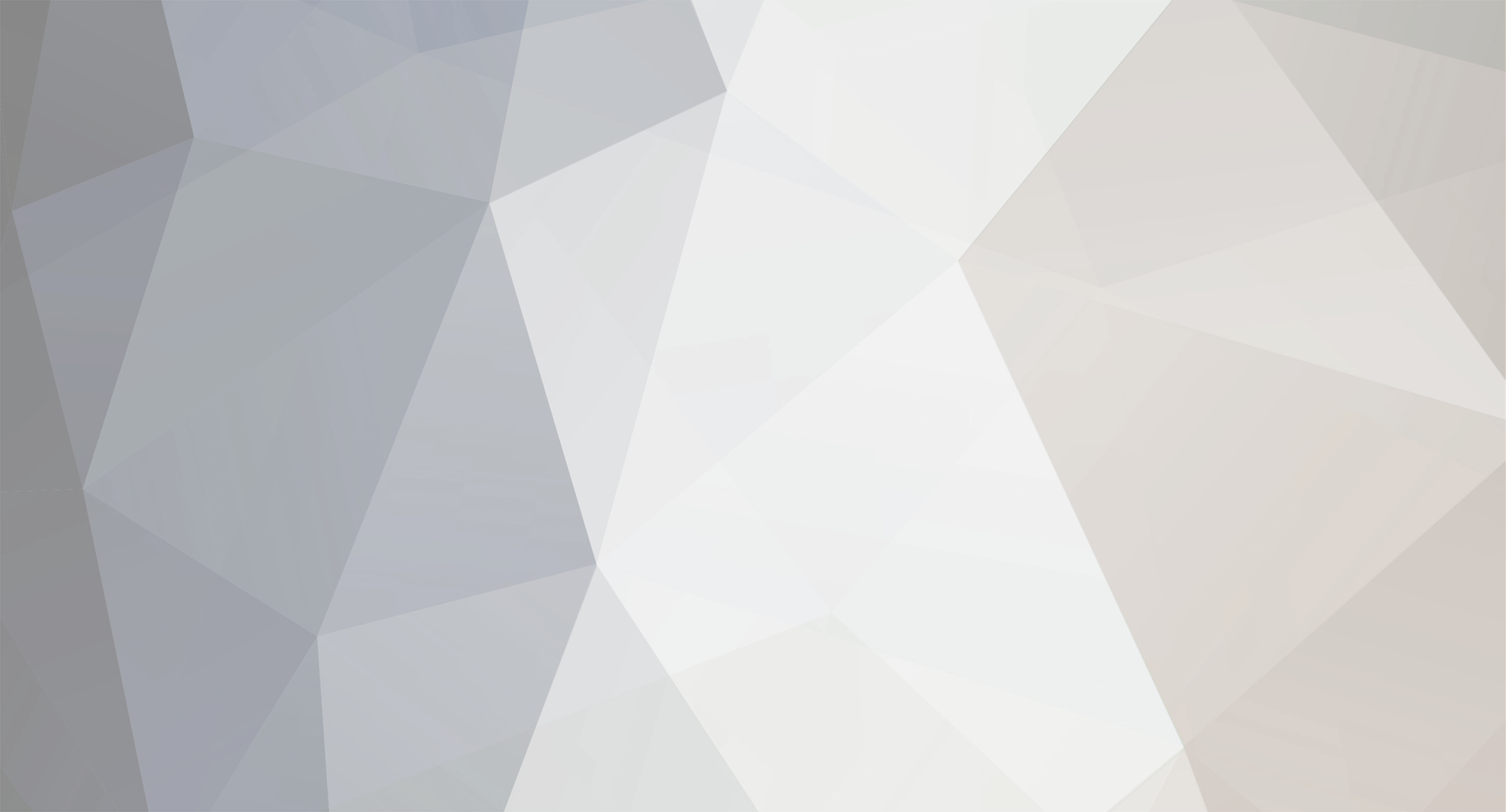
A64Pilot
Basic Member-
Posts
7,896 -
Joined
-
Last visited
-
Days Won
21
Everything posted by A64Pilot
-
Not really, almost all spark ignition engines are indirectly injected, that is to say the fuel is usually injected onto the back of the intake valve and waits for the engine to inhale it. Until very recently ver few spark ignition engines were direct injection,which means the fuel is directly injected into the combustion chamber, Mazda is coming out with a direct injected gasoline motor which is very similar to a Diesel, just burns gasoline. It’s sort of a hybrid spark / Diesel engine https://www.extremetech.com/extreme/253842-mazdas-2019-efficiency-breakthrough-diesel-engine-runs-gasoline injecting to the back side of the intake valve does several things, it cools the valve for one, but more importantly it means you can continuously inject fuel and let the engine “inhale” it when it’s ready to do so. ‘A very major reason why Diesels are relatively low RPM motors is that you have to time fuel injection to when it’s time for combustion to occur, which is a very small amount of time, and until very recently with common rail the injection pressure to shorten the time interval required with higher RPM just wasn’t possible, Common rail runs such high pressures that its enabled all kinds of new possibilities with Diesels like multiple injection events and variable timing etc, well pressure and electronic injectors of course. ‘We aren’t carbureted because we have dry intakes, and carbureted motors don’t. ‘Now if we were Throttle body injection, then we’ll that’s pretty much a carburetor in a way, but we aren’t.
-
I have the same and when finances allow I’ll install a monitor, but a very valid argument is that my airplane has been flying around for 40 years without one, and it’s original engine made TBO. ‘So just how essential is a monitor? I’m an engine guy, and I like having the info available, so I’ll install one, but readily concede that an engine can be operated well and safely without one.
-
Honestly it appears that my IO-360 Lycoming will run smoothly LOP until the power is just so low that it’s just not logical to cruise that way, without Gami’s. ‘I’ve had Gami’s on two air-lane previously, a C-210 with IO-520 and my Maule with an IO-540. ‘I think Continentals combustion chamber design will allow LOP and still produce good power, and Lycoming’s is less tolerant as in power drops off more quickly LOP. Neither engine is bad and neither is superior, they are very similar, but are different. My IO-360 is a field overhaul, by someone who has a good reputation with the locals and advertises he balances within 1 gm, he may be CC’ing combustion chambers too, I don’t know, or just as likely my engine just got lucky and the fuel flows happen to match up with each cylinder by luck?
-
