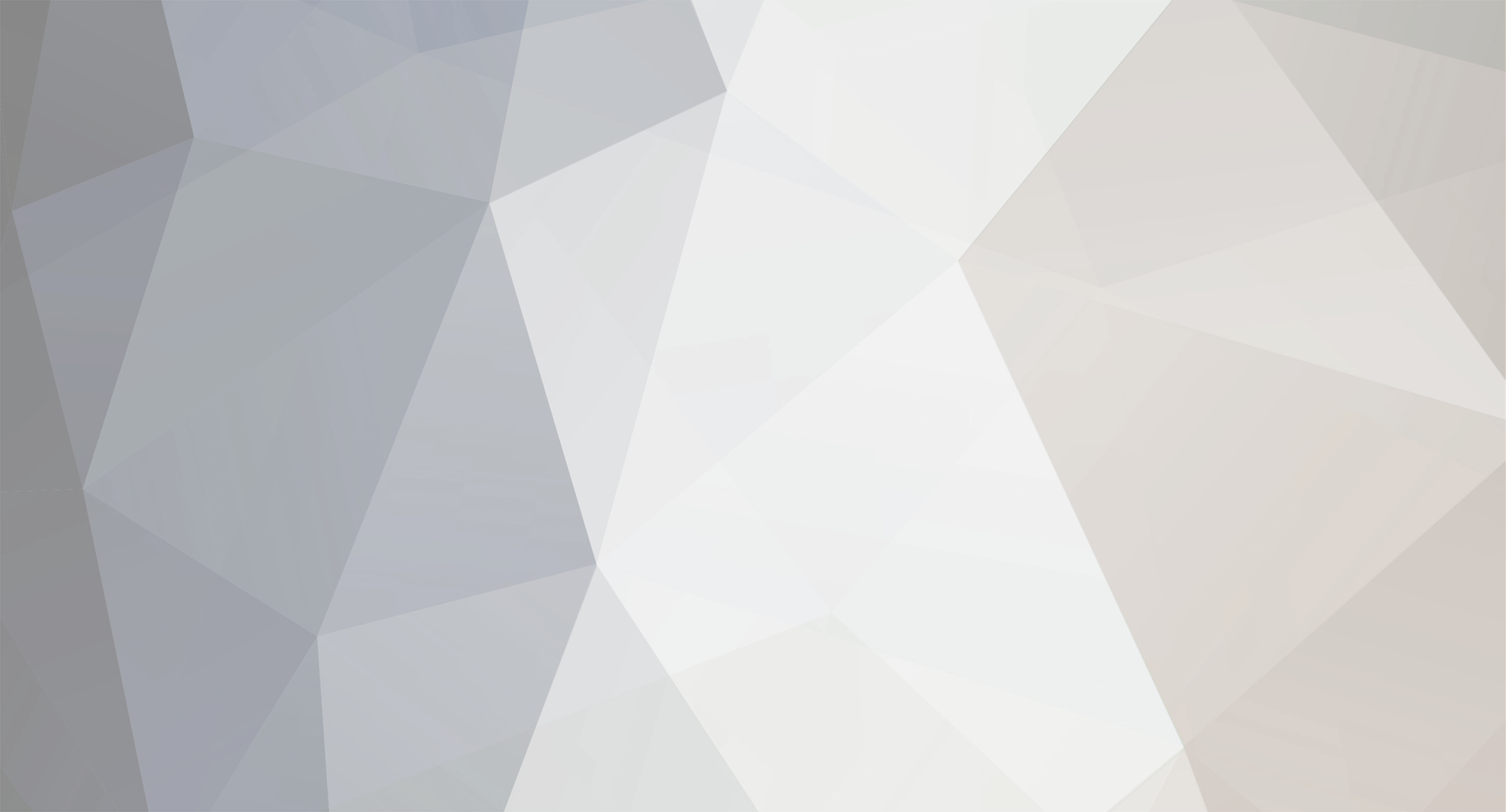
bcg
Supporter-
Posts
698 -
Joined
-
Last visited
-
Days Won
4
Content Type
Profiles
Forums
Blogs
Gallery
Downloads
Media Demo
Events
Everything posted by bcg
-
You went big, that's awesome. I've mentioned before that I bought a C with 20 hours in my logbook, finished private in it and went straight into instrument. 18 months later and I've got almost 300 hours in that C and several 1,000+ mile XCs, including a trip to OSH. It's been a fantastic first plane for me and it was a lot less expensive than a traditional trainer. Mine was flying about 100 hours a year with the previous owner, I still ended up having to do the starter, battery, generator to alternator conversion (generator failed), an ignition switch (which wasn't a big deal except that it's $800 for the part), overhaul the exhaust and I had a stuck valve that bent a push rod and required a cylinder replacement. All of that added up to about $10,000 in parts and I did most of the work myself, under supervision. I also did some avionics work, first replacing a failed KLN90B GPS with a Garmin GPS 175 and then redoing the panel completely at annual, which was another $23,000 or so in parts, again with me doing most of the work under supervision. The avionics at annual was just supposed to be adding an EDM930 but, I got caught up in scope creep and it kind of got away from me. I'm really happy with the outcome though, it's been a joy to fly behind the new panel. I also had an IRAN done on the prop at annual time, mostly because it needed to be repainted and the shops doing the eddy current inspection were starting to complain about it not being airworthy because of the lack of paint. Anyway, like you, I say if you want the plane and can afford it, get it. Just be realistic about planning for first year expenses, mine was well cared for but, it's still a 60 year old airplane with 6600 TTAF and 1800 SMOH, stuff is going to break and none of mine was predictable or preventable, other than the bent rod. I didn't recognize that the morning sickness I was experiencing was probably a stuck valve and didn't get on that as quickly as I should have, I'd like to think that with the knowledge I've gained and the logs from the EDM I would catch that early enough to just ream the valve guides instead of bending a push rod and having to replace the cylinder if it happened again. If I didn't have such a great shop on my field that was willing to let me work under supervision, my expenses would probably have been 2-3x what they were with labor added. I'm not going to count the value of my time in the costs because honestly, I don't want an accurate total...lol
-
Edit - battery adapter showed up today, adding a pic of that. V3 The biggest issues with the last version were that the drive wheel was outside the center of the nose wheel where it wanted to pull the tow bar out when you started putting tension on it and trying to turn. The other problem was that to get enough pressure to have good contact, you'd end up so low you couldn't see where you were going. To solve that, I built a new tow bar from scratch that has the part that goes into the nose gear offset so I could move the drive wheel over and I put a bend in the top part. I still made this a 2 piece tow bar so it can be broken down for easy storage in the plane. I think I'm going to put a quick connect on the motor cable so that the 2 parts can completely separate. Milwaukee battery adapter is supposed to be here tomorrow, I'm going to wait on that to finish this and test it out. I expect this one to work the way I'd hoped the last one would and only take up a little more space. Sent from my Pixel 6a using Tapatalk
-
Let me get the rest of the kinks worked out first and then I'll share what I did and used.
