but I suspect much higher, who knows? It was at light weight with no loads. Silly as this may sound but I was uncomfortable up there in a Crop Duster.
-
Alternator STC SA 10682SC belt replacement
A64Pilot replied to CaptainRamius's topic in General Mooney Talk
Gates does manufacture very good belts, but like most everything else there are different grades. I believe their green stripe line is best, if that part number can be had as a green stripe belt I think I’d go that route. My data may be old, maybe there is something heavier duty than the green stripe now. Normally I’d say a belt is a standard part, but if the STC calls out a specific part by manufacturer and part number you are likely only allowed to use what they specify -
I’d start with a pre-buy and go to an Annual if the IA after getting a decent look thinks it’s a good airplane, but don’t waste your Annual money until your pretty sure it’s a good airplane. Don’t worry about paint and other cosmetic things and nickel and dime stuff like worn tires or whatever. Of course use them if possible to get a good price, but don’t pass on a very good 56 yr old airplane because the fabrics worn or has faded paint A pre-buy can be more comprehensive than an Annual, it’s not defined, all an Annual gets you is it has a min set of standards that must be followed, but crappy Annuals do exist, so it’s really important to shop the inspector pretty hard. I would want an Annual, it’s my opinion that the average IA is more careful with inspecting if their name is going in the book attesting to the aircraft airworthiness than they are telling you verbally it looks good to them. Use Mooney’s checklist for the Annual. If at all possible have the IA that will be taking care of the Airplane perform the Pre-buy / Annual. Your going to spend some $$ and you may not get anything out of it except being told to walk away, don’t be too upset if that happens, if it does that person most likely saved you a whole bunch of money, so buy them a beer and tell them thank you, you might just want them for the next airplane. Look really, really hard for corrosion, in fact make that your first inspection points, no need to go further if any significant corrosion is found. In my opinion on older aircraft but maybe not this old that factory worn interior and factory faded paint is a plus, it has to have been well cared for for factory P&I to last that long.
-
Ref the Sidewinder tug being too heavy to put into and out of the baggage compt. At 20 ish pounds I don’t think so, my electric scooter is over 30 I think as a reference. No doubt it takes up more room than a manual tow bar though, and it does have a Lithium Ion battery to consider, but then so does your phone and Ipad and likely other things too. Having fake knees and arthritic back and shoulders etc. the hardest part to me is getting the thing into and out of the nose wheel tube. If it’s level ground and you can use a regular tow bar without strain then that’s easier. The sidewinder comes into play when it’s uphill or you have a lip to go over or the plane is just too heavy for you to move by hand, or your old like me with a bad back etc. I knocked up a tow bar out of iron plumbing pipe and used my golf cart initially, but you have much more control with the Sidewinder and can of course feel the steering stops with it when you can’t the golf cart, so I’m very comfortable going all the way to the stops with the Sidewinder where as the golf cart could I believe pretty easily cause damage. If you want a power something that you can travel with I’m not aware of anything better than a Sidewinder, yet. I think if it were aluminum it would be better, but have no idea how much weight it would save nor how much more it would cost. If weight is an issue the drill motor I believe is easily removed without tools. I think just spin the clamp loose and unplug it.
-
I would assume during overhaul you got new baffling. By fixed center cowl flap are you talking about a modification? Cooling “lips” are very common on float planes because of course they are working harder at slower airspeed than wheeled aircraft and run hotter just like banner tow aircraft do. Here is a picture of one installed on a C-140 for example, I don’t know if it was ever on floats or the owner is just looking for additional cooling.
-
I was briefed years ago that it had gotten to the point that if you had a floor of people using type writers that it was possible by monitoring the buildings power supply to determine everything that was being typed. As I said it’s possible to monitor conversations being had from a significant distance simply by monitoring the I guess the magnetic field of the pilots microphone, significant as in line of sight distance, so miles. How practical is that? I’d guess not very
-
Many “house jacks” are mechanical screw type of mechanisms. I considered using one as aircraft jacks, if they can lift a house they certainly can support a Mooney. ‘Google House jack
-
They are on my wishlist, I have something home made that works, but I’d rather have the Meyers, but over $2k is tough, so I’m looking for used, but I suspect they are all spoken for and just about never come up for sale as I think many others have them on their list too. Personally if I were buying new I’d spend the extra grand on the Meyers over say the Alpha, you can home build an Alpha. A Meyers is beyond most people’s ability to build. It’s just a much safer jack. I beg to differ on nothing happens if a jack blows an O-ring or leaks down, it’s possible if one let’s go that the airplane could fall off of the other jack, especially if the wheels are up or the actuator or other parts are removed for repair or replacement, then it’s likely it will.
-
Bingo, that’s it. A Mooney may be climbing at as high or even a higher rate, but it’s going faster so it’s gradient is lower. The neighbor in his 180 HP 172 which is an older one that that H2AD motor I think and got converted to 180 HP will take off right before me, I’ll catch and pass him of course but he’s at a higher altitude when I do. I go by under him, a Bonanza or Viking goes by above him, the Viking above the Bo likely I suspect because it has 300 HP, but then they have at least 85 to 100 more HP than me too, but neither is much if any faster at cruise, but burn roughly 1/3 more fuel. I think actually I’m faster than the Viking, if so it’s not by much though, the Bo is faster than I am, but again not by much though. Say for example your told to cross X fix at or above a certain altitude, an airplane climbing at 1,000 FPM at 80 MPH will easily make that but another climbing at 1,000 FPM at 100 MPH may not. Cooling is the other issue, it seems other aircraft just don’t require as much speed to keep engine temps down, I suspect that’s simply Drag reduction of the Mooney, maybe the older Mooney’s don’t but it seems my J likes higher speeds to keep temps down. Higher speeds reduce both rate and gradient of course. There is a surprising amount of drag in engine cooling, you can find varying numbers on the internet but it’s one of the best places that big drag reduction can be had, I suspect some of the J’s drag reduction came from improved engine cooling air flow management. Don’t get me wrong it does really well for a four cylinder airplane, but then most four passenger four cylinder airplane’s aren’t strong climbers. Climb performance is a function of excess HP and when you only have 180 to 200 horses and your a moderately fast airplane there just isn’t a lot of excess.
