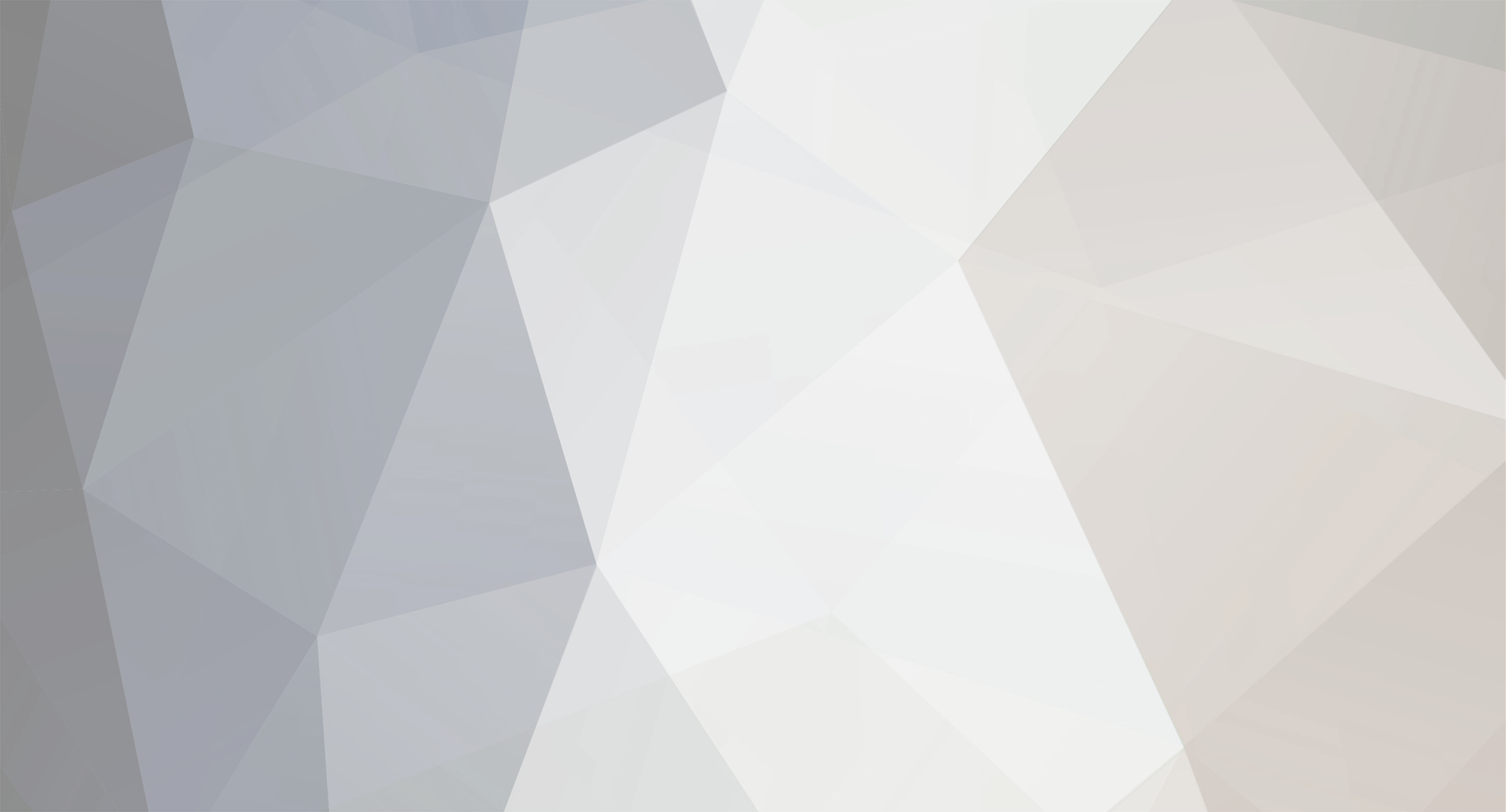
Gary0747
Supporter-
Posts
505 -
Joined
-
Last visited
Content Type
Profiles
Forums
Blogs
Gallery
Downloads
Media Demo
Events
Everything posted by Gary0747
-
I have been communicating via PM with some who have already replaced their hybrid weight with a used -7 weight and one said they came up short of weight like you suggest. I think he said his mechanic had to mount the weights outward from being fully inserted and had to use some kind of curable putty to get in balance. Mounting outward in this case was also driven by having to drill new holes since the holes in the old weight did not line up with his elevator holes. I wonder if the -7 weights actually weigh less than the -1 hybrid weights? The SB says they are a different weight but it does not say which is heavier.