-
It worked, got the plane in and out but, not well enough that I'd have been happy if I paid for it. Using an already made tow bar won't let me put the drive tire where I really need it to be for this to work really well so I'm going to build one from scratch exactly how it needs to be. It was nice to not be worn out and winded after getting the plane in the hangar though, especially since it was raining off and on and everything was wet. And, I got a couple of approaches and a hold done today in actual with 700' ceilings so that was nice. Sent from my Pixel 6a using Tapatalk
-
Let the games begin - MAJOR Avionics Upgrade.
bcg replied to Pinecone's topic in Avionics/Panel Discussion
I'm sure they have a way of doing the labels already. When I did mine though, I powder coated the panel with a layer of white, partially baked it, coated it again with black, fully baked it and then used the laser to burn the black off and reveal the white for my labels. It came out really clean and was, for me anyway, a lot faster than trying to color fill them. I also did it as 2 pieces, the tan comes out separate from the black so I can remove and replace the panel without having to remove the yokes or pull the TPM cables from the engine. Look forward to seeing your finished panel, I wish I could have done something more like what you're doing. Mine was a huge upgrade for me though and I'd like to replace the C with a 252 or Bravo in the future so I just couldn't justify the cost. -
V 2, minus the Milwaukee battery adapter that won't be here until Sat. /// Side rant, Amazon Prime sure has gotten slow lately, it's ridiculous. /// Assuming this works the way I expect, I'll pull the motor and tire off, strip the rest of the paint and powder coat it so it'll be pretty. Sent from my Pixel 6a using Tapatalk
-
Now that I have the wheel location nailed down, I should be able to safely mount the motor more permanently. I took a piece of 2" x 6" 1/8 plate and put a couple of slotted holes in it to allow adjustment of the motor to take the chain on it off and tighten it. Welded that to the tow bar and I'll bolt the motor onto it. Welding it on put a couple of bumps inside the tube so the smaller piece won't slide down anymore, which kind of sucks but, I'll be able to just pull it out and have 2 small pieces which will make this easier to keep in the plane so I can take it with me. I'm liking how this is coming together now, I think it's going to be really functional and as lightweight/portable as something like this can be. Sent from my Pixel 6a using Tapatalk
-
I think I'm going to move the wheel forward another 3/4" and it'll be good. It kind of rides on the side/top of the nose wheel but, that gives more surface area for contact so it should work well. Now that I know where the tire needs to go, I can put all the other stuff back on. Sent from my Pixel 6a using Tapatalk
-
Respectfully, if you have both green and magenta needles and your G5 is driving a non-Garmin AP, your installation isn't by the book. I'm glad you have someone looking at it, when you get it back you should have either a green or magenta needle only, not both. I'd want magenta so I could get GPSS steering and RNAV approaches via the AP. Look at pages 23, 179 and 154-157 in this doc, your answers are there. https://static.garmin.com/pumac/190-01112-10_28.pdf. I didn't like the answer when I did mine either, had I known going into it I would probably have gotten a GTN650 instead of the 175 and SL30, it wouldn't have been that much more. Unfortunately, I figured this out after I already had everything in hand and was into the install so, I made the best of it. Good luck, I hope they get it worked out for you. Sent from my Pixel 6a using Tapatalk
