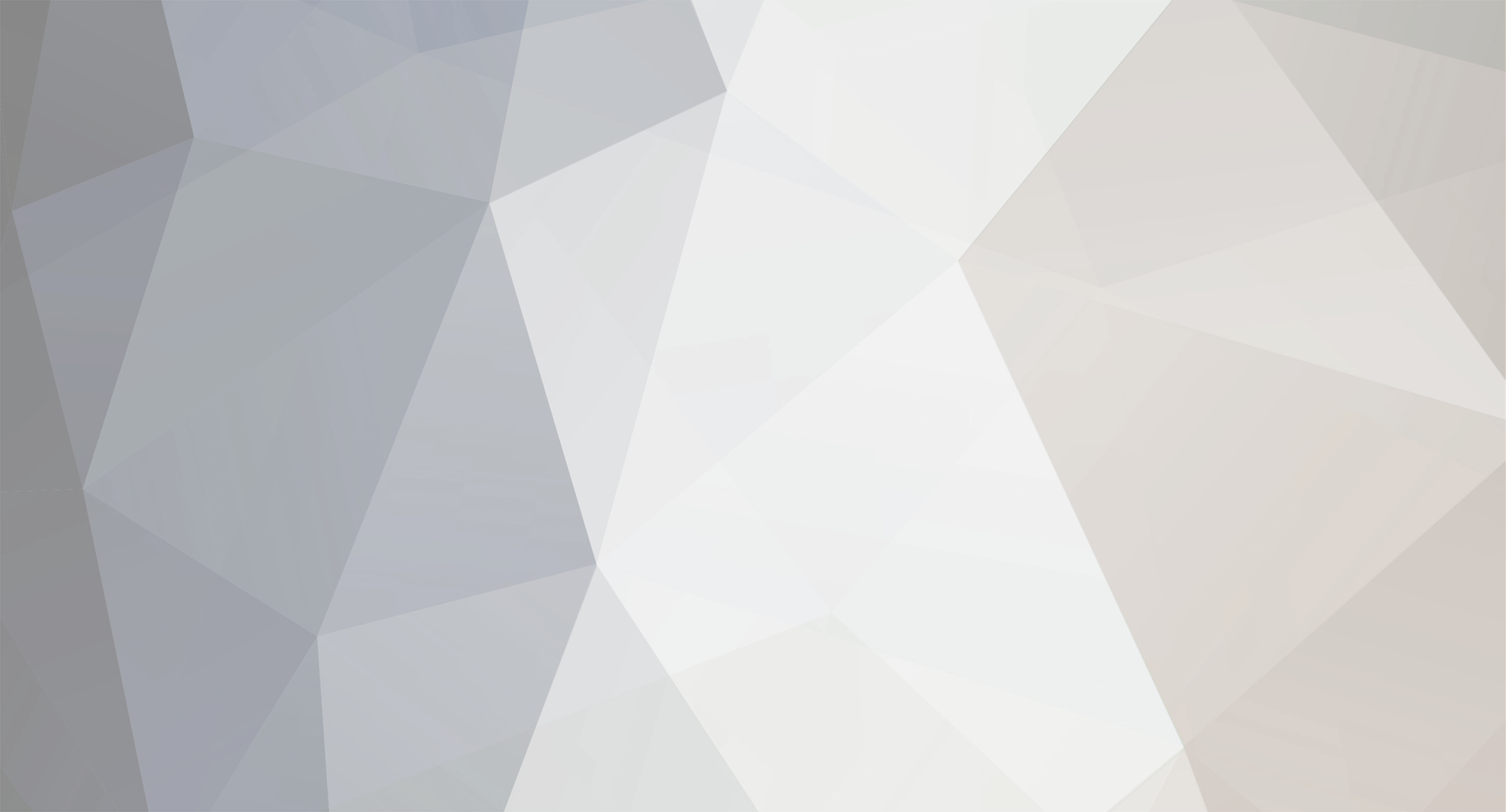
A64Pilot
Basic Member-
Posts
7,684 -
Joined
-
Last visited
-
Days Won
21
Content Type
Profiles
Forums
Blogs
Gallery
Downloads
Media Demo
Events
Everything posted by A64Pilot
-
Yes, well at higher power they do, in fact they have a sensor that adjust timing to achieve a point just prior to detonation. A “knock” sensor. It’s why higher power cars will actually get better fuel milage on high octane gas. The average grocery getter won’t though because they won’t approach detonation most times, in fact as premium car gas flame front spread is slightly slower having a similar effect to reducing timing, they may actually get slightly less mileage on premium. That's ignoring ETH or ethanol fuel, whike it does increase octane it’s BTU per volume is much less than gasoline. I used to hyper mile our Prius years ago as a game, and ETH fuel dropped milage by a significant margin, 10% almost if memory serves. It took a hit on ETH free Premium too 72.6 MPG was the best I ever got and that was no traffic back country roads using every trick I knew.
