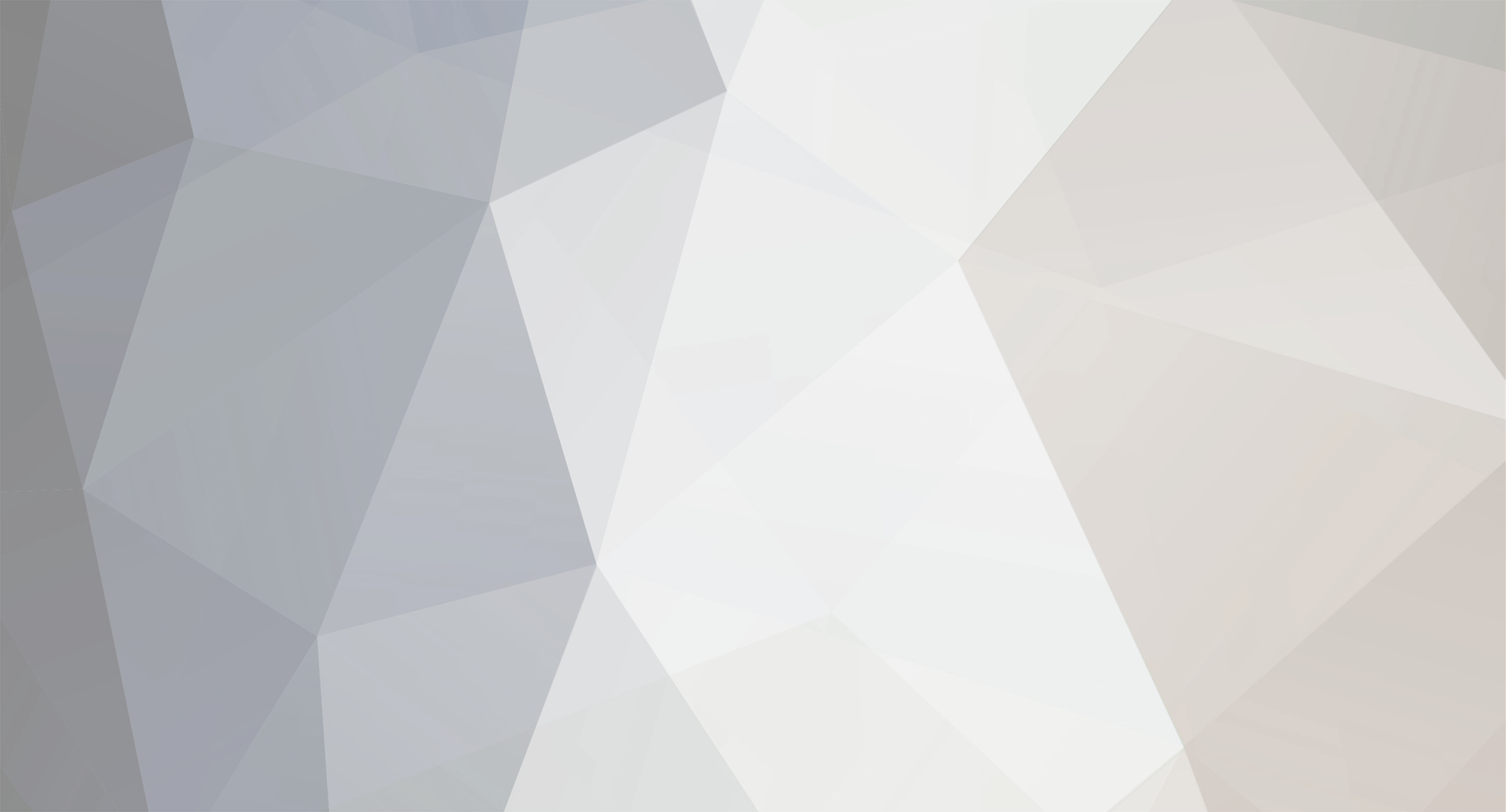
PaulM
Basic Member-
Posts
393 -
Joined
-
Last visited
PaulM's Achievements
-
G1000 and Garmin Flightstream in the Mooney
PaulM replied to Farolone's topic in Avionics/Panel Discussion
I'm on my way home from San Marcos TX, where Brian just installed the FS210 in my Bravo. It works perfectly.. $400 for the .37 update. $1000 for the FS210 install, and the cost of the FS210. We tried to install the wiring directly from the GTX345R to the FS210, but the single RS422 port on the 345R already feeds the GIA63W. Connecting just RS232 doesn't support Connext FMT 3 (It supports FMT 1 and FMT 4, but the FS210 wouldn't come online with either of those 2. In the end it doesn't matter you can leave bluetooth on the GTX345R and FS210 and you get the flight plan transfers and the ADSB weather and traffic. The install does require the Cirrus manifest for the FS210, just setting the serial port to Connect isn't enough. -
Yes, 50GB is very low for home use (given TV streaming).. I get 100-200Mbits consistently, but I use about 1TB/month with all of the TV/Video. Especially where I went to 4K when I had the available bandwidth. As for a window in a house, no, you really need a good view of the sky (roof) Also, if I am flying somewhere away from home, my wife is not going to be without internet. So the home starlink stays at home.. A flying starlink is on a "I don't really need it" in a Mooney.