-
Cam Guard creating starter adapter slipping
A64Pilot replied to NewMoon's topic in General Mooney Talk
I don’t think Camguard is intended or advertised to be a friction modifier. I think it’s intended to be a corrosion preventative, but I’m no expert on oils. I only know what I read, I have had no formal education on oil. But I’ve not dug into it so I don’t know. Corrosion is I’m sure one reason why cams fail, but I suspect it’s not a very big reason or I’d suspect that there would be a huge difference in cam failures in aircraft in Arizona and Florida or no failures in flight school aircraft that fly several times a week, but they fail too. The odd thing is I feel certain that “back in the day” they didn’t fail, why? Can it be as simple as age? Back then they weren’t that old? Fuel changed, 100LL is different than the fuel it replaced, could that be a factor? I suspicion part of it is the cams themselves are different somehow, meaning it’s the newer cams that are failing, that would explain why the Snowbirds in my neighborhood aren’t losing cams, vast majority of their aircraft are antiques, with antique engines, or maybe on the old cams the ones that were going to fail did so years ago, leaving only the ones that don’t fail in service? About at least 1/3 of my neighborhood are snowbirds, that is “Home” is up North and they go home every Summer, and they all own aircraft and none of them that I’m aware of preserve their engines and most are Lycomings. They do this every year, none fly their airplanes home. For some reason none have lost cams, a few I think have ended up with polished bores of course, but most haven’t. Frankly I can’t explain Lycoming cam failures, I can’t find any higher incidence in failures based on well, anything. I have never seen any evidence of internal corrosion of engines that haven’t spent long periods of time not being flown, and oddly sometimes no or only light corrosion in engines that haven’t flown in years while others literally right next door have serious corrosion. There are several airplanes in my neighborhood that have sat for years, sometimes the Husband dies and it’s years before the Wife sells his airplane. One a year or so ago was a very pristine twin Comanche, sat for years, bought by a couple of A&P’s. One cylinder had light corrosion, both cams were fine, they pulled a couple of cylinders to inspect. There is a C-140 that has sat for about the same time, it’s Continental is rusted so bad it’s seized. Same neighborhood both in dry as in no leaks hangers. My Wife inherited a 1923 Ford Model-T. Without getting too deep into it I’m nearly certain the car wasn’t operated likely since 1938 when I think it was restored. Anyway it had a couple of leaking valves and I pulled the head to re-cut valve seats and replace the valves. Car had been stored in several locations mostly Ohio in a barn type building then several years in a garage in Al and in a car transport trailer. Anyway there was zero as in no corrosion in the engine or cam. I expected pretty severe corrosion of course but there was none, not light corrosion but none. I can’t explain why. It had sat unused and no preserving for over 80 years. Then take boats, just about every larger boat that sits in salt water has salt water in the exhaust system, many sit for months at a time or longer, yet significant internal corrosion is very rare? I can’t explain that either. I mean they sit and some cylinder of course has an open exh valve and there is salt water in the exhaust, why don’t they rust solid? There is nothing special about their engines, they aren’t built from special metals, many are just “marinized” car and little tractor / forklift etc engines, sailboats that have little motors anyway. So why do airplane engines often rust if unused? They do, I’ve seen too many rusted and pitted cylinders so I know they do, but everything from farm tractors to boats, lawnmowers etc unless they get water in the cylinder, don’t. Why is that? Most every lawnmower sits unused for months at a time every year, some just under tarps or whatever, yet they don’t rust or some do I’m sure but most don’t. Sorry for the long post, engine corrosion is something that I have wondered about for years and it seems you can’t say for sure until you inspect. So does Cam Guard help? Who knows, if I flew infrequently I’d probably use it, but I feel pretty sure that’s it’s been out long enough and used by enough people that if it caused any problems that we would know by now. I wish there was an “energy conserving” airplane oil though as I think reducing friction would likely make our engines last longer, perhaps it’s the ashless requirement that keeps that from being possible, or maybe the amount of oil sold doesn’t support spending $$$ on improving the oil? -
I can believe that, I took the first post to mean initial rate as in low altitude climb. The RV’s are little airplanes with big motors, so of course they climb quickly, but that short thick wing is actually a high drag wing they get their speed from brute force not low drag, I imagine they aren’t stellar gliders. Mooney does do better at higher altitudes than down low, to me they just aren’t stellar climbers, I think due to their relatively low HP per size / weight of aircraft. It is only a 200 HP airplane, but then my Maule was only 235 and I don’t think many are going to try to claim a 4 cyl Mooney can climb with an M-6 235 Maule, but at high altitude it just might. Maule’s wing isn’t nearly as efficient by a long shot. Surprisingly the Mooney wing looks long but really isn’t longer than many. All 100 series Cessna’s from the lowly 172 and on have 36’ wings I believe, so real close to ours. The Bo has relatively short wings at 33’ , but has more wing area, even the 172 has more wing area than a Mooney, not by a whole lot