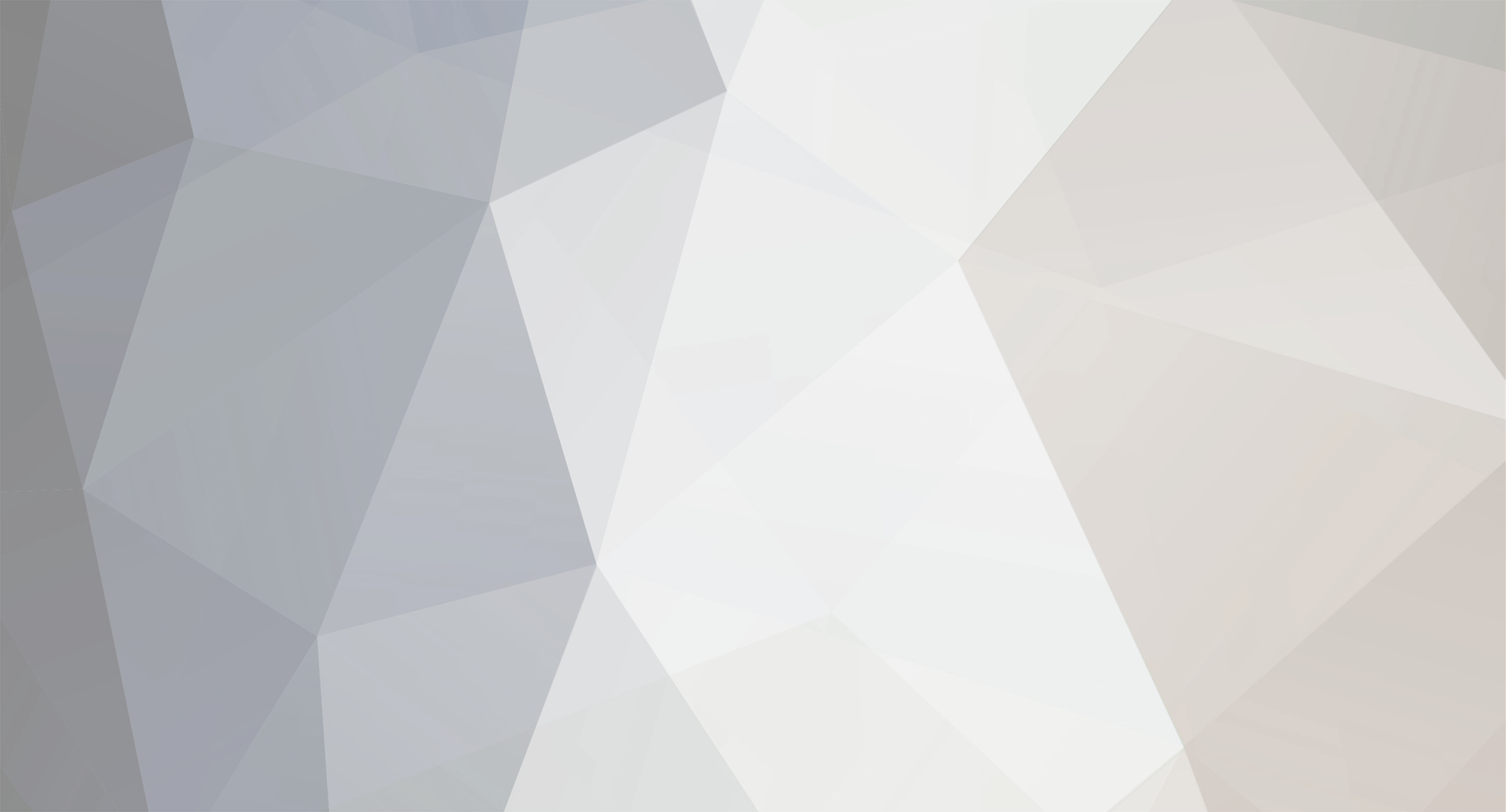
1980Mooney
Basic Member-
Posts
3,366 -
Joined
-
Last visited
-
Days Won
6
Content Type
Profiles
Forums
Blogs
Gallery
Downloads
Media Demo
Events
Everything posted by 1980Mooney
-
Seeing as how problems during the landing phase appear to be the biggest source of incidents and accidents for Mooney's, one would think that it should be the leading topic of discussion. Instead it seems to morally offend some owners to even mention it. It is very hard to know the actual rate of gear-ups, gear collapses, bounces which porpoise into strikes, overshoots of TDZ or runway excursions that result in damage. Many are not reported publicly. In order to discuss a solution one needs to know the rate at which it occurs and all the factors influencing it. If one finds it emotionally troubling to discuss the facts and circumstances contributing these landing phase incidents and accidents, then just stop reading about Safety and Accidents. Given that the 4 lead topics in in the "Mooney Safety and Accident Discussion" have not been updated in 6-7 years, it is clear that the entire discussion is not very popular and that many prefer a "head in the sand" attitude.
