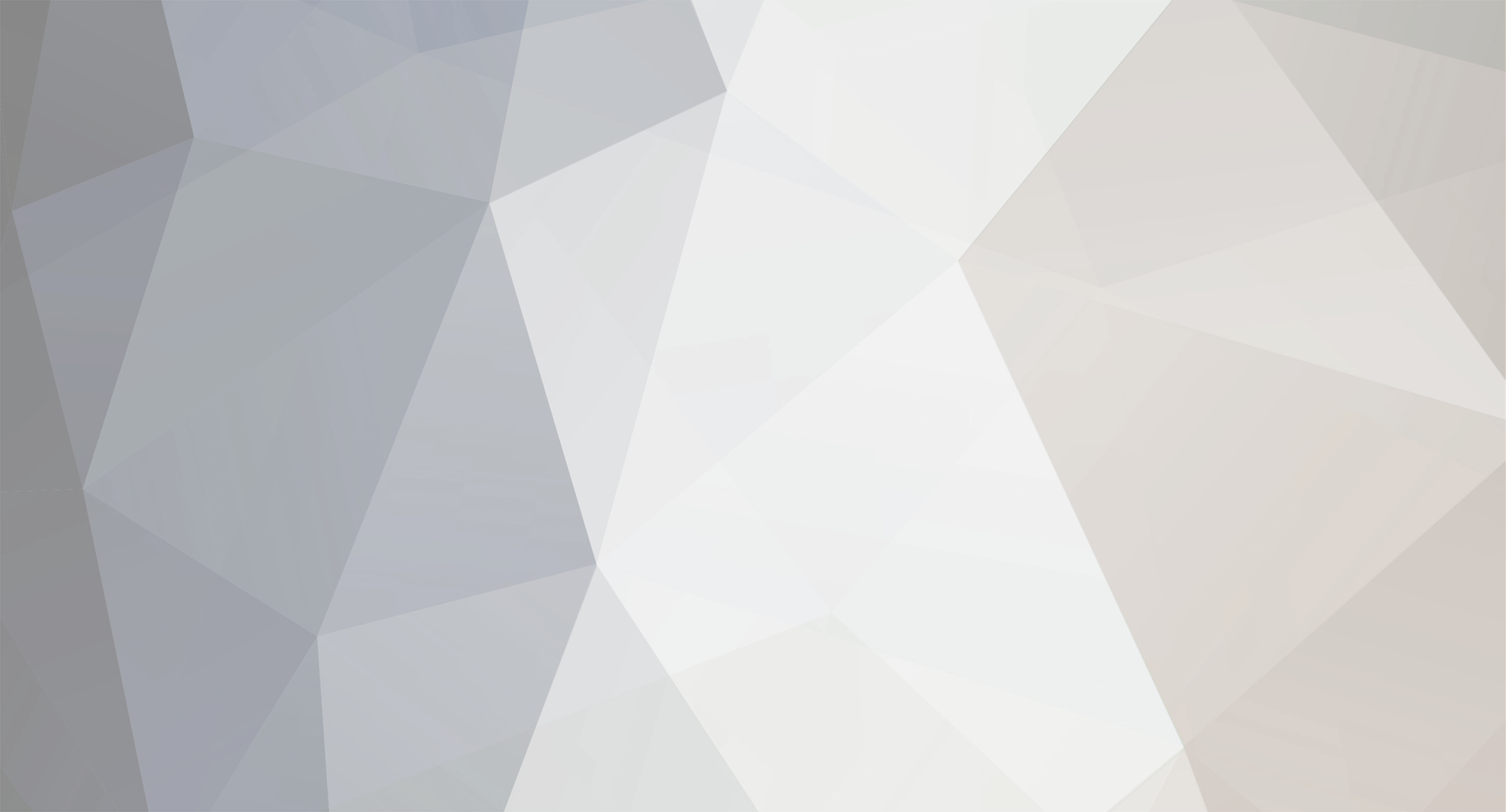
65C_flier
Verified Member-
Posts
54 -
Joined
-
Last visited
Profile Information
-
Gender
Male
-
Model
M20J 1978
Recent Profile Visitors
The recent visitors block is disabled and is not being shown to other users.