-
Plans are now documented: >Business LOCAL PRIORITY - 50GB $65/MO >What is the maximum speed the Priority plans will operate at? >Local Priority: 350 mph >Global Priority: 550 mph Data will be limited to 1Mbit/sec if you run out of data and don't "top off"
-
You can also blow out the 5A trickle charge fuse if you start on #1... and it hasn't recovered yet, and you switch to #2. The depleted battery will take more than 5A.. and kill that fuse. I don't start on the best battery, I just switch #1 to #2 every full start (but not a just got fuel restart) Given the discussion about 2000+rpm for the alternate alternator this is the G1000/AC powered system with the backup alternator on the vacuum pump pad.
-
No.. the Connext protocol interface is configured only for the flight plans. the .37 software will already accept the radar mosaic from either XM or ADSB-UAT (the previous software had a bug with ADSB) For the FS210 to stream the ADSB data you need to connect it to the 345R (or 88). this also puts the bluetooth point in the cabin, removing the delivery from the rear access problems.
-
Starlink Business: https://www.starlink.com/service-plans/business GLOBAL PRIORITY - 50GB $250 Reliable Fixed & In-motion Use For smaller General Aviation aircraft or for aircraft that we do not have an STC for yet, Starlink Mini may be used as a Portable Electronic Device (PED), on the interior of an aircraft only. Supports aircraft ground speeds with <250kts, land and ocean: Mobile Priority at $250/mo. https://www.starlink.com/support/article/36fcdd07-e552-3dec-c6cc-bf8b8bb669cd
-
That is the user manual... has nothing to say about maintenance/hardware diagnostics. 190-00303-04 is the G1000 master line maintenance manual (2008) If a garmin tech couldn't find anything easy, then it is intermittent, and will be a problem to debug. Usually the next step is to put the plane on GPU and start to push on the wire bundles and see if anything drops off line. If this happens in flight at least take a picture of the LRU status on the 4th main menu. (you said no LRU problems)..
-
https://static.garmin.com/pumac/G1000:Mooney_G1000_GFC700SystemMaintenanceManual.pdf There is also Garmin Doc 190-00303-04 for generic G1000 information, I can't find a current copy online.
