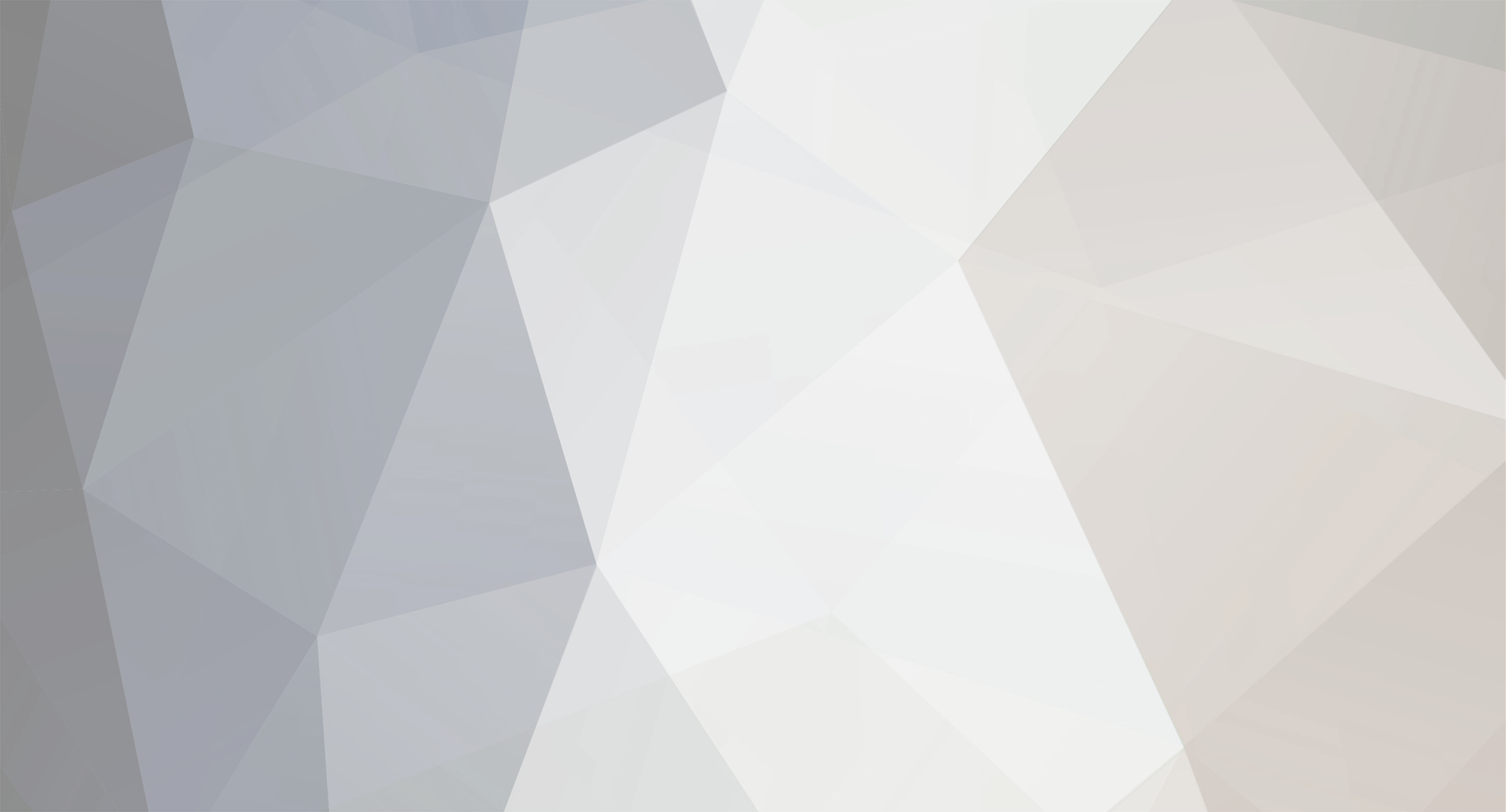
A64Pilot
Basic Member-
Posts
7,885 -
Joined
-
Last visited
-
Days Won
21
Content Type
Profiles
Forums
Blogs
Gallery
Downloads
Media Demo
Events
Everything posted by A64Pilot
-
I have been down this route with different regulatory agencies including the FAA. If it’s installed in the aircraft, and there is no required equipment list, then from a regulatory perspective, it has to work. The line of thought is how can a pilot determine what equipment is necessary for flight if it’s not called out in a min equipment list? Trust me pointing out the required equipment list in part 91 won’t work. My answer would be to not make a write up in the logbook or placard the piece of equipment as inop, and if asked, which is extremely unlikely, I mean less likely than winning the lottery. answer that it broke on the last flight.