-
I know that, that’s why I said even if he knew how LOP wouldn’t have given him what he wanted which was to keep up with me, it was an IO-520 though and not a 550, a 300 HP 520, except your wrong on the 50 ROP, it’s a mixture that as long as you follow Lycomings directions and don’t lean above 75% power it’s a mixture that still gives good power, it’s a perfectly acceptable mixture and Lycomings have been running it and living long lives for far longer than any of us have been pilots. In fact follow Lycomings directions and you will never hurt a motor. You know though that I almost always cruise LOP. 120 KIAS I get 20 NMPG 135 KIAS I get 16.87 155 KIAS based on just about every magazine article I would get 14.7 NMPG, the 155 the mags quote is I’m sure ROP, because I doubt the average J can cruise 155 KIAS LOP. Yeah I know some are sure theirs will run 165 KIAS, but I suspect that’s Knots Internet Air Speed. Do you see a trend? Sure LOP saves some fuel, but the primary fuel savings is from speed reduction. One big thing that always seems to be ignored, and that’s only a fraction of the GA fleet is even capable of LOP, GAMI made some that were close capable but usually just barely, even with a small GAMI spread many engines just won’t run LOP most of the time, my 540 wouldn’t very well, just barely. The majority of the fleet when they lean to roughness then slowly enrichen end up often about 50 ROP but as they aren’t balanced it’s usually cylinders scattered from about peak to 50 ROP, and they do fine, so long as they don’t try it at high manifold pressure. However back before flat motors most everyone ran round motors LOP, especially the Supercharged ones. The “new way” to operate engines isn’t new, it’s 100 years old. You can see a round motor st night go LOP by watching it’s exhaust color Lycoming has a reputation to live up to, and it’s not one of being a dog, it’s one of making power, so they have never recommended a mixture that gives up too much power, if they did I’m sure they thought people would complain. Not beating on Continental, but I only can think of one race plane class with Continentals, no Aerobatic aircraft, and the real tell to me is no Helicopters. To detonate it takes among other things heat and a big reason being ROP or LOP enough prevents detonation is there isn’t enough heat. However going real rich wastes fuel but the power drop off is slight, go lean of peak and the power drops drastically. Thats the one reason we take off and climb ROP. It’s perfectly safe to do so IF, and that’s a BIG if, but if your engine will run LOP enough to prevent detonation. The problem is it would be a dog, serious decrease in performance. However it’s a rare motor that will run that lean, our angle valve Lycomings will but even in Lycomings it may be the only one that will. Years ago in my Maule I ran a simple test point, at my usual cruise altitude of between 10 and 12 thousand I ran LOP at full throttle and 2200 RPM (redline on that motor was 2400) it’s wasn’t but maybe 20 LOP it wouldn’t go any deeper. Anyway then adjusted mixture to 50 ROP and reduced throttle until I was at the exact airspeed, if memory serves the difference in fuel flow was less than 1 GPH. That airplanes engine was only a couple hundred hours after overhaul with Gami injectors and fine wire plugs and I had a MVP-50 so it was as equipped for LOP as was possible. I flew high because a Maule had too much wing for performance cruise and while you lose HP with altitude you lose drag even faster up to a point, that point for an M6 Maule was between 10 and 12 thousand feet. I used to do a lot of long cross countries in that airplane. One day I might do that in the Mooney just to see, maybe the Mooney is different However you have to ensure airspeeds are identical, if they aren’t then it’s not an apples to apples comparison. As you lose power LOP that’s why I say run that test full throttle, and truthfully your giving LOP a little advantage by being full throttle your reducing its pumping losses. My best mileage is 120 KIAS of course but who can fly that slow? I do sometimes when I’m in a group of slow airplanes, but my go to cruise is 8 GPH 23 squared which gives me 135 KIAS good fuel milage and at 60% power it’s below the number that Lycoming recommends for maximum engine life, because I hope to never have to buy an overhaul, and if I take care of it I won’t have to, that’s a function of being old. One day you realize you don’t have a need for a 30 year roof anymore.