-
One cylinder hotter than the others, should I worry?
1980Mooney replied to AndreiC's topic in General Mooney Talk
You never mentioned exhaust temperatures. Do you have an engine monitor that measures exhaust temperatures on each cylinder? If so is #2 in line with the others? -
I think you are right. It is hard to find real world weights of full engines with accessories. Nothing official from Mooney or Lycoming that I can find. Some have posted anywhere from 540 to 590 lbs. dry. Compared to @snowman ‘s current IO-360-A1A, the Bravo upgrade adds 2 cylinders, turbo,intercooler, and TKS will require a second alternator. It will have a heavier engine mount/frame, heavier cowl and a possibly heavier prop (his F shows a 3 blade) hung father out. And although not specifically engine weight, that engine adds about 6-21 lbs of Charlie weights in the tail for CG.
-
It is not just the extra cost to maintain the single turbo charger, it is just a very expensive engine. And heavy engine (702 lbs). Useful Load for a TKS equiped Bravo is 840 lbs. per Sept, 1996 Flying Magazine test flight of the then newly introduced TLS Bravo. With full fuel (534 lbs.) that leaves only 306 lbs. payload for passengers, crap on the hat rack and luggage. Just make sure to sell it before it needs major engine work.....
-
This may help. It shows serial number range by model by year. Mooney Model Chronology (mooneyevents.com)
-
It is possible to stay in business building parts for shrinking fleets. Like True Flight Tiger AA-5. But to do it you have to shrink or "right size" for that business. You can't continue to carry the overhead, insurance, legal liability, management of a company that thinks it is still a manufacturer of aircraft. Commander Aircraft was trying to do it for the 112/114 fleet, but they have now failed completely. About | True Flight Aerospace
-
Apparently, you missed this. Key Points: "We currently enjoy good margins manufacturing parts for several other aircraft companies: our main challenge is scaling up." 35 employees "I believe the future lies in composite technology, which allows for rapid production in molds" "Our plan includes refining existing models to build more efficiently and increase their useful load." Interestingly blames the Trump Administration trade wars for the inability of Soaring America (subsidiary of Meijing Group) to continue funding the business resulting in shut down of aircraft manufacturing. That means that Mooney remained a negative cashflow sinkhole with every Ultra that they built.
-
Except Mooney hasn't put a Lycoming in a Mooney in nearly 2 decades. The last Lycoming 4 was installed in the Mooney factory in 1998 and the last Lycoming 6 was installed in 2007. The Lycoming backlog at Vans is because those are non-certified low cost engines. It makes sense that Lycoming would give priority to their higher priced certified engine customers. I don't think that there is a 2 year backlog of Continentals.
-
That is a great looking M20J. Resist any thought or comments from anyone here saying "never to early to start thinking about or saving for upgrades". Just learn to fly it, learn more about it, improve your proficiency and enjoy it for now. I also bought a used M20J long ago while working on my PPL. I finished the PPL with the flight school Cessna 172 while flying the Mooney with a Mooney instructor at the same time. Also start working on your Instrument as soon as time, money and life's interruptions permit. It is still on Trade-A-Plane. It looks nicely equipped. I see from the pics that it has Rosen visors.