65C_flier's Achievements
-
Problem is fixed. It was either the fuel selector or the gascolator. On close inspection there was some slight blue fuel staining on the top of the gascolator bowl (shaw aero 1540-3), so a new o-ring kit was installed. The top of the fuel selector shaft looked pretty worn, but we ended up reinstalling for a ground run after the gascolator o-rings were installed and fuel pressure was good. Next flight, climbed to 8000ft and left the mixture rich. We saw about a 2 needle-width drop (to ~20 PSI), but assumed that was ok given the excessively rich mixture. Performed fine throughout the rest of the flight including go arounds. Noticed a few drops of fuel coming from the sniffle valve drain line (sump breather line) after the flight which I had never noticed before, but I assume that is unrelated and not a problem (normal fuel injector draining?)
-
Thanks Skip. I had similar thoughts about the boost pump being downstream of the suspected leak so it shouldn't help, but the tempest video linked a few times in this post seems to indicate the additional pressure might blow enough through to effectively get the engine pump going (at 11min 35sec). That might also explain why it works for a bit after RPM reduction, but creeps back in. I agree there is still a good chance it is the engine driven pump, i just want to eliminate any easier options first.
-
Yes. Same symptoms.
-
Hi all, I am having a fuel pressure issue with my 78J (IO-360A3B6D) that sounds similar to some of the issues discussed in this thread. I am hoping somebody might have experienced the same symptoms as me and be able to offer some advice before we go pulling too much apart. About 10 flights after my last annual I noticed that my fuel pressure on the ship's gauge during cruise climb with boost pump off was lower than its usual 25PSI (middle-of-the-green). It progressively got worse over the next few flights to the point where it dropped below the green (14 PSI) which really got my attention. Switching the electric boost pump on put the pressure back to around 23PSI. In cruise with boost pump off and leaned, the engine pump held around 23PSI. After some troubleshooting on the ground it was much worse than I thought. I took a video (that I cant figure out how to upload). At full power run-up the fuel pressure drops from 23PSI to about 6PSI and the RPM drops about 100RPM (from 2650 to 2550). Fuel pressure then oscillates between 6-10PSI as the RPM oscillates between 2550-2650 every 5-6 seconds. The boost pump puts the pressure back to 23PSI and stable RPM 2650. I had a look through my JPI data and I can clearly see the exact flight where this started. The graph below is an example from one of the later flights. The fuel flow starts to oscillate every 5-6 sec as soon as the boost pump is switched off. The EGTs follow. FF stabilizes for a few minutes when I reduce RPM for cruise climb, but then it returns. RPM is stable and I don't recall noticing the fuel px gauge oscillating at all during flight, but it is clear from the data that something is very wrong. The engine driven pump was overhauled a few years ago and there is no sign of fuel or oil from the drain line. No fuel stains around the servo or anywhere else. No loose fitting that we could find. My assumption is that air is being sucked in through a gascolator o-rings (which were replaced last annual) or the fuel tank selector. Interested in any advice before we go and pull those apart. I am also worried that the old Airight fuel selector (610289-007) will be difficult to repair or impossible to replace.
-
Might have to give this a try. I've got 2 x 430Ws and the #2 unit has a "LOSS OF SIGNAL" for 1-2 mins about every second flight during climb out. On some occasions I have pulled up the satellite page on both units and watched the #2 unit slowly get signal back for each satellite shown on #1. Very rarely happens more than once on any given flight. It hasn't bothered me too much as the #1 unit is solid and I don't keep the database updated on the #2 unit anyway, but it sounds consistent with a loose antenna connection so it is worth a look.
-
Questions after my first familiarization flight
65C_flier replied to Papa K's topic in Modern Mooney Discussion
You will at least feel the yellow range vibration if it is a 79J with a 2 blade McCauley. I realise that is okay for non-continous use, but I try to avoid the yellow range for as long as practicable (until final). I guess the point is, there is no perfect number that covers all the possible Mooney variations. Know the POH and determine what works best forn your config. -
Questions after my first familiarization flight
65C_flier replied to Papa K's topic in Modern Mooney Discussion
When you get time, you could go out and do some stalls in all landing configs you might use (flap land, takeoff flap and no flap) to validate your POH stall numbers at a high and low weight. Make a chart for 1.3Vso and use that as threshold speed for your specific flap/weight. 100kts (not mph) base and 90 base should usually work. Use the POH procedures for cowl flaps initially until you get time to analyse your specific aircraft behaviour, then adjust from there as other have suggested (easier to monitor it with an engine analyser). Cowl flaps seem quite dependent on the specific aircraft (e.g. condition of your baffling) and obviously DA, climb speed, etc. Recently I have found my OilT and CHT creeping up above my preferred limits on hots days in cruise at 24 squared (or WOT if higher). I might need some new rubber on the baffles and re-rig the cowl flap closed position open a bit more. The engine analyser alert at 400F CHT occasionally reminds me I have forgotten to open the cowl flaps during practice missed approaches on hot days... -
+1. First flight after buying a 78J with Century III I thought the elec trim wasn't working until reading the Century Manual. After figuring out how to use it I decided it was too course and it annoyed me disconnecting the ROLL or HDG modes if I needed to trim. So now I just trim manually and leave the elec trim switch off. AP still works in all modes including ALT hold. Trim switch still disengages all AP modes.