-
Did someone say full rich? I’ve never heard of detonation or pre-ignition full rich. I’ve seen it happen on an airplane left leaned out and the pilot forgot to push the red knob back in, shot a touch and go and a few minutes into the climb heard the rattle, by then the damage was done. It’s odd though on every engine I’ve seen detonated to death it’s always one cylinder and not multiples. My Brother detonated the IO-520 to death. because he didn’t know what he was doing and was too lean for the power he was running. Even if he knew how LOP wasn’t an option at the speeds he was trying to make. Odd thing is the cars of the late 70’s would rattle like hell pulling a hill, but it never hurt anything?
-
Thanks I’ll have a look. I don’t need a backseat, it’s possible I may leave it out
-
While I don’t think it would hurt I don’t think your supposed to use nylon washers. Am I the only one that noticed rudder trim? on a J?
-
You can put your arms out and make decent turns. I’ve heard open the doors but surely that excessive. My C-140 and the early 150’s have identical fuselages, in fact the very early 150’s still have the 140 gear box in them, because they were 140’s, but Cessna had a whole bunch of unsold 140’s they didn’t want more. Cessna built over 7,600 of them in five years.
-
IF you trim for hands off at the bottom of the approach you need to practice with a full throttle go-around. Hint be prepared for excessive nose up pitching moment, if your prepared for it and have at least moderate upper body strength you can handle it, some weren’t and didn’t. I’m sure it’s why some have stalled Mooney’s on a go-around. If you think a Mooney is heavy in pitch, then you have never flown a C-210, with just two in the front seat it’s way heavier than a Mooney. Mooneys are heavy on the controls in my opinion because of the small control throws. I measured aileron throw the other day and if memory serves it was less than half my C-140, I didn’t measure elevator throw but bet it’s the same, without pedal extenders a Mooney has you sitting very close to the panel, you simply couldn’t have the control travel of a Cessna your chest is in the way, and that lack of travel means higher forces of course. Its the limited control travel that’s the reason of the myth of sports car like handling, in truth they are without being disrespectful but sort of doggy, especially in roll. It’s not supposed to handle like a Pitts though, it’s a stable cross country traveller and flown that way it’s plenty responsive. Frankly I’m at a loss to try to explain prop strikes. Every GA airplane I know of should be landed on the mains and the nose wheel kept in the air until it slowly comes down on its own, they should never be three pointed, landed flat whatever you call it. If you land and carry the nose in the air I don’t know how you could wheelbarrow or porpoise and prop strike. If your too fast, go around, never try to salvage a bad approach, just isn’t worth it.
-
Thanks, but if you watch the video it makes the point that it’s a variable volume but also variable pressure pump so many times that it seems apparent that many like me thought it was a variable volume but relatively constant pressure pump, but it’s not. Pretty hard to argue with that video. Diaphragm pumps that are constant volume and constant pressure pumps do exist, they work like vane and gearotor pumps do, that is they simply waste the excess volume through a pressure relief valve. So either we operate in a range that likely doesn’t even come close to max flow of the pump so that pressure remains relatively constant or really I don’t have another explanation, just be guessing.