-
Which remote Garmin ADSB to Legacy G1000
PaulM replied to drstephensugiono's topic in Modern Mooney Discussion
You can make the system ADSB compliant with a 335R (WAAS) or 345R (WAAS). This will need either a GPS duplexer or another GPS antenna added to feed the WAAS GPS in the 3X5R. You do not have to upgrade the GIA33 to GIA63W's... that is only required for the latest software versions and LPV approaches. Now, I feel that the update to GIA63W is worth the $$ I did that and installed a 345R at the same time for ADSB compliance. Today, the choice would be for the 3X5RD (duplex) for space based ADSB compliance. -
G1000 and Garmin Flightstream in the Mooney
PaulM replied to Farolone's topic in Avionics/Panel Discussion
Then it should only be adding the 3 wires between the MFD and FS210 and setting the port to Connext Format 1. (unless that other Cirrus manifest is required) That should be the minimum to enable the flight plan transfer.. The other wires to the GDL69 and 345R are only needed to get the complete FS210 experience. Transfer, ADSB, + GDL69a control. -
G1000 and Garmin Flightstream in the Mooney
PaulM replied to Farolone's topic in Avionics/Panel Discussion
I'm pretty sure that if you update to the .37 software. Each software reload will put in the manifests from that software card. That will be the GTX33ES firmware version. Fixing the version is the only item on that special 3X5R manifest. I see that it is page D27 in Rev 9. I was referencing an older rev. -
G1000 and Garmin Flightstream in the Mooney
PaulM replied to Farolone's topic in Avionics/Panel Discussion
Hmm.. figure D-18 page D26... (I think I wrote that from another install manual first). As for requiring a specific manifest from Cirrus, I can't say. Many of the configuration expansions for GDL88 and GTX345R were done by manually updating the config on the RS485 and RS232 ports, manifests weren't required. This might be one of the, you can do it by loading the cirrus manifest.. but you can also do it by setting the Connext format manually. No matter what you will need a Garmin tech to load the 345R manifest which is an update to the gtx.rgn -
G1000 and Garmin Flightstream in the Mooney
PaulM replied to Farolone's topic in Avionics/Panel Discussion
Sure, lets build this.. #1 FS210 install manual https://www.rvplane.com/pdf/Garmin/FlightStream210IM.pdf Pages B2 (Power) B3 GDL69 connection B5 RS232 to the GTN (G1000 GDU1000 MFD) GTX345R install manual: http://www.aeroelectric.com/Installation_Data/Garmin/Garmin_GTX3X5_InstallationManualRev9-2017-06.pdf D37 shows a RS232 and RS422 rather than 2 RS422.. From the cirrus wiring diagrams: http://servicecenters.cirrusdesign.com/tech_pubs/SR2X/pdf/wm/SR22/html/wmmain.asp FS210: diagram 24-50-08 Page 12 Shows GDL69, and wires to UAT and MFD MFD: diagram 31-60-02 Page 9 Shows Data Link (210) connected to RS232 #3 (Matches picture in previous post) Once all wires are configured, you must turn off bluetooth on the GTX345R, configure and update the FS210. Update the G1000 to .37. the GTX345 needs different configurations after GDU software v15.X , you can find them in the GTX3x5 manual above. Page C11 & C12 Manually configure GDU#2 RS232 #3 to protocol Connext Format 1 (in & out) There will be some config in the GDL69 page for RS232 #3 Connect format ?, and the GTX345R needs to be set for Connext format 3 Input and Output. There will also be a G1000 manifest to load the GTX345R which is needed after the .37 update since .37 still expects a GTX33ES. Remember your 8GB terrain cards and the 4.9arc terrain database for SynVis. (it will technically fit on the 4GB cards if you don't have approach plates. ) -
G1000 and Garmin Flightstream in the Mooney
PaulM replied to Farolone's topic in Avionics/Panel Discussion
As I theorized in a previous thread, I knew it would work.. If a software rev has the feature, it is there, just that the default config templates (that are airframe specific) won't include it. you just have to configure the interfaces by hand. I have all of the Cirrus wiring diagrams related to this and everything is documented in the FS210 Install manual/wiring diagram except for the 2 wires from the MFD. Those would connect to RS323 #3. (as shown in the picture) I still need to get .37 installed, and convince the tech to add the extra wires. Two annuals ago I had a number of extra wires run from the front to the back to be able to connect the FS210 and a ARTEX1000 to include the NEMA datastream from a GIA63W. (Also in the Cirrus wiring) -
I once took off in my Bravo on a single mag (If your run-up is interrupted by something, do the checklist again from the top). .. and as soon as I leaned for cruise the EGT's shot over redline. I have no idea how high it would have gone if I didn't reduce MP and figure out what was wrong. (about 15 seconds after the redline alert) This is the G1000 trace for that flight.. the EGTs were in the 1700's and the TIT hit over 1800 . The bravo has an iconel exhaust which can take 1750.. but will burn it out over time, so I don't normally run it that hot. https://apps.savvyaviation.com/flights/shared/flight/3798462/fb5e68da-c7ec-4b5a-83ee-bcd26c41660a The EGT3 probe is failing, that is why I was flying to the MX shop. So everyone should check what their plane does, but a max power setting with a single mag is going to be very hard on the exhaust..