-
First time I declared an emergency…
65C_flier replied to Candy man's topic in Mooney Safety & Accident Discussion
I'd generally be more worried about the liquid juice than the electronic juice and I'd rather get on the ground quicker, so I'd usually keep it up and rely on the manual extension if required. I try to do the manual extension myself every annual and have a generally look at the motor/clutch/spring to add a bit of extra confidence that it is going to work when I need it. -
First time I declared an emergency…
65C_flier replied to Candy man's topic in Mooney Safety & Accident Discussion
Good discussion. I've had a similar problem 2.5hrs into a 5hr flight and decided to head back to the origin where my A&P lived. The most concerning thing for me was having my Aspen EFD1000 detect low voltage and swap to it's internal battery which rapidly depleted from 100% to shutdown in less than 30mins. Made me pretty thankful for the VFR day and standby vacuum powered AI. I hadn't thought of a panel plug to ship's antenna for my hnadheld. Might look onto that. -
I usually takeoff at MTOW (family and full fuel). Doesn't seem to be a problem, but I agree staying at MTOW for the full flight is a penalty, as is stress on the airframe landing at MTOW.
-
Hi all, Has anyone thought much about converting a Mooney to an electric motor? Might be a few years (decades?) away, but it seems like it might be feasible eventually. Some rough math for a J (using metric, sorry but its easier). Interested in whether anyone has thought more about it. 200hp (presumably at the output shaft) = 150kw. Electric motors are around 3x more efficient, but we still need 150kW going to the prop, so a 150kW electric motor is required Weight available: remove IO-360 engine 300lb, 64Gal fuel 384lb = 684lb (310kg). Might scrape together another 10kg in fuel components. Assume 50kg for (a theoretical 90% efficient) 150kW output motor, assume new prop same weight as old prop, 20kg for battery controllers gives 250kg available for batteries Power required for takeoff & climb (5 mins at 100% and 10 mins at 75%) = 31.25 kWh motor output (34.7 kWh battery input for 90% efficient motor) Cruise at 60% power = 90 kWh per hour of cruise (100 kWh input) Current batteries are around 250 Wh/kg or 4kg per kWh. Battery weight required: takeoff/climb 139kg, cruise 400kg/hr. With 250kg to play with that only allows 15 min takeoff/climb and 17 mins cruise (no reserve). Not very useful. Even if you throw another 200kg of batteries on the back seat, you only get 47 min cruise (no reserve). If (when?) batteries improve to 500 Wh/kg, that gets us to 54min cruise (no reserve) or 1.9hr (no reserve) with an extra 200kg of batteries. So it would take more like 2500 Wh/kg to get something comparable to what we have currently got (5.3hrs with 45min reserve). Charging rates would also rule out 2 long hops in a day, so we are probably never going to get anything comparable to what we have currently go, but I wonder what people's threshold would be to make it feasible.
-
Good info, thanks Clarence. . The rod end I am looking for appears welded. I think I'll keep looking around for a used one.
-
Does anybody know if it is possible to replace the rod ends on the MLG links like it is on the NLG links? Ive got a rear link, PN 550009-000 with a shot rod end bearing (from a 78J but I think it is common on most of the pre-80s Mooneys). Not sure what the rod end PNs are as the Parts Catalog doesn't list them separately.
-
Gascolator Gasket 2" x 1/16"
65C_flier replied to 1964-M20E's topic in Vintage Mooneys (pre-J models)
Thanks for the observations. The dark marks on the brake line are just grease/oil and good point about the safety wire. That pic was prior to removal and it was fixed on reinstall.