-
As mine don’t work with the Master off I’m fairly sure they are electric, positive actually as I’ve seen the back side of them. 81 J If they are like I think they are they aren’t individual gauges, but a cluster, which of course is no longer obtainable. It works, it’s in the green barely, I’m not mucking with it. I know it works because if I leave the red knob out 15 min or so after shutdown the fuel pressure is astonishingly high so I’ve gotten in the habit of pushing the red knob in after shut down and bleeding the pressure off then of course pulling it back out. Knowing it works of course does not mean it’s accurate. Where is the transducer located anyway? Master off in my airplane literally leaves you with an artificial horizon, tach and MP gauge, standby compass and nothing else. I used to have a dead weight tester, with that verifying its accuracy would be simple.
-
I want to know how the single seat in an 81J is removed, it’s not obvious to me. I admit to not really trying yet though it’s always fallen below the line, but I should get in there and corrosion treat the main spar etc.
-
Well I stand corrected then, I thought what the video called the lost motion linkage would maintain set pressure. So does everyone else but me see significant pressure decrease in cruise compared to taxi RPM? If so how much? 95% or better of my time is turbines and they have either vane or gearotor pumps not diaphragms, the one other aircraft I’ve had that was fuel injected didn’t have fuel pressure gauge, it had a fuel flow gauge that was really a pressure gauge calibrated in GPH.
-
A vane pump allows flow even if the motor is seized, the Weldon I believe had a bypass valve I know because on the S2R-H80 I had two Weldon pumps in series, only one pump was run, the second was just a back-up in the event the first failed. There was no failure mode that wouldn’t allow fuel to flow through the pump. A diaphragm pump can provide constant pressure through a wide range of flow, until the pressure relief valve closes. At that point as liquids are incompressible then pressure will fall off of a cliff. Often for a simple GM type of diaphragm fuel pump pressure is regulated by a spring on the diaphragm, when set pressure is reached instead of the diaphragm moving the spring is compressed so the stroke of the pump is variable to maintain a constant pressure.
-
Pressure is the same regardless of fuel flow or which tank. If there was a restriction then of course pressure would drop as flow increased and go up when there was no flow. So it’s either both pumps are at the low end of acceptable (unlikely I think) or the gauge is reading incorrectly. My bet is gauge, but transducer or gauge itself?
-
Flow is what’s relevant, if you can get flow, you have enough pressure. My cold oil pressure in run up is in the yellow, but I believe Lycoming recently raised the max oil pressure limit by quite a bit, doesn’t change our POH of course or redlines on our gauges but may lessen the concern. I don’t think my cold oil relief valve is cracked open in cruise as my pressure will increase with RPM, if it’s fully closed then of course all that will change if I shimmed it more the pressure when cold will go even higher but my cruise pressure won’t change. So I think what I have is what I have, but I’ve not verified the oil pressure either. I understand the advantage of no wet lines in the cockpit, but I’m not completely sold on electric gauges, mechanical ones are more reliable. About 1 min after takeoff from X23 yesterday to take my Son home the high / low volt light started flashing, quick check showed alternator off line, turning master on and off did nothing as well as recycling the field CB, I set up cruise at 23 squared and 8GPH and turned off the master for the flight, which meant that I only had RPM and MP pressure, no other engine gauges at all, if they were mechanical I’d still have had them. When I landed at Camilla I hooked his truck to my jumper cables, charged for 15 min or so and left the cables connected for starting, and came home Master off. Must not have used much battery as my tender only took an hour for full charge. Luckily turned out to be a broken terminal to the field on the alternator. Took a look at that and at least on my aircraft the wire was unsupported for quite a length, added a short piece to the wire and zip tied it to the larger alt output wire and left a drain loop just to remove the strain from the terminal end, maybe that will help keep it from breaking again? Seems to happen often enough on Mooney’s it’s likely there is a common cause, I’m thinking the unsupported wire could be it.