-
Here is the earlier data for the 1966 and 1967 M20F production. It includes the smooth elevator design which may require different balance movement from the later non smooth design. I forget at which serial number the change was made. These early serial number M20F were the ones which got the hybrid weights. It sure looks like the SB 345A in step 4 did not use these moments for the smooth elevator but may have used the moments for the later non smooth elevator?
-
I think they have all been installed in matching pairs by the factory. That is not the issue I was talking about. My point is some aircraft came off the assembly line with hybrid weights and some came off with solid weights. They were mixed by airplane serial number. All in the early serial numbers. The factory at the time made no indication of them having different elevator balance numbers. I think they were correct in doing this since there is no logical reason why a weight having a minor difference in CG location would matter. The moment required by the elevator to prevent flutter should be the same and should be equal but opposite to the same moment provided by the elevator weight. Granted the moment arm may be slightly different but the total moment provided by the weights should be the same and driven by the design requirements of the elevator. Nothing I have seen explains why 1967 design balance numbers should be changed by any shape or form of the balance weights utilized today.
-
It is hard for me to understand why there is now this distinction between hybrid and non hybrid weights since the original manuals did not make this distinction. In fact the hybrid and non hybrid weights appear to have been mixed together randomly in the production of the early M20F airplanes. It sounds like the reasoning is the CG for the moment arm for the weight is different for hybrid and non hybrid weights. I can’t see why the elevator itself really cares as long as the elevator itself has the correct force and moment? To complicate the issue further those that have already found and reused salvaged solid weights have found that the mounting holes do not match and have had to drill new holes by moving the weight out a bit. This will change the CG on the weight just like the hybrid weight does. I don’t see why this matters though as long as the correct force moment is being exerted on the elevator itself.
-
I hope the people who have already done the rebalance using this SB have recognized that the control horn does not come off for rebalancing. The SB clearly leads one to think that. Also the weight balance numbers in the SB do not agree with the M20F service manual numbers. I think the factory owes the owners some clarification. Perhaps another example why a NPR comment period would have been appropriate.
-
Yes I was a bit confused by that too since the SB shows taking them apart and the M20F service manual did not seem to explain but the M20J and M20M service manuals do a better job. Step 3 says: Elevators and rudders are balanced with the control horn facing upwards.
-
I think Mooney must have learned a much easier way to install weights using threaded inserts in the lead and a screws. All the more recent model Mooney’s were done this way. Going this way should allow the weights to be easily removed to inspect or modify if repainting and rebalancing is needed. part number for the threaded insert is MS51830-201L and the screw is NAS623-3-1 Both appear cheap and readily available.
-
Iron Rivet called out in the parts manual is part number 430026-999 and found on the Lasar web site for $16.43 each. But the SB20-345A calls out a different part number 224497 iron rivet which I am not able to search and find. A previous Mooney Space discussion on weight replacement before this SB is attached here. A knowledgeable mechanic contributor makes the statement that the normal A&P mechanic will not have the ability to install the iron rivets because they should be driven red hot. I hope this is not the case.
-
It appears the comment period on the AD has now been expanded to 40 days? At least that is what is showing up on the web site now? If it is actually changed they may want more ongoing feed back since implementing the new weights may not begin for that long?
-
Neither the SB or the Service Manual seem to make this distinction. It seems like an immediate clarification is warranted so if it is a mistake and the wrong balance numbers were used there might have to be a redo and some unhappy owners. Another reason for having a comment period and a NPR?
-
Trying to figure out why the balance numbers in the SB345A for the primary focus Airplane of this the M20F are different from the factory manual? I have manual #104 dated July 1980. The balance range in that is 20 to 22 in-lb . Compared to the SB showing 14-16.75 in-lb? Perhaps it was changed in a previous SB? Or a mistake. Not sure how to resolve?
-
One added difficult step in doing the elevator removal for the 100 hour inspection for anyone with good hybrid weights is if you have the Laser hinge gap seals mod. Each hinge seal has four rivets to remove and replace every time the inspection is done! Yes the smart thing to do is just replace the weights and do the removal only once but no weights are currently available new or used so grounding the airplane may be the only realistic option!
-
If Mooney had included X-ray in the SB it would have likely been in the AD. Since it seems the FAA has taken everything in the SB as the right answer with no opportunity for discussion or input via a NPR. Is this a new approach or have they done it this way much in the past except on Emergency ADs?. I recall even the Piper wing spar AD had opportunity for comment, some delay on inspections and some reasonable changes on how to implement?
-
It does have micro cracks and chips.
-
Lots of discussion on finding the exact magnet that the SB specifies. My view is any magnet will attach to a good non corroded hybrid weight because the steel tube will be intact. But the corrosion product of the steel tube will likely be very weakly attracted to a magnet if at all. I hope the factory tested this on some bad weights before specifying this magnet. I see no downside to using the strongest magnet you can find.