-
Agreed - good comparisons are hard to come by. But results of the bottom line "acid test" are clear - (does more money come in than goes out) In mid 2001, when Mooney was building about 100 long-bodies per year supposedly efficiently (per VP. Ops Valencia article above) they failed the "acid test" and went bankrupt In late 2019, when Mooney had been building 10-14 long-bodies per year, (inefficiently per comments from Pollack) they ceased all production, laid off 229 employees, including all employees on the aircraft production and parts lines because they were failing the "acid test" and needed to stop the negative cash flow.
-
Think about it another way. Take a Cirrus SR22T vs. an Acclaim Ultra or a SR22 vs and Ovation Ultra If Mooney were building in volume and could get the same volume purchasing discounts as Cirrus what costs are the same and what are different. Same: Continental 550's Hartzell Props Garmin Avionics Tires - Goodyear? Maybe the cost/time to make a modern interior Different: Fixed gear on Cirrus (lower cost) vs Mooney retract (Eaton actuator high cost, etc) Parachute system (CAPS) on Cirrus Composite construction man-hours at Cirrus vs Steel welding, Aluminum fab/riveting manhours at Mooney. I suspect that the man-hours to build a composite Cirrus is much, much less than a Mooney.
-
Good numbers are hard to come by. In 1977 there was less complexity - 24 of those were short body C's, the rest mid-bodies, the cheap Royalite interiors, no turbos, 4 cylinders only, no rudder trim, etc. Now the article above notes that it was taking 4,300 hours to build a Mooney. Valencia claims that they got it down to 2,900 but we know for a fact that merely 17 months after that article, Mooney filed for bankruptcy in July, 2001. So either those "savings" were not real or they were losing lots of money elsewhere. In 2022 at MooneyMax, Jonny Pollack said it took 9,000 hours to build a Mooney. I suppose it is possible that he doesn't really know what is going on at Mooney. He also said that direct costs (ie Cost of Goods Sold) eat up 85% of revenue leaving only 15% gross margin (contribution) to cover all the fixed costs (legal, management, engineering, accounting, insurance, etc). That won't cover the costs. Healthy manufacturing companies usually have gross margins of 33-50%. In 2020, when interviewed Pollack said it takes 1,800-2,000 man-hours alone to build a wing. https://aviationweek.com/business-aviation/aircraft-propulsion/sounding-board-five-minutes-mooney-international-ceo-jonny
-
First of all Mooney was not just operating at a "book loss", it was hemorrhaging cash losses. We don't know the details but we know the Mejing Group invested a lot of cash (rumored to be $150-200 million) and got nothing back but losses. At the meager rate that they were building Ultra's, they were not getting volume pricing and were probably paying Continental, Hartzell and Garmin $350,000 cash per Acclaim for full powerplant and avionics. They probably had to pay another $100,000 for all the materials, bits and pieces that Mooney does not make (Eaton was sticking them at least $15,000 - maybe $20,000 - for just a single new landing gear actuator.) So Mooney is already out $450,000 in cash costs per plane. Now add direct manufacturing labor and variable manufacturing overhead which are real cash costs. Jonny commented once that the wings alone were taking 3,000 manhours. If a plane could be built in 5,500 manhours (direct including painting and testing) [FYI -Jonny once mentioned 9,000 manhours per plane] and let's assume that they were paying a measly $30/hour (add 20% for vacation, medical, benefits so that costs Mooney $36/hour in real variable direct costs) then labor adds another approx. $200,000 - maybe more. So now cash costs are at least $650,000. Now Mooney's are not just going to sell themselves (regardless how passionate we are in our thinking). This is not a case of people lined up and the Factory are just order takers like at McDonalds. The planes have to marketed with a sales organization. Regardless of factory or dealer sales/marketing structure, it costs more cash per plane before it is