-
No, and boost doesn’t raise it but a tiny bit, based on both boost and mechanical giving the same pressure readings and no operating issues as in my 19 GPH on takeoff doesn’t change pressure, I’m letting sleeping dogs lie. But I don’t like operating in the bottom of a range, since taking that photo I’ve added a washer or two to oil pressure which brought it up a little but not as much as I’d like, I like oil pressure at the top of the green
-
Rate of fatal accidents in Mooneys over time
A64Pilot replied to DXB's topic in Mooney Safety & Accident Discussion
They actually could afford them 50 years ago, as a kid going to the local airport on a weekend you couldn’t wash your airplane unless you got there early. Too many in line. There would be 10 pilots in one of the two FBO’s discussing the exact same thing we argue about now, like reduced power climbs and leaning it out etc. So much traffic there were two follow me trucks that would race to the taxiway vying you to follow them to their FBO, of course two full maintenance shops on the field, and one full blown Avionics shop. Full blown pilot school with a fleet of newish Beechcraft’s to train in and rent and several CFI’s on staff, They sold the aircraft and bought new about every two years, who would rent an old airplane? Same town today there is one FBO locked behind what looks like a prison fence that services the occasional Biz Jet, I think there may be one aging A&P/IA associated with it. Avionics shop is gone, no traffic to speak of on Weekends and you occasionally see some old Dr dragging his Baron out of a T hangar, no rental aircraft, maybe one or two beat to death OLD 172’s but I don’t think so. Incidentally the towns population is more than double what it was in 1970. Back then before you left to go to the airport you called the FBO and they would pull your aircraft out of the hangar and put it on line, it was part of hangar rent, when you got back they would top it off and put it away. No T hangars back then, but then you didn’t pump your own car gas either, or put air in your tires or check oil. Different, more affluent world for Joe Average There were more aircraft manufacturers doing a good business than there were Auto manufacturers. Average airplane was five or less years old, but most pilots were plumbers, electricians, house builders, Pharmacist's and of course Doctors. Price of a 172 in 1970 was $12,500, about half the price of the average house. Median price of house now is supposed to be $380,000, can you get a new 172 for half that now? If you could I bet airplanes would be selling. https://www.statista.com/statistics/272776/median-price-of-existing-homes-in-the-united-states-from-2011/ Oh, and average age of GA aircraft isn’t 5 years old anymore, it’s more like 50 years old according to the FAA, and there are only a couple of GA manufacturers, most that are still building GA aircraft make their money from building Biz Jets but still build the rare single engine piston out of tradition I guess. https://www.faasafety.gov/files/events/EA/EA68/2023/EA68121005/EA68121005F.pdf -
No, and boost doesn’t raise it but a tiny bit, based on both boost and mechanical giving the same pressure readings and no operating issues as in my 19 GPH on takeoff doesn’t change pressure, I’m letting sleeping dogs lie. But I don’t like operating in the bottom of a range, since taking that photo I’ve added a washer or two to oil pressure which brought it up a little but not as much as I’d like, I like oil pressure at the top of the green
-
To keep the cyl head temps in the middle of the green. LOP is a reduction in power and therefore CHT temps. Attached photo is Cruise in Florida cowl flaps fully closed as I almost always cruise that way. OAT I’d guess mid 60’s F but don’t remember, full throttle, RPM probably 2300 because she’s smooth there and LOP burning 8.2 GPH. Pretty warm temps. Using the 14.9 number that’s 61% power which is all you can get at 8500 with mid range RPM, you can get more of course by going ROP, but that burns more fuel and has other detrimental effects besides just the wallet. I adjust cowl flaps to whatever opening gives me the middle of the green temps.
-
Just read the accident report you linked, what was the cause of the engine failure?
-
Mine is N1141N, ATC always has trouble with that, so now I say November eleven, forty one November, that’s easier to get your head wrapped around. I reserved my old Maule number as I had it changed to my initials when I recovered it and the other day found it available again, oddly when you search the FAA database according to them my Maule never existed. So I reserved it in case I repaint the Mooney, unlikely but it is only $10 a year, what annoys me no end is if you look up that N number it shows my full name and address, why not post my Social Security number while we are at it?