Cylinder wear isn’t really so much a function temp as Heads are, cylinders don’t really get that hot, because combustion doesn’t occur there and mostly because hot gases are not expelled through the cylinder, but through the head. That is why GM in the 90’s finally began to “reverse” coolant flow through their engines and put the coolest water into the heads first and then onto the cylinders. previously the coolant flow was from the bottom up, because way back in the day engines didn’t have water pumps and were cooled by thermal siphon, which simply means heat rises. ‘But we don’t monitor cylinder temps because it’s simply not a issue, we monitor cylinder head temps because it is
-
They chart is useful, even though it only is at one operating condition, it does show HP outputs relation to mixture etc. ‘But another thing, you can’t really “balance” injectors as individual cylinders are not balanced, they have different sized combustion chambers resulting in different compression ratios and even the piston are not identical. rods different length etc. ‘A lean burn engine is nothing new either, Chrysler and I believe Honda did it in the 70’s but abandoned it due to emission problems it presents, the Current Suzuki outboards use lean burn at certain RPM’s when possible, it’s not at lower RPM as the engine woud run rough and at high power y9u can’t be lean or you’ll put holes in your pistons, but at mid power levels the Suzuki will go very lean and sip fuel. Absolutely
-
No, fuel flow does matter, it matters a whole lot. What shoud be considered is that throttling by fuel flow is nothing new, Long time ago a guy named Rudolph Diesel developed an engine that was entirely throttled by fuel flow, it operates at all times without a throttle valve regulating air flow, it never has a vacuum in its intake manifold, it’s if you will the ultimate LOP engine. It also demonstrates rather well that fuel flow does matter, as fuel flow is the way that power production is regulated. One thing people lose sight of is that these engines are heat engines, that is the motive force is derived by the rapid expansion of air from heating, it’s not an explosion or anything else, it’s no different than a turbine in that respect, and just like a turbine the max power output is pretty much determined by how much heat the engine can handle. ‘So within limits increasing the amount of air that’s available to expand by heat will increase efficiency, but the heat has ti there to expand the air, and of course the heat comes from fuel flow.. A turbo is a pure heat driven turbine, and what makes a turbo “happy” is lower temps, and 25 LOP is hotter than 50 ROP, by 25 degrees of course. Replace those numbers with any others you want to, a turbo only know temps, it doesn’t care LOP or ROP. ‘Cylinder head temps follow power production, they are cooler at LOP because power is down, not because there is any “excess” air available to cool the heads.