sold. Another $50,000 - 75,000/per plane? Maybe. Now costs total $700,000-725,000 and that is variable cash cost/outlay. So might Mooney receive $70,000 - 95,000 in cash contribution to go towards paying the fixed cash costs like Legal, insurance policies, building rent on main buildings, inventory and property taxes (Texas has one of the highest business property taxes in the nation), management salaries and benefits, etc. Might it cover? At 2018 sales rates - absolutely NOT. They were losing cash. At your "30/month" case?. Possible . But then there is the amortization of investment "book" costs - all the investments in building, tools, Ultra engineering, etc. Will it cover the historical investment costs? Doesn't sound likely. But your "case" is nonsensical. 30/month. That is like saying if Piper could have still sold 30 Saratoga's per month, or Commander sell 30 114's/month or American sell 30 Tigers per month - would they all be profitable and still actively built? First, for Mooney to ramp up production by a factor of 20, with that many manhours/plane, Mooney would need about 1,000 direct workers in manufacturing. That demand would probably drive up wages in Kerrville and materially raise costs. But more importantly there is no demand for 30 Ultras/month. Just like there is no demand for 30 Bonanza's/month. Unlike Mooney, Textron can still build them if when there is demand. But for Mooney or the Bonanza to jump to 30/month demand, it would take a complete redesign and as said a marketing/price war to steal a major share of customers away from Cirrus and Diamond. And that takes a huge investment which in turn saddles the new plane with heavy amortized costs. So you are back to more losses. And no return on your investment. We just need a billionaire that buys into the vision and doesn't really care about losing his wealth.
-
Bringing in a Mooney from outside the U.S.
1980Mooney replied to Zorro's topic in General Mooney Talk
That is the most common. Plenty of discussion and examples. https://www.fnlpilots.org/blog/2021/02/imported-from-canada/ https://www.pilotsofamerica.com/community/threads/buying-a-plane-from-canada-and-delivering-to-the-us.125234/ -
Bringing in a Mooney from outside the U.S.
1980Mooney replied to Zorro's topic in General Mooney Talk
-
Bringing in a Mooney from outside the U.S.
1980Mooney replied to Zorro's topic in General Mooney Talk
Import it from what country? Don’t forget that it was originally exported from the US. For instance there are many posts on importing from Canada. -
Knisley Welding is family owned since 1974 and remains independent (for now). I suspect that they are on Arcline’s/Hartzell’s shopping list - just waiting for an heir that wants to cash out. https://knisleyexhaust.com
-
A lot has changed in the last 7 years. Hartzell bought AWI in Jan 2020 (AWI had already bought Kosola and Associates in Albany, GA back in 2013). In Jan 2021, Hartzell bought Dawley - they shut Dawley down, laid everyone off, moved equipment and consolidated in AWI Minneapolis. In July 2022, they acquired Acorn Welding in Canada. And late last year the venture capital, Arcline Investment Management, bought Hartzell. They have been raising prices across the entire Hartzell product line to get a return for their investors ( including Janitrol Aero, Fuelcraft, Plane-Power, Powerup ignition, Kelly Aero, Sky-Tec and AeroForce Turbocharger Systems- and they just bought Cleveland Wheel and Brake a couple months ago)There is a lot less competition now. It’s all just Hartzell Aerospace Welding now in reality. The notion that they compete against one another is a joke. https://hartzellaerospacewelding.com
-
Are you in a hangar?
-
@LANCECASPER is right. The 280 hp STC is still ultimately owned by Bob Minnis. It was first in the name of Minnis Aviation LLC. Then it was in the name of PowerLite LLC. In 2019 PowerLite LLC was changed to AvPower LLC. They are all Minnis. You will see documents in all the names. STC Number: SA02988AT You will need a Hartzell PHC-J3YF-1RF/F7693DF(B) which is the standard 3 blade prop on Cirrus SR-22 and SR-22T. You should be able to find a used or overhauled one easily.