-
P-38 procedure for LOP in 1940 something NOTES ON MIXTURE CONTROL The engine ls fitted with a Bendix-Stromberg carburettor Instead of the usual two-position mixture control, as fitted to British engines. the mixture control has the following 4 main positions: FULL RICH: In this position there is no automatic compensation for altitude and temperature AUTOMATIC RICH: This is the position for the richest mixture which is automatically maintained by the compensating device. AUTOMATIC LEAN: This is the normd position for weak mixture. The automatic device maintains the mixture at this setting also. IDLE CUT OFF: For stopping the engine and while priming during engine starting operations. Furthermore, the mixture strength can be progressively weakened by moving the lever from the AUTOMATIC HIGH position towards the IDLE CUT-OFF position, the weakening being effective also in the region beyond the AUTOMATIC LEAN position up to the point where the IDLE CUT-OFF operates (at the extreme end of the travel). At any point in this range the automatic compensating device is in operation. Although placing the mixture control in the AUTOMATIC LEAN position gives a considerable reduction in fuel consumption, it is possible to obtain a consumption of about 5% lower by adjusting the mixture control as follows: 1. Obtain the desired engine cruising conditions 2. Change the airscrew control from AUTOMATIC to MANUAL. In this position the airscrew becomes effectively a fixed pitch airscrew 3. Set the mixture control to the position determined by weakening the mixture until a drop of 40 to 50 R.P.M. is indicated. The position may possibly be between AUTOMATIC LEAN and IDLE CUT OFF 4. Return the airscrew control to AUTOMATIC If changes in altitude or cruising conditions are made, this setting should be checked by repeating the above operations.
-
There is a triad to most efficient, full throttle because it reduces pumping losses, it’s one reason why Diesels are so efficient, because there is never any vacuum in ones manifold, even at idle they are at full throttle, as there is no throttle. Best BSFC which is normally LOP, a stock Diesel is always LOP, because it’s throttled only by fuel flow, get one ROP and it smokes heavily. Then lastly very low RPM to reduce frictional losses. The toyota Prius is an exercise in operating efficiently, it can’t go LOP due to emissions, but it’s very common for the Prius computer to be running the car at 1200 RPM or so and full throttle, the Prius PSD or transmission if you will can vary RPM over a wide range, so it’s computer would run the engine full throttle and dial the RPM down until power developed matched demand. It did other tricks too of course. Pumping losses are real but minuscule. Try it yourself, climb up decently high (say 10 to 12 thousand or so), go full throttle at low RPM, then increase RPM significantly and reduce throttle until airspeed matches the first test point exactly, give several minutes for it to stabilize, you guys with Autopilots have a real advantage, but compare fuel flows, the lower RPM should be lower due to both greater prop efficiency and less engine friction, so operating high MP and low RPM is more efficient, that was what Lindbergh went to the Pacific theater to teach in WWII, incidentally the P-38’s POH had a procedure to lean to LOP, they just didn’t call it that then. Maybe it will work in a Mooney, but when I ran the test points in a Maule it really didn’t make much difference, there is increased efficiency, just wasn’t as much as I had hoped. I say go up high in order to be able to stay with the factory chart limits of not being too oversquare, but look at your charts perhaps you won’t need to go so high
-
It’s 75% power in a Lycoming, not 65%. It’s 65% power in a Lycoming for max engine life, or do you guys think Lycoming doesn’t know what they are talking about with this too? Its tough to exceed 75% power above 5,000 ft running ROP, do you guys think you are LOP? Or do you do cross country flights down low?
-
I’m hoping for at least two manufacturers and an established track record. Competition seems to drive both quality and cost. I know want in one hand etc. In the Military there was a saying, “never fly the A model of anything”. I flew an A for years, later the D model, the D really was much more reliable, so maybe there is something to that saying. I don’t expect any magic, hopefully reliability and decreased inspections
-
I know that and thought I had explained that adinfanitum Point I try apparently unsuccessfully to make is if you stay within those numbers you are protected if you make a mistake is all, because as you say those numbers are safe for ANY setting. I guess too just ignore that Lycoming says for max engine life to fly at or below 65% power too? Anyone is free to do as they please, years ago I was taught during a risk analysis class the most conservative response rule, that is when faced with more than one possibility, choose the one that’s less likely to get you into trouble. It’s in everything, some push fuel, argue that you don’t have to land with the reserve just have planned to have it. Most conservative response is land and re-fuel. Those that are arrogant enough to believe they are better, that they know what they are doing, that they don’t make mistakes can of course operate as they please.