-
If you have both green and magenta needles, then someone connected 2 nav sources to that G5. I'm going to guess that the software got updated at some point (there should be a log book entry for that) and either at the same time or later, the GPS 175 was installed and connected to the G5, contrary to the instructions. When you update the software, you need to install according the manual that's valid for that software so the Rev A manual is superseded by the software upgrade to whatever revision of the manual corresponds with the software installed. You're in Portugal? I don't know the rules there however, in the US, your installation isn't legal since it doesn't comply with the STC. It's not going to crash the airplane but, it's technically not airworthy in this configuration. I missed that you had 2 NAV radios earlier, with that clarification, your panel should consist of the G5 HSI and 2 additional CDIs so that each NAV source has it's own instrument. Here is what I would suggest doing to get your system working with the most utility. I would remove the NAV radio that is currently connected to the G5, make sure the GPS 175, GAD29, G5 are all wired correctly, reconfigure the software for that setup and put in another CDI for the NAV radio. Alternatively, you could leave both nav sources on the G5, disconnect the AP from the G5 and use the NAV radio that's currently going to the stand alone CDI to drive the AP. This would give you the same functionality you have currently in a way that complies with the STC. You can have 2 nav sources on the G5 if it's either connected to a Garmin AP or not connected to a non-Garmin AP. This isn't really a DIY job unless you've got Portugal's equivalent of a friendly A&P/IA to look over your shoulder and sign off on the work. The one thing that I'm confused by though, is that you're saying the GPS RNAV approach shows up on the G5 in a green needle. This should not be the case, all GPS guidance should be magenta so, if that is indeed what's happening, this definitely needs to be looked at by someone qualified because something is definitely wrong. In the case that GPS guidance is truly showing up in green, disregard the rest of what I said and take it to an avionics shop for proper troubleshooting, it's likely going to need to be pretty in depth to figure this out. Definitely more than we can do over the Internet.
-
Maybe, it depends. Here's how it would work. 175 connected to GAD29B/D vai AIRNC 429 and the G5 via RS 232. GAD29B/D connected to G5 via AIRNC 429. NAV radio connected to the standalone CDI. Then the AP will be driven by the GPS and you'll have GPSS routing and would not be able to track a VOR or LOC with the AP. What is the CDI you have installed connected to right now? Is it giving RNAV approach guidance? Do you have both a green and magenta arrow on the G5 HSI or only green? If I knew this, I could better answer the question.
-
I just realized you're at RDB. My dad is in Dallas and I fly into RDB once or twice a month to see him. Next time I'm up, you should join us for lunch.
-
Awesome, thank you! I found one for the Milwaukee M18 batteries, since my tools are all Milwaukee and I've already got a bunch of those batteries and chargers I'm going to go that route. That'll take up a lot less space than the battery I was using and make this a whole lot more portable. The C is easy to push around on a flattish surface, the little bit of uphill, door tracks and concrete lip going into the hangar are tough to do alone though. I have to get a running start so the momentum carries the plane in but, doing that I can't steer, or watch where it's going really. I don't want to run into a wall and it's inevitable that I will eventually if I keep doing it the way I have been.