-
My ashtrays are rusty and look like crap. so I’d like to replace them with something, 81 J model as I assume they may be different by year ‘Searching finds a device called an ashlight that some say Spruce has, but I can’t find it on a search. New ash trays would be preferable if they exist, Univair lists two Cessna ash trays, one is $125 ea, the other like $600 ea. so that’s out even if they are correct. These things have to come from somewhere else, some kind of car or boat maybe? can’t be aircraft specific ‘Anyone have a source on replacement ashtrays or ash lights or anything to plug those holes?
-
Going off of memory a NAS bolt is not a close tolerance bolt. ‘However the difference between an AN and NAS is that the NAS is significantly stronger OK, looked it up an AN bolt is 125,000 tensile strength an NAS is 160,000 both can be close tolerance, if they are they have a triangle on the head.
-
If you read Lycomings literature, they even state pretty often that engines operated at 65% power or lower will last longer. ‘Ever heard of TANSTAAFL? It’s from one of my favorite Science Fiction writers, it’s “There Ain’t No Such Thing As A Free Lunch” Simply stated it says there are advantages and disadvantages to every single way that you can operate an engine, so pick a way that fits your desires and to Hell with all the supposed experts, most of us fly less than 100 hours per year. my aircraft is 41 years old and has 2200 hours on it, and that’s not all that unusual. Engine was overhauled 10 years ago and has about 400 hours on it, It may never reach overhaul while I own it. So it’s likely that for most of us that we won’t ever fly an engine for a full overhaul period, so making changes to the way we want to fly to get 10% longer life from an engine does what? ‘But for instance I’m going flying today, the mission is just to fly, and hopefully to introduce our little dog to flying, so why bore around at high speed, burning fuel? Slow down burn less fuel, make less noise and make the turbulence more comfortable?
-
No, I don't have any papers etc, I’m just an old engine builder and A&P etc. In my earlier years I raced most anything on wheels, and built the motors. ‘Even though I’ve always said that we fly behind our Grandfather’s engines, they are more advanced than many realize. It’s the exhaust more than anything that “kills” most existing aircraft installations. The engine manufacturers have little to nothing todo with exhaust design, it’s supplied by the airframe manufacturer and almost often ease of manufacturing / cost / weight / fitting into existing space etc take precedence over performance. ‘Still I wouldn’t be surprised if our engines aren’t operating close to 100% volumetric efficiency at full throttle openings, and if they had an honest tuned exhaust, they should. There are a whole lot of misunderstandings about our motors and even more marketing selling “improvements” for them that more often than not offer little actual improvements and or bring out their own sets of problems.
-
I’m new and just noticed this thread. ‘Is this device made by Aglaser? Years ago I had a very similar device added to the factory drawings for a laser altimeter for Ag aircraft, and this looks awfully similar
-
Where did you get that model? The other day if memory serves I was at 130 true and 7.5 gph. I remember that specifically as 130 kts is 150 MPH, and divided by 7.5 is 20 MPG, which is the fuel mileage my C-140 gets with its C-85 burning 5 GPH but only traveling at 100 MPH. Mooney is efficient, but can’t be that efficient. I probably had a little tailwind to get the 130 kts, I didn’t look at it very hard. ‘But I’m interested in that software Oh, and after Retirement I worked at the Test Activity as a contract test pilot, that was when we would cruise around looking at personnel in the boats etc, believe it or not but a favorite place to cruise below the tree tops down the river was called the Pee river. Thwt was its name, honestly.
-
Your partially correct, within limits. for example you wouldn’t want to run a motor at 30” manifold pressure and 2000 RPM, nor would you want to run one at 15” and 2700 RPM. If you want to run one hard, it’s your airplane and as long as y9u stay within published limits, it ought to make TBO. ‘There are times when I want to go fast too, but there are times that to use a phrase we had in the military just OFO, Out **** Off, and since your flying just for the fun of flying and don’t have a destination, why hurry? Thst was the point of this thread, what power settings do those who are just OFO run, and why? The guy who posted the 120 kts came in my opinion the closest to answering the original question, and backed up his answer with logic, an explanation of where 120 kts came from. So I think next time I’m out just goofing off, I’ll likely pull it lean of peak and set a power to get 120 kts.
-
That would be what I’m looking for, be nice to have a cheat sheet. ‘Who was they?