-
What they don’t say is that LOP is simply another way of reducing power, you see identical results by decreasing manifold pressure once LOP. ‘What they also don’t say also is that there is an efficiency peak, they seem to indicate that the leaner, the more efficient. ‘I don’t want this to turn into a LOP discussion, if you want to operate deep LOP that’s fine. My experience with it is at the altitudes I travel at that it just doesn't make enough power
-
Higher RPM is not just more distance travelled, it’s mostly the kinetic energy that has to be dealt with as reciprocating mass comes to a complete stop and rapidly accelerates in the opposite direction., those forces are transmitted through the bearings of course. The rotating mass, crankshaft etc has essentially no max RPM, or said another way its actual limit is well in excess of the reciprocating parts. The upper RPM limit of a race motor is set by piston speed, the piston is the weak limit. From a TBO perspective, an engine is designed to be run at max allowable continuous power until TBO, it’s if you wanting to go beyond TBO, or if at TBO your not wanting to buy a bunch of parts is where part power comes in. My 540 at overhaul all the hard parts met new limits so I didn’t turn the crank or have to buy one, largely because it was a 235 and had a redline RPM of 2400. Lycoming has stated in print that motors run at or below 65% power will last longer
-
Fuel flow is missing as well as actual EGT, now I know EGT will change based on location but the delta won’t. as well as fuel flow differences, they ought to be the same. ‘For that matter, where do the numbers in red come from? Lycoming? or did someone else put them there? Not arguing their accuracy, just thinking that they ought to be in the chart for the chart to meaningful. Of course that’s why they were added wasn’t it? ‘This chart to me is meant to be representative, meant to illustrate something. What I’d like is a performance planning chart, one with numbers. If correct it does seem to indicate that the efficiency peak is at -20F LOP and that by running even lower LOP is less efficient doesn’t it? Assuming the numbers in Red are real and correct of course, but either way it shows a efficiency peak, which is not what you usually hear from LOP converts, they often say the leaner the better
-
Unfortunately Lycoming chose to not put numbers on that chart, rendering it pretty much useless
-
Now, I’ve not worked on Mooney’s before so this is a general aircraft statement. But there should be a battery power wire already in the aircraft as electric clocks are common, and if memory serves correctly this wire is required by FAR to have within 1 foot of the battery to have a circuit protection device, most often a simple cartridge fuse. Nothing else that I’m aware of should remain “hot” with the master off. However I concede that I’m used to working on older type aircraft and these modern glass displays may have a keep alive power similar to a clock, but would expect them to still be fused within one foot of the battery if they were.
-
Yes the C-210 with an IO-520 I flew a lot was OK with LOP, OK meaning didn’t fall on its face. My Parallel valve IO-540 wasn’t, it lost too much power to be usable, Unsure how my angle valve Lycoming in the Mooney will. However what’s interesting is that it will operate smoothly LOP until power just goes away, meaning fuel flow is sufficiently balanced with stock injectors, no Gami’s needed. I think I will likely stick with Lycomings recommendation and operate at peak at 65% or lower power, I assume Lycoming recommends this due to possibly their combustion chamber shape simply losing power at LOP, it will run of course but loses power, and that may make customers unhappy, so don’t recommend it.
-
how much oil - M20J - IO-360-A3B6D
A64Pilot replied to dominikos's topic in Modern Mooney Discussion
The 2 quart level is a level that if you fall below will result in engine failure and if doesn’t I believe that oil level supposedly requires an overhaul. The upper level is determined by hours of fuel on board of a standard airplane, then using the max allowable oil consumption multiplied by number of hours of fuel available won’t take you below the min safe level. This is why identical engines in different aircraft will have different min oil levels according to the POH. ‘This is the formula used to determine max oil consumption for Lycoming’s .006 x BHP x 4 ÷ 7.4 = Qt./Hr. https://www.victor-aviation.com/pdf/tech-docs/SI1427B.pdf So if I do the math correctly, and check it cause I often mess up the math, but we are allowed to use .65 quarts per hour and it’s not excessive. So take .65 quarts times the max time aloft we can achieve, add that to two and you will get the min oil level at take off. Understand that’s MIN level, not recommended level and it allows for zero leakage. so a little extra can be similar to having a little extra fuel in the tanks Most engines max level is above the point where it will blow out the excess, the engine manufacturers know that of course but that allowable level may be required in order to ensure some aircraft can use that engine due to the rather long endurance they may have. ‘For some reason STC’d long range or ferry tanks are not accounted for in this oil consumption formula, so it’s possible in theory to run out of oil if your ferrying an aircraft for example, why long range tanks don’t require higher oil levels I can’t explain, it would seem they should. Who would fly a aircraft that burns a half quart an hour? -
Where do you find this lean of peak table your adjusting fuel flow to? That would be helpful as X fuel flow at X RPM should equal X percentage of power output, within limits of course. Previously I had to find peak on the richest cylinder, then lean to get desired LOP setting, anything below -20 made the airplane unacceptably slow on my 540, and at the altitudes that gave me the highest true airspeeds (9 to 11,000) I lost too much airspeed LOP so I abandoned it, LOP works, it does reduce fuel consumption, but for me in the last airplane that was instrumented and equipped for it, it did so I believe primarily by reducing power so much. 50 LOP is a huge power loss, and at altitude there is no “simply increase throttle to recover power lost” your already there, turbo may be different, I speak of normally aspirated Oh, and on edit, wear is directly tied to RPM, one theory is its because of the kinetic energy of the rotating components, the higher the kinetic energy that there is, the higher the wear. I believe it’s largely due to the forces required in a reciprocating engine in reversing directions thousands of times per min. Plus of course for things like rings and bearing surfaces, the higher RPM results in more distance per unit of time they are drug across cylinder walls etc. RPM is the biggest reason why slow turning stationary motors last so much longer than their higher turning cousins, generators for instance in your part of the world to get 50Hz a single pole generator turns 3000 RPM, a double pole, 1500. The 1500 RPM generator lasts longer, twice as long? maybe not, but it’s generally accepted that the life is longer.
-
It would be very unusual for a prop to be more efficient at high RPM, the reason is drag, at higher RPM, the drag increase is quite substantial. But there is a lot of misunderstanding about props, due largely to marketing. Engines are geared to slow down the prop, even the old R-1340 was both direct drive and geared, gearing adds weight and complexity so of course direct drive is preferred, but that means you need to make power at a low RPM due to prop limitations and that’s tough, so it’s a compromise as everything is. ‘However even if a prop was more efficient at high RPM, the engine isn’t, the reason it’s not is drag, it takes quite a lot of energy to spin a motor and that energy is of course “wasted” as in it’s not being used to drive the airplane. ‘So from a efficiency perspective the lowest RPM that will allow you to make the required power will almost always be the most efficient. ‘However as of course horsepower is torque times RPM, once you reach the torque limit an engine can produce the only way to get more power is by turning up the RPM. The Toyota Prius is of course an example of an engine designed and operated as efficiently as possible, the Prius is computer controlled, and most often the Prius is run at wide open throttle with the computer turning down the engine RPM via the planetary gear system so that at full throttle it’s output matches what’s required. It’s not uncommon to see a Prius at 1200 RPMor less even at highway speed if your going slightly down a hill etc.
-
Looking for Hangar in central Florida
A64Pilot replied to BillC's topic in Hangars / Aviation Real Estate
Not sure where Brooksville is exactly, but to get it out of the weather until you find something closer I bet we could probably fit it inside of my hanger. ‘I’m in Weirsdale Fl which is real close to the Villages, South of Ocala. -
Home & hangar for sale near Atlanta
A64Pilot replied to Patriot1's topic in Hangars / Aviation Real Estate
I know this sounds nuts, but at 97fl we pay $150 a year. I’m pushing to have that increased as it just covers expenses and I’d like to see a fund build up for expenses that you know will eventually happen, but it’s falling on deaf ears. -
One possibility is he hit the car that was moving much slower with his righting tip, that could have pulled the aircraft around 90 degrees to the right?
-
So without going out and flying it, what power setting gets you 120 KIas?
-
Just looking and correct me if I’m wrong, but Carson’s speed is 1.316 time VG? Understand I learned what Carson’s speed was about 1 min ago. A J model’s VG is 90 KIAS? If so then 1.316 times 90 is 118 or so, which is so close to 120 that you can consider 120 as being the best speed for endurance ‘ fuel consumption and the desire to actually get somewhere?
-
I had to look up Carson’s speed because I had never heard of it, but it’s apparently the right side of what in the Military was referred to as “bucket” airspeed or close anyway. If you look at any L/D chart, even helicopters you’ll notice that it’s bucket shaped and Carson’s speed is apparently the front edge or right side of that “bucket” A nice compromise in speed vs fuel consumption
-
Just looking for power settings for when we are just out for the fun of flying or maybe sightseeing, looking at the trees turning color or whatever, not trying to maximize anything, a nice comfortable cruise is all, one that generates enough heat to keep the oil above 180f etc. I just got my Mooney and it will be a couple of months until the finances recover enough for me to install an engine monitor so all I have is the 40 yr old factory gauges so I only have approximations of what oil temp and cyl head temps are
-
Primary efficiency gains from LOP is from slowing down, not so much from an increase in BSFC. However there are a few people who stand to gain financially from selling products that if they are to be believed are required for LOP operation so it’s not surprising there are converts. Bottom line, if you keep power output low enough you simply can’t hurt your engine with the mixture knob, and rich mixtures are only required at very high power outputs which are of course inefficient. Maybe I should come “clean” a little, I have a background in aircraft testing, not really piston engine aircraft, but testing is testing. I’ve done some testing in my Maule with an IO-540W1A5D Lycoming that had Gami’s and fine wire plugs, engine was well broken in with a couple hundred hours on new Millennium cylinders and I had a MVP-50 that was multi point calibrated within 90 days. Anyway what I came up with was that the majority of efficiency increase from LOP came from the rather serious reduction in power output and not so much from any increase in actual engine efficiency gained from LOP. Said another way, set an exact airspeed say at peak EGT, write down the fuel burn, than set that same airspeed LOP and see what fuel burn is. You may find that the biggest variable is airspeed and if your after absolute minimum fuel consumption, that poking along at Vy is likely to give you the max range and endurance, but who can stand flying that slow? However what I was asking is whats some good settings that the engine runs smoothly and keeps oil temp above 180F in a typical warm day and what airspeed do you get and the fuel burn. In theory if your after absolute min consumption, full throttle to reduce pumping losses and very low RPM for prop efficiency and engine drag reduction and leaned as far as it will run to reduce power output as low as possible and airframe drag due to lower airspeed is the answer, and that’s ignoring altitude, which is of course not an insignificant variable.
-
I guess this is a model specific question, mine is a J. ‘I know many are all about speed, but sometimes your not in a hurry and efficiency has its own attractions. So what do you J model guys use for a low power cruise manifold and rpm setting wise? I know in theory that low RPM increases both propellor efficiency and reduces engine drag so the lower the RPM, the more efficient on paper. But I’ve done some testing with a different airframe and found that while I’m sure that’s a correct statement that the differences weren’t measurable with a known accurate to .1 GPH fuel flow gauge and indicated airspeed. My motor seems “happiest” vibration wise not going lower than 2350, but I’ve not extensively studied this, there may be sweet spots at lower RPM’s that I’m unaware of, plus I don’t know how well my prop is balanced as it’s a new to me airplane, so what power settings do others use? I’m not meaning this to get into a LOP discussion, although it may end up delving into that, just wondering what others use for a power setting and why those numbers is all.