-
I have not been able to find the referenced section X1, but it sounds like they are telling us to chemically “strip a corrosion sensitive” part? This appears to be ignoring the later guidance in M20J Service and Maintenance Manual section 20-00-02 on Corrosion Detection and Prevention. They are looking for microscopic cracks which must be a new standard for condemning counter weights. From my knowledge of corrosion and as indicated in the M20J manual you should not get solvents into cracks and locations where they are hard to either neutralize or wash out. Using a stripping solvent with a chlorinated hydrocarbon component has damaged a number of aircraft in the past too. They don’t say that directly but I have seen this and have a background dealing with this type of corrosion. In any case these hybrid corrosion sensitive weights were likely manufactured with microscopic seam cracks between the steel tube and the lead. You can see this area in my previous posting of photos of two hybrid weights that had been in service for 55 years. I was asking if anybody knew why one was still in perfect shape and one was totally destroyed to see if anybody understood the mechanisms at work here. Nobody answered so here is what I think based on my background. The round seam on the side is a microscopic crack that if not adequately sealed will allow water and contaminates and paint stripper in when exposed to that. The liquids essentially become electrolytes allowing a galvanic cell and the resulting corrosion. The key here is you can have dissimilar metals in contact but if you eliminate the electrolyte there will be no corrosion. You can see in the photo the good weight has had paint and a sealant covering the crack between the steel and the lead. The airplane also has been well maintained and kept in a good dry environment. It has not been tied down near the ocean which can be an extreme hazard for galvanic corrosion over time. I believe the hybrid weights are a risky design that obviously fail much easier if not properly maintained. But I think the hybrid weights can last indefinitely if the side seams are kept sealed. I know this thinking is contrary to some who think all hybrid weights are a ticking time bomb. But I don’t think they have an adequate understanding on the mechanisms at play here. Bottom line in my opinion if the factory is calling for a chemical strip of the corrosion sensitive weights that would be a mistake which is likely to cause new galvanic corrosion. Haven’t we normally just scraped select locations with a knife probing for corrosion? That would be adequate in my mind plus negate the need for removing and balancing the elevator. End of My Rant
-
Come on guys in all seriousness this thing is a mess! Over 3000 aircraft needing immediate inspection and log book entry by an inspector. In my view all that was needed is the FAA to allow an immediate owner inspection guided by the photos and info in the SB to locate any serious corrosion overlooked in previous inspection. Then at next annual and when Mooney has parts available complete what is need to be done with the weights. Nobody is going to fall out of the sky going this way. There is a chance the FAA might make some changes so be sure to give them your comments. Go to: regulations.gov and search for FAA 2023-24
-
Given that the corrosion products occupy more volume than the original materials I think any serious corrosion like this can be detected by looking for bulging and increase in size regardless of the amount of paint. I think most of the photos I have seen of bad weights confirm this. They grow and crack and eventually lose structural integrity.
-
I don’t know the Gauss or material but a small telescoping pick up tool magnet will attach strongly to a hybrid weight leaving no doubt.
-
What could cause the difference in these two hybrid counter weights? Both 55 years old. One on the bottom the (good one) has flown 6500 hours in a wide variety of weather and to many locations over those years. Is it suddenly going to disintegrate like the one one on the top? Or is an annual inspection simply looking for cracks and expansion around the exposed end going to be adequate versus elevator removal counter weight removal repainting and rebalancing the elevator every hundred hours?
-
Contacted two service centers and both had no idea when. One said perhaps March. They have been working on this for four months so far.
-
Original sbm20-345 was issued back in October but the latest sbm20-345A was issued in December with this surprising addition to part 2 remediation if hybrid was found and no cracks.
-
Yes, and what is the underlying reasoning for this 100 hour elevator removal and weight disassembly? All the photos I have seen of totally messed up weights show the parts inside the elevator to be fine. This stands to reason since all the bimetallic parts subject to galvanic corrosion are well outside this area and can be easily inspected with out disassembly and rebalance. In fact I think all this elevator removal reassembly creates the increased likelihood of a “maintenance induced failure”. Not to mention cost and down time
-
That clearly should have been caught years ago at annual. Most likely it was not painted and sealed properly or spent a long time tied down close to the ocean. The problem is some people have posted photos hybrid weights in perfect condition. What is the remedy for them? Also it has been reported the factory has not been able to provide replacement parts yet?
-
From what I read. Neither the SB or the AD specifies who is to inspect. Some may be at an airport where aircraft mechanics are not available on short notice. So if the owner can not inspect then I assume the 3000 plus aircraft mentioned as covered and requiring this inspection would be grounded until an IA is available? Perhaps delaying the inspection requirement to the next annual would be better? This discussion was started back in October on another posting. Here is a link for those wanting more info.