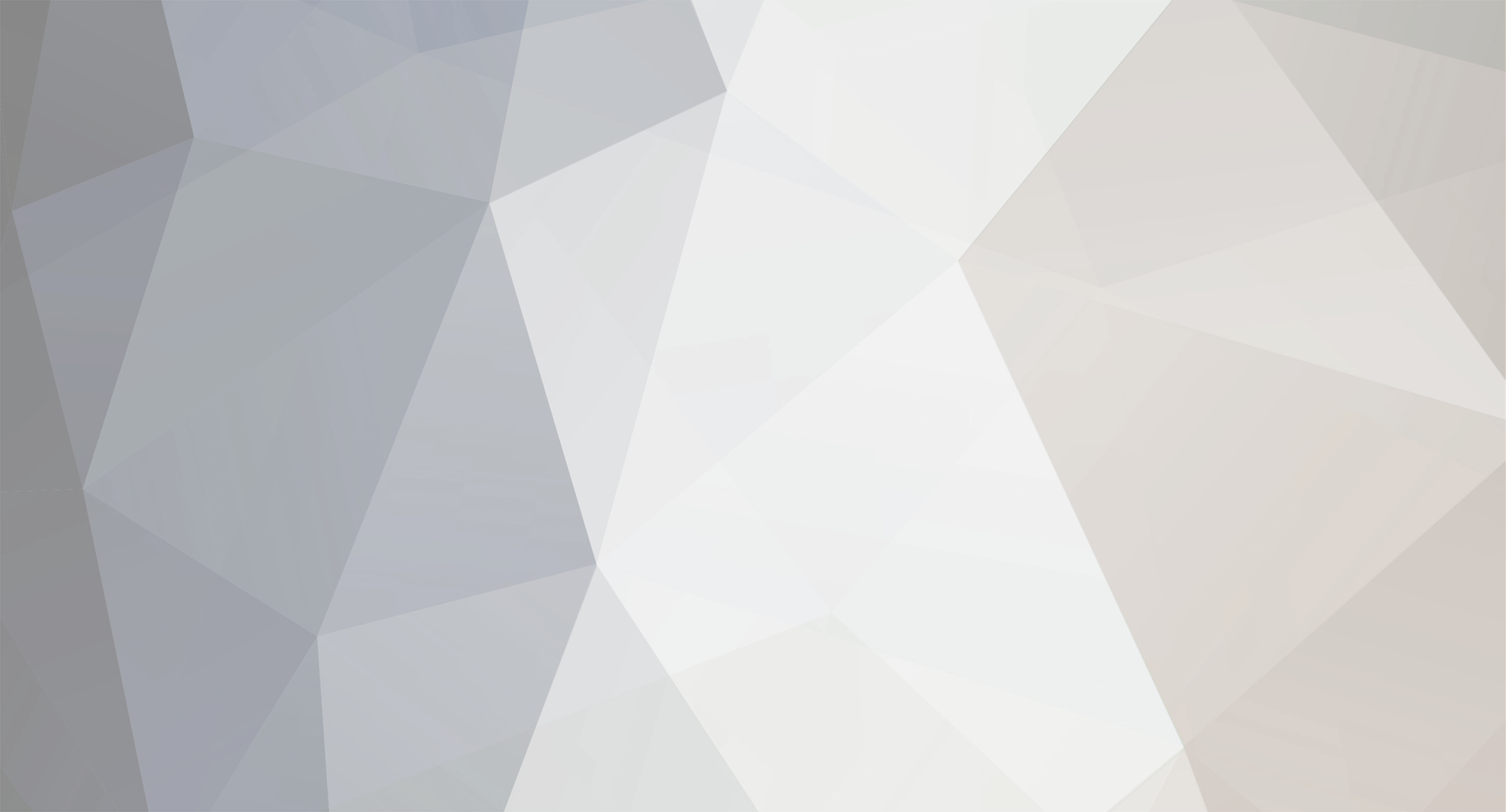
RobF15E
Basic Member-
Posts
7 -
Joined
-
Last visited
Profile Information
-
Reg #
N505L
-
Model
M20C
Recent Profile Visitors
The recent visitors block is disabled and is not being shown to other users.