-
What is that CDI connected to? The early G5s only had the ability to connect to a single navigator, period. If you've got one of those, the limitation won't be there because connecting to 2 navigators was impossible at the time. Sent from my Pixel 6a using Tapatalk
-
With a non-Garmin AP, the only way to track a LOC in the G5 is to have a combo navigator like a GTN or Avidyne IFD. It's a limitation. I put a 2nd G5 and SL30 in my plane thinking I could connect them both to the G5 and discovered that wasn't the case so I had to retain my Collins CDI for the SL30 and only connect the 175 to the G5. Search Google for the doc I posted to answer the limitations question above, that's the G5 installation manual. Towards the end of the document are instructions on exactly how the settings should be in the GPS 175 and G5 for different APs. You just need to go through your config and make sure that's what was done. In order to get this functioning correctly, you're probably going to have to install a separate CDI for the NAV radio. The G5 doesn't know what it's supposed to be tracking without the Garmin AP, they have it setup so that all that magic happens in the GFC500, not the G5. Unless you're comfortable with redoing wiring, you're going to end up having to take this to someone to do it for you. Even if you can do the work yourself, you're going to need an IA to sign it off for you. It's not really complicated if you're technically savvy, you've just got to read and understand the installation instructions and have the right tools. The crimper for the pins is several hundred bucks by the time you get the dies and stuff with the less expensive J Ready. If you buy the actual aviation crimper, you're pushing a grand pretty quick. I'm happy to help how I can but, I think in the end you're likely going to have to take it somewhere since you really should have another CDI installed for the install to comply with the STC. Where are you located? If you're close enough, I can look at it and go through things. It's almost impossible to troubleshoot something like this remotely, I'm having to make some assumptions based on what you're describing and they could be entirely incorrect. Lots of possibilities as to how things can be connected and installed. It might even be something as simple as a bad connection somewhere, although that doesn't sound likely based on what you have said. Sent from my Pixel 6a using Tapatalk
-
That sanding disc is an interesting idea. The direct drive definitely makes it more compact and I like the way the battery is setup. What did you use for the battery holder?
-
I hadn't seen the photos, I'll look at your gallery now. Thanks for the offer, if I run into something I can't work out I'll get in touch.
-
I'm actually still working mine out. I've had to move the tire, my math had errors. I'm on V 3 now, going to try it tomorrow and see if I've got it right. Once I know for sure where everything needs to go, I'll weld a mount for the motor into the bar with some adjustment for tightening the chain. This will end up rolling the tire, I think. Getting it to the ground will make it way too big to be easily portable. Sent from my Pixel 6a using Tapatalk
-
It's in the Limitations section. In version 190-01112-10 Rev. 30, that's Page 23, and it's the last line, which says - "cannot interface with dual navigators if G5 is interfaced with a non-Garmin autopilot"
-
I don't know enough about that AP to say for sure but, it's possible that he has both a Heading and a L/R error input, which would in theory allow it to both track a VOR and follow a GPS. The S-Tec 50 in mine has both, I probably have the names wrong because I'm just going by memory here. If there are both green and magenta needles on the HSI though, it's hooked up incorrectly. It might work, I think the Experimental version allows it (again it's been a while since I read the manual so I could be wrong), it's definitely not "legal" on a Certified aircraft installation. I think the answers to his question are probably in the installation manual though, and someone just didn't read them. It took me a couple of weeks to really understand what was and wasn't allowed and how it all needed to interconnect and interact when I added the 2nd G5 and GAD29B to my plane to replace the Icarus SAM GPSS. It's straightforward once you understand it, getting to that point can be a little confusing though.
-
Do you have both the NAV radio and the GPS connected to the G5? If so, that's not correct per the install manual. With a non-Garmin AP, you're only allowed to connect 1 nave source to the G5. If I installed it, I would have put the GPS onto the G5 and kept a separate CDI for the NAV radio. In heading mode, is it following the heading bug on the G5 HSI or the NAV radio CDI/HSI/whatever? Did you follow the install manual for the G5 settings for the AP? Verify those are all correct before going any further. If they are, and the wiring is correct (the GPS is connecting to the GAD29 via ARINC29 and the G5 via RS232), then you should have a GPSS option in the G5 to enable that mode. It kind of sounds to me like someone installed this without reading the manual and a somewhat incomplete understanding of how it should be connected/programmed and what the limitations are with a non-Garmin AP.
-
On the gear ratio, the motor has a reduction gear in it and is meant for electric bikes or scooters (think small electric Vespa, not Razor) so, it should have lots of torque. The tire is probably going to have to come down some or I'm going to need to add an extension for the handle to get the angle right for standing comfortably, or move the wheel over to have it ride on the nose wheel. I'd rather have it on the ground though, it should require less effort to move it that way. Sent from my Pixel 6a using Tapatalk
-
Engineers like "elegant" solutions. Technicians like functional design. I'm a technician... [emoji2] Sent from my Pixel 6a using Tapatalk
-
It is variable speed. The control box has a switch to reverse direction and a dial to control speed. Sent from my Pixel 6a using Tapatalk
-
Yeah, once I get measurements and dimension worked out, I may fabricate something more finished looking and see what it would cost to produce them en masse. There's probably a decent sized market for a $500 powered tow bar, especially if I can make it fold so it's easy to take with you. Sent from my Pixel 6a using Tapatalk