-
Volumetric efficiency of greater than 100% is common in high performance engines, usually at full throttle and at the specific RPM that the exhaust and intake are tuned for, exhaust wise you have the restriction of the exhaust to occur just before the exhaust pulse goes though and as the exhaust valve opens, that makes the pressure in the exhaust be below atmospheric and the exhaust is sucked out of the cylinder. ‘On the intake side you design the intake so that the inertia of the gasses in the intake will have a higher than atmospheric pressure before the intake valve opens, so your pushing air into the intake and sucking it out of the exhaust and you have greater than 100% efficiency, but only at a narrow RPM range and usually only at full throttle, partial throttle’s purpose is to block incoming air. Race motors have exceeded 100% for decades https://forums.autosport.com/topic/94318-more-than-100-volumetric-efficiency-on-a-na-motor/
-
985 is supercharged just like the 1340, due to this neither should have any reversion, as they are under boost. Its the supercharger more than anything that gives very even fuel mixture, that and the fact the intake is under pressure. Reversion is what that back flow is called, to see and feel it take the air filter off of just about any small motor and hold your hand behind the carburetor, you’ll feel the pulse and most likely your hand will be wet with fuel You have valve overlap to take advantage of the inertia of the gasses flowing though the engine, a well designed normally aspirated engine will exceed 100% volumetric efficiency when operated at optimum load and RPM. ‘However as the exhaust in aircraft is the responsibility of the airframe manufacturer, it’s pretty common for them to be pretty poorly designed as far as tuning is concerned.
-
Corrosion Behind Foam Replacement Insulation
A64Pilot replied to AerostarDriver's topic in General Mooney Talk
take some of the removed foam, put it in water and squeeze it, if it absorbs the water like a sponge it’s open cell foam, and that’s possibly what caused the problem. ‘I’ve not seen the Mooney foam but hope it’s closed cell -
Glareshield instrument removal for M20J
A64Pilot replied to SPEEDMOONEY's topic in General Mooney Talk
I’m going out on a limb and assume English isn’t a first language, and this may be a Google translation or something. I believe he’s looking for a removed instrument panel glareshield. -
The momentum transfer is huge and very efficient. An example of that is the engines that will shut down cylinders when the power isn’t needed, it’s very efficient, they shut down the valve train to eliminate pumping losses
-
Not really, almost all spark ignition engines are indirectly injected, that is to say the fuel is usually injected onto the back of the intake valve and waits for the engine to inhale it. Until very recently ver few spark ignition engines were direct injection,which means the fuel is directly injected into the combustion chamber, Mazda is coming out with a direct injected gasoline motor which is very similar to a Diesel, just burns gasoline. It’s sort of a hybrid spark / Diesel engine https://www.extremetech.com/extreme/253842-mazdas-2019-efficiency-breakthrough-diesel-engine-runs-gasoline injecting to the back side of the intake valve does several things, it cools the valve for one, but more importantly it means you can continuously inject fuel and let the engine “inhale” it when it’s ready to do so. ‘A very major reason why Diesels are relatively low RPM motors is that you have to time fuel injection to when it’s time for combustion to occur, which is a very small amount of time, and until very recently with common rail the injection pressure to shorten the time interval required with higher RPM just wasn’t possible, Common rail runs such high pressures that its enabled all kinds of new possibilities with Diesels like multiple injection events and variable timing etc, well pressure and electronic injectors of course. ‘We aren’t carbureted because we have dry intakes, and carbureted motors don’t. ‘Now if we were Throttle body injection, then we’ll that’s pretty much a carburetor in a way, but we aren’t.
-
I have the same and when finances allow I’ll install a monitor, but a very valid argument is that my airplane has been flying around for 40 years without one, and it’s original engine made TBO. ‘So just how essential is a monitor? I’m an engine guy, and I like having the info available, so I’ll install one, but readily concede that an engine can be operated well and safely without one.
-
Honestly it appears that my IO-360 Lycoming will run smoothly LOP until the power is just so low that it’s just not logical to cruise that way, without Gami’s. ‘I’ve had Gami’s on two air-lane previously, a C-210 with IO-520 and my Maule with an IO-540. ‘I think Continentals combustion chamber design will allow LOP and still produce good power, and Lycoming’s is less tolerant as in power drops off more quickly LOP. Neither engine is bad and neither is superior, they are very similar, but are different. My IO-360 is a field overhaul, by someone who has a good reputation with the locals and advertises he balances within 1 gm, he may be CC’ing combustion chambers too, I don’t know, or just as likely my engine just got lucky and the fuel flows happen to match up with each cylinder by luck?