RobF15E's Achievements
-
Great! Running it along with all the other wires should be fairly easy. Takeair, Thanks for the original photo. Your back bay looks a bit different from mine. I have a large bellow for the retractable step that sits right about where the jump receptacle is. How is your step retracted? Thanks for all the arrows, they make it easy to trace the path of the cable. Once I tackle this project, I'll take lots of pictures and copy the paperwork for anyone else who wants to undertake the project. If it weren't for my follow on project of moving the oil cooler, I probably wouldn't do this. Even with one of the cowl closure mods on my 65 C, I still get some reverse air flow at higher air speeds. The doghouse on my "C" isn't quite big enough to house the oil cooler like it is on the "E". Time to be creative.
-
Tommy123, thanks for your inputs. The batteries on all the Mercedes, BMWs and Audis I have owned are in the trunk for CG. OK, so I like German sports cars.... They start just fine - as long as the battery is in good shape - which is the same if it is in the engine compartment. I'll ensure my cables are of the correct gauge and are copper.
-
Marauder, Thank you for the picture. That is where I was wanting to install it. I don't want all the weight on the rear shelf since I'm not certain it is stressed for it. What kind of bracket does the battery box sit on? I was thinking about an "L" shaped shelf attached to the baggage compartment wall and the rear shelf. Does your negative ground just attach to the rear shelf as N201 mentioned? I assumed the Negative cable would run all the way to the front and ground on the engine mount. I was worried using the skin that there might be issues with the avionics and ground loops causing noise in the audio equipment. If that isn't an issue, that would save weight and cost. Does the positive cable just run underneath the floor? Where does it pop up and into the engine compartment? Sorry for so many questions, but I'd rather copy a successful install, and the "E" is obviously a successful install. Any additional pictures are great. No hurry as I am working on my ground transportation this weekend, but I know some others are also interested. I would imagine if Sabremech starts producing a cowl for the "C" model, there will be quite a few who need to move the battery. CG can be a real issue. I have the 3 blade prop and a thicker 201 mod windshield. I did lose nose weight with lighter alternator mod and lightweight starter. My "C" was tail heavy before the 3 blade prop and it was pitch sensitive. It is more stable now that it is nose heavy, but I think it cost a couple of knots. It is difficult to tell since the 3 blade was installed with an overhauled engine. Climb improved as expected with the 3 blade. I knew cruise might suffer some. I didn't get specific numbers as the plane was with my Cuz for all the mods and 8-9 years after that while I was stationed in Alaska, then California. Now the kids are out of the house, I got my bird back and I am tinkering away....
-
Gentlemen, I am still hoping to do this mod, but would really like to duplicate what someone else has already done. There are several different ways to mount the battery box and run the cables which is why I was hoping someone with an E model, or a C with the battery in the tail could take some pictures. Words are nice, pictures are better. I have already done W&B calcs to see where I would be after the Mod. I am also looking to the future (many years from now) when I replace the flooded cell battery with a Lithium battery that will be much lighter. I am also hoping to pull the Oil cooler back behind the baffling, so weight isn't my only concern. Thanks for your time. Last request. I and Jstickler76 have asked for people's opinions. Please don't slam folks who's opinion doesn't match yours. It is fine to disagree, but I see a lot of unnecessary insults tossed at folks. That's not helpful. This forum is better than many of the auto forums I participate in, so I appreciate that.
-
M20c rear window replacement
RobF15E replied to M20Bdriver's topic in Vintage Mooneys (pre-J models)
I am adding pictures of the 2 drill guides I made. on Amazon I ordered Round Spacer, Aluminum, Plain Finish, #4 Screw Size, 3/16" OD, 0.115" ID, 11/16" Length, Made in US (Pack of 25) They sell less than 25 but I had other uses for them. The long one has one end ground down for #6 screw and the other for #8. The shorter one is a #6 countersunk washer epoxied to the spacer. I had to drill out the hole in the washer since I was using it in the #8 holes. Drill the hole before you glue it. I agree with drill one hole put a screw in. The biggest area I had some trouble with was along the top, because the skin was not fitting close to the glass so it left a couple of holes higher than they should have been. I drilled the pilot holes with the glass in place, then removed it and drilled the holes to size and countersunk the holes in the garage. -
M20c rear window replacement
RobF15E replied to M20Bdriver's topic in Vintage Mooneys (pre-J models)
I just replaced all of mine with the thicker IR solar grey from LP Aero. I had an STC one piece sloped windshield from SWTA from 20 years ago. It took a couple of months for LP Aero to get the approval to make the windshield form me. The folks there were really helpful as I had some small issues with the glass not having the perfect curve. I didn't have to do much trimming to the side windows, but a ton to the windshield. I used my router table and a carbide trimming bit in a rip fence. It cuts very cleanly. Now my router table is integrated with a full size Jet table saw, so it isn't going to move or bounce around. I also used a belt sander for fine tuning the edges. With a 36 grit belt, it will remove material pretty quickly. Measure twice, cut a little, measure twice more, cut a little less..... Don't leave any sharp edges, bevel everything including the screw holes. Cracks start easily from sharp edges. I used a countersink to bevel both sides of the screw holes - just a little on the back side, more on the front where the dimpled sheet metal is. Also drill the holes slightly oversize to allow for less than perfect measuring and thermal expansion of the screws. Last tip, if you have stubborn caulk/sealant to remove, don't use a wire or nylon bristle bush in a drill. It will remove the caulk well, but it will also remove the dimpled sheet metal, leaving you a hole that is now too large with no dimple... Don't ask how I know..... Don't be afraid of the solar grey tint - it isn't really tint the way we think of it. What I got from LP Aero looks like 97% light transmissivity. I have not flown the plane yet, still putting it back together from a lot of work this annual, so I can't comment on the thicker glass or the IR reduction. Having someone help hold the glass in place while you are drilling is a big help. I didn't want to end up damaging my sheet metal holes (any more than I already did), so I made a couple of drill guides that worked really well. I bought some aluminum stand offs on Amazon that had the right sized hole in the center for my pilot bit (1/8) I then ground down the end to make it look like the taper on a flat head screw. I then was able to lock it into a needle nose vice grip and put it in the countersunk hole and drill through the plexi. This ensured the pilot hole was centered. I followed that up with the final sixed drill bit with the plexi on my garage. Then countersunk and beveled. I also made a countersink doing the same thing, except I went a step further and epoxied the ground end of the stand off to a #6 beveled washer, That helped keep the guide perpendicular to the glass. Separate tip. Get some zip lock baggies, 1 for each window. Get a permeant marker. Put a number on each aluminum tab and on the airframe so you can keep them in the right order. Make certain that the number you put on the sheet metal is far enough away from the caulk that when you use the nylon brush I told you not to use, you don't clean the number right off the aluminum.... I hate learning the hard way.... You have to put the tabs back in the original spots because of the little holes in you trim. they are all different. No automated machines built these planes. All done by hand. I also thought I would be cool and rabbit the edges of the thicker windows so they would be flush fitting like some of the really sweet homebuilts I have seen. Don't. Not only is it time consuming and difficult on curved plexi, my sheet metal had beveled edges which kept my rabbited edges from being flush fitting anyway.. Anyway, I am not an expert on window installation, just sharing the mistakes I made and the few things that went well. Follow at you own risk. I'll see if I can find my homemade drill guides and take a picture. Oh yeah, plexiglass drill bits only. Regular drill bits will bit a pull through to fast. no, I didn't make that mistake.... this time.. ;-) -
I am also looking to move the battery back to the tail in my 65 M20C. I also had a 3 bladed prop put on the nose at overhaul and it changed my tail heavy plane to a nose heavy plane. Before the prop, I had replaced the gen and starter with light weight versions so I was a bit tail heavy. When flying, it was always a bit pitch sensitive. If a passenger leaned forward, the plane would descend a bit. Slide the seat back a notch, trim forward. Landings with the nose wheel in the air were easy, actually too easy as I scraped the tail once.... OK, so it isn't an Eagle and I shouldn't be doing an Eagle walk with it.... Now with the heavy nose, it is much more stable in level flight and I have to trim the snot out of it for greaser landings. I did a series of weight and balance checks assuming I moved the battery back and added weight for new cables. I didn't plan on moving the solenoids as I like my jump start door on the front cowl. I was able to remain within the W&B envelope for all configurations I would fly in. I'd like to duplicate the M20E installation but no one I know has an "E". Can anyone with an "E" provide some pictures of the battery mount and the wire routing? My plane is down for the annual now, so I will be doing this soon. If I am able to pull it off, I'll gladly share pictures and paperwork for others. Expect that the plane may pick up a couple of knots, but will require more work to keep level. Alas, I don't have an auto pilot.... I also have a one piece windshield mod with the thicker glass adding weight fwd of the CG.