-
Cylinder wear isn’t really so much a function temp as Heads are, cylinders don’t really get that hot, because combustion doesn’t occur there and mostly because hot gases are not expelled through the cylinder, but through the head. That is why GM in the 90’s finally began to “reverse” coolant flow through their engines and put the coolest water into the heads first and then onto the cylinders. previously the coolant flow was from the bottom up, because way back in the day engines didn’t have water pumps and were cooled by thermal siphon, which simply means heat rises. ‘But we don’t monitor cylinder temps because it’s simply not a issue, we monitor cylinder head temps because it is
-
They chart is useful, even though it only is at one operating condition, it does show HP outputs relation to mixture etc. ‘But another thing, you can’t really “balance” injectors as individual cylinders are not balanced, they have different sized combustion chambers resulting in different compression ratios and even the piston are not identical. rods different length etc. ‘A lean burn engine is nothing new either, Chrysler and I believe Honda did it in the 70’s but abandoned it due to emission problems it presents, the Current Suzuki outboards use lean burn at certain RPM’s when possible, it’s not at lower RPM as the engine woud run rough and at high power y9u can’t be lean or you’ll put holes in your pistons, but at mid power levels the Suzuki will go very lean and sip fuel. Absolutely
-
No, fuel flow does matter, it matters a whole lot. What shoud be considered is that throttling by fuel flow is nothing new, Long time ago a guy named Rudolph Diesel developed an engine that was entirely throttled by fuel flow, it operates at all times without a throttle valve regulating air flow, it never has a vacuum in its intake manifold, it’s if you will the ultimate LOP engine. It also demonstrates rather well that fuel flow does matter, as fuel flow is the way that power production is regulated. One thing people lose sight of is that these engines are heat engines, that is the motive force is derived by the rapid expansion of air from heating, it’s not an explosion or anything else, it’s no different than a turbine in that respect, and just like a turbine the max power output is pretty much determined by how much heat the engine can handle. ‘So within limits increasing the amount of air that’s available to expand by heat will increase efficiency, but the heat has ti there to expand the air, and of course the heat comes from fuel flow.. A turbo is a pure heat driven turbine, and what makes a turbo “happy” is lower temps, and 25 LOP is hotter than 50 ROP, by 25 degrees of course. Replace those numbers with any others you want to, a turbo only know temps, it doesn’t care LOP or ROP. ‘Cylinder head temps follow power production, they are cooler at LOP because power is down, not because there is any “excess” air available to cool the heads.
-
What they don’t say is that LOP is simply another way of reducing power, you see identical results by decreasing manifold pressure once LOP. ‘What they also don’t say also is that there is an efficiency peak, they seem to indicate that the leaner, the more efficient. ‘I don’t want this to turn into a LOP discussion, if you want to operate deep LOP that’s fine. My experience with it is at the altitudes I travel at that it just doesn't make enough power
-
Higher RPM is not just more distance travelled, it’s mostly the kinetic energy that has to be dealt with as reciprocating mass comes to a complete stop and rapidly accelerates in the opposite direction., those forces are transmitted through the bearings of course. The rotating mass, crankshaft etc has essentially no max RPM, or said another way its actual limit is well in excess of the reciprocating parts. The upper RPM limit of a race motor is set by piston speed, the piston is the weak limit. From a TBO perspective, an engine is designed to be run at max allowable continuous power until TBO, it’s if you wanting to go beyond TBO, or if at TBO your not wanting to buy a bunch of parts is where part power comes in. My 540 at overhaul all the hard parts met new limits so I didn’t turn the crank or have to buy one, largely because it was a 235 and had a redline RPM of 2400. Lycoming has stated in print that motors run at or below 65% power will last longer
-
Fuel flow is missing as well as actual EGT, now I know EGT will change based on location but the delta won’t. as well as fuel flow differences, they ought to be the same. ‘For that matter, where do the numbers in red come from? Lycoming? or did someone else put them there? Not arguing their accuracy, just thinking that they ought to be in the chart for the chart to meaningful. Of course that’s why they were added wasn’t it? ‘This chart to me is meant to be representative, meant to illustrate something. What I’d like is a performance planning chart, one with numbers. If correct it does seem to indicate that the efficiency peak is at -20F LOP and that by running even lower LOP is less efficient doesn’t it? Assuming the numbers in Red are real and correct of course, but either way it shows a efficiency peak, which is not what you usually hear from LOP converts, they often say the leaner the better
-
Unfortunately Lycoming chose to not put numbers on that chart, rendering it pretty much useless
-
Now, I’ve not worked on Mooney’s before so this is a general aircraft statement. But there should be a battery power wire already in the aircraft as electric clocks are common, and if memory serves correctly this wire is required by FAR to have within 1 foot of the battery to have a circuit protection device, most often a simple cartridge fuse. Nothing else that I’m aware of should remain “hot” with the master off. However I concede that I’m used to working on older type aircraft and these modern glass displays may have a keep alive power similar to a clock, but would expect them to still be fused within one foot